
강관의 고주파 저항용접에서 내로우갭 주위의 전자기장 및 온도분포 해석
Copyright © The Korean Society for Precision Engineering
This is an Open-Access article distributed under the terms of the Creative Commons Attribution Non-Commercial License (http://creativecommons.org/licenses/by-nc/3.0) which permits unrestricted non-commercial use, distribution, and reproduction in any medium, provided the original work is properly cited.
Abstract
When a narrow gap was formed under appropriate welding conditions in the steel pipe manufacturing process using high-frequency resistance welding, temperature distribution was analyzed to predict the length of the gap. Assuming the length of the gap from the apex point to the welding point at an applied voltage, and calculating the temperature distribution around the gap, the length of the gap with an appropriate fusion width at the welding point could be estimated. Along with this, the current density and magnetic flux density distributions that appeared in the narrow gap were obtained according to the change in the applied voltage, and the distribution shape and size of the electromagnetic force acting on the gap were also predicted. The current density, magnetic flux density, and electromagnetic force gradually increased along the narrow gap, showing the maximum value at the welding point. In the temperature distribution in the narrow gap, the surface of the front end began to melt at an appropriate applied voltage, and the melting width was the largest at the welding point. As the applied voltage increased, the narrow gap became longer, and the appropriate gap length appeared in proportion to the applied voltage.
Keywords:
High frequency resistance welding, Finite element analysis, Temperature distribution, Electromagnetic field, Narrow gap키워드:
고주파 저항용접, 유한요소해석, 온도분포, 전자기장, 내로우갭1. 서론
송유, 보일러, 기계 시스템 등 열악한 환경에 사용되면서 내압을 받게 되는 강관(Steel Pipe)은 고강도를 포함하여 높은 품질과 신뢰성이 요구되고 있다[1]. 이들 강관은 주로 단순하면서도 생산성이 높은 고주파 저항용접(High Frequency Resistance Welding, HFRW) 공정으로 제작되고 있다. 이 공정에서는 강 스트립(Steel Strip)이 환형으로 성형되면서 용접 위치로 이송되고, 스트립의 양 가장자리(Edge)에 위치한 전극에 고주파 전압이 인가된다. 이때 소재에 흐르는 고주파 전류는 스트립 가장자리 표면(Edge Surface)에 집중하게 된다. 전류에 의한 저항열로 접합부 표면이 용융되고, 용융부가 압축롤(Pressure Roll)에 의해 가압되어, 압접된 접합부가 형성된다[2]. HFRW 공정으로 제작되는 강관에서는 용접에 의한 결함을 저감하는 것이 매우 중요한데, 공정이 단순함에도 불구하고 공정변수 간의 높은 상관성으로 인하여 각 공정변수와 결함과의 관계를 규명하기가 어렵다. 그럼에도, HFRW 공정의 향상을 위한 여러 연구가 수행되어 왔다. 특히 입열량의 변화에 따른 실험에서, 입열량이 작으면 용융의 발생이 없는 냉접점이 나타나고, 입열량이 많아지면 침입결함이 발생하는 현상을 보였다[3-5]. 입열량이 작으면 스트립 가장자리의 기하학적 수렴 위치와 용접 위치가 일치하게 되며, 양 가장자리 표면이 충분히 용융되지 않는다. 입열량이 적정하면 두 가장자리 접촉부 표면에 용융이 발생되고, 전자기력(Electromagnetic Force)이 용융부를 소재 표면(Strip Surface)으로 밀어냄으로써, 일정 폭의 내로우갭(Narrow Gap)이 발생하면서 갭 종단부에 용접 위치가 형성된다[4]. 