
직접에너지적층 공정을 이용한 폐쇄형 알루미늄 폼 제작에 관한 연구
Copyright © The Korean Society for Precision Engineering
This is an Open-Access article distributed under the terms of the Creative Commons Attribution Non-Commercial License (http://creativecommons.org/licenses/by-nc/3.0) which permits unrestricted non-commercial use, distribution, and reproduction in any medium, provided the original work is properly cited.
Abstract
In this study, based on directed energy deposition (DED) technology, one of the additive manufacturing technologies, a porous material fabricated by mixing various aluminum alloys and foaming agent was manufactured. First, the foaming agent formed pores inside the deposited materials and differences in foaming characteristics were observed depending on the type of aluminum. Also, the foaming characteristics according to the laser power, which is a representative process variable, were analyzed. As a result, a closed-cell porous material with a maximum porosity at a laser power of 1,100 W was manufactured. Results of the compression test showed that the porous material made by the pores generated therein collapses to absorb energy, and the internal pores disappear to become high density. Therefore, Young’s modulus and yield stress were reduced by the pores inside the sample of pure aluminum and Al6063. However, it was found that the specific energy absorption, which is an advantage of the foamed materials, increased compared to non-porous materials. The findings of this study confirmed that it was possible to manufacture DED-applied foam materials using aluminum powder and a foaming agent.
Keywords:
Directed energy deposition, Aluminum foam, Closed-cell, Foam characterization, Compression test키워드:
직접에너지적층, 알루미늄 폼, 폐쇄형, 발포 특성, 압축시험1. 서론
금속적층제조(Additive Manufacturing)은 열에너지를 이용하여 금속 분말 또는 와이어를 용융 및 응고시켜, 2차원 단면의 층들을 높이 방향으로 적층하여 3차원 형상으로 제조하는 방식이다. 적층제조 기술은 재료 효율성을 높이면서 복잡한 형상의 부품을 적층할 수 있는 잠재력을 가진 제조 기술로 평가받고 있다[1]. 또한, 적층가공은 유연한 설계 자유, 짧은 리드 타임, 낮은 구매 비율(Buy-to-fly)과 같은 이점으로 인해 고성능 구조 부품을 생산하기 위한 새로운 패러다임으로 간주되고 있다[2]. 금속 소재를 이용한 적층제조 기술은 분말베드융합(Powder Bed Fusion, PBF)과 직접에너지적층(Directed Energy Deposition, DED) 방식으로 구별된다. DED 공정은 자유도가 높아 구리/철강, 구리/알루미늄, 그리고 철강/알루미늄과 같은 다양한 합금 및 이종 소재를 사용할 수 있어 부품 제조에 많은 유연성을 제공한다[3,4]. 아울러 DED 공정은 레이저 조사에 의해 생성된 용융풀의 빠른 냉각 속도로 인해 치밀한 조직을 생성시키기 때문에 우수한 기계적 특성을 가진다[5].
한편, 알루미늄은 경량 및 내부식성과 같은 우수한 특성으로 인해 적층제조기술의 초기 채택 산업인 항공 우주 산업에서 중요한 역할을 하였다[6]. 특히, 이러한 알루미늄 소재를 이용한 다공성(Porous) 구조 재료는 우수한 구조적 특성으로 인해 최근에 큰 주목을 받고 있다. 다공성 소재란 내부에 기공을 포함하고 있는 재료로, 높은 비표면적, 가벼운 무게, 높은 비강도 및 에너지 흡수, 내화학성과 같은 우수한 특성을 가지고 있다[7]. 특히, 다공성 알루미늄은 높은 비강성과 우수한 기계적 그리고 물리적 특성으로 인해 흡음, 단열 및 에너지 흡수 등 많은 분야에서 널리 활용되고 있다[8].
기존의 다공성 소재의 제조 방법은 조작이 간편하고 비용이 저렴하지만, 복잡한 형상을 제작하는 데 어려움이 있고 영역별 기공의 크기와 분포를 조절하는 것이 불가능하기 때문에 부품 설계의 유연성에 한계가 있다[9]. 반면, 금속적층제조기술을 이용한 다공성 소재 제작은 기공의 밀도, 분포 및 크기를 제어할 수 있기 때문에 최근 연구가 활발히 이루어지고 있다. 다공성 소재는 내부의 기공의 형태에 따라 폐쇄형 구조(Closed Cell)와 개방형 구조(Open Cell)로 구분할 수 있다. 폐쇄형 구조는 내부의 기공들이 연결되지 않고 독립적으로 존재하는 구조이며, 내부의 기공들이 서로 연결된 구조는 개방형 구조를 뜻한다. Wang 등은 적층제조를 이용하여 격자 구조를 가지는 다공성 금속 소재를 제작하였고, 격자 구조의 유효 열전도도에 관한 연구를 하였다[10]. Dong 등은 PBF 공정을 이용하여 Al2O3 개방형 구조의 세라믹 소재를 제작하여 미세 구조 설계와 관련된 연구를 하였다[11].
현재까지 수행된 적층제조기술을 활용한 다공성 소재와 관련된 연구는 대부분 PBF 공정을 이용한 개방형 구조 설계 및 제작에만 국한되어 있다.
한편, Shim 등은 최초로 DED 공정과 발포제를 이용하여 티타늄 발포 소재 제작을 시도하였으며, 티타늄 내부에 기공을 생성시켜 다공성 구조 제작을 성공하였다[7,12]. 이는 약 30%의 기공률을 가지는 폐쇄형 구조의 다공성 소재로 DED 변수를 조절하여 제조가 가능함을 밝혔다. Koike 등은 DED 공정을 통해 SUS 316L 분말과 발포제를 이용하여 다공성 구조를 만들었다[13].
