
표면자동추종 적층기술을 이용한 DED방식 적층제조
Copyright © The Korean Society for Precision Engineering
This is an Open-Access article distributed under the terms of the Creative Commons Attribution Non-Commercial License (http://creativecommons.org/licenses/by-nc/3.0) which permits unrestricted non-commercial use, distribution, and reproduction in any medium, provided the original work is properly cited.
Abstract
Directed energy deposition (DED) additive manufacturing technology enhances the functionality of existing or damaged parts by adding metallic materials to the surfaces. Blown-powder DED technology utilizes a focused, high-energy source to fuse the part's surface with the supplied metal powder. Maintaining a constant stand-off distance (SOD), the distance between the deposition head and the workpiece, is a key factor in ensuring deposition quality, as variations in SOD will change the powder focus position and the laser spot size on the surface. Therefore, traditional additive manufacturing systems require CAD or pre-scanned surface data. In this study, we proposed auto-surface tracking technology. No workpiece CAD data or pre-scanned surface data are required, and in-situ measurement and feedback control can automatically consider the deposition height differences that cause a change in SOD when depositing the next layer. The accuracy of the SOD measurements and feedback control error was verified using a step height sample. The mean SOD measurement error was 4.7 μm with a standard deviation of 42 μm (reference SOD, 14 mm). The feasibility of the auto-surface tracking technology was confirmed through the additive manufacturing processes of the gear and an actual blanking mold applied in the defense and industrial fields.
Keywords:
Additive manufacturing, 3D printing, Auto-surface tracking, Stand-off distance, Melt pool, DED키워드:
적층제조, 3D 프린팅, 표면자동추종, 스탠드 오프 거리, 용융풀1. 서론
적층제조기술 중 DED (Directed Energy Deposition) 방식은 집속된 고출력 열에너지로 모재와 금속적층소재를 용융시켜 반복적으로 레이어를 형성하여 3차원 형상을 제조하는 방식이다[1,2]. 레이저를 열원으로 사용하는 DED 방식이 상대적으로 작은 열영향부를 가지며 최종제품형상에 가깝게 제조가능하여 손상된 부품의 보수 및 이종소재 적층을 통한 표면 성능향상 등에 주로 활용되고 있다[3-5].
DED 공정에서 SOD (Stand-Off Distance)는 적층 프로세싱 헤드와 적층 대상물 사이의 거리로 정의된다. SOD의 변화는 적층 대상물 표면에서의 레이저 빔 크기 및 파우더 포커싱 위치 변화로 이어지고 결국 용융풀 크기, 용융풀으로의 파우더 공급량이 달라져 적층량 변화는 물론 궁극적으로 적층품질 저하를 유발한다.
3차원 형상을 만들기 위해서는 일반적으로 CAD 데이터 또는 표면 스캐닝을 통해 형상정보를 취득하고 이를 기준으로 적층량이 일정하다는 전제로 적층용 프로세싱 헤드를 매 층마다 정해진 높이만큼 이송시킨다. 하지만, 적층 대상물의 크기, 형상에 따라 열용량이 달라지기 때문에 각 층에서의 적층량이 바뀌게 된다. Fig. 1은 박벽(Thin Wall) 형태의 적층결과를 나타낸다. 그림과 같이 적층물 하단부의 두께가 상부에 비해 얇음을 알 수 있는데, 이는 처음 적층이 시작될 때 모재로의 급속한 열확산으로 용융풀의 크기가 작아지기 때문이다. 이러한 경향 또한 모재의 크기 및 형상에 따라 다른 양상을 보여 실제 원하는 적층높이를 얻지 못하고 결국은 반복적인 시행착오를 통하여 공정을 도출하게 된다. 기존의 연구들은 표면형상 정보를 획득한 후 각 층별로 정해진 적층높이에 도달하도록 공정 중 적층높이를 측정하여 파우더 공급량, 레이저 파워 등의 공정조건을 제어하는 방식의 연구가 주로 진행되었다[6-10]. 하지만 표면 형상정보를 얻기 위해 스캐닝 작업이 필요하며, 실제 적층 대상물과 적층제조 장비와의 상대좌표 정렬이 필요하는 등 생산성 저하의 원인이 된다.
