
절삭가공의 디지털 전환을 위한 디지털 쓰레드
Copyright © The Korean Society for Precision Engineering
This is an Open-Access article distributed under the terms of the Creative Commons Attribution Non-Commercial License (http://creativecommons.org/licenses/by-nc/3.0) which permits unrestricted non-commercial use, distribution, and reproduction in any medium, provided the original work is properly cited.
Abstract
Currently digital transformation has a huge impact on human lives. Digital transformation does not just mean a transformation of a (non-) physical element to a digitally identifiable element. It focuses on the utilization of digital technology for transforming (improving) procedures or routines of business and operation. The manufacturing industry has been adopting the most recent digital technology, and lots of digital data are being created. To utilize the stored data, data analysis is essential. Because the manufacturing data is created in a different format at every manufacturing step, the integration of the data is always the bottleneck of the data analysis. Querying of the right data at the proper time is fundamental for high-level data analysis. The digital thread is introduced to provide the inter-reference of digital data based on a context. This paper proposes a digital thread framework for the machining process. The context of the proposed framework consists of the questions of how the product will be machined, how it is (was) being produced, and how it was made. A prototype software was developed to verify the proposed framework by implementing the creating, storing, and querying modules for simulation, monitoring, and inspection data.
Keywords:
Machining, Digital thread, Virtual machining, Process monitoring, Inspection키워드:
절삭가공, 디지털 쓰레드, 가상 가공, 공정 모니터링, 검사1. 서론
4차 산업혁명과 COVID19 팬데믹 등 거대 전환점에서 제조 산업에 급격한 변화 요구가 있어왔고, 그 중심에 디지털화가 있다[1]. 디지털 전환(Digital Trans-formation)은 정보와 컴퓨팅, 통신 및 연결 기술 조합을 통해 중대한 변화를 촉발하여 대상을 개선하는 것을 목표로 하는 일련의 프로세스로 정의되고 있다[2]. 제조 산업에서는 수없이 발생되는 경험적, 아날로그적 데이터가 디지털로 전환되면서 제조 공정의 첨단화, 지능화가 진행되고 있다.
디지털 전환의 중요 요소인 정보(Information)는 디지털화된 데이터(Digitalized Data, D)로부터, 통신(Communication)은 자산(Asset) 간의 네트워크(Network, N)로부터, 개선(Improvement)은 인공지능(Artificial Intelligence, AI)과 같은 솔루션으로 연결된다. 즉, 디지털 전환의 핵심인 D. N. A. 각 요소는 유기적이고 자율적으로 제조 공정이 운영되어 효율성과 품질향상 등의 목적을 달성하도록 활용된다.
제조 디지털 전환과 관련되어 디지털 트윈(Digital Twin), 디지털 그림자(Digital Shadow), 디지털 쓰레드(Digital Thread) 등 다양한 개념들이 정의되고 일부는 표준으로 제정되고 있다[3,4]. Grieves는 2002년 제품 수명주기 관리(Product Lifecycle Management) 관련 발표에서 현재의 디지털 트윈 개념을 처음으로 소개하였고, 물리적 시스템에 대한 디지털 정보 구조로서 개체(Entity)를 자체적으로 생성하고 해당 물리적 시스템과 연결된 형태로 정의하였다[5,6]. Negri는 제조산업에서의 디지털 트윈은 감지된 데이터와 연결된 스마트 장치(Device), 수학적 모델 및 실시간 데이터 처리를 통해 생산시스템의 동작을 각 수명 주기 단계에서 실시간으로 예측하고 최적화하는 것으로 정의하였다[7]. 디지털 트윈과 유사한 개념인 디지털 그림자는 실제 자산에서 디지털 객체로의 데이터 흐름은 자동으로 되지만, 디지털 객체에서의 실제 자산의 상태 변경은 자동으로 되지 않아 상호연계성 측면에서 낮은 단계로 구분된다[5]. 한편, Levia는 기능적으로 구분되어 있던 시각을 뛰어넘어서, 자산의 생명 주기(Lifecycle) 전반에 걸쳐 연결된 데이터의 흐름과 통합적 조회를 제공하는 통신 체계(Framework)로 디지털 쓰레드를 정의하였다[8]. 기능, 장비, 모델, 신호 등이 모두 디지털 쓰레드의 대상이 될 수 있다. 디지털 쓰레드는 Fig. 1과 같이 디지털 트윈 객체와 자산 간의 데이터/모델 연결성을 높이고, 다양한 산업군의 각 프로세스에서 발생되는 데이터를 활용하여 효율 개선 및 최적화 등을 위해 활용되고 있다[9-12]. Singh은 설계 및 제조 측면에서 고려되어야 하는 하중, 소재 특성, 제조관련 인자, 비용 등을 수학적 모델링과 측정을 병행한 디지털 쓰레드를 통해 항공부품을 설계하는 가이드 라인을 제시하였다[9]. Zhang은 항공기 조립 공정의 실시간 예측과 최적화를 위해 디지털 쓰레드 기반의 디지털 트윈 프레임워크를 제안하고, 드릴링, 리벳팅 등 각 공정 단계마다의 공정 및 품질 예측/분석을 통해 개선한 사례를 소개하였다[10]. Jagusch는 조선(Shipbuilding)에서의 제품 설계단계, 공정계획 등을 디지털 쓰레드로 연결하는 모델을 통해 디지털 트윈에 반영함으로써 개별적인 프로세스를 연결하고, 최적화하는 방법을 제안했다[11]. Feldhausen은 CNC 기반의 적층-절삭 하이브리드 제조에서 열화상 모니터링과 NC통신을 통한 기계 및 프로세스 정보를 기반으로 한 디지털 쓰레드를 구현하고 동적 드웰(Dwell)을 통한 품질 최적화 개념을 소개하였다[12]. 절삭가공은 인구절벽 및 숙련자의 감소로 인한 영향이 큰 산업이며 디지털 전환 요구도가 높고 자율제조 기술 개발이 시급히 필요한 제조 공정이다. 절삭가공 기반 제조 공정의 개선을 위해서 절삭공구의 마모 예측이나 가공공정의 정확성 추정 등에 디지털 트윈을 적용한 연구 및 사례가 있어왔으나[13,14], 절삭가공 공정 전주기에 걸쳐 사용되거나 생성되는 다양한 정보 간 연계를 제공하는 디지털 쓰레드와 관련한 연구는 심도 깊게 이루어지지 않았다.