따라서, 최근에는 DED 공정을 이용한 다공성 소재의 제작 그리고 폐쇄형 구조를 가지는 경량 소재 제작을 위한 적층제조 기술의 활용에 관한 연구가 점차 이루어지고 있다. 하지만, 위치별로 기공률과 기공 크기를 제어하는 기술과 원하는 위치에만 국부적으로 기공을 형성하는 기술은 아직까지 연구가 부족하다. 따라서 본 연구에서는 알루미늄과 발포제를 혼합하여 폐쇄형 구조의 다공성 알루미늄 폼(Aluminum Foam)을 제작하고, 발포-적층된 소재에 대한 특성을 평가 및 분석해보고자 한다.
2. 실험 방법
2.1 DED 공정 원리와 사용 장비
Fig. 1(a)는 DED 공정의 발포 적층 원리 및 방법을 나타낸다. DED 공정은 모재 표면에 금속 분말이 공급되면서 동시에 고출력 레이저 빔(Beam)을 조사하여 용융풀(Melting Pool)을 형성한다. 분말은 보호 가스(Shielding Gas)에 의해 용융풀로 전달되고 레이저 빔에 의해 용융된다. 용융된 분말은 빠르게 응고되어 비드(Bead)를 형성하고 그 결과, 적층 트랙이 형성되고 가장자리(Contour)에서 내부(Pocket)를 채워 나가는 방식으로 하나의 레이어(Layer)가 형성된다. 이 과정을 Layer-by-layer 방식으로 반복 적층하여 3차원 형상이 제작된다.
DED 공정을 이용한 발포 적층 원리는 혼합 분말이 고출력 레이저에 의해서 용융점까지 가열 및 용융된다. 동시에 발포제는 500-700oC에서 연소 및 분해되기 시작한다. 분해된 발포제는 가스를 발생시키며, 금속의 용융과 응고는 짧은 시간에 이루어지는 반면에 발포제가 분해하는 시간은 상대적으로 느리다. 따라서, 외부로 배출되지 못한 가스는 용융된 금속 안에 갇히게 되어, 결국 적층 소재 내부에 기공으로 존재하게 된다.
본 연구에서는 DMT (Direct Metal Tooling) 장치(MX3, Insstek Co., Korea)가 사용되었다(Fig. 1(b)). 이 장치에는 4 kW CO2 레이저 시스템, 수치 제어 시스템, MX-CAM 소프트웨어, 5축 NC 공작 기계, 3개의 호퍼(Hopper)와 파우더 공급 시스템으로 이루어져 있다. 실험 과정 중 산화를 방지하고 작업물을 보호하기 위한 보호 가스이자, 공급되는 분말을 운반하기 위한 가스로 아르곤(Argon)을 사용하였다. 분말 공급 장치가 장착된 헤드는 광학 비전 시스템을 포함하고, 모재 표면으로부터 9 mm 떨어진 노즐에서 직경 1 mm의 레이저 빔이 조사된다.
2.2 재료
본 연구에서 사용된 분말은 3종류이며, 순수 알루미늄 1종과 알루미늄 합금 2종(Al6063과 AlSi10Mg)을 사용하였다. 이 분말들은 가스 분무법(Gas Atomization)을 통해 분말화되었다. DED 장비에서 원활한 분말 공급을 위해 Figs. 2(a)-2(c)와 같이 구형의 분말을 사용하였으며, 직경은 45-145 μm (HANA AMT, Korea)이다. 적층소재 내부에 기공을 형성하기 위해 기존의 알루미늄 발포 공정에 사용되는 발포제 분말을 사용하였으며(Fig. 2(d)), 이는 직경 50-120 μm (GOODFELLOW, United Kingdom)의 비정형 분말이다. 알루미늄 분말과 발포제 분말을 미리 혼합하여 분말 공급 호퍼에 주입한다. 사용된 분말에 대한 화학적 조성비는 Table 1에 나타낸 바와 같다. 모재는 AlMg1SiCu를 사용하였으며, 길이 100 mm, 너비 50 mm, 그리고 두께 10 mm를 가지는 직육면체이다.
2.3 시편 제작 및 방법
본 연구에서는 발포 적층 실험을 하기에 앞서 DED 공정 변수에 따른 각 알루미늄 분말의 적층 특성을 관찰하기 위해 주요 공정 변수에 따라 기초 실험을 진행하였다. 이러한 기초 실험을 바탕으로 안정적인 적층 비드 및 레이어 형성이 가능한 조건을 최종 선정하였다. 선정된 공정조건을 기반으로 발포 적층 실험을 진행하였고, 기계적 물성을 분석하기 위해 각 알루미늄 분말을 이용하여 비다공성(Non-porous) 소재와 다공성 소재의 경도 및 압축 시험을 진행하였다. Fig. 3과 같이 가로, 세로, 그리고 높이를 각각 30, 30, 10 mm로 적층한 사각형 다공성 샘플을 직경 7 mm, 높이 7 mm인 원통형으로 절단하여 압축 시험편을 제작하였다.
2.4 시편 전처리 및 분석 조건
시편 분석을 위해 시편을 절단하여 마운팅하였다. 그리고 실리콘 카바이드(SiC) 사포(Sandpaper)로 #2400 grit까지 연마한 후, 다이아몬드 서스펜션(Diamond Suspension) 용액으로 0.1 μm grade까지 연마하였다. 이후 켈러(Keller) 용액을 이용하여 에칭(Etching)하였다. 경도 시험은 ASTM E384에 준하여 마이크로 비커스 경도계(Akashi, HM-122)를 사용하여 미세 경도(Microhardness)를 측정하였으며, 하중 0.1 kgf로 10초간 압입하여 생긴 압흔의 면적을 측정하였다. 압축시험은 만능 재료 시험기(KDMT-158, South Korea)를 사용하였으며, 0.5 mm/min의 속도로 압축 시험을 수행하였다. 시험은 시편 당 3회 반복 시험하였다. 또한, 응력-변형률 곡선으로부터 선형 기울기에 대한 탄성계수를 계산하였으며, 항복 응력은 0.2% 오프셋(Offset) 방법을 기초하여 추출하였다.