이때 가장자리 표면에 작용하는 전자기력이 용용부뿐만 아니라 산화물을 밀어내는 정화(Cleaning) 작용을 하게 된다. 입열량이 더 커지면 갭의 길이가 매우 길어지고 갭 내부에 브리지(Bridge)가 발생하게 된다. 이때 용접부 주위에서의 전자기력이 감소하고 밀려났던 용융부가 표면장력에 의해 갭으로 재유입되는 현상이 발생하여, 침입 결함의 원인이 된다[4-6]. 내로우갭의 길이가 길면 침입결함의 가능성이 높게 되므로, 길이를 최소화하는 용접조건을 선택하는 것이 필요하다[5]. 고입열의 경우에 전자기력은 용접 위치 근처에서 폭이 넓은 내로우갭을 형성하게 되고, 내로우갭 내에 발생하는 브리지의 이동을 야기하게 된다. 갭에 나타나는 이와 같은 현상을 규명하기 위한 목적으로, 내로우갭을 일정 길이로 가정하여 갭 주변의 전자기력에 대한 수치해석을 수행하였다[7]. 한편으로는, 입열량을 주요 공정변수의 하나로 판단하고, 용접품질과의 관계를 기계적 시험과 금속학적 분석으로써 규명하였다[2]. 또한 용접 중에 용접부의 온도와 전기적 매개변수 등을 계측하여, 용접결함이 발생하지 않는 적정 온도 범위를 유지하는, 최적의 공정변수를 실시간으로 설정하는 방법을 제시하고자 하였다[1]. 따라서 내로우갭 발생과 결함발생 기구를 규명하기 위해서는 먼저 입열량 등 공정변수에 따른 용접부 주위의 온도분포를 파악할 필요가 있다. 그럼에도 온도분포 해석 등 공정변수에 따른 용접 현상을 효과적으로 규명한 해석적 연구가 미흡한 실정이다[8]. 선행한 연구에서는 두 가장자리가 기하학적으로 수렴하는 위치에서 용접이 수행되는 경우에 용접부 주변에 대한 전자기장과 온도분포 해석을 수행하였다[9]. 이로써 공정변수에 따른 용접 위치와 주위 소재에서의 온도분포를 비교적 정확히 예측할 수 있었다. 이와 같은 결과는 용접 중에 내로우갭이 존재하지 않는 경우의 해석 결과이다. 적정 용접조건에서는 스트립 수렴 위치와 용접 위치는 차이가 발생하고, 두 위치 사이에는 일정 폭의 내로우갭이 존재하게 된다[3-5]. 따라서 내로우갭의 발생을 고려한 모델링과 해석이 필요하다. 용접 중 발생하는 내로우갭 길이는 입열량과 상관성을 갖고 있어 예측하기 어렵기 때문에 시행착오와 같은 형태의 해석이 필요하게 된다. 적정한 입열량에 대응되는 갭 길이는, 용접 위치에서 용융폭이 일정 크기가 될 때, 스트립 수렴 위치와 용접 위치까지로 설정할 수 있다.
본 연구에서는 용접 공정변수의 설정이나 변동에 따라 용접위치가 변화되는 현상을 모사하여, 주어진 용접조건에서 내로우갭의 길이를 가정하고, 스트립 수렴 위치에서 실제 용접 위치까지의 갭 형성을 고려한 온도분포 해석을 수행하였다. 이로써 용접 위치에서 적정한 용융부 크기를 갖는 갭의 길이를 선택하여, 적합한 길이의 내로우갭을 형성하는 적정한 용접 공정변수의 산출이 가능함을 보이고자 하였다. 또한 갭 표면에 작용하여 용융부를 밀착하게 되는 전자기력의 분포형태와 크기를 예측하고자 하였다. 온도분포 해석을 위해서는 전류밀도분포, 파워분포 등에 대한 해석이 필요하고, 전자기력분포 해석을 위해서는 전류밀도분포와 자속밀도분포의 해석이 선행되어야 하는 바, 갭 주변에 나타나는 전자기장 해석과 온도분포 해석을 유한요소해석 기법을 이용하여 차례로 수행하였다.
2. 강관 용접 공정의 전자기장 및 온도분포 해석
2.1 공정 및 모델링
Fig. 1은 강관을 고주파 저항용접(HFRW) 공정으로써 제작하는 과정을 보여주고 있다. 관의 형태로 성형된 강 스트립의 두 가장자리(Strip Edge)는 V 형상으로 이송하게 되고, 맞대어지는 스트립의 두 가장자리(Edge) 근방에 미끄럼 전극(Sliding Contactor)을 설치하여 고주파 전압을 가하게 된다. 이로써 전류는 V 형상의 선단에 위치하는 수렴 위치(V-convergence Point, 또는 Apex Point)를 통해 두 전극 사이를 흐르게 된다. 이때 고주파의 특성으로 전류가 전도체 표면을 따라 흐르게 되는 표피효과(Skin Effect)가 나타나고, 또한 한 전극에서 용접 위치로의 전류 흐름과 용접 위치에서 다른 전극으로의 전류 흐름은 서로 반대 방향이고 그 간격이 좁아 근접효과(Proximity Effect)가 발생하여[4,7], 전류는 더욱 소재 표면에 집중하여 흐르게 된다. 이때의 전기저항에 의한 발열로써 가장자리의 표면을 가열하게 되면, 스트립 가장자리 표면의 온도가 상승하고, 표면에 산화막이 형성되기 시작한다. 입열량이 낮은 경우는 두 가장자리의 수렴 위치인 에이펙스점(Apex Point)과 용접 위치인 용접점(Welding Point)이 중첩되고, 해당 위치에서 가장 크게 가열된다. 용융 상태에 이르면 용융부와 산화막은 전자기력에 의해 상하로 밀려 스트립 표면(Strip Surface)으로 흘러가게 된다. 입열량이 더 증가함에 따라 에이펙스점과 용접점은 분리가 되고, 두 위치 사이에는 일정 길이의 내로우갭이 형성된다. 실제 용접부의 위치는 공정변수에 따라 에이펙스점과 가압 위치 사이에서 변화되고[4-6], 내로우갭의 길이는 에이펙스점과 용접점 사이의 거리로 나타낼 수 있다. 용접은 일정한 폭의 갭을 유지하면서 수행되는 것이 바람직하다[5]. 입열량이 커지면 용융량이 많아지고 전자기력이 커지게 되어, 내로우갭의 길이가 길어지게 될 것으로 예상되는 바, 용접조건에 따라 내로우갭의 길이 예측이 필요하게 된다.