본 논문은 제조공정의 디지털 전환을 위한 데이터 연결 및 상호운용 기술, 즉 디지털 쓰레드를 절삭가공에 적용한 연구를 소개한다. 2장에서는 절삭가공을 위한 디지털 쓰레드 프레임워크 개념을 소개하고, 3장에서는 디지털 쓰레드 중 공정의 예측/분석을 위한 가상가공과 모니터링기술, 4장에서는 품질정보 관리를 위한 측정 및 표준화 연계 기술을 소개한다. 5장에서는 제안된 디지털 쓰레드를 구현하여 활용성을 검토한 내용을 설명한다.
2. 절삭가공과 디지털 쓰레드
2.1 디지털 쓰레드
디지털 쓰레드는 고려하는 대상에 따라 다양한 형태를 가질 수 있다. 서론에서 설명한 바와 같이 디지털 쓰레드는 고립된 데이터 간 연결을 바탕으로 통합된 조회 기능을 제공하기 위해 제안되었다. 제조현장에서 사용하거나 발생하는 데이터는 생성하는 주체에 따라 다양한 형태를 갖고 있고 대부분 생성된 장소에 저장되고 있다. 데이터 통합의 필요성이 강조됨에 따라 데이터를 중앙에서 관리하고자 하는 노력이 많이 이루어지고 있으나, 데이터를 모아두고 있을 뿐 각 데이터를 조회하기 위한 색인 및 데이터 간의 연계가 부족하다. 이럴 경우, 데이터 생성에 관여하지 않은 활용자가 필요한 데이터를 검색하는 데 많은 어려움을 겪게 된다. 제조현장에서 디지털 쓰레드를 구축하는 가장 큰 이유는 데이터의 재활용을 위한 토대로 활용할 수 있기 때문이다. 특히, 스마트공장에 대한 관심이 일반화됨에 따라 제조현장에서 사용되거나 생성되는 데이터를 분석하여 제조공정을 최적화기 위해 저장된 데이터를 적절하게 조회할 필요성이 높아지고 있어 데이터를 효율적으로 저장하고 조회하는 기능에 대한 필요성이 대두되고 있다. 디지털 쓰레드는 데이터 간 연계정보를 갖고 있기 때문에 임의의 데이터를 시작점으로 관련된 데이터를 모두 조회할 수 있게 해준다. 이를 통해 일반적으로 데이터를 분석할 때 필요한 원인과 결과 간의 정합성을 확보할 수 있게 된다.
2.2 절삭가공용 디지털 쓰레드
Fig. 2는 본 논문을 통해 고려하고 있는 절삭가공 분야의 디지털 쓰레드의 범위를 보여주고 있으며, 절삭가공이 이루어지는 현장에서 필요하거나 생성되는 데이터를 생성되는 순서대로 나열하고 있다.
절삭가공은 가공해야 하는 제품의 형상을 표현하는 CAD 모델에서 시작한다. CAD 모델은 가공물의 형상을 정의하기 위해 사용되는 점, 선, 면의 정보를 갖고 있으며, 추가적으로 품질 정보를 갖고 있어 향후 검사 공정과 연계하는데 활용할 수 있다.
CAM 시스템은 CAD 시스템을 통해 정의된 형상 모델을 입력받아 CNC 공작기계를 운용하는데 필요한 공구경로를 생성한다. CAM 시스템은 형상정보 이외에 공정계획이라는 중요한 정보를 필요로 한다. 공정계획은 품질과 생산성을 결정하는 중요한 요소로서 가공전략과 가공조건을 포함하고 있다. 가공전략은 황삭, 중삭 및 정삭과 같이 원소재에서 불필요한 소재를 제거하는 단계에 대한 정보를 갖고 있기도 하고, 등고선 가공이나 지그재그 가공과 같이 불필요한 소재를 제거하는 방법을 표현하고 있기도 하다. 가공조건은 불필요한 소재가 제거되는 양을 결정하는 요소인 가공 깊이와 이송속도, 추가적으로 한 번의 공구-소재 맞물림으로 제거되는 소재의 양을 결정하기 위해 필요한 스핀들 회전속도로 구성된다. 가공조건은 피삭재의 재질, 공구의 형상 및 소재 등의 정보를 바탕으로 결정된다.