본 연구에서는 CAD 데이터나 표면 스캐닝을 통한 표면 형상정보 취득작업 없이 SOD 측정 및 피드백 제어로 실시간으로 적층물 표면을 추종하여 항상 일정한 SOD를 유지하는 표면자동추종 적층기술을 개발하였다. 2가지 타입의 SOD 측정 모듈을 개발하였으며 성능검증은 물론 표면자동추종 적층기술을 이용하여 실제 자동차용 블랭킹금형 제작 및 국방용 기어부품 보수 등 산업계 및 국방분야에의 실제 적용을 통한 유용성을 확인하였다.
2. DED 방식 적층제조시스템
2.1 적층제조시스템 구성
Fig. 2는 자체 개발한 DED 방식 적층제조시스템을 나타낸다[11-12]. 이 시스템은 1,700 × 1,100 × 1,000 mm3 (X× Y × Z)의 넓은 적층영역을 가지고 있으며, 최대출력 5 kW의 고출력 파이버 레이저(YLS-5000, IPT Photonics)와 자체 개발한 프로세싱 헤드, 정밀 파우더 피더, SOD (Stand-Off Distance) 측정 및 제어 모듈 등을 탑재하고 있다.
2.2 SOD 측정모듈 및 표면자동추종 적층 특성
표면자동추종 적층을 위한 센서로 각각 PSD (Position Sensitive Detector)와 열화상 카메라로 구성된 서로 다른 두가지 타입의 SOD 측정모듈을 개발하였다.
첫 번째 모듈은 크게 광학계와 PSD로 구성되어 있으며, 별도의 측정광원을 사용하지 않고 프로세싱 헤드 측면에 설치되어 PSD로 측정한 프로세싱 레이저 빔의 위치변화를 광삼각법을 이용하여 높이로 변환한다. PSD 표면에 있는 광점의 위치에 비례하는 출력전류가 발생하게 되며 전류의 비로부터 위치를 간단하게 계산할 수 있다. ND (Neutral Density) 필터로 측정광량 조절, 레이저 라인 필터(1070 ± 5 nm)를 사용하여 외부광의 영향을 제거하였으며, 2.5 × 34 mm2의 측정영역 및 프로세싱 레이저 파장(1070 nm)에서 높은 감도를 가지고 있는 1차원 PSD (S1352, Hamamatsu Photonics)를 장착하였다. PSD 타입의 SOD 측정모듈은 복잡한 연산이 필요 없기 때문에 1 kHz 수준의 빠른 측정이 가능하다.
성능 검증을 위하여 Table 1과 같은 공정조건으로 평판시편에서 표면자동추종 적층을 수행하였다. Fig. 3은 목표 SOD 14 mm일 때 평면에 지그재그로 30 × 10 mm2 영역을 적층하였을 때의 피드백 결과를 보여준다. 목표 SOD에 아주 가까운 14.03 mm를 유지하였으며 표준편차도 0.1 mm 수준으로 양호한 표면추종 적층이 가능함을 확인하였다.
Fig. 4는 피라미드 형태로 단차가 형성된 표면에 표면자동추종 적층한 결과이며, 그림과 같이 표면 데이터없이 단순한 영역지정만으로 표면단차를 반영한 적층이 가능함을 확인하였다.
PSD 타입 SOD 측정모듈의 경우 위치변화가 전류 값으로 출력되어 측정속도가 빠른 장점이 있으나, 적층소재 및 공정조건에 따라 설정 레이저 출력이 변경될 경우, ND 필터의 교체가 필요하며 공정 모니터링을 위한 용융풀의 온도 정보를 획득하지 못하는 단점이 있다. 이와 같은 단점을 보완하기 위하여 고온 열화상 카메라를 센서로 사용한 SOD 측정모듈을 개발하였다(Fig. 5).