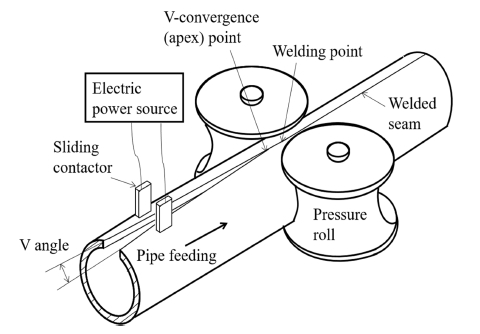
Schematic drawing of high frequency resistance welding process of steel pipe [4] (Adapted from Ref. 4 on the basis of OA)
강관의 HFRW 공정에서 내로우갭의 길이와 갭 내의 전자 기력을 예측하기 위해서는 전자기장과 온도분포 해석이 필요하다. 이 공정에서는 스트립 소재에 고주파 전류가 인가되면 이로 인해 자기장과 소재 내에 다시 와전류가 생성되는 전자 기장 현상이 발생하게 된다. 이와 같은 전자기장 현상은 맥스웰방정식으로부터 유도하여 다음과 같은 방정식으로 묘사할 수 있다[10].
(1) |
(2) |
(3) |
여기서 μ는 투자율, 는 자기벡터포텐셜, σ는 전기전도도, 는 전원전류밀도, 는 와전류밀도, 는 전기장세기이다. 식(1)에서 자기벡터포텐셜을 구하고, 이를 이용하여 식(2)와 (3)에서 와전류를 구할 수 있다. 따라서 소재에 인가된 전원 전압에 의한 전류와 이로 인한 자기장으로 생성된 와전류에 의해 전도체에 발생하는 줄열(Joule Heat), q는 식(4)와 같이 나타낼 수 있다.
(4) |
식(1)-(4)에 대한 해는 수치해석적 방법으로 구할 수 있고, 식(4)에서 같이 줄열이 산출되면, 온도분포 해석에서의 열원으로 이용할 수 있다.
한편, 접촉전극과 용접점 사이에 분포하는 전자기력은 전류와 자속밀도의 작용으로 발생하게 되고, 균일한 자기장에서 선형 도체에 가해지는 전자기력으로 가정하면, 다음과 같이 나타낼 수 있다.
(5) |
여기서 는 전자기력 벡터, I는 전류, 은 전류 방향벡터, 는 자속밀도 벡터이다.
선행한 연구에서 동일한 강관 형상의 적정한 용접부는 두께 중앙의 용융부 폭이 0.4 mm일 때 형성되는 것으로 조사되었다[9]. 본 연구에서는 설정된 전압으로 용접을 수행하는 경우, 1.0 mm의 일정한 폭을 갖는 임의 길이의 내로우갭이 발생한다고 가정하고 온도분포를 해석하여, 갭의 끝 위치인 용접점에서 적정 용접부 폭인 0.4 mm를 나타내게 될 때의 갭 길이를, 실제 용접 시에 나타나는 갭 길이로 판단하고자 하였다. 또한, 이때 얻어진 갭 내부의 전자기장, 특히 전자기력의 분포와 세기 등을 해석하여 스트립 표면의 용융부에 가해지는 힘의 크기를 가늠하고자 하였다.
2.2 전자기장 해석 모델
HFRW의 해석에 사용한 소재는 API 표준 X65급 스트립이고, 성형된 강관의 형상은 외경 609.6 mm, 내경 578.8mm, 두께 15.4 mm이다. 스트립이 강관 형상으로 성형되어 용접 위치로 진입하는 V 형상의 각도는 6o로 일정하게 두었다. 전극에는 320 kHz의 고주파 전압이 인가된다.
