
유리 기판 상 구리 패턴화 전극의 Mask-less 증착을 위한 레이저 유도 증착 공정 연구
Copyright © The Korean Society for Precision Engineering
This is an Open-Access article distributed under the terms of the Creative Commons Attribution Non-Commercial License (http://creativecommons.org/licenses/by-nc/3.0) which permits unrestricted non-commercial use, distribution, and reproduction in any medium, provided the original work is properly cited.
Abstract
This study investigated the Laser-Induced Plasma Backward Deposition (LIPBD) process for transparent glass-copper composite film production. LIPBD was compared with Laser-Induced Backward Transfer (LIBT). Controlling laser parameters and the z-axis position of Depth of focus (DOF) resulted in various post-deposition outcomes. The optimal deposition depth was 10 µm to 90 µm, ensuring good glass-copper adhesion. Scanning electron microscopy (SEM) and energy dispersive spectroscopy (EDS) mapping confirmed copper and copper oxide (CuO) particles. X-ray diffraction confirmed Cu and CuO peaks. The adhesive test showed a strong binding between glass and deposition, but the parts of the cracks caused by heat accumulation were delaminated during the test. LIPBD offers controlled deposition potential for glass-copper composites. Optimizing laser parameters leads to high-quality films. This study provides valuable insights into nanotechnology and the semiconductor industry, with potential applications across diverse fields.
Keywords:
Laser induced deposition, Mask-less copper pattern, Laser induced plasma backward deposition키워드:
레이저 기반 증착 공정, 마스크 없는 구리 패턴, 레이저 기반 플라스마 유도 역방향 증착1. 서론
유리는 높은 투명성, 전기저항성, 내식성과 더불어 낮은 유전 상수, 전기 손실을 가지기 때문에 다양한 응용 분야에 기판으로 사용되는 소재이다[1-3]. MEMS 센서, 반도체 패키징, 광학, 미세 유체, 에너지 저장/생성/운송 등 수많은 산업에서 필수적인 역할을 하는 유리는 평탄성, 투명성, 내열성, 내구성과 같은 독특한 특성들과 고온 작업 온도에서 낮은 변형률 등과 같은 여러 장점들로 인해 인쇄회로 기판(Printed Circuit Board, PCB) 분야에서도 많은 관심을 받고 있다[4,5]. Glass PCB (Printed Circuit Board)라고도 불리는 이 기술은 태양광 발전장치, 투명 LED, 디스플레이, 광전자 및 신재생 에너지 등 여러 산업에서 널리 적용된다[2,5,6].
그러나, Glass PCB의 필수 공정인 금속화(Metallization) 공정에는 여러 어려움이 있다. 먼저, 유리 기판에 구리를 금속화하기 위해서는 여러 복잡한 전처리 과정을 거친다[3,7,8]. 현재 산업에서 유리 기판 위 구리를 금속화하는 공정들은 전해도금 및 무전해 도금으로, 금속화 과정 전 습윤, 감광, 광산화, 활성화와 같은 패턴 마스크를 이용한 복잡한 전처리 공정들이 필요하다. 다음으로, 유리 기판은 금속화된 구리와 밀착력이 낮다[8]. 앞서 설명한 이러한 복잡한 금속화 전처리 공정에도 불구하고, 유리 기판은 우수한 물리적 및 화학적 안정성을 가지고 있기 때문에 유리 기판과 금속화 증착물 사이의 밀착력이 낮다는 단점을 가진다. 위와 같은 문제점들을 해결하기 위해서 마스크를 이용하지 않는 단순한 공정으로, 구리와 유리 기판 사이의 높은 밀착력을 부여하는 새로운 금속화 증착 공정이 필요한 실정이다.
최근 레이저를 이용한 패터닝 증착 공정 기술들이 보고되고 있다. 레이저는 빛을 원하는 부위에만 선택적으로 조사할 수 있기 때문에, 이를 활용하면 마스크를 이용하지 않고 간단하게 유리 기판 위에 금속화가 가능하다. Kim 등은 구리 전구체 용액을 활용하여 유리 기판 위에 구리 패턴을 증착하고자 하였다[9-11]. 유리 기판 위에 구리 나노 입자를 도포한 후 레이저로 선택적 용융을 통해 구리를 증착한 연구들도 보고되었다[12]. 이와 같은 연구들은 레이저를 이용하여 마스크 없이 간단하게 구리를 금속화 및 증착했다는 점에서 의의를 가지지만, 여전히 유리 기판과 구리 사이의 접착력이 낮다는 문제점을 가진다[13].
위 문제를 해결 가능한 새로운 공정으로, 레이저 유도 플라스마 보조 후면 증착(Laser-induced Plasma Backward Deposition, LIPBD)이 있다. 본 공정 기술을 이용하면 기존 레이저를 이용한 간단한 금속화 패터닝 공정이 가능함과 더불어, 플라스마와 증착물의 상호작용을 통해 유리 기판 위에 우수한 밀착력을 가지는 구리의 금속화가 가능하다. 최근 LIPBD를 이용하여 유리 기판 위 구리의 패터닝에 대한 연구들이 진행되었다[8,14]. 관련 연구들은 공정 조건에 따른 증착물의 특성을 보고하였지만 공정 조건에 따른 기판에 생기는 결함 정도에 대해서는 분석을 진행하지 않았다[8,14]. 또 LIPBD 증착물을 시드로 무전해도금을 진행해 공정을 완성했기 때문에, LIPBD 단일 공정을 통해 구리 패턴 증착을 이루거나, 공정 조건에 따른 기판의 결함과 손상에 대한 연구는 부족한 실정이다.
