
Superhydrophilic Modification of a Polypropylene Depth Filter for Efficient Oil–water Separation

Copyright © The Korean Society for Precision Engineering
This is an Open-Access article distributed under the terms of the Creative Commons Attribution Non-Commercial License (http://creativecommons.org/licenses/by-nc/3.0) which permits unrestricted non-commercial use, distribution, and reproduction in any medium, provided the original work is properly cited.
Abstract
Purification of water through oil–water separation is essential for preserving the ecosystem and protecting human health. Although a conventional polypropylene depth filter can effectively purify water, modifying the wettability of a filter for oil–water separation is difficult owing to its low reactivity. In this study, we developed a superhydrophilic polypropylene filter with a hydrogel layer that could enable effective oil–water separation by using plasma treatment and dip coating, which enabled an even distribution of the coating solution across the filter. The fabricated filter was superhydrophilic with a water contact angle of 0o. It showed a high repulsive force with oil in water with an underwater oil contact angle of 142.9o. When such filter was applied to an oil–water separation device, it effectively purified water with low oil content (< 15 ppm) at a flow rate of 300 mL/min. These results demonstrate potential applications of such filters in areas such as wastewater treatment and oil spill cleanup.
Keywords:
Superhydrophilic, Polypropylene, Depth filter, Plasma treatment, Dip coating, Oil–water separation키워드:
극친수성, 폴리프로필렌, 심층 필터, 플라즈마 처리, 딥 코팅, 유수분리1. Introduction
Oil–water separation is a crucial process in several industrial and environmental applications. The mixing of oil and water in industrial processes can lead to severe issues, such as equipment corrosion, contamination, and reduced efficiency, resulting in increased operational costs and environmental hazards. Furthermore, industrial and domestic wastewater, and marine oil spills can severely pollute the environment and adversely affect human health and ecosystems [1-5]. Therefore, efficient and sustainable oil–water separation technologies must be developed to meet the growing demand for clean water and protect the environment.
In recent years, superhydrophilic and superhydrophobic surfaces have gained significant attention in the field of oil–water separation [6-14]. Superhydrophilic surfaces have a high affinity for water, allowing the water to spread and form a thin film while repelling oil. In contrast, hydrophobic surfaces have a low affinity for water and a high affinity for oil, forming an oil layer on the surface to repel water. Various methods can be used to produce extremely hydrophilic and hydrophobic surfaces, such as changing the surface roughness of a substrate or applying a wettability modification coating.
Depth filters, which are commercially used to remove impurities from wastewater, comprise tens to hundreds of porous layers. Depth filters are more resistant to impurity penetration and show superior filtering performance at higher pressures than single-membrane filters [15]. However, they are usually made of polypropylene or polyethylene, which have low surface energy and reactivity [16]. Consequently, modifying their surface wettability is difficult. Recently, an extremely hydrophilic depth filter with a polyacrylamide (PAM) hydrogel coating was fabricated by physically coating polyimide(PI) on the depth filter and chemically bonding it with 1-methyl-2-pyrrolidone(NMP)/N′ -dicyclohexylcarbodiimide(DCC) and acrylamide(Am) [17]. However, PI and NMP/DCC have harmful effects on the human body and require several hours to fabricate.
This study presents a superhydrophilic filter that can be quickly fabricated without the use of harmful chemicals. Plasma treatment was used to increase the surface energy of the polypropylene-based depth filter. Subsequently, a hydrogel layer was formed through PAM polymerization to produce an extremely hydrophilic depth filter. The fabricated filter had a contact angle of 0o with water and showed a high repulsive force with oil in water with an underwater oil contact angle of 142.9o. By applying this filter to a continuous oil–water separation device, an oil–water separation device that can continuously separate water and oil was manufactured; the amount of oil in the water was less than 15 ppm up to a flow rate of 300 mL/min. These results show that the developed filter has a high economic and environmental value and can quickly separate clean water in various industries and environments where oil–water separation is necessary.
2. Experimental Section
2.1 Materials
The polypropylene depth filter (with a nominal pore size of 10 μm) used in this study was obtained from CS Technofil Co. Ltd. (Korea). N,N′-methylenebisacrylamide (BIS) and ammonium persulfate (APS) were purchased from Samchun Chemical (Korea), while Oil Red O was obtained from Sigma-Aldrich (USA). Diesel was purchased from SK Energy (Seoul, South Korea).