Fig. 2는 전자기장 해석에 사용된 기하학적 형상과 유한요소 해석 모델로서, 관으로 성형된 형상에서 용접부를 중심으로 하는 관의 일부와 전원을 공급하는 두전극(Contactor)을 보이고 있다. 이는 사전 해석을 통해, 전류밀도분포, 자속밀도분포 등을 고려하여, 스트립 가장자리가 서로 근접되는 V 형상 주위와 접합부를 제외하면 그 크기가 매우 낮아 해석결과에 영향을 미치지 않는 것으로 판단하여 선정한 형상이다. Fig. 2(a)에서는 스트립의 두 모서리(Strip Edge) 두께 방향 표면(Edge Surface)이 서로 만나는 에이펙스점과 용접점 그리고 두 위치 사이에 형성되는 내로우갭을 보이고 있다. V 영역(V 형상 구역), 전극 그리고 내로우갭을 포함한 길이 400 mm와 관 도심의 수직 상향 선에서 ±30o 이내를 해석영역으로 설정하였다. V 영역이 시작되는 관의 끝에서 전극 중심까지는 80 mm, 전극에서 에이펙스점까지는 130 mm로 일정하게 설정하였다. 전극은 가로 22 mm, 세로 30 mm의 단면을 가진 사각 기둥 형태이며, 전극 사이 거리는 58 mm, 전극 표면과 스트립 표면과의 간극은 0.1 mm로 각각 설정하였다. Fig. 2(b)는 유한요소해석을 위한 모델로, 요소의 크기와 분포를 보이고 있다. 특히 에이펙스점에서 용접점까지의 내로우갭 주위에서 0.01 mm 크기로 분할하는 등, 해석영역을 약 450,000개의 사면체 요소로 분할하였다. 해석영역에는 전극, 전극과 스트립 표면 사이의 공극, 스트립 등이 포함되고, 스트립 상하 표면으로부터 200 mm 이격된 위치까지의 공기층은 해석영역에 포함하였다. 전극에 주파수 320 kHz의 전압이 인가되는 경우, 적용된 소재의 침투깊이는 0.0065 mm 이하 크기로 예측된다[11]. 전도체 표면을 따라 전류가 흐르는 경우에는 표면임피던스경계조건(Surface Impedance Boundary Condition)을 적용하여 해석할 수 있으므로[11], HFRW에서의 고주파수 특성으로 소재 내부로의 전류 흐름은 없다고 가정하여, 전자기장 해석에서는 표면임피던스경계 해석기법을 적용하였다.
전극에 인가되는 전압의 범위가 240-270 V까지 5 V 간격으로 변화하고, 각 전압에서 임의로 설정된 갭의 길이는 0-40 mm까지 5 mm 간격으로 변화된다고 가정하여, 내로우갭 주변에서 발생하는 전류밀도, 자속밀도, 전자기력, 파워밀도 등을 계산하였다. 이와 같은 전자기장분포의 계산은 전자기장 해석이 가능한 유한요소법 기반의 상용소프트웨어인 FLUX3D 프로그램[12]을 활용하여, 3D 교류 정상상태 해석으로 수행하였다. 소재의 비투자율은 300, 전기저항은 0.5 × 10-6 Ω, 전극의 비투자율은 1, 전기저항은 1.72 × 10-8 Ω으로 각각 일정하고, 전극이 스트립 소재와 접촉되는 공극에서의 접촉 저항은 10-4 Ω으로 가정하였다. 전자기장 해석에서 확보한 파워밀도는 온도분포 해석을 위한 열원으로 활용하였다.
2.3 온도분포 해석 모델
전자기장 해석에서 계산된 파워를 외부 열원으로 하는 열전달 해석을 수행하여 스트립 소재 내의 온도분포를 구하였다. 온도분포 계산을 위한 열전달 해석(온도분포 해석)에서는 강관의 길이 방향 단면에 대한 2차원 해석을 시간변화에 따라 수행하여 정상상태 3차원 해석과 유사한 결과를 얻고자 하였다. Fig. 3에 나타낸 바와 같이 시간의 변화(t1, t2, ..., tn)에 따라 단면 형상이 변화하므로, 공정의 열전달 현상은 강관의 이송에 따라 변화하는 2차원 단면에 이송방향 해당 위치의 발열량이 열원으로 작용되는 과도상태로 모델링하고 해석하였다. 이로써 강관 길이 방향 각 단면의 온도분포를 계산할 수 있게 된다. 2차원 해석영역에서 시간변화에 따른 과도상태의 열전달 지배방정식은 다음과 같다.
(6) |
여기서 x, y는 위치, T는 온도, k는 열전도도, Q는 입열량, ρ는 밀도, c는 비열, t는 시간이며, 초기조건은 상온으로 설정하였고, 경계조건은 표면에서의 대류 조건을 사용하였다. 온도분포 해석에서는 전자기장 해석과 동일한 기하학적 형상을 대상으로 하였고, 용접속력은 강관의 성형 이송속력인 220 mm/sec로 설정하였다. 스트립 소재의 밀도, 비열, 열전도도 등 열적 성질은 온도변화에 따라 변화하는 특성을 고려하였다[13].
온도분포 해석에서 해는 유한요소법 기반의 상용소프트웨어 ABAQUS를 활용하여 구하였고[14], 유한요소해석을 위한 해석 영역과 메시는 Fig. 4와 같다. 해석영역에서는 Fig. 3에서 보인 시간에 따른 갭 간격의 변화를 고려할 수 있게 하였고, 사각형 요소를 사용하여 분할하되, 내로우갭 부근에는 조밀하게 하여 약 30,000개 요소로 분할하였다. 온도분포 해석결과 분석을 위해, 갭이 완전히 닫히는 용접점에서 용융 온도 이상에 도달하는 크기를 추출하였으며, 두께 중앙부의 용융폭을 용접점에서의 용융폭(Fusion Width)으로 나타내었다.