CAD 시스템과 CAM 시스템에서 활용하거나 생성한 정보들은 각각의 시스템에서 정의된 전용의 형식으로 저장되기 때문에 현장에서 활용하기에 제약이 있는 경우가 많아 국제표준에 근거하여 중립적인 형태로 정보를 저장하는 방법이 활용되고 있다. 본 연구에서도 CAD 시스템과 CAM 시스템의 정보를 분석하고 저장하기 위해서 STEP 표준을 사용했으며, CAD 정보를 분석하기 위해서는 ISO 10303 AP242 표준을 이용했고, CAM 정보는 CAM 시스템이 제공하는 API를 이용해서 수집한 정보를 ISO 14649 표준에 기반하여 저장하였다.
제품의 형상정보와 공정계획정보를 이용해 생성된 공구경로는 가상가공기술을 이용해서 검증할 수 있으며, 예측된 절삭 물리량을 바탕으로 공정을 최적화하는데 활용할 수도 있다.
지금까지 설명한 데이터들은 대부분 사무실에서 생성되어 왔으나, 최근 작업현장에서 생성되는 경우가 많아지고 있다. 또한, 새롭게 갱신되는 경우도 있으나 대부분 하나의 제품과 하나의 공정을 기준으로 일회성으로 생성되는 특징이 있다. 반면 작업현장에서 가공 중에 발생하는 모니터링신호와 제품을 측정한 데이터는 제품이 가공될 때 마다 생성되는 특징이 있다.
제품을 가공할 때 수집되는 모니터링정보를 원인으로 가공된 제품의 측정값을 결과로 놓고 상관관계를 분석하는 것이 보통 과거에 모니터링기술을 활용하는 방법이었다. 본 논문을 통해 제안된 디지털 쓰레드를 통해 가상가공기술의 예측 물리량을 조회할 수 있으면, 모니터링신호와 측정값 간의 상관관계 분석에 도움이 될 것이다. 특히, 가상가공기술을 통해 공구의 이송에 따라 계산된 가공 깊이 및 가공 폭과 같은 가공조건은 추가적인 원인으로 상관관계 분석에 활용할 수 있다.
제품의 품질은 디지털 쓰레드를 구성하는 마지막 데이터로 제조공정의 결과를 보여주는 가장 중요한 데이터이다. 품질은 종류도 다양하고 측정하는 방법도 다양하며, 많은 측정기 제조사들이 전용의 형식을 이용해서 측정 데이터를 관리하고 있기 때문에 디지털 쓰레드를 구성하는 큰 걸림돌이 될 수 있다. 본 논문에서는 품질 데이터 중 ISO 10303 AP242 표준의 기하치수 및 공차(Geometric Dimensioning and Tolerancing, GD&T)를 대상으로 검사데이터를 관리하고 있다. AP242에서는 기하공차(Geometric Tolerance)가 치수공차(Dimensional Tolerance)를 포함하는 개념이지만, 국내 제조현장에서는 기하공차와 치수공차를 구분하여 이해하기도 하여, 본 논문에서는 혼동을 방지하고자 GD&T로 표현하였다.
본 논문은 제안된 절삭가공의 디지털 쓰레드 중 공구경로가 생성된 이후의 단계인 가상가공기술부터 모니터링기술 및 품질측정까지 작업현장에서 사용되고 생성되는 데이터들을 관리하는 방법에 대해 설명하고 있다.
3. 가상가공기술과 모니터링기술
3.1 가상가공기술
가상가공은 공구와 소재 간 상대운동을 통해 이루어지는 절삭가공을 컴퓨터환경에서 모사하는 시뮬레이션 기술이다. 가상가공은 절삭력 예측을 통해 공정조건을 선정하는데 주로 사용되고 있으며, 과거에 정적특성만을 고려하였으나, 최근에는 동적특성까지도 고려하여 공정조건을 최적화하는데 사용되고 있다. 또한, 가상가공기술은 공정조건을 선정하는 단계를 넘어 공구경로를 검증하고 최적화하기 위해 활용되고 있다. CAM 시스템이 생성한 원시 공구경로를 대상으로 공구의 이송에 따른 절삭력 변화를 예측하여 다양한 전략을 바탕으로 이송속도를 최적화하는 것이 일반적이며 적극적으로 공구경로 자체를 변경하는 경우도 있다. 일반적으로 가상가공기술은 실제 가공을 수행하기 전에 활용하는 기술이었으나 최근 가공을 수행하는 중에 활용하는 방법도 제안되고 있다[15].
가상가공을 수행하는 가상가공모듈은 컴퓨터의 메모리상에 수치적으로 정의된 피삭재모델과 공구모델을 이용하여 주어진 공 구경로에 의해 발생하는 피삭재와 공구간의 상대운동을 모사한다. 가상가공모듈은 이러한 상대운동을 통해 발생하는 맞물림 (Engagement) 양을 계산하고 그 결과와 절삭모델을 이용하여 절삭력 등의 절삭 물리량을 계산한다. Fig. 3은 가상가공기술을 통해 예측된 절삭력과 실가공을 통해 측정된 절삭력을 비교해서 보여주고 있다. 일반적으로 주어진 공구경로를 일정한 간격으로 분할하여 맞물림 양과 절삭 물리량을 계산하게 되며, 본 논문에서는 가상가공모듈에서 생성한 공구의 이송거리에 따른 피삭재-공구간 맞물림 양과 절삭 물리량을 JSON (Javascript Object Notation) 형식으로 저장하고 조회할 수 있게 가상가공데이터를 관리하도록 구현했다.