2.2 Fabrication of the Superhydrophilic Filter
To increase the surface energy of the hydrophobic polypropylene filter, plasma treatment was performed before coating a PAM hydrogel layer onto the depth filter. The AP-300 Plasma System (Nordson, U.S.) was used for plasma treatment; the reactor's internal pressure and discharge power set to 80 mTorr and 150 W, respectively. The treatment time was 6 min, and the oxygen supply rate was set to 20 sccm. After the plasma treatment, the polypropylene filter was immersed in a 65oC coating solution (with 60 mM BIS and 90 mM APS) for 1 h. Finally, the treated filter was washed three times with deionized water and dried in an oven at 65oC.
2.3 Characterization
The surface morphologies were observed using field-emission scanning electron microscopy (SEM; SU6600, Hitachi, Japan), and the surface chemical compositions were analyzed using Fourier transform infrared spectroscopy (FT-IR; Nicolet iS50, Thermo Fisher Scientific Co., USA). The water contact angles and underwater oil contact angles were measured using a contact angle analysis device (SmartDrop, Femtofab Co., Korea), and the reported water and oil contact angles were the average values of five experimental points. Diesel was used as the oil layer in all the experiments. Each filter was treated with 2 L of an oil–water mixture (at a ratio of 1:4 v/v) at various flow rates. An oil–water separation device consisting of a peristaltic pump (WT600-1F, Dongbang Hitech Inc., Korea), pressure controller (PCR series, Alicat Scientific, USA), differential pressure transmitters (HN35, Nuritech, Korea), pressure indicators (PD1, Nuritech, Korea), and flow control valves (HF 400S, Tokimec, Korea) was constructed to treat large amounts of oil–water mixtures. The flow rate of the oil–water mixture was regulated using a peristaltic pump (100 mL/min). The oil content of the samples was determined using a total organic carbon analyzer (TOC-L, Shimadzu, Japan), whereas the water content was measured using a coulometric KF titrator (C10S, Mettler Toledo, Switzerland).
3. Results and Discussion
3.1 Fabrication of the Superhydrophilic Depth Filter
Figure 1(a) illustrates the fabrication method of the polypropylene filter with the polyacrylamide-based hydrogel layer. First, the polypropylene depth filter was treated with plasma to increase its wettability for deep coating. Figures 1b and 1c show the SEM images of the filters treated with pristine and O2 plasma (OP), respectively. The surface of the filter fiber does not significantly change after plasma treatment. Subsequently, the OP-treated filter was dip-coated in a solution containing APS (a radical source) and BIS (a crosslinker). The alkene moieties of BIS are radical initiators, and radical polymerization occurs via APS. During polymerization, hydrophilic polymer groups surrounded and coated the filter fibers, resulting in a well-coated hydrophilic on the filter surface, as shown in Figure 1(d).
3.2 Wetting Characteristics of a Superhydrophilic Depth Filter
The surface components of the substrate were analyzed using FTIR before and after coating with PAM. New peaks at 1538 (C = O), 1652 (C = O), and 3296 cm−1 (N-H) were observed after PAM coating, in contrast to the pristine state, indicating the successful coating of hydrophilic groups on the filter surface (Fig. 2(a)).