3. 결과 및 고찰
Fig. 5는 HFRW 공정에서 해석영역을 대상으로 한 전자기장 해석의 결과로, 스트립 가장자리에 나타나는 전류밀도 분포와 자속밀도 분포를 보이고 있다. Fig. 5(a)는 전류밀도 분포로, 대부분의 크기가 전극과 전극 사이인 스트립 가장자리의 V 영역과 내로우갭 영역에 나타나며, 특히 가장자리 표면에 집중되고, V 영역 중앙을 기준으로 좌우 대칭으로 또 상하에서 유사하게 분포하고 있음을 알 수 있다. 내로우갭 내에서는 용접 위치로 갈수록 크기가 증가되고, 내로우갭의 종단부인 용접점에서는 가장 자리 표면부에 더 밀집되고 상하부에서 가장 크게 나타나고 있다. 이는 고주파 전류로 인한 표피효과와 근접효과가 중첩하여 나타난 결과로 분석할 수 있고, 이 위치에서 입열량이 가장 높을 것으로 예측할 수 있다. Fig. 5(b)는 자속밀도 분포로, 전류밀도 분포와 유사한 형태로 스트립 가장자리에 나타나고 있다.
Fig. 6은 내로우갭 길이를 25 mm로 일정한 크기로 가정하고 인가전압을 240-280 V로 변화할 때, V 영역의 시작 위치에서 스트립의 상부 가장자리를 따라 내로우갭 종단부까지의 전류밀도와 자속밀도의 크기 변화를 보여주고 있다. 관의 끝에서 전극 중심까지는 80 mm, 전극에서 에이펙스점까지는 130 mm인 길이를 감안하면, 약 210 mm 이후는 내로우갭에서의 크기인 것을 알 수 있다. 따라서 두 크기가 전극부를 지나면서 내로우갭까지는 점진적으로 증가하고 내로우갭의 종단부인 용접점에서는 급격하게 증가하는 것을 알 수 있다. 용접점에서 표피효과와 근접효과의 중첩이 최대로 나타나고 있다. 이는 Fig. 5에서 보인 현상과 동일한 결과를 나타내고, 인가전압의 증가에 따라 전류 밀도와 자속밀도의 크기가 증가하고 있음을 알 수 있다.
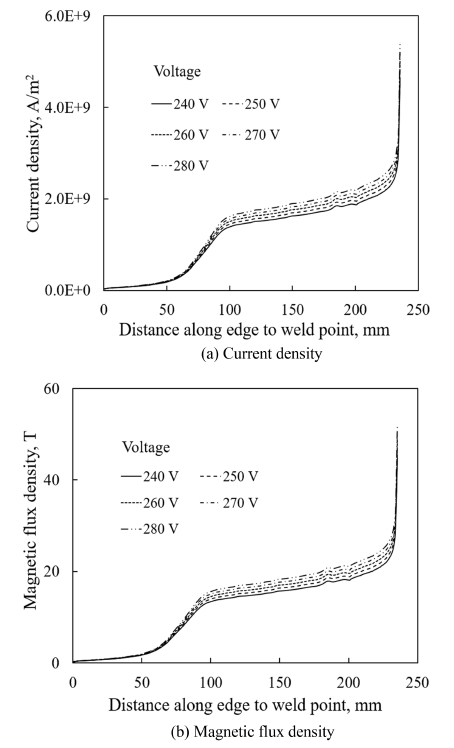
Current density and magnetic flux density from V-area to weld point along end of strip edge with change of input voltage
Fig. 7은 인가전압을 260 V로 일정하게 두고 내로우갭 길이를 5-40 mm로 변화한 경우, V 영역의 시작 위치에서 스트립 가장자리의 가장자리를 따라 내로우갭 종단부까지의 전류밀도와 자속밀도의 크기 변화를 보여 주고 있다. 전류밀도와 자속밀도는 전극에서 내로우갭을 따라 점진적으로 증가하고, 내로우갭의 종단부에서 급격히 증가하고 있다. 용접점 주위에서의 근접효과로 약 2배 정도 크게 나타나고 있다. 내로우갭에서는 전류밀도와 자속밀도의 증가로 전자기력이 증가할 것으로 예상된다. 한편, Fig. 7(a)에서 보인 갭의 길이 변화에 따른 전류밀도의 변화에서, 갭의 길이가 길어질수록 전류밀도가 낮아지고 있다. 이는 전류가 흐르는 경로가 내로우갭을 따라 길어져, 임피던스(Impedance)의 증가로 인하여 전류가 감소된 결과임을 알 수 있다. 높은 전류밀도에 의해 발열이 커지고 이로 인한 용융량의 증대로 결국 갭의 길이가 길어지게 되는 것이다. 이로 인해 전류밀도는 낮아지고 적정 길이의 갭이 형성되면, 더 이상 갭 길이의 증가는 없이 용접점이 형성되는 것으로 판단할 수 있다. 따라서 적정한 전류밀도가 형성되는 갭의 길이가 존재하게 된다. Fig. 7(b)는 갭의 길이에 따른 자속밀도의 변화를 보이고 있다. 자속밀도는 갭의 길이가 길어질수록 낮아지고 전류밀도에 비례함을 알 수 있다.