본 연구에서는 LIPBD 공정을 사용하여 추가적인 공정 없이 단일 공정으로 면형 증착을 수행하였다. 본 연구의 목적은 LIPBD 공정 기술을 활용하여 유리 기판 위에 구리를 면형으로 증착하는 최적의 레이저 조건을 분석하고, 증착물의 특성과 기판의 손상 정도를 평가하는 것이다. 선형 증착과 달리 면형 증착은 기판에 부과되는 열의 축적량이 많고, 이는 기판의 손상을 야기한다. 레이저 조건에 따른 열의 축적 및 기판의 손상을 LIPBD 테스트 시편 제작을 통해 분석하였다. 제작된 시편 위증착된 증착물들의 구조와 성분을 주사전자현미경(Scanning Electron Microscopy, SEM), 에너지 분산 분광법(Energy-dispersive X-ray Spectroscopy, EDS), X-선 회전 분석법(X-ray Diffraction, XRD) 등을 활용하여 분석하였고 Tape Peeling Test를 통해 기판의 손상 정도를 판단하였다.
2. 실험방법
2.1 레이저 공정 시스템
LIPBD를 위한 공정 시스템은 Fig. 1에 나타내었다. 공정에는 펄스 파이버 레이저 마킹기 (LG-20P PRO, Ideal Laser) 시스템과 증착 대상 물질인 60(길이) × 60(너비) × 20 mm3(두께) 크기의 구리판 그리고 증착 대상 기판인 76(길이) × 52(너비) × 1 mm3(두께)의 크기를 가진 대형 슬라이드 글라스(Inexus)가 사용되었다. 레이저 시스템의 레이저 소스는 Nd:YAG 레이저로 1,064 nm의 파장을 가진다. 레이저의 빔 반경(Laser Beam Diameter, D)은 0.05 mm이고 초점 심도(Depth of Focus, DOF)는 0.459 mm이다. 레이저 소스에서 나온 레이저는 증폭기를 통과하여 Galvo-scanner로 진입한다. Galvo-scanner는 진입한 레이저의 x 축, y 축 방향을 결정한다. 방향이 결정된 레이저는 초점 렌즈를 통과한 후 유리 기판을 투과해 구리판으로 조사된다. 구리판 위에 대형 슬라이드 글라스가 위치되는데, 레이저는 슬라이드 글라스를 통과해 구리판에서 초점이 맞고 유리 기판 방향으로 증착이 수행된다.
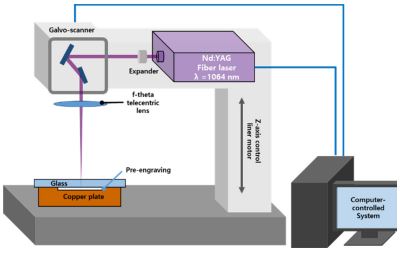
Schematic of the laser processing system and Laser Induced Pulsed Backward Deposition (LIPBD) system
레이저의 세기와 방향, 선 간격, 펄스 반복률은 컴퓨터 제어 시스템을 통해 조절된다. 레이저 파워는 7.34 W부터 21.14 W의 범위로 조사되었다. 레이저 속도(Laser Speed, v)와 반복률(Frequency, f)은 레이저 스팟 간격(Laser Spot Distance, Sd, (1))과 레이저 스팟 오버랩(Laser Spot Overlap, So, (2))의 함수로 표현할 수 있다.
(1) |
(2) |
본 연구에서는 변인 통제를 위해 f를 고정하고 v를 다양하게 구성하여 Sd와 So에 변화를 주었다. Sd가 0.01 mm 단위로 증가할 수 있도록 v들을 선정하였다. Table 1에서 선정한 v에 따른 Sd와 So 변화를 나타내었다.

Laser spot distance (Sd) and laser spot overlap (So) calculation that vary depending on the laser speed (v)
Sd와 So는 하나의 레이저 선 안에서 적용되는 변수들이다. 본 연구에서는 균일한 레이저 조사를 위해 Table 1의 각각의 레이저 조건에 따라 Line Distance를 Sd와 동일하게 하여 선 방향과 선에 수직인 방향의 오버랩을 일치시켰다.
2.2 Spacing Depth에 따른 증착 특성 분석
유리 기판과 구리판 사이의 간격(Spacing Depth)에 따라 달라지는 LIPBD 공정 증착물들의 증착 특성 분석을 위해, 레이저 시스템으로 구리판의 사전 각인(Pre-engraving)을 수행하였다. 구리판은 가장 균일한 오버랩을 가지는 Table 1의 600 mm/ sec 속도 조건 그리고 21.14 W의 레이저 세기로 0회부터 50회까지 다양한 반복 횟수로 사전 각인되었다. 사전 각