3.2 모니터링기술
절삭가공은 국소적으로 과도한 힘이 걸림에도 불구하고 절삭현상이 이루어지는 부분을 실시간으로 직접 확인할 방법이 제한적이기 때문에, 절삭가공을 대상으로 연구하는 연구자들은 대부분 자연스럽게 모니터링기술에 관심을 갖게 된다. 절삭가공을 모니터링하기 위해서 다양한 센서들이 현장에서 활용되고 있다. 절삭가공 모니터링의 대상이 되는 물리량은 적절하게 선정된 센서를 통해 전기신호로 변환되고 변환된 전기신호를 다시 사람, 혹은 컴퓨터가 처리할 수 있는 정보, 일반적으로 숫자로 변환시켜 활용하게 된다. 절삭가공은 대부분 공작기계가 수행하게 되며, 최근의 공작기계는 대부분 CNC를 탑재하고 있다. CNC는 공작기계를 제어하는 핵심 부품으로 공작기계 현재 상태에 대한 다양한 정보를 갖고 있다. CNC가 내부에서 관리하는 정보는 CNC 제조사가 공작기계 제조사를 위해 다양한 방법으로 제공하고 있는데, 그 방법은 CNC 제조사에 따라 다르고 같은 제조사의 경우도 모델에 따라 다른 경우도 있다. 과거에는 공작기계 제조사만 CNC의 내부 정보를 활용하였으나, 공정 모니터링에 대한 관심이 높아짐에 따라 다양한 주체들이 CNC의 정보를 요구하게 되었으며, 이에 따라 CNC 제조사들도 자체적으로 관리하던 내부 정보들을 개방하고 있다. 그러나, 제조현장에는 필요에 따라 제조사와 모델이 서로 다른 다양한 CNC가 활용되기 때문에, 공작기계를 모니터링하기 위해서는 CNC 제조사가 제공하는 서로 다른 방법을 이용해야만 했다. 이러한 문제는 자연스럽게 일원화된 CNC 인터페이스에 대한 요구로 이어졌으며 현재 대한민국에는 TORUS라는 HMI 플랫폼이 공개되어 활용되고 있다[16]. 본 논문에서 활용한 공작기계 모니터링시스템 중 정보를 수집하는 모듈은 2개의 세부 모듈로 구성되는데, TORUS를 이용해서 개발한 CNC 정보 수집 모듈과 NI 사의 DAQ와 라이브러리를 이용해서 개발한 센서 신호 수집 모듈이다. Fig. 4는 한국생산기술연구원에서 개발한 절삭가공 모니터링시스템으로 연구에 활용할 목적으로 가능한 많은 정보를 수집하기 위해 설계되었다. 개발된 모니터링시스템은 TORUS를 이용한 CNC와의 통신을 통해 공구의 이송과 관련한 대부분의 CNC 정보를 수집하고 있으며, 공구동력계, 가속도계, 전류/전압계, 마이크 등 공작기계 모니터링을 위해 사용되는 대부분의 센서를 이용할 수 있도록 DAQ를 선정하여 절삭력, 진동, 소음 및 각종 모터에 공급되는 전압/전류를 측정할 수 있게 구성했다. 절삭력은 절삭가공과 관련된 물리량 중 가장 중요한 정보로 공구동력계를 이용해서 측정하는 것이 가장 정확하다고 알려져 있으나, 비용 및 공간상의 제약으로 작업 현장에서의 활용에 제한적이기 때문에, 비교적 손쉽게 사용할 수 있는 다른 센서들을 이용해서 절삭력을 추정(Reconstruction)하는 연구들이 많이 소개되고 있다[17,18]. Fig. 5는 공작기계의 스핀들 모터에 공급되는 전류값으로 추정한 절삭력과 공구동력계를 이용해서 측정한 절삭력을 비교해서 보여주고 있다.
3.3 가상가공기술과 모니터링기술의 통합
절삭가공 분야에서 가상가공기술은 공구의 이송에 따른 물리량을 예측하는 기술이고 모니터링기술은 공구의 이송에 따른 물리량을 측정, 혹은 추정하는 기술이다. 본 논문은 현장에서의 활용성을 높이기 위해서 측정된 절삭력을 활용하지 않고 추정된 절삭력을 활용하여 수행되었다. Fig. 6은 예측 물리량과 추정물리량을 통합하는 원리를 보여주고 있다. 가상가공기술을 통해 생성된 물리량은 가공거리를 기준으로 저장되어 있다. 즉, 공구의 이송거리에 따른 다양한 기하량과 물리량 정보를 갖고 있다. 모니터링기술을 통해서 추정된 물리량은 시간을 기준으로 생성된다. 예측값과 추정값을 동기화하기 위해서 모니터링시스템에서 수집하는 CNC 정보를 활용하였다. 예측된 물리량은 공간에 대한 정보를 함께 갖고 있고, 추정된 물리량은 시간에 대한 정보를 함께 갖고 있는데, CNC 정보는 공간과 시간에 대한 정보를 모두 갖고 있기 때문 예측값과 추정값을 동기화하는데 기준으로 활용할 수 있다. 예측값은 공간상의 오차가 있고, CNC 통신의 예측 불가능한 약 0.1초 이내의 시간 지연에 따른 시간/공간의 오차로 인해 동기화의 오류가 발생할 가능성이 있으나, 예측값의 공간 분해능을 높이고 CNC 통신의 속도를 일정 수준으로 유지한다면, 동기화 오차는 공구의 이송속도를 고려하여 예측 가능한 수준으로 관리할 수 있다.