PSD를 대신하여 2대의 열화상 카메라를 프로세싱 헤드 중심으로 좌우대칭으로 설치하여 측정사각지대를 줄이고, 이미지 프로세싱을 통하여 용융풀 중심점 도출 및 이에 따른 SOD를 계산한다. 열화상 카메라(PI05M, Optris)는 온도측정 범위 900-2,000oC, 최대 프레임률 1 kHz를 가지고 있어 고속측정이 가능하며 SOD 측정은 물론 공정관리를 위한 용융풀 모니터링용으로도 사용된다. 표면자동추종 적층을 위한 SOD 측정의 개략적인 프로세스는, 먼저 ROI 정의를 통하여 스패터(Spatter)에 의한 노이즈 영향을 줄이고, 사전 정의된 한계강도 이상 영역으로부터 용융풀 윤곽선을 추출한다. 다음으로 2차원 포인트 세트를 둘러싸는 최소 원을 찾아낸 다음 마지막으로 이를 통해 용융풀 중심을 찾아 SOD의 변화량을 도출하게 된다. 프로세싱 헤드는 SOD 14 mm일 경우 최적의 적층효율을 가지도록 설계 및 제작되었으며, SOD 측정모듈은 이를 기준으로 Z축 방향으로 ±6 mm의 높이변화를 800 Hz 수준으로 측정 가능하도록 설계되었다.
Fig. 6은 개발한 표면자동추종 적층기술 적용 전(a)과 후(b)의 적층결과를 나타낸다. 표면자동추종 적층을 적용하였을 경우 피드백 제어를 통하여 목표 적층높이 5 mm에 달하는 결과를 얻을 수 있었으나, 이를 적용하지 않고 정해진 동일 레이어 두께를 기준으로 적층한 경우 적층높이는 목표 적층량에 미치지 못하는 3.2 mm에 그쳤다.
스테이지와의 상대이동 거리비교 및 단차시편을 이용하여 열화상 카메라 타입 SOD 측정모듈의 성능검증을 수행하였다. Fig. 7은 레이저 파워 300 W, 파우더 공급량 7.4 g/min 조건으로 프로세싱 헤드가 장착되어 있는 Z축 스테이지를 300 μm 스텝으로 순차적으로 상승 시 측정한 SOD 측정값을 나타낸다. 설정 SOD 14 mm 위치에서의 평균 오차 4.7 μm, 표준편차 42 μm가 확인되었으며, 300 μm 단차변화를 명확하게 구분 가능함을 확인할 수 있었다.
Figs. 8(a)와 8(b)는 각각 표면자동추종 적층 기능의 유용성 검증을 위한 0.5, 1.5, 3 mm의 단차로 구성된 시편의 디자인 및 실제 표면자동추종 적층결과를 나타낸다. 또한, 이때의 SOD 실시간 피드백 제어 결과를 Fig. 9에 도시하였다. Fig. 9의 X축과 Y축은 각각 단차 시편의 위치와 그 위치에서의 SOD 값을 나타낸다. 단차변화에도 피드백 제어를 통해 목표 SOD 14 mm를 일정하게 유지하고 있음을 알 수 있다. 그래프 내의 스파이크 형태의 SOD 변화는 단차 시편의 급격한 높이 변화에 따른 것이나 실제 표면자동추종 적층 시에는 필터링을 통해 제거하였다. 일반적으로 실제 적층공정에서는 준비과정에서 이와 같은 급격한 단차가 있는 표면은 적층시 품질에 영향을 미칠 수 있어 그대로 사용하지 않고 완만한 표면을 형성하도록 가공하여 사용한다.
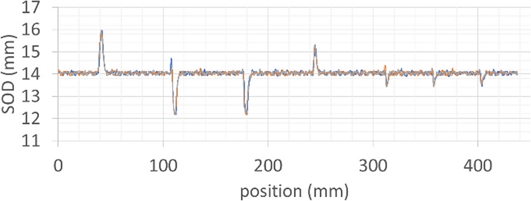
Real-time SOD feedback control results for the step height sample using auto-surface tracking deposition function
표면 프로파일 추종 정밀도 검증을 위하여 레이저 거리 센서(Conopoint-10, Optimet, Accuracy 6 μm)로 측정한 단차 프로파일과 표면자동추종 적층 시 피드백 제어에 따른 Z축 이송결과를 각각 Fig. 10 에 나타내었다. X축은 단차 시편에서의 위치, Y축은 피드백 제어 후의 Z방향 스테이지 이송량을 나타낸다. 갑작스런 높이변화(±3 mm)에도 SOD 측정 및 실시간 피드백 제어를 통하여 표면을 정밀하게 추종하고 있음을 확인할 수 있다. 단차 시편 가공면이 가지고 있는 공차(±0.05 mm), 레이저 거리센서의 오차는 물론 적층공정에서의 고출력 레이저 조사, 파우더 비산 및 스패터 발생 등 열악한 조건에서도 각 단차에서의 평균 오차 최소 4.6 μm, 최대 34 μm으로 우수한 표면자동추종 적층성능을 가지고 있음을 확인하였다.