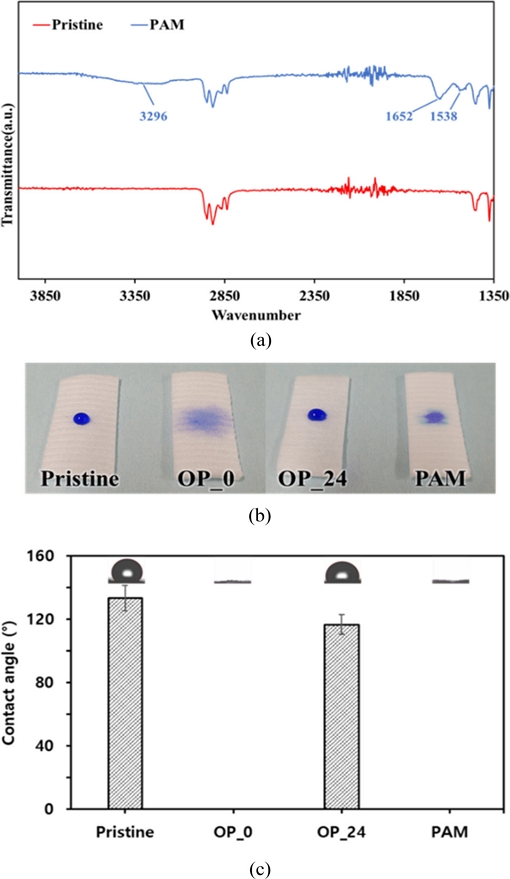
(a) FT-IR spectra of the pristine- and PAM-treated surfaces. (b) Photograph of water droplets during the coating process. (c) Changes in the water contact angle of the filter surface during the coating process
Water contact angles were measured on the filter surface at various fabrication stages. The pristine filter showed high hydrophobicity with a contact angle of 133.4±8.0o owing to the hydrophobic nature of polypropylene and the micro-sized filter fibers. After OP treatment, the contact angle of the filter (OP_0) was measured to be 0o owing to the formation of temporary OH groups on the filter surface, which can be attributed to the plasma. However, the hydrophilic property imparted to the filter by plasma treatment was unstable, and the contact angle after 24 h of plasma treatment was 116.6±6.3o, indicating a partial restoration of the hydrophobicity observed before plasma treatment [18,19]. In the case of the filter with the PAM hydrogel layer formed after plasma treatment, superhydrophilicity with a contact angel of 0o was observed, possibly because of the hydrophilic nature of the microstructured fibers and PAM-modified filter. Furthermore, the PAM-modified filter had an underwater oil contact angle of 142.9±7.0o and exhibited a high repulsive force with oil in water.
3.3 Importance of Plasma Treatment
To investigate the effect of plasma treatment on hydrogel coating, we compared filters that were deep-coated with and without plasma treatment. Figures 3(a), 3(b) water droplets on the filters without and with plasma treatment, respectively. We compared their wettability by dropping blue dye on the outside and inside of the filter surfaces. Both filters showed a good hydrophilic coating on the outer surface. However, the filter without plasma treatment showed hydrophobicity on the inside because of the inability of the coating solution to penetrate the filter fibers owing to the hydrophobic nature of polypropylene. Moreover, the SEM image of the filter without plasma treatment suggest that the PAM hydrogel material was barely coated (Figure 3(c)). In contrast, the filter with plasma treatment showed an evenly distributed hydrogel coating on the filter fibers, thereby confirming the necessity of plasma treatment for an evenly coated hydrophilic depth filter.
3.4 Oil–water Separation Using a Superhydrophilic Filter
To evaluate the performance of oil-water separation in a continuous oil–water separation system, the system was designed as depicted in Figure 4. The oil-water mixture is pumped into filter housing 1, and purified water is discharged through a superhydrophilic depth filter. The pressure controller maintains pressure on the hydrophilic filter and discharges the accumulated oil to the top. The oil is purified by the superhydrophobic glass fiber (GF) filter in filter housing 2. To fabricate the superhydrophobic GF filter, GF filter was plasma-treated and coated with octadecyltrichlorosilane using a previously reported method [20]. The mixture that is not filtered by the superhydrophilic PAM and GF filters returns to the original oil–water mixture via the return pipe. The fluid undergoes a circulation process in the system, and returns to the original oil–water mixture through the return pipe, thereby continuously separating water and oil.
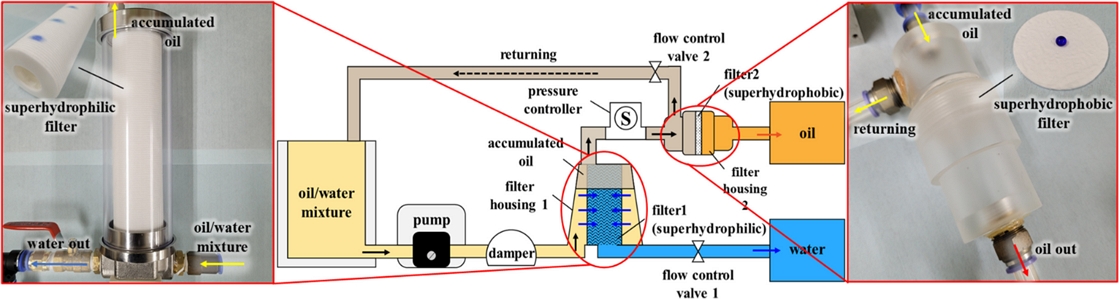
Schematic of the oil-water separation device composed of a superhydrophilic and superhydrophobic filter
An actual photograph of the oil–water separation system is presented in Figure 5(a). In this experiment, the oil–water mixture was separated into water and oil at various flow rates, and the purities of water and oil were measured when 1 L of water and 250 mL of oil were produced. The oil–water mixture before separation and the separated water and oil are shown in Figure 5(b). The purified water had a purity of 5.46 ppm at 100 mL/min, 8.27 ppm at 200 mL/min, and 14.02 ppm at 300 mL/min, demonstrating an excellent separation performance of less than 15 ppm. Additionally, the oil was continuously separated with high purity, with 35.60 ppm at 100 mL/min, 50.04 ppm at 200 mL/min, and 69.82 ppm at 300 mL/min. Therefore, the proposed system based on a superhydrophilic depth filter is suitable for oil–water separation in various applications.