예측된 물리량과 추정된 물리량을 동기화해서 비교하면 다양한 기능을 수행할 수 있다. 우선, 절삭력을 예측하기 위해 사용하는 절삭계수를 현장 상황에 맞게 최적화할 수 있다[19]. 또한, 예측된 값과 추정된 값에 일정 수준 이상의 오차가 발생한 경우 공구 마모/파손 및 소재 장착 불량 등의 공정 이상을 검출할 수도 있어, 이에 대한 연구가 활발하게 이루어지고 있다.
4. 품질 검사
4.1 품질과 제조의 디지털 쓰레드
모델 기반 기업활동(Model Based Enterprise, MBE)은 제품의 3D 형상을 제품 수명 주기 전체에서 사용하는 것이며, 설계 형상 외에도 GD&T, 소재 사양, 부품 리스트, 공정 사양 등을 포함하는 개념이다[20]. 디지털 쓰레드는 이러한 모델 기반의 정의, 제조 및 검사를 결합하는 데이터의 총체(Ensemble)를 정의할 수 있으며, 전체 프로세스의 추적성을 높이는데 효과적으로 활용된다[21]. 부품의 품질 정보와 검사 결과는 설계-제조-검사 에 대한 제조산업 디지털 쓰레드의 결과 데이터로써 중요하며, ISO/TC184/SC4에서는 이러한 검사 결과를 포함하여 품질정보의 상호 운용성을 높이기 위한 프레임워크를 ISO 23952로 표준화하고 있다[22]. 본 논문에서는 GD&T 검사 결과를 절삭가공후 부품의 품질을 나타내는 지표로 선정하였고, 기계상 측정(On-machine Measurement, OMM)으로 취득한 좌표데이터를 이용하여 GD&T 결과를 연산한다. 또한, 품질 검사의 디지털쓰레드를 위해서 CAD 정보, GD&T 정보, GD&T 검사 결과가 상호 조회될 수 있는 데이터 구조를 설계하였다. 검사 데이터는 실제 가공된 형상에 대한 정보 제공 외에도 3절의 가상가공 및 모니터링 데이터와 연계하여 예측 모델을 보완하는 참조데이터로도 활용할 수 있다.
4.2 디지털 쓰레드를 위한 표준화 CAD 정보 데이터
부품의 솔리드 모델은 CATIA, NX UG, SolidWorks 등 다양한 CAD 프로그램에서 작성되며, 일반적으로 객체를 면(Surface)의 집합으로 표현하는 B-Rep (Boundary Representation)으로 설계된다[23]. ISO 10303은 각 CAD 프로그램의 모델링 데이터 간 호환이 어려운 문제를 해결하고자 제정된 표준으로, 제품 모델 데이터 교환을 위한 표준화된 데이터 형식이다[24]. 특히 ISO 10303AP242는 Fig. 7과 같이 3차원 형상정보뿐만 아니라 모델기반(Model Based Definition, MBD)으로 제품 및 제조정보(Product & Manufacturing Information, PMI), 공정계획(Process Plans) 등을 포함하고 있다[25]. 본 연구에서는 CAD 프로그램에 중립적인 디지털 쓰레드 구축을 위해서 AP242를 기준으로 하였고, AP242의 CAD 정보와 GD&T 정보를 추출하여 데이터화하는데 활용하였다.
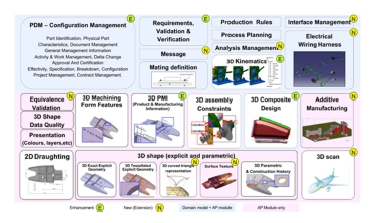
Overview of ISO 10303 STEP AP242 edition 2 “Managed model based 3D engineering” [26] (Adapted from Ref. 26 on the basis of website)
CAD 형상정보는 AP242 스키마에 의거하여 Fig. 8과 같이 B-Rep의 정의로부터 상호 참조관계를 통해 형상을 정의하는 점과 법선 벡터까지 연결되어 있다. 품질과 설계의 디지털 쓰레드를 위해서 상호 참조를 위한 기준 특성(Feature)의 정의가 필수적으로 설정되어야 하고, 본 연구에서는 AP242의 GD&T에서 지정하는 기하 특성인 ‘ADVANCED_FACE’로 결정하였다. 이 특성은 면의 범위(Face Bound)를 정의하여 기본 구성단위인 점과 법선 벡터를 결정한다. AP242 규격 파일(STP)을 입력하면 CAD 정보 데이터는 ‘ADVANCED_FACE’ 정보를 포함하여 Fig. 9(a)와 같은 데이터 구조로 디지털 쓰레드 조회 모듈로 전송되며, 전송 형식은 데이터 교환에 용이한 개방형 표준 형식인 JSON으로 선정했다.