3. 발포 적층 실험 결과
3.1 발포 특성
상기 언급된 분말들과 발포제, 그리고 공정조건을 이용하여 발포 적층 실험을 수행하였다. Fig. 4는 혼합 분말들을 이용하여 적층된 샘플의 사진들을 나타내고 있다. 일반적인 분말 적층 소재와는 달리 발포 반응에 의해서 구름 형상의 표면을 형성하고 있으며, 표면에서는 분말들의 뭉침도 관찰되고 있다.
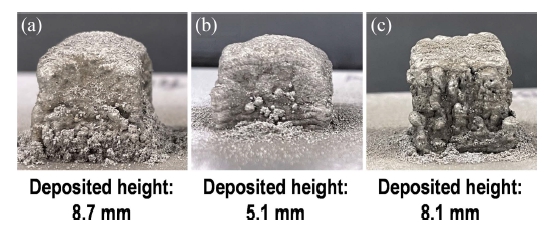
Deposited-foams and deposited heights: (a) as-foamed pure aluminum, (b) as-foamed Al6063, and (c) as-foamed AlSi10Mg
한편, 발포 적층 과정에서 발포량에 따라 발포 적층재의 최종 높이가 달라지게 된다. 따라서, 적층 높이를 통해 간접적으로 발포량을 평가할 수 있다. 발포 적층된 순수 알루미늄(As-foamed Pure Aluminum)의 실제 적층 높이는 8.7 mm이며, 설계 높이(3 mm)보다 5.7 mm 높게 적층된 것을 확인할 수 있다. 발포 적층된 Al6063 (As-foamed Al6063)의 실제 적층 높이는 5.1 mm로, 설계 높이보다 2.1 mm 더 높게 적층되었으며, 발포 적층된 AlSi10Mg (As-foamed AlSi10Mg)에서도 5.1 mm 더 높게 적층되었음을 관찰할 수 있다. 따라서, 동일한 공정 조건에서 순수 알루미늄의 발포량이 가장 많다는 것을 간접적으로 추정할 수 있다.
Fig. 5는 발포 적층된 샘플의 단면 사진을 보여준다. 발포제를 첨가하여 적층된 소재의 내부에는 다수의 기공이 형성된 것을 볼 수 있다. 우선, 적층 내면에 생성된 기공은 구형의 형상을 나타내고 있다. 발포제가 분해되면서 H2 가스가 내부에 갇혀 기공을 형성하게 되는데, Hauser 등의 연구에 의하면 이러한 수소에 의한 기공은 다른 기공보다 균질하게 분포한다고 보고하였습니다[14]. 또한, 수소는 산화막으로 존재하기 때문에 기공의 형성하는데 있어 안정에 도움이 된다고 보고하였다. 따라서, 발포에 의해 생성된 기공은 균질하고 구형의 형상을 나타내고 있다. 세 가지 샘플들을 비교하면, As-foamed Pure Aluminum은 As-foamed Al6063과 As-foamed AlSi10Mg에 비해 기공의 개수와 크기가 큰 것으로 관찰된다. 또한 As-foamed Al6063에서는 적층 위치별로 기공 크기에 차이가 있음을 알 수 있다. 이는 Al6063에 포함되어 있는 Mg의 함량에 따른 것으로 분석된다. Kim 등에 따르면, 0.45-0.9 wt% 정도의 Mg 함유량은 용융된 알루미늄 합금의 표면장력을 낮추는데 적합하다고 보고하였다[15]. 즉, Al6063에 함유되어 있는 Mg은 표면장력을 낮추어 기공과 용융풀 사이의 계면 에너지를 줄이는 역할을 한다. 이로 인해 기공이 서로 결합되지 않고, 기공의 크기가 감소되는 것이다. 반면, As-foamed AlSi10Mg에서도 다수의 기공이 형성된 것을 확인할 수 있다. Hastie 등에 의하면, 적층제조로 제작한 AlSi10Mg에서 형성된 기공 중 96%가 수소에 의한 기공으로 보고하였다[16]. 알루미늄 합금에서 수소는 Al 입자와 Al2O3 입자표면의 산화막 형태로 존재한다. 표면 산화막은 진공상태에서도 알루미늄 입자에 형성될 수 있다. 분말에 포함되어 있던 수분이 알루미늄과 반응해 산화막을 형성하게 되고, 이 과정에서 방출된 수소가 빠져나가지 못하고 기공을 형성하게 된다. 수소는 다공성을 유발하고, 이는 적층 과정에서 온도가 증가함에 따라 기공의 크기는 더욱 커지게 된다.