3. 표면자동추종 적층실증 실험
3.1 국방부품 적층제조 보수
Fig. 11은 국방 장비에 사용되는 기어로 가혹한 작동환경 하의 작동으로 손상된 부위(a)와 표면자동추종 적층을 통해 이를 보수한 부품(b)을 나타낸다. 기어 부품은 수천 RPM의 고속회전으로 인하여 시일(Seal) 조립부의 마모가 발생하나 기존방법으로는 수리가 불가능하여 폐기되는 부품이다. 마모로 인한 결함을 기계가공으로 제거한 후 개발한 표면자동추종 적층기술을 이용한 보수 및 후가공을 통해 요구되는 최종형상을 확보하였다. 기존 부품의 경우, 단조금형강 소재로 제작되어 HRC 50 이상의 경도가 요구되나, 내마모성 강화를 위하여 기존 소재보다 경도가 높은 몰리브덴-텅스텐 합금 고속도 공구강 소재인 AISI M2 금속분말을 적층소재로 선정하였다. CAD 데이터 및 번거로운 정렬작업 없이, 요구되는 적층 높이의 확보는 물론 포어(Pore) 없는 건전한 표면 및 HRC 61.2의 경도 확보로 기존 소재보다 더 우수한 내마모성을 가지는 기능향상 보수가 가능하게 되었다. 육군종합정비창에서 요구하는 물성, 치수 및 성능 테스트를 통과하였으며, 국방장비에 장착 후 현재 실전 배치되어 정상 운용되고 있다.
3.2 블랭킹 금형 적층제조
개발 기술의 산업계 적용 예로, 자동차부품 제작용 블랭킹(Blanking) 금형을 적층제조 기법으로 제작하였다. Fig. 12는 표면자동추종 적층기능을 이용해 프린팅한 적층부(a)와 후가공을 통해 최종 완성한 자동차 ECU 브라켓(Bracket) 제작용 블랭킹(Blanking) 금형사진(b)을 나타낸다.
전산해석을 통해 실제 프레스 공정에서 금형의 응력 분포를 계산하여 적층영역을 최소화하면서도 블랭킹 성능의 확보가 가능한 최적 적층영역을 도출하였다. 소재는 내마모성 강화를 위하여 AISI M2 금속분말을 이용하여 내마모성을 향상시켰다. 표면자동추종 적층 기능을 통하여 번거로운 작업없이 적층품질 및 목표 적층량 확보가 가능하였다. 제작된 블랭킹 금형은 실제 자동차 부품 양산에 적용되어 기존 대비 내마모성 향상으로 금형수명 증가를 확인하였다.
4. 결론
실시간 SOD (Stand-Off Distance) 측정 및 피드백 제어를 통한 표면자동추종 적층기술을 개발하여, 국방 및 산업부품 제작에 적용을 통한 유용성을 검증하였다. 각각 PSD (Position Sensitive Detector) 및 열화상 카메라를 센서로 이용하는 2가지 종류의 SOD 측정모듈을 개발하여 성능을 확인하였다. PSD 타입 SOD 측정모듈은 1 kHz 이상의 고속측정이 가능하며, 열화상 카메라 타입 SOD 측정모듈은 800 Hz의 샘플링이 가능하고 SOD뿐만 아니라 용융풀 온도 측정이 가능하여 공정 모니터링으로도 사용 가능한 장점이 있다. SOD 측정모듈의 성능검증 결과 SOD 14 mm 위치에서 측정 평균 오차 4.7 μm, 표준편차 42 μm를 가지며 300 μm 단차변화를 명확하게 구분 가능하였다. 단차시편을 이용한 표면자동추종 적층 성능평가의 결과, 가공면의 공차, 공정 시 발생하는 파우더 비산, 스패터 등의 열악한 조건에도 각 단차에서의 평균 오차는 최소 4.6 μm, 최대 34 μm로 우수한 표면자동추종 적층 성능을 보여주었다. 개발된 표면 자동 추종 적층기술을 적용하여 국방부품용 기어 보수 및 실제 자동차부품 제작용 블랭킹 금형을 제작하였으며, 부품의 실전배치 및 양산 적용을 통해 기술의 유용성을 검증하였다.