4.3 디지털 쓰레드를 위한 GD&T 데이터
절삭가공 부품의 품질 검사 데이터를 절삭가공 디지털 쓰레드와 연계하기 위해, 본 연구에서는 AP242를 기반으로 GD&T 정보와 검사 결과를 저장하는 데이터 구조를 설계하였다. 제조현장에서 부품의 GD&T 검사 데이터는 3차원측정기(Coordinate Measuring Machine, CMM), 기계상 측정, 머신 비전(Machine Vision) 등을 통해 취득되며, 본 연구에서는 검사 절차의 간소함을 위해 터치프로브 기반의 기계상 측정 모듈을 통해 측정된 GD&T 검사 결과를 디지털 쓰레드에 연계할 수 있게 제공하였다.
치수공차는 ‘DIMENSIONAL_CHARACTERISTIC_REPRESENTATION’정보로부터 해당 GD&T를 참조하도록 하였다. GD&T는 Table 1과 같이 분류되고, 데이텀(Datum) 유무에 따라서 구분하여 참조하도록 하였다. GD&T 정보 데이터는 AP242의 GD&T 및 참조 정보로부터 공차의 표현, 크기, 대상 기하 특성을 각 공차 항목마다 저장되도록 하였고, Fig. 9(b)와 같이 데이터 구조를 수립하였다. 데이텀이 필요한 GD&T인 경우, 각 공차 항목은 데이텀에 대한 정의와 기하 특성을 참조하여 GD&T정보 데이터에 포함시킨다.
공작기계에서 기계상 측정을 통한 GD&T 검사 결과는 Fig. 10과 같은 절차로 디지털 쓰레드 조회 모듈로 전송된다. 측정되는 대상 점 위치는 GD&T 정보로부터 정의된 공차와 CAD 형상 정보에 의해 면이 결정되면, 사전에 설정한 GD&T별 측정점 개수를 고려하여 결정한다. 프로브 충돌을 방지하기 위한 안전거리, 접근거리 등 측정관련 설정 정보와 결정된 측정 점 위치 정보를 통해 측정경로가 생성된다. 생성된 측정 경로를 CNC 공작기계에 입력하여 실행하면, 해당 점의 측정된 3차원 좌표데이터가 유저 변수(User Variable) 저장 또는 직접 통신을 통해 취득된다. GD&T 검사 결과는 이 좌표 데이터와 공차별 계산식에 따라 연산된다. GD&T 검사 결과 데이터는 Fig. 9(c)와 같이 연관된 CAD 정보와 GD&T 정보를 참조하여 디지털 쓰레드 조회 모듈에 전달될 수 있도록 식별자를 부여하였다. 이 검사 데이터는 GD&T 검사 대상 점 및 측정된 좌표, 데이텀 측정 대상점 및 측정된 좌표와 GD&T 계산 결과를 포함한다. ISO23952에서는 이러한 품질 검사에 대한 결과뿐 아니라 계획, 실행, 통계 등을 QIF (Quality Information Framework) 형식으로 범용적 데이터 교환이 되도록 표준화하고 있고, AP242와 비교 및 연계를 위한 연구도 진행되고 있다[27].
5. 절삭가공 디지털 쓰레드 구현
본 논문에서 제안한 절삭가공 분야의 디지털 쓰레드 프레임워크의 기능을 검토하기 위해 디지털 쓰레드 조회 및 가시화 모듈을 구현했다. 제안된 디지털 쓰레드 프레임워크를 통해 관리되는 정보는 생성 순서대로 품질정보가 포함된 CAD 정보, CAM 정보, 가상가공정보, 모니터링정보 및 측정 정보이다. 공작기계의 기계능력지수를 평가하기 위해 사용되는 KS B ISO 10791-7을 참조하여 NX UG를 활용하여 대상 모델을 설계하였고, 진직도(Straightness)와 경사도 (Angularity)를 GD&T 정보로 삽입한 후 AP242 규격으로 저장하였다. NX CAM을 활용하여 공구경로를 생성하였으며, 한국생산기술연구원이 보유한 가상가공기술을 활용하여 절삭 물리량을 생성하였다.
Fig. 11은 개발된 가시화 모듈을 보여주고 있다. 프로젝트의 간단한 설명부터 CAD, CAM, GD&T, 가상가공 데이터 및 모니터링 데이터를 선택하여 가시화할 수 있으며, 하단의 세부 정보창을 통해 자세한 정보를 조회할 수 있다. Fig. 11은 황삭 가공경로를 대상으로 가상가공기술을 통해 예측한 절삭토크의 크기를 색으로 비교하여 보여주고 있다.
Fig. 12는 품질 검사 데이터 모델을 검증하는 순서를 보여주고 있다. 개발된 AP242 규격 파일 해석 모듈을 이용하여 CAD와 품질 정보 데이터를 추출하였으며, CAD 및 GD&T 정보 데이터와 앞서 제안한 검사 절차를 통해 측정을 위한 터치프로브 이송경로를 생성하였다. 절삭가공 공정이 완료된 직후 절삭공구를 대신해 장착된 터치프로브가 측정 경로를 따라 이송하며 기계상에서 좌표를 측정하였다. 측정된 좌표를 이용하여 진직도 및 경사도를 계산한 후 디지털 쓰레드 프레임워크에 전달하였다. 총 8개의 제품에 대해 측정이 이루어졌으며, Fig. 13은 경사도 검사 결과를 보여주고 있다. 경사도이기 때문에 데이텀이 필요하며, 목표치가 0.01 mm인데 측정값이 0.05 mm 이상이기 때문에 빨간색으로 표기되었다.