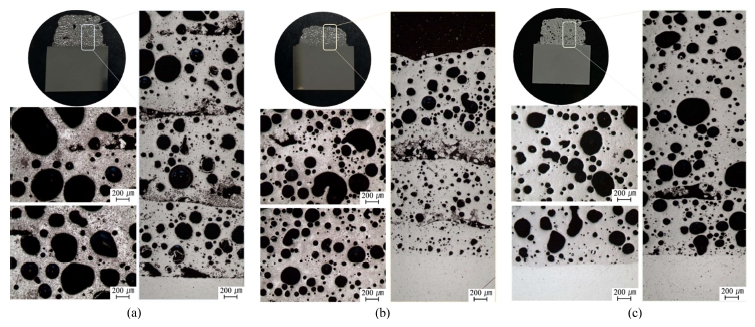
Optical images of cross sections of deposited-foam samples: (a) as-foamed pure aluminum, (b) as-foamed Al6063, and (c) as-foamed AlSi10Mg
한편, As-foamed Pure Aluminum과 As-foamed Al6063의 적층부 일부 레이어에서 계면 결함(Inter-layer Defect)을 확인할 수 있다. 우선, Al6063은 열팽창계수가 높고, 냉각 범위가 넓어서 열팽창으로 인해 용접 시에 고온 크랙(Hot Cracking)이 발생하기 쉬운 합금으로 알려져 있다[17]. Louvis 등의 연구에 의하면, 결정립계(Grain Boundary)에서 산화막이 형성되고, 이것이 균열의 주요 원인으로 밝혀졌다[18]. 용융풀의 표면에는 습윤에 영향을 미치는 산화막이 있으며, 적층 시 공급되는 분말은 이러한 산화막이 파괴되어야 용융풀에 잘 융합된다. Al6063 분말이 레이저에 의해서 용융되고, 곧바로 냉각되면서 적층된 레이어 표면에는 산화막으로 뒤덮이게 된다. 산화막은 용융점이 높고 레이저 에너지 흡수를 방해하는 요소로 작용하기 때문에 공급된 Al6063 분말에 흡수되는 에너지가 부족하기 때문에 레이어 계면 결함이 유발되는 것으로 판단된다. 즉, 적층 시 생성되는 산화막에 의해서 공급되는 에너지 밀도가 낮아지게 되고, 이는 공급된 분말을 완전히 녹이지 못하기 때문에 레이어와 레이어 사이에 분말 미용융(Lack of Fusion)과 같은 결함이 발생하게 된다. 이러한 결함은 레이어 간 계면에서 국부적으로 존재하지만, 취약부로 작용할 수 있기 때문에 기계적 특성 저하를 야기할 수도 있다.
한편, As-foamed AlSi10Mg는 레이어 계면 결함이 현저히 적은 것을 확인할 수 있다. AlSi10Mg에 함유된 실리콘(Si)은 공정(Eutectic)에 가까운 성분을 만들어 고체화 균열을 억제한다[16]. 또한 실리콘은 용융된 알루미늄의 유동성을 개선시키며, 실리콘의 응고 범위가 좁고 레이저를 잘 흡수하는 특성 때문에 계면에서의 결함이 적은 것으로 추측된다. Gupta 등은 Ti과 1 2.6 w t%의 Si를 포함하는 공정(Eutectic) Al-Si 합금 사이의 금속간 화합물 형성을 조사했으며, Al3Ti와 더불어 Ti5Si3도 함께 형성되는 것을 밝혔다[19]. 즉, Ti과 Si의 금속간 화합물의 반응열에 의해 As-foamed AlSi10Mg에서는 레이어 계면 결함이 적은 것으로 추측된다.
3.2 레이저 출력에 따른 발포 특성
Fig. 6은 레이저 출력에 따른 적층부 내 기공 분포를 나타낸다. As-built Pure Aluminum의 기공률이 가장 높은 것을 알 수 있다. Sasikumar 등에 의하면, 순수 알루미늄에서 산화물 입자(알루미나) 형성으로 인한 점도 증가가 발포 안정화에 기인한다고 보고했다[20]. 적층 과정 중 공기에 노출된 순수 알루미늄의 용융풀은 쉽게 산화된다. 이러한 산화물은 발포 안정화에 기여하는 이중막 및 산화물의 형태로 존재한다. 순수 알루미늄의 용융풀에서 산화물 입자를 형성함과 동시에 기공벽에 산화물 층 및 클러스터로 존재하는데, 이는 기공 안정화를 가져온다. 한편, As-foamed Al6063은 다른 시편에 비해 기공률이 현저히 작은 것을 확인할 수 있다. 발포 초기 기공의 성장은 점성력(점도 및 표면 장력)에 의해 결정되며, 점성력이 높을수록 기공의 성장을 막아 기공의 크기를 감소시킨다. Al6063에 첨가되어 있는 Mg은 표면장력을 낮추어 기공이 합쳐지는 것을 방지한다. Al6063은 우수한 표면처리를 목적으로 Mg과 Si 등의 합금 원소 첨가량이 적기 때문에 생성되는 산화물의 양이 적다. 따라서, 중금속 원소들의 양이 적어 용융풀의 점성은 증가하게 된다. 용융풀의 점성 증가는 용융풀이 기공 벽내의 흐름을 적게 하고 이는 기공벽의 두께를 두꺼워지게 한다[21]. 즉, As-foamed Pure Aluminum과 As-foamed AlSi10Mg에 비해 높은 점성으로 인해 기공벽의 두께가 두꺼워졌으며, 이로 인해 시편 내부의 밀도는 높아지고 최종적으로 기공률은 감소한다.
한편, As-foamed Al6063에서는 병합된 기공들에 의해 불규칙한 형상의 기공들이 분포하는 것을 관찰할 수 있다. 적층 과정 중 지속적인 레이저 조사에 의해 용융풀의 온도는 증가한다. 온도가 증가할수록 용융풀의 유동성 증가로 병합된 기공의 숫자는 증가하게 된다[22]. 따라서, 합금 원소의 양이 비교적 적고, 열전도도가 높은 Al6063은 적은 온도 변화에도 빠른 속도로 응고와 냉각이 일어나게 된다. 기공 안정화 요소인 산화물의 양도 적고 기공이 안정하게 성장하기 위한 시간도 충분하지 못하여 불규칙한 기공이 많이 분포하고 있는 것으로 판단된다.