4. Conclusions
In this study, we successfully developed a superhydrophilic depth filter based on PAM hydrogel coating treated with O2 plasma (OP) and applied it to an oil–water separation system to obtain high-purity water and oil. Plasma treatment and hydrogel coating showed excellent performances in modifying the wettability of the polymer surface; however, the plasma treatment yielded a temporary coating, while hydrogel coating was not adequately deep. However, when plasma treatment and dip coating were simultaneously performed, excellent hydrophilic properties were imparted to both the inside and outside of the hydrophobic depth filter; thus, an oil–water separation system was developed using this filter. Because the mixture before separation in this study had more water than oil, a large amount of water was primarily removed by the superhydrophilic depth filter. However, if the proportion of oil is greater than that of water, the separation rate may decrease or the content of oil in the separated water may increase. Therefore, if a superhydrophobic depth filter is developed and an oil–water separation system employing the superhydrophilic depth filter is formed, a system capable of selectively and quickly separating high-purity water and oil regardless of the ratio of water to oil can be developed. We expect this oil–water separation system based on wettability-modified depth filters to be applied in various industrial and environmental fields, such as wastewater treatment and marine oil spills.
Acknowledgments
This work was financially supported by the National Research Foundation of Korea (NRF) grant funded by the Korea government (MSIT) (NRF-2021R1A2C2008600).
REFERENCES
-
Adham, S., Hussain, A., Minier-Matar, J., Janson, A., Sharma, R., (2018), Membrane applications and opportunities for water management in the oil & gas industry, Desalination, 440, 2-17.
[https://doi.org/10.1016/j.desal.2018.01.030]
-
Joye, S. B., (2015), Deepwater horizon, 5 years on, Science, 349(6248), 592-593.
[https://doi.org/10.1126/science.aab4133]
-
Atlas, R. M., Hazen, T. C., (2011), Oil biodegradation and bioremediation: A tale of the two worst spills in US history, Environmental Science & Technology, 45, 6709-6715.
[https://doi.org/10.1021/es2013227]
-
Ji, Z.-G., Johnson, W. R., Wikel, G. L., (2014), Statistics of extremes in oil spill risk analysis, Environmental Science & Technology, 48(17), 10505-10510.
[https://doi.org/10.1021/es501515j]
-
Wang, L. K., Hung, Y. T., Shammas, N. K., (2006), Advanced physicochemical treatment processes, Humana Press.
[https://doi.org/10.1007/978-1-59745-029-4]
-
Gupta, R. K., Dunderdale, G. J., England, M. W., Hozumi, A., (2017), Oil/water separation techniques: A review of recent progresses and future directions, Journal of Materials Chemistry A, 5(31), 16025-16058.
[https://doi.org/10.1039/C7TA02070H]
-
Yu, J., Cao, C., Pan, Y., (2021), Advances of adsorption and filtration techniques in separating highly viscous crude oil/water mixtures, Advanced Materials Interfaces, 8(16), 2100061.
[https://doi.org/10.1002/admi.202100061]
-
Yu, Z., Ni, J., Fang, L., Wu, D., Zhu, H., (2015), Multilayer three-dimensional structure made of modified stainless steel mesh for in situ continuous separation of spilled oil, Industrial & Engineering Chemistry Research, 54(47), 11838-11843.
[https://doi.org/10.1021/acs.iecr.5b02154]
-
Rasouli, S., Rezaei, N., Hamedi, H., Zendehboudi, S., Duan, X., (2021), Superhydrophobic and superoleophilic membranes for oil-water separation application: A comprehensive review, Materials & Design, 204, 109599.