6. 결론
디지털 쓰레드는 디지털 트윈과 함께 절삭가공 기반 산업의제조현장의 디지털 전환을 위한 핵심 기술이다. 본 연구에서는 절삭가공 기반 제조현장의 전주기에서 발생하는 데이터의 상호운용성(Interoperability)을 제고하기 위해 CAD, CAM, 가상가공, 공정 모니터링, 검사로 이어지는 절삭가공 디지털 쓰레드 프레임워크를 제안하였다. 이를 구현하기 위한 디지털 쓰레드 조회모듈을 개발하여 3차원 CAD 모델을 시작으로 가상가공, 모니터링, 검사 데이터가 상호 참조되어 조회될 수 있는 것을 확인할 수 있었다. 가상가공, 모니터링 및 측정 데이터를 위치상으로 동기화하고 분석하여 상호 간 연관성을 규명하는 연구가 추가로 진행 중이다. 더불어 가공품의 품질을 결정하는 주요 요인 중 하나인 공구마모를 관리하는 방안에 대해서도 고려하고 있다.
국제표준인 AP242 형식으로 저장된 형상정보와 품질정보를 기반으로 절삭가공 현장에서 필요하거나 생성되는 정보를 관리하였다. 이때, 정보 관리의 기준은 각 제조 단계에서 공정 행위가 이루어지는 면(Surface)으로 하였다. 가상가공 데이터와 모니터링 데이터를 동기화하여 예측치와 추정치 간 비교 분석을 가능하도록 하였으며, 일원화된 CNC 통신 방식을 적용하여 CNC 의존성을 낮추었다. 가공 직후 기계상에서 측정된 GD&T 검사데이터를 제품별, 품질별로 조회하는 것도 가능하다. 공구경로생성에 필요한 가공전략 및 가공조건을 ISO 14649를 기반으로 저장하는 모듈은 개발하였으나, 상용 모듈을 활용해서 공구경로를 생성할 때 AP242의 면정보가 변경되는 점은 향후 해결해야 하는 과제이다. 서로 다른 식별자로 저장된 면을 일치시키는 형상모델링 분야의 다양한 방법을 검토하여 적용할 예정이다. 국내 산업현장에서는 여전히 2D 도면으로 GD&T를 관리하고 있고, 3D 모델 기반의 GD&T 표현과 검사가 보편화되지 않고 있다. 하지만, 3D 모델 기반의 GD&T 표현은 자동으로 공차정보가 기입된 2D 도면을 생성하거나 CMM 측정 경로를 생성하는 데 활용될 수 있으며, 3차원 CAD 활용 비중이 높은 상황을 고려할 때, 가까운 미래에 보편화될 것으로 예상된다.
제안된 디지털 쓰레드는 범용성을 확보하기 위해 국제표준을 기반으로 데이터를 관리하였으나, 작업현장에서 활용되는 대부분의 CAD/CAM 및 측정 솔루션은 저마다의 방식으로 데이터를 관리하고 국제표준은 데이터 교환을 위해 최소한으로 활용되고 있으며, 가상가공이나 모니터링데이터는 표준으로 논의되고 있지도 않는 단계라는 점이 디지털 쓰레드를 적용할 때 걸림돌이 될 수 있다. 그러나, 디지털전환의 큰 흐름속에 데이터 간 상호 참조가 가능한 디지털 쓰레드에 대한 현장의 요구는 계속해서 높아질 것이며 다양한 방법으로 해결 방안이 제시될 것으로 예상된다.
Acknowledgments
본 논문은 한국생산기술연구원 “[Key-Tech] DNA 플랫폼 기반 자율제조 기술(1/5) (kitech EH-23-0006)”의 지원으로 수행한 연구입니다.
REFERENCES
-
Jones, M. D., Hutcheson, S., Camba, J. D., (2021), Past, present, and future barriers to digital transformation in manufacturing: A review, Journal of Manufacturing Systems, 60, 936-948.
[https://doi.org/10.1016/j.jmsy.2021.03.006]
-
Vial, G., (2019), Understanding digital transformation: A review and a research agenda, The Journal of Strategic Information Systems, 28(2), 118-144.
[https://doi.org/10.1016/j.jsis.2019.01.003]
-
Singh, M., Fuenmayor, E., Hinchy, E. P., Qiao, Y., Murray, N., Devine, D., (2021), Digital twin: Origin to future, Applied System Innovation, 4(2), 36.
[https://doi.org/10.3390/asi4020036]
- ISO23247-1, (2021), Automation systems and integration–Digital twin framework for manufacturing–Part 1: Overview and general principles.
-
Kritzinger, W., Karner, M., Traar, G., Henjes, J., Sihn, W., (2018), Digital twin in manufacturing: A categorical literature review and classification, Ifac-PapersOnLine, 51(11), 1016-1022.