As-foamed AlSi10Mg는 레이저 출력이 높아질수록 기공의 크기가 커지는 것을 알 수 있다. 레이저 출력이 높아질수록 더 큰 용융풀이 생성되고, 이로 인해 더 많은 양의 가스를 발생시킨다. 더 많은 양의 가스를 발생시킬수록 병합된 기공으로 인해 큰 기공이 형성된다. 또한, 모세관 현상에 의한 유동과 중력에 의한 유동의 영향을 받아 기공의 벽 두께가 얇아지면서 기공의 병합을 일으키기도 한다[23]. 따라서 발포 온도가 높아질수록 과도하게 큰 기공과 불균일한 기공 분포가 발생하는 것을 확인할 수 있다.
4. 기계적 특성
4.1 미세 경도
Fig. 7(a)는 각 시편의 적층부에서의 경도 분포를 나타내고 있으며, Fig. 7(b)는 각 시편의 적층부의 평균 경도를 나타낸다. As-built Pure Aluminum의 경도는 주조된(Cast) 순수 알루미늄과 비슷하다. 하지만, 나머지 두 합금 분말의 적층재(As-built)는 주조된 합금에 비해서 경도가 상승하였다. 한편, 모든 소재에 대해서 발포 적층된 소재(As-foamed)가 발포되지 않은 비다공성 소재(As-built)에 비해서 경도가 상승하였음을 알 수 있다.
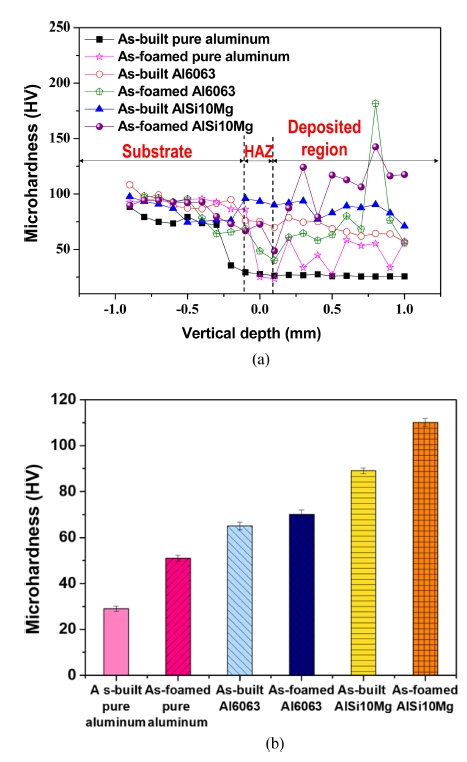
(a) Distribution of micro-hardness along height direction and (b) average micro-hardness of deposited part for each sample
본 연구에서 사용된 적층 조건에서는 발포제가 완전 분해되지 않음이 선행 연구[24]에서 이미 밝혀져 있다. 따라서, 세 시편의 적층부에서는 발포제에 함유된 Ti 입자가 분해되지 못하고 잔류하고 있다(Fig. 8). Ti 입자는 잔여 불순물 그리고 입자 크기 등에 의해서 영향을 받는다. Ti 입자에는 C, N, O와 같은 다른 불순물들이 있고, 이는 입자의 경도를 증가시킨다[25]. 또한 적층부 내부에는 알루미늄과 발포제의 반응으로 Al3Ti와 같은 금속간 화합물이 존재한다. Al3Ti와 같은 보강 미립자는 알루미늄 매트릭스 복합재(Aluminum-matrix Composite)를 생산하기 위해 알루미늄 합금에 첨가해 기계적 특성을 효과적으로 개선할 수 있다[26]. 결과적으로, 발포 적층된 소재는 발포제를 첨가함에 따라 완전히 분해되지 못하고 잔류하고 있는 입자와 금속간 화합물에 의해 기공이 있음에도 불구하고 경도가 상승함을 확인할 수 있었다.
4.2 압축 시험
Fig. 9는 압축 시험 결과로 나온 응력-변형률 곡선이다. As-foamed Pure Aluminum과 As-foamed Al6063은 연성거동을 나타내고 있다. 반면에, As-foamed AlSi10Mg의 곡선에서는 특이점이 관찰되고 있다. Hu 등에 의하면 불규칙한 기공 분포는 응력 집중을 유발하는데, 큰 기공의 존재는 낮은 국부 상대 밀도로 이어질 수 있고, 이는 인근 영역의 저하된 하중 지지 능력을 유발한다고 보고하였다[27]. 따라서, As-foamed AlSi10Mg의 불규칙한 기공 분포는 응력 집중을 유발해 곡선 상 특이 거동이 나타난 것으로 추측된다.