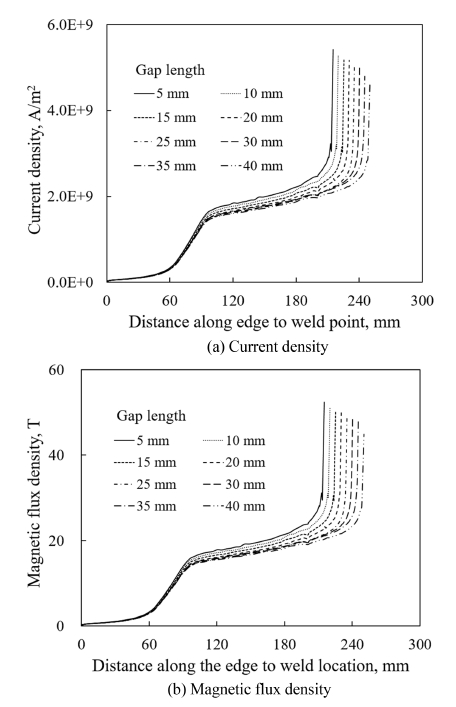
Current density and magnetic flux density from V-area to weld point along end of strip edge with change of narrow-gap length
Fig. 8은 인가전압의 변화에 따른 가장자리 표면의 전자기력 분포를 보이고 있다. 이는 갭의 길이를 30 mm로 일정하게 두고 인가전압의 변화에 따라 해석한 결과로, V 영역과 내로우갭 영역에서 스트립 가장자리 단면에 분포하는 원주방향 전자기력의 크기이다. 단면을 반대방향으로 미는 힘을 양의 크기로 나타낸 바, 단면을 누르는 압력으로 작용되고 있다. 이와 같은 힘에 의해 가장자리 표면으로부터 스트립 가장자리로 유동하는 플래쉬(Flash)가 발생하게 될 것으로 예측할 수 있다.
전자기력은 V 영역을 중심으로 하는 두 가장자리 표면에 대칭적으로 분포하였다. Fig. 8(a)에서, 인가전압이 250 V인 경우, 전자기력은 내로우갭에서 2 × 105에서 3 × 105 N/m2의 크기로 점진적으로 증가하여, 용접 위치 근방에서 2배 이상으로 급격히 커지고 있다. 이는 전류밀도와 자속밀도의 분포에서 예상된 현상이다. 특히 소재 상하 표면부가 두께 중앙부보다 더 큰 힘이 작용하는 것을 보이고 있다. 역시 Fig. 5에서 보인 두 위치에서의 전류밀도와 자속밀도의 차이에서 예상될 수 있다. Figs. 8(a), 8(b), 8(c)에서 보인 바와 같이 인가전압이 250에서 280 V로 높아질수록 용접점에서 전자기력은 최대 9 × 105에서 11 × 105 N/m2로 증가되고 있다.
Fig. 9는 갭의 길이를 30 mm로 일정하게 두고 인가전압의 변화에 따라 해석한 전자기력의 분포로, 1 mm 폭을 가진 내로우 갭의 종단부인 용접점에서 강관의 축방향 표면에 작용하는, 즉 관의 이송방향으로 폭 1 mm와 깊이 15.4 mm인 두께 벽면을 미는 축방향 전자기력의 분포 형태를 보이고 있다. Fig. 9(a)에서, 인가전압이 250 V인 경우, 두께의 중앙부에는 약 6 × 105 N/m2의 크기, 두께의 상하부에서는 최대 13 × 105 N/m2의 크기를 보이고 있다. Figs. 9(a), 9(b), 9(c)는, 인가전압이 250에서 280 V로 높아지면, 벽면에 작용하는 최대 전자기력이 13× 105에서 16.5 × 105 N/m2로 증가되는 것을 보이고 있다. 축방향으로 작용하는 힘이 Fig. 8에서 보인 원주방향으로 벽면을 미는 힘보다 더 크게 나타나고 있어, 내로우갭 내에 용융금속에 의한 브리지가 발생하면 이를 축방향으로 미는 힘의 정도를 가늠할 수 있다. 깊이 방향으로 상하 가장자리가 중앙보다 전자기력이 훨씬 더 크게 작용하고 있고, 상하의 폭 방향으로도 가장자리가 다소 더 크게 나타나고 있다.