[https://doi.org/10.1016/j.ifacol.2018.08.474]
-
Grieves, M., Vickers, J., (2017), Digital twin: Mitigating unpredictable, undesirable emergent behavior in complex systems, Transdisciplinary perspectives on complex systems: New findings and approaches, 85-113.
[https://doi.org/10.1007/978-3-319-38756-7_4]
-
Negri, E., Fumagalli, L., Macchi, M., (2017), A review of the roles of digital twin in CPS-based production systems, Procedia Manufacturing, 11, 939-948.
[https://doi.org/10.1016/j.promfg.2017.07.198]
- Leiva, C., (2016), Demystifying the digital thread and digital twin concepts, IndustryWeek. https://info.ibaset.com/hubfs/Demystifying_the_Digital_Thread_and_Digital_Twin.pdf
-
Singh, V., Willcox, K. E., (2018), Engineering design with digital thread, AIAA Journal, 56(11), 4515-4528.
[https://doi.org/10.2514/1.J057255]
-
Zhang, Q., Zheng, S., Yu, C., Wang, Q., Ke, Y., (2022), Digital thread-based modeling of digital twin framework for the aircraft assembly system, Journal of Manufacturing Systems, 65, 406-420.
[https://doi.org/10.1016/j.jmsy.2022.10.004]
-
Jagusch, K., Sender, J., Jericho, D., Flügge, W., (2021), Digital thread in shipbuilding as a prerequisite for the digital twin, Procedia CIRP, 104, 318-323.
[https://doi.org/10.1016/j.procir.2021.11.054]
-
Feldhausen, T., Saleeby, K., Kurfess, T., (2021), Spinning the digital thread with hybrid manufacturing, Manufacturing Letters, 29, 15-18.
[https://doi.org/10.1016/j.mfglet.2021.05.003]
-
Qiao, Q., Wang, J., Ye, L., Gao, R. X., (2019), Digital twin for machining tool condition prediction, Procedia CIRP, 81, 1388-1393.
[https://doi.org/10.1016/j.procir.2019.04.049]
-
Armendia, M., Cugnon, F., Berglind, L., Ozturk, E., Gil, G., Selmi, J., Evaluation of machine tool digital twin for machining operation in industrial environment, Procedia CIRP, 82, 231-236.
[https://doi.org/10.1016/j.procir.2019.04.040]
-
Altintas, Y., Aslan, D., (2017), Integration of virtual and on-line machining process control and monitoring, CIRP Annals, 66(1), 349-352.
[https://doi.org/10.1016/j.cirp.2017.04.047]
- TORUS. HMI platform product. http://www.torus.co.kr/product_list.html.php
-
Kim, J., Yoon, J., Lee, D., (2019), Estimation of tangential cutting force using spindle load of CNC machining center, Journal of the Korean Society of Manufacturing Technology Engineers, 28(6), 343-349.
[https://doi.org/10.7735/ksmte.2019.28.6.343]
-
Mostaghimi, H., Park, C. I., Kang, G., Park, S. S., Lee, D. Y., (2021), Reconstruction of cutting forces through fusion of accelerometer and spindle current signals, Journal of Manufacturing Processes, 68, 990-1003.
[https://doi.org/10.1016/j.jmapro.2021.06.007]
-
Kang, G., Kim, J., Choi, Y., Lee, D. Y., (2022), In-process identification of the cutting force coefficients in milling based on a virtual machining model, International Journal of Precision Engineering and Manufacturing, 23(8), 839-851.
[https://doi.org/10.1007/s12541-022-00677-4]
- Lubell, J., Chen, K., Horst, J., Frechette, S., Huang, P., (2012), Model based enterprise/technical data package summit report, NIST Technical Note.
-
Hedberg, T., Lubell, J., Fischer, L., Maggiano, L., Barnard Feeney, A., (2016), Testing the digital thread in support of model-based manufacturing and inspection, Journal of Computing and Information Science in Engineering, 16(2).
[https://doi.org/10.1115/1.4032697]
- ISO23952. (2020), Automation systems and integration-Quality information framework (QIF)-An integrated model for manufacturing quality information.
-
Lienhardt, P., (1991), Topological models for boundary representation: A comparison with n-dimensional generalized maps, Computer-aided Design, 23(1), 59-82.
[https://doi.org/10.1016/0010-4485(91)90082-8]
- ISO10303-1, (2021), Industrial automation systems and integration-Product data representation and exchange-Part 1: Overview and fundamental principles.
- ISO10303-242, (2020), Industrial automation systems and integration-Product data representation and exchange-Part 242: Application protocol: Managed model-based 3D engineering.
- STEP AP242 Project, AP242 Ed2. http://www.ap242.org/edition-2/
- Heysiattalab, S., Morse, E. P., (2016), From STEP to QIF: Product and manufacturing information, Proceedings of the 31th American Society of Plumbing Engineers Annual Meeting, 312-317.
Senior Researcher in the Precision Mechanical Process and Control R&D Group, Korea Institute of Industrial Technology. His research interest is machine tool metrology and precision process control.
E-mail: hhlee84@kitech.re.kr
Principal Researcher in the Digital Transformation R&D Department, Korea Institute of Industrial Technology. His current research topics are in-process monitoring/control using CNC communication and sensors, virtual machining, and process optimization.
E-mail: dylee@kitech.re.kr