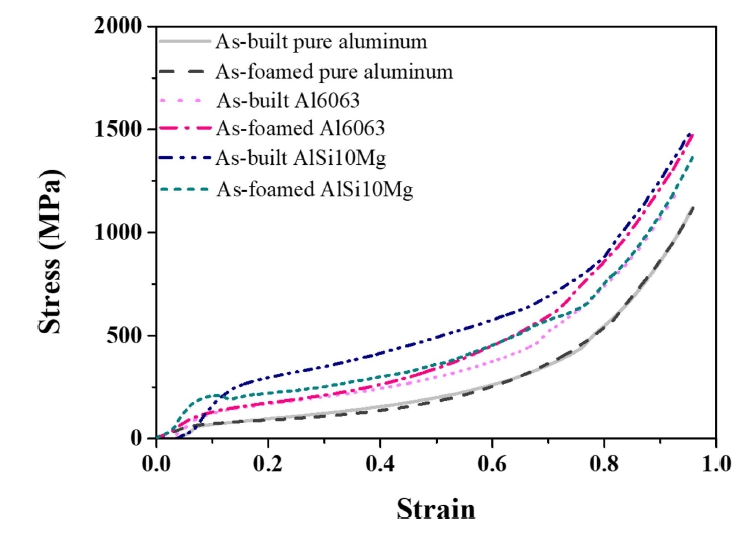
Compressive stress-strain curves of fabricated porous material samples obtained from compressive test
Figs. 10(a)-10(d)는 각 시험편에 대한 압축 시험에 따른 특성 값들을 나타내었다. As-built Pure Aluminum과 As-built Al6063은 발포제없이 적층된 샘플에 비해 탄성계수와 항복응력이 감소한 것을 확인할 수 있다. 이는 내부가 비어 있는 다공성 및 저밀도 때문인 것으로 판단된다. As-foamed AlSi10Mg는 As-built AlSi10Mg에 비해 항복 응력이 감소하였다. 이는 다공성으로 인한 저밀도 때문이다. 시편 내부에는 잔류 Ti 입자가 존재하였다. 따라서, 이러한 입자의 존재는 큰 압축 응력을 필요로 하기 때문에 As-foamed AlSi10Mg의 탄성 계수가 증가한 것으로 판단된다. 하지만, 발포-적층 소재는 비다공 적층 소재에 비해, 내부 기공이 압축 하중에 의해 붕괴되면서 에너지를 흡수하고 고밀도화 되는 변형의 크기인, 고밀도화 변형률(Densification Strain)이 증가한 것을 알 수 있다. 이는 다공성으로 인해 고밀도화되는 변형 구간이 길어진 것이며, 이는 에너지 흡수능(Energy Absorption)이 증가하였음을 의미한다. As-foamed Pure Aluminum과 As-foamed Al6063은 발포-적층 샘플이 우수한 에너지 흡수능을 가진다는 것을 확인할 수 있었다. 하지만, As-foamed AlSi10Mg는 고밀도화되는 변형량은 커지지만, 전체 에너지 흡수능은 감소한다. 이는 As-foamed AlSi10Mg 내 불규칙한 기공 분포로 인한 낮은 압축강도 때문인 것으로 판단된다.
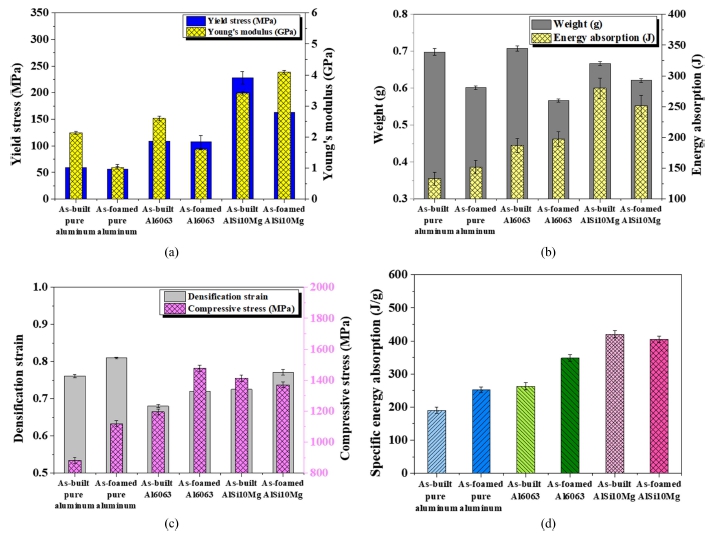
(a) Yield stress and Young’s modulus, (b) densification strain and compressive stress, (c) weight and compressive energy absorption, and (d) resulting specific energy absorption obtained from compression test for each sample
앞서 설명한대로 발포제 첨가에 의해 발포-적층 소재 내부에는 금속간 화합물들이 형성되었다. Suzuki 등에 의하면, α-Al 및 α-Ti 상으로부터 Al3Ti 상의 형성 및 성장은 부피 수축으로 이어진다[28]. 즉, 알루미늄과 발포제의 반응으로 부피가 5.4% 감소하게 되고, Al3Ti의 형성은 기공과 균열을 발생시킨다. 따라서, 발포제의 분해는 육안상으로 확인할 수 있는 큰 기공의 형성뿐만 아니라, 금속 간의 반응으로 인한 Al3Ti 형성이 부피 수축을 유발해 미세 기공을 형성하기도 한다. 이러한 크고 작은 기공에 의해 무게가 감소되며, 결국 As-foamed Pure Aluminum과 As-foamed Al6063에서 비에너지 흡수능(Specific Energy Absorption)이 증가하였음을 볼 수 있다. 여기서, 비에너지 흡수능은 전체 흡수 에너지(응력 변형률 곡선에서 적분값)를 무게로 나누어 계산된다. 발포-적층된 Pure Aluminum과 Al6063는 비다공 적층 소재 대비 비에너지 흡수능이 각각 35.8, 24.6% 향상되었다. 이러한 결과들로부터 DED 공정과 발포제를 이용해 비에너지 흡수능이 향상된 폐쇄형 다공 소재(Pure Aluminum과 Al6063)제작이 가능함을 확인할 수 있었다.
5. 결론
본 연구에서는 Pure Aluminum, Al6063, 그리고 AlSi10Mg 분말에 발포제를 혼합하여 DED 공정으로 폐쇄형 다공성 소재를 적층 제조하였다. DED에서의 주요 공정 변수인 레이저 출력에 따른 발포-적층 특성을 비교 관찰하였다. 이로부터 도출된 결과는 다음과 같다.