Fig. 10은 HFRW 공정에서 시간변화에 따른 관의 길이방향단면에서의 온도분포 해석결과를 보여주고 있다. 여기서는 인가전압을 260 V, 내로우갭 길이를 20 mm, 용접속력을 220 mm/sec로 설정하여 해석한 경우로, 전극의 접촉부 전후 V 영역(0sec, 0.6 sec), 에이펙스점(1.2 sec), 내로우갭 위치(1.32 sec), 용접에 의해 접합된 위치(1.39 sec) 등을 따라 스트립의 두 가장자리가 좁혀지며 만나는 갭 주위 단면에서의 온도분포가 예측되어 있다. 전극 접촉부 주위에서의 가열 정도는 크지 않고, 에이펙스점을 지나 내로우갭 영역에서는 표면 전체가 용융상태에 도달하는 것을 알 수 있다. 용접점에 도달하면 갭은 더 가열되고 표면에서의 용융부 깊이가 더 증가하는 것을 알 수 있다.
Fig. 11는 일정 전압이 인가된 상태에서, 임의로 설정된 갭 길이에 따른 온도분포 해석에서 얻은 용접점의 단면에 나타나는 온도분포를 보이고 있다.
특히 두께 중앙의 용융폭이 0.4 mm 전후가 되는 특정한 갭길이에 대한 온도분포만을 보이고 있다. 이는 두 스트립 가장자리가 접촉하여 형성된 용접점 주위를 원주방향으로 일부 나타낸 단면으로, 상부는 스트립의 외면, 하부는 스트립의 내면이다. 온도는 상하 표면부에서 높게 나타나며 두께의 중앙 접촉부에서 최소가 됨을 알 수 있다. 갭의 길이가 길게 설정된 경우에서 용융폭이 더 좁게 나타나고 있다. 이는 인가된 동일 전압에 대하여 전류 경로가 길어져 임피던스가 증가하고 전류의 감소로 인한 결과이다. 최적 입열량 여부를 적정 용융폭으로 가늠하고자 한 해석에서, 인가전압이 높아질수록 갭 길이가 더 길어진 위치에서 적정한 용융폭이 나타나는 것을 알 수 있다. 이러한 온도분포 해석으로써 설정한 전압에서 일정 폭을 갖는 내로우 갭 길이를 예측할 수 있게 된다.
Table 1은 인가전압 변화에 따라, 임의로 갭 길이를 변화한 경우, 용접점에서 두께방향 중앙에서의 용융부 폭이 적정 용융폭인 0.4 mm에 근접한 결과를 나타낸 갭 길이에서의 계산 결과를 보이고 있다. 전압이 높아질수록 적정 용융폭이 나타나는 갭 길이가 증가함을 알 수 있다.
Fig. 12는 Table 1의 계산 결과를 선형 보간하여, 인가전압에 의해 적정 용융폭이 나타나는 내로우갭 길이를 보여주고 있다. 240 V인 경우에 에이펙스점에서 적정 용접부를 형성한 다음, 전압이 증가하면 갭이 발생하기 시작하여, 270 V인 전압이 인가되면 38 mm의 갭이 발생하는 등 전압의 크기에 비례하여 갭 길이가 증가한 위치에서 용접이 수행되는 것으로 판단할 수 있다. 즉, 인가전압이 커지면 에이펙스점과 용접점 사이에 내로우 갭이 길어지면서 용접이 진행되는 것을 알 수 있다. 그럼에도 이상적으로는 내로우갭의 길이가 짧은 경우가 결함의 가능성이 낮기 때문에 최소의 갭 길이가 되는 조건에서 용접하는 것이 더 양호한 용접부를 얻을 것으로 판단된다.
4. 결론
강관 제작을 위한 고주파 저항용접 공정에서 적합한 용접이 이뤄지는 내로우갭의 길이와 갭 내에서의 전자기력을 예측하고자 수치해석기법에 의한 온도분포 해석과 이와 연관된 전자기장 해석을 수행하였다. 해석의 결과, 인가전압의 변화에 따라 용접점의 위치가 변화되는 현상을 모사할 수 있었다. 특히, 적정 용 융폭을 형성하는 위치에서 용접이 가능하게 된다는 점을 고려하고 온도분포 해석을 수행하여, 인가전압이 240에서 270 V까지 변화되어 설정될 때 내로우갭 길이는 0에서 38 mm까지 전압에 비례하여 형성되는 것을 예측할 수 있었다. 이와 같은 조건에서는 내로우갭 내면이 용융되기 시작하여 용접점에서 0.4 mm의 용융폭이 나타나게 된다. 이와 함께, 적정 전압 범위에서의 내로우갭에 나타나는 전류밀도와 자속밀도 분포를 얻을 수 있었고, 갭 내면의 용융부에 작용하는 전자기력의 분포형태와 크기를 가늠할 수 있었다. 전류밀도와 자속밀도는 내로우갭 내에서 점진적으로 증가하고, 내로우갭 종단부에서 급격히 증가하여, 용접점에서 최대 크기를 나타내었다. 인가전압이 250 V인 경우, 원주방향 전자기력은 내로우갭에서 2 × 105에서 3 × 105 N/m2의 크기로 점진적으로 증가하고, 용접 위치 근방에서 2배 이상으로 급격히 증가하였다. 축방향 전자기력은 두께 중앙부에서 약 6 × 105 N/m2, 두께 상하부에서 최대 13 × 105 N/m2의 크기로 나타났다. 인가전압이 높아질수록 내로우갭과 용접점에서 전자 기력은 비례적으로 증가하였다.