Acknowledgments
본 논문은 정부의 재원으로 한국기계연구원 기본사업(NK242J)의 지원을 받아 수행된 연구입니다. 실증에 도움을 주신 육군종합정비창 관계자분께 감사드립니다.
REFERENCES
-
Monzón, M., Ortega, Z., Martínez, A., Ortega, F., (2015), Standardization in additive manufacturing: Activities carried out by international organizations and projects, The International Journal of Advanced Manufacturing Technology, 76, 1111-1121.
[https://doi.org/10.1007/s00170-014-6334-1]
-
Frazier, W. E., (2014), Metal additive manufacturing: A review, Journal of Materials Engineering and Performance, 23, 1917-1928.
[https://doi.org/10.1007/s11665-014-0958-z]
-
Arias-González, F., Del Val, J., Comesaña, R., Penide, J., Lusquiños, F., Quintero, F., Riveiro, A., Boutinguiza, M., Pou, J., (2017), Laser cladding of phosphor bronze, Surface and Coatings Technology, 313, 248-254.
[https://doi.org/10.1016/j.surfcoat.2017.01.097]
-
Zuback, J., DebRoy, T., (2018), The hardness of additively manufactured alloys, Materials, 11(11), 2070.
[https://doi.org/10.3390/ma11112070]
- Liu, Q., Djugum, R., Sun, S., Walker, K., Choi, J., Brandt, M., (2017), Repair and manufacturing of military aircraft components by additive manufacturing technology, Proceedings of the Australian Aerospace Congress (AIAC 2017), 363-368.
-
Iravani-Tabrizipour, M., Toyserkani, E., (2007), An image-based feature tracking algorithm for real-time measurement of clad height, Machine Vision and Applications, 18, 343-354.
[https://doi.org/10.1007/s00138-006-0066-7]
-
Davis, T. A., Shin, Y. C., (2011), Vision-based clad height measurement, Machine Vision and Applications, 22, 129-136.
[https://doi.org/10.1007/s00138-009-0240-9]
-
Song, L., Bagavath-Singh, V., Dutta, B., Mazumder, J., (2012), Control of melt pool temperature and deposition height during direct metal deposition process, The International Journal of Advanced Manufacturing Technology, 58, 247-256.
[https://doi.org/10.1007/s00170-011-3395-2]
-
Fathi, A., Khajepour, A., Toyserkani, E., Durali, M., (2007), Clad height control in laser solid freeform fabrication using a feedforward PID controller, The International Journal of Advanced Manufacturing Technology, 35(3-4), 280-292.
[https://doi.org/10.1007/s00170-006-0721-1]
-
Mazumder, J., Dutta, D., Kikuchi, N., Ghosh, A., (2000), Closed loop direct metal deposition: Art to part, Optics and Lasers in Engineering, 34(4-6), 397-414.
[https://doi.org/10.1016/S0143-8166(00)00072-5]
- Ha, T., Shin, H., Lee, C., Heo, S., (2017), Auto tracking module for DED type metal 3D printing system, Proceedings of the Asian Society for Precision Engineering and Nanotechnology, 1237-1239.
- Ha, T., Lee, C., Shin, H., Heo, S., (2018), Fabrication of Ti-6Al-4V thin cylinder by DED metal 3D printing process. Proceedings of the International Symposium on Precision Engineering and Sustainable Manufacturing, PP007.
Head of the Department 3D Printing, Korea Institute of Machinery & Materials (KIMM). His research area includes 3D printing process and equipment development.
E-mail: taehoha@kimm.re.kr
Principal researcher in the Department 3D Printing, Korea Institute of Machinery & Materials (KIMM). His research interest is process simulation and additive manufacturing.
E-mail: heo@kimm.re.kr
Director in the Advanced Manufacturing System Research Division, Korea Institute of Machinery and Materials (KIMM). His research interest is metal 3D printer.
E-mail: lcwlej@kimm.re.kr
Senior Researcher in the Department 3D Printing, Korea Institute of Machinery & Materials (KIMM). His research interest is design for additive manufacturing by using optimization methods.
E-mail: mkjung@kimm.re.kr
Team Manager. Advanced Body Research in the R&D Center, AJIN Industrial Co., Ltd.. His research interest is industrial application of additive manufacturing.
E-mail: cjw@wamc.co.kr