발포 적층 소재의 높이는 적층 내부 발생된 기공으로 인해 설계 높이(3 mm)보다 더 높게 적층 되었으며, 소재별로 서로 다른 발포 특성이 나타났다. 한편 Pure Aluminum과 Al6063에서는 발포 과정 중에 생성된 산화물이 레이저 흡수를 방해하여 레이어 계면 결함이 발생하였다.
레이저 출력 1,100 W에서 발포 적층될 경우, 최대 기공률을 가지는 폐쇄형 구조의 다공성 소재를 제조할 수 있었다. Al6063은 Mg의 함유량과 산화물로 인해서 기공이 크게 성장하지 못해 다른 소재에 비해 기공률이 낮았다.
알루미늄과 발포제의 반응으로 금속간 화합물이 형성되었다. 또한, 용융풀의 빠른 응고로 인해 완전히 용융되지 못한 Ti 입자들이 잔류하였고, 이러한 잔류 입자와 불순물에 의해 경도가 상승되었다. 따라서, 적층부 내부에 기공이 있음에도 불구하고 발포-적층된 소재의 경도는 감소하지 않았다.
압축 시험 결과, 응력-변형률 곡선은 전형적인 다공성 소재의 압축 특성을 보였다. 내부에 생성된 기공에 의해 만들어진 다공성 구조가 붕괴되면서 에너지를 흡수하고, 기공이 없어지면서 시편은 고밀도화가 진행되는 것으로 관찰되었다. Pure Aluminum과 Al6063에서는 발포 적층된 소재의 비에너지 흡수능이 증가한 것으로 확인되었다.
이러한 결과를 바탕으로, 향후에는 다양한 공정 변수에 따른 발포 및 적층 특성을 관찰할 계획이다. 또한, 발포 적층된 폐쇄형 다공성 소재에 대해서 진동 및 충격 하중에 대한 거동, 그리고 열전달 성능에 대해서도 연구해보고자 한다.
Acknowledgments
본 연구는 한국산업기술평가관리원(KEIT) 산업기술혁신사업(No. K-G012000875302)과 한국연구재단 개인기초연구사업(No. 2021R1A2C101197311)의 지원을 받아 수행되었음. 또한, 2022년도 교육부의 재원으로 한국기초과학지원연구원 국가연구시설 장비진흥센터의 지원을 받았음.
REFERENCES
-
DebRoy, T., Wei, H., Zuback, J., Mukherjee, T., Elmer, J., Milewski, J., Beese, A. M., Wilson-Heid, A. d., De, A., Zhang, W., (2018), Additive manufacturing of metallic components–process, structure and properties, Progress in Materials Science, 92, 112-224.
[https://doi.org/10.1016/j.pmatsci.2017.10.001]
-
Zhu, Z., Hu, Z., Seet, H. L., Liu, T., Liao, W., Ramamurty, U., Nai, S. M. L., (2023), Recent progress on the additive manufacturing of aluminum alloys and aluminum matrix composites: Microstructure, properties, and applications, International Journal of Machine Tools and Manufacture, 104047.
[https://doi.org/10.1016/j.ijmachtools.2023.104047]
-
Shinjo, J., Panwisawas, C., (2022), Chemical species mixing during direct energy deposition of bimetallic systems using titanium and dissimilar refractory metals for repair and biomedical applications, Additive Manufacturing, 51, 102654.
[https://doi.org/10.1016/j.addma.2022.102654]
-
Li, B., Han, C., Lim, C. W. J., Zhou, K., (2022), Interface formation and deformation behaviors of an additively manufactured nickel-aluminum-bronze/15-5 PH multimaterial via laser-powder directed energy deposition, Materials Science and Engineering: A, 829, 142101.
[https://doi.org/10.1016/j.msea.2021.142101]
-
Dinda, G. P., Dasgupta, A. K., Mazumder, J., (2009), Laser aided direct metal deposition of Inconel 625 superalloy: Microstructural evolution and thermal stability, Materials Science and Engineering: A, 509(1-2), 98-104.
[https://doi.org/10.1016/j.msea.2009.01.009]
- Davis, J. R., (1993), Aluminum and aluminum alloys, ASM International.
-
Seo, J.-Y., Shim, D.-S., (2018), Effect of track spacing on porosity of metallic foam fabricated by laser melting deposition of Ti6Al4V/TiH2 powder mixture, Vacuum, 154, 200-207.
[https://doi.org/10.1016/j.vacuum.2018.04.058]
-
Ren, X., Han, D., Sun, L., Zhang, X. G., Jiang, W., Tao, Z., Lu, G. X. (2023). Experimental and numerical investigations of aluminum foam-filled auxetic circular tubular metamaterials with elliptical cells. Construction and Building Materials, 374, 130900.
[https://doi.org/10.1016/j.conbuildmat.2023.130900]
-
Feng, X., Zhang, Z., Cui, X., Jin, G., Zheng, W., Liu, H., (2018), Additive manufactured closed-cell aluminum alloy foams via laser melting deposition process, Materials Letters, 233, 126-129.
[https://doi.org/10.1016/j.matlet.2018.08.146]
-
Wang, N., Kaur, I., Singh, P., Li, L., (2021), Prediction of effective thermal conductivity of porous lattice structures and validation with additively manufactured metal foams, Applied Thermal Engineering, 187, 116558.
[https://doi.org/10.1016/j.applthermaleng.2021.116558]
-
Dong, Y., Chen, A., Yang, T., Gao, S., Liu, S., Guo, B., Jiang, H., Shi, Y., Yan, C., (2023), Microstructure evolution and mechanical properties of Al2O3 foams via laser powder bed fusion from Al particles, Advanced Powder Materials, 2(4), 100135.