[https://doi.org/10.1016/j.matdes.2021.109599]
-
Chen, C., Weng, D., Mahmood, A., Chen, S., Wang, J., (2019), Separation mechanism and construction of surfaces with special wettability for oil/water separation, ACS Applied Materials & Interfaces, 11(11), 11006-11027.
[https://doi.org/10.1021/acsami.9b01293]
-
Cho, H., Liu, G., Zhang, Z., Qiao, P., Shan, Z., Hwang, W., (2015), An effective method for separation of oil and water using superhydrophobic/superoleophilic aluminum mesh, Science of Advanced Materials, 7(12), 2623-2627.
[https://doi.org/10.1166/sam.2015.2582]
-
Hong, S. K., Bae, S., Jeon, H., Kim, M., Cho, S. J., Lim, G., (2018), An underwater superoleophobic nanofibrous cellulosic membrane for oil/water separation with high separation flux and high chemical stability, Nanoscale, 10(6), 3037-3045.
[https://doi.org/10.1039/C7NR08199E]
-
Woo, S., Cho, H., Park, J., Shin, Y., Hwang, W., (2020), A novel approach to designing a biomimetic wettable patterned surface for highly efficient and continuous surfactant-free oil emulsion separation, Separation and Purification Technology, 248, 116864.
[https://doi.org/10.1016/j.seppur.2020.116864]
-
Kim, S., Woo, S., Park, H. R., Hwang, W., (2021), One-step versatile fabrication of superhydrophilic filters for the efficient purification of oily water, ACS Omega, 6(4), 3345-3353.
[https://doi.org/10.1021/acsomega.0c05830]
-
Purchas, D., Sutherland, K., (2002), Handbook of filter media. Elsevier.
[https://doi.org/10.1016/B978-185617375-9/50006-7]
-
Pieracci, J. P., Armando, J. W., Westoby, M., Thommes, J., (2018), Industry review of cell separation and product harvesting methods, Biopharmaceutical Processing, 165-206.
[https://doi.org/10.1016/B978-0-08-100623-8.00009-8]
-
Kim, S., Cho, H., Hwang, W., (2021), Robust superhydrophilic depth filter and oil/water separation device with pressure control system for continuous oily water treatment on a large scale, Separation and Purification Technology, 256, 117779.
[https://doi.org/10.1016/j.seppur.2020.117779]
- Han, Y. R., Andisetiawan, A., Kim, J. H., Yoon, J. S., Choi, D. S., Yoo, Y. E., (2015), An experiment investigation on the duration of the hydrophilic effects of the plasma treatment, Proceedings of the Korean Society for Precision Engineering 2015 Spring Conference, 830-831. https://www.dbpia.co.kr/journal/articleDetail?nodeId=NODE06364577
-
Vesel, A., Junkar, I., Cvelbar, U., Kovac, J., Mozetic, M., (2008), Surface modification of polyester by oxygen-and nitrogen-plasma treatment, Surface and Interface Analysis, 40(11), 1444-1453.
[https://doi.org/10.1002/sia.2923]
-
Woo, S., Park, H. R., Park, J., Yi, J., Hwang, W., (2020), Robust and continuous oil/water separation with superhydrophobic glass microfiber membrane by vertical polymerization under harsh conditions, Scientific Reports, 10(1), 21413.
[https://doi.org/10.1038/s41598-020-78271-9]
Ph.D. candidate in the Department of Mechanical Engineering, Pohang University of Science and Technology. His research interest is nanostructured system and wettability modification.
E-mail: rseabc@postech.ac.kr
Professor in the Department of Mechanical Engineering, Chosun University. His research interest is surface engineering.
E-mail: jwlee07@chosun.ac.kr
Now postdoctoral research associate in the Department of Aerospace and Mechanical Engineering, University of Notre Dame, U.S. His research interest is the design of functional nanostructures and their applications.
E-mail: skim53@nd.edu
Ph.D. candidate in the Department of Mechanical Engineering, Pohang University of Science and Technology. His research interest is nanostructured system and wettability modification.
E-mail: kihwan@postech.ac.kr
Ph.D. candidate in the Department of Convergence IT Engineering, Pohang University of Science and Technology. His research interest is ultrasound scattering analysis based on the high frequency imaging.
E-mail: gun9509@postech.ac.kr
Professor in the Department of Mechanical Engineering, Pohang University of Science and Technology. His research interest is nanostructure application.
E-mail: whwang@postech.ac.kr