Acknowledgments
이 연구는 2023년도 경상국립대학교 연구년제 연구교수 연구 지원비에 의하여 수행되었음.
REFERENCES
-
Simion, P., Dia, V., Istrate, B., Munteanu, C., (2014), Controlling and monitoring of welding parameters for micro-alloyed steel pipes produced by high frequency electric welding, Advanced Materials Research, 1036, 464-469.
[https://doi.org/10.4028/www.scientific.net/AMR.1036.464]
- Maksuti, R., (2020), Quality evaluation of high frequency electric resistance welded joint, International Journal of Food Technology and Nutrition, 3(5-6), 23-29.
- Kang, D., Choi, J., Jang, Y., Kim, Y., (1998), Analysis of high frequency electric resistance welding phenomena using high speed cinematography, Journal of Korean Welding Society, 16(2), 29-36.
- Haga, H., Aoki, K., Sato, T., (1980), Welding phenomena and welding mechanisms in high-frequency electric resistance welding-1st report, Welding Journal, 59(7), 208s-212s.
- Choi, J., Chang, Y., Kim, C., Oh, J., Kim, Y., (2004), Penetrator formation mechanisms during high-frequency electric resistance welding, Welding Journal, 83(1), 27s-31s.
- Hasegawa, N., Hamatani, H., Fukami, T., Nakaji, T., Takeda, Y., Motoyoshi, T., Tanimoto, M., Ohsawa, T., (2015), Development of a new optical monitoring system for HFRW processes, Nippon Steel & Sumitomo Metal Technical Report, 107, 114-120. https://www.nipponsteel.com/en/tech/report/nssmc/pdf/107-19.pdf
-
Kim, C.-M., Kim, J.-K., (2009), The effect of electromagnetic forces on the penetrator formation during high-frequency electric resistance welding, Journal of Materials Processing Technology, 209(2), 838-846.
[https://doi.org/10.1016/j.jmatprotec.2008.02.079]
-
Okada, N., Sakamoto, H., Matsuo, T., Takatani, K., (2012), Numerical analysis model of electric resistance welding pipe, Tetsu to Hagane-Journal of the Iron and Steel Institute of Japan, 98(7), 368-377.
[https://doi.org/10.2355/tetsutohagane.98.368]
-
Yang, Y. S., Bae, K. Y., (2022), Numerical analysis of high frequency electric resistance welding process of steel pipe, Journal of the Korean Society for Precision Engineering, 39(12), 931-938.
[https://doi.org/10.7736/JKSPE.022.093]
- Jang, S., Seo, J., Lee, H., Hong, J., Lee, J., (1996), The skin effect and current distribution characteristics of a coil streaming with high frequency, Proceedings of the Korean Institute of Electrical Engineers Conference, 222-224.
- Hwang, S.-R., Shin, P.-S., (2017), A study on the minimization of tie-plate loss of cast resin transformer using surface impedance boundary condition, Transactions of the Korean Institute of Electrical Engineers, 66(9), 1334-1340.
- Altair, Altair flux™ 2019.1 user guide. https://blog.altair.co.kr/wp-content/uploads/2019/07/AltairFlux2019.1_NewFeatures.pdf
-
Bae, K.-Y., Yang, Y.-S., Yi, M.-S., Park, C.-W., (2018), Numerical analysis of heat flow in oxy-ethylene flame cutting of steel plate, Proceedings of the Institution of Mechanical Engineers, Part B: Journal of Engineering Manufacture, 232(4), 742-751.
[https://doi.org/10.1177/0954405416654183]
- Washington University in St.Louis, Abaqus/cae user's manual. https://classes.engineering.wustl.edu/2009/spring/mase5513/abaqus/docs/v6.5/books/usi/default.htm?startat=pt01ch05s05hlb05.html
Professor in the Department of Mechanical Engineering, Chonnam National University. His research interests are in manufacturing processes.
E-mail: ysyang@chonnam.ac.kr
Professor in the School of Mechatronics Engineering, Gyeongsang National University. His research interests are in manufacturing processes and mechatronics.
E-mail: kybae9@gnu.ac.kr