[https://doi.org/10.1016/j.apmate.2023.100135]
-
Shim, D.-S., Seo, J.-Y., Yoon, H.-S., Lee, K.-Y., Oh, W.-J., (2018), Additive manufacturing of porous metals using laser melting of Ti6Al4V powder with a foaming agent, Materials Research Express, 5(8), 086518.
[https://doi.org/10.1088/2053-1591/aad117]
-
Koike, R., Matsumoto, T., Aoyama, T., Kondo, M., (2020), Fabrication method for stainless steel foam block in directed energy deposition, CIRP Annals, 69(1), 173-176.
[https://doi.org/10.1016/j.cirp.2020.04.060]
-
Hauser, T., Reisch, R. T., Breese, P. P., Lutz, B. S., Pantano, M., Nalam, Y., Bela, K., Kamps, T., Volpp, J., Kaplan, A. F., (2021), Porosity in wire arc additive manufacturing of aluminium alloys, Additive Manufacturing, 41, 101993.
[https://doi.org/10.1016/j.addma.2021.101993]
-
Kim, J.-D., Lee, J.-H., Kim, J.-S., (2009), Characteristics of butt welded AZ31 magnesium alloy with laser welding conditions, Journal of Advanced Marine Engineering and Technology, 33(4), 517-523.
[https://doi.org/10.5916/jkosme.2009.33.4.517]
-
Hastie, J. C., Koelblin, J., Kartal, M. E., Attallah, M. M., Martinez, R., (2021), Evolution of internal pores within AlSi10Mg manufactured by laser powder bed fusion under tension: As-built and heat treated conditions, Materials & Design, 204, 109645.
[https://doi.org/10.1016/j.matdes.2021.109645]
-
Kotadia, H. R., Gibbons, G., Das, A., Howes, P. D., (2021), A review of Laser Powder Bed Fusion Additive Manufacturing of aluminium alloys: Microstructure and properties, Additive Manufacturing, 46(102155), 102155.
[https://doi.org/10.1016/j.addma.2021.102155]
-
Louvis, E., Fox, P., Sutcliffe, C. J., (2011), Selective laser melting of aluminium components, Journal of Materials Processing Technology, 211(2), 275-284.
[https://doi.org/10.1016/j.jmatprotec.2010.09.019]
-
Gupta, S. P., (2002), Intermetallic compounds in diffusion couples of Ti with an Al–Si eutectic alloy, Materials Characterization, 49(4), 321-330.
[https://doi.org/10.1016/S1044-5803(02)00342-X]
-
Sasikumar, S., Georgy, K., Mukherjee, M., Kumar, G. V., (2020), Foam stabilization by aluminum powder, Materials Letters, 262, 127142.
[https://doi.org/10.1016/j.matlet.2019.127142]
- Song, Y.-H., Park, S.-H., Jeong, M.-J., Kang, K.-J., Hur, B.-Y., (2008), Effect of foaming temperature on cell structure of 606X series aluminum alloy metallic foams, Journal of Korea Foundry Society, 28(2), 79-84.
- Tak, B.-S., Kim, B.-G., Jeong, S.-R., Hur, B.-Y., (2010), The effect of thickening agent on foaming and mechanical properties of A356 alloy, Journal of Korea Foundry Society, 30(6), 241-246.
-
Seo, J.-Y., Lee, K.-Y., Shim, D.-S., (2018), Effects of process parameters on properties of porous foams formed by laser-assisted melting of steel powder (AISI P21)/foaming agent (ZrH2) mixture, Optics & Laser Technology, 98, 326-338.
[https://doi.org/10.1016/j.optlastec.2017.08.008]
-
Zhou, X., Li, Y., Chen, X., (2020), Development of AlMg35-TiH2 composite foaming agent and fabrication of small pore size aluminium foams, Journal of Materials Processing Technology, 283, 116698.
[https://doi.org/10.1016/j.jmatprotec.2020.116698]
-
Schumann, E., Silvain, J.-F., Bobet, J.-L., Bardet, M., Lu, Y., Kotousov, A., Lamirand-Majimel, M., (2016), The effects of ball milling and the addition of blended elemental aluminium on the densification of TiH2 power, Materials Chemistry and Physics, 173, 106-116.
[https://doi.org/10.1016/j.matchemphys.2016.01.045]
-
Gong, Y., Ma, S., Hei, H., Ma, Y., Zhou, B., Wang, Y., Yu, S., Wang, X., Wu, Y., (2020), Tailoring microstructure and its effect on wear behavior of an Al–7Si alloy reinforced with in situ formed Al3Ti particulates, Journal of Materials Research and Technology, 9(4), 7136-7148.
[https://doi.org/10.1016/j.jmrt.2020.04.061]
-
Hu, L., Li, Y., Zhou, X., Yuan, G., (2022), Characterization of as-cast microstructure of aluminum foams by melt foaming method, Materials Letters, 308, 131112.
[https://doi.org/10.1016/j.matlet.2021.131112]
-
Suzuki, A., Kosugi, N., Takata, N., Kobashi, M., (2020), Microstructure and compressive properties of porous hybrid materials consisting of ductile Al/Ti and brittle Al3Ti phases fabricated by reaction sintering with space holder, Materials Science and Engineering: A, 776, 139000.
[https://doi.org/10.1016/j.msea.2020.139000]
Master in Department of Ocean Advanced Materials Convergence Engineering, Korea Maritime and Ocean University. Her research interest is metal additive manufacturing.
E-mail: khj0104185@naver.com
Associate Professor in Department of Ocean Advanced Materials Convergence Engineering, Korea Maritime and Ocean University. His research interests include direct energy deposition (DED), incremental and roll forming for sheet metal, and structural analysis as well as optimal design.
E-mail: think@kmou.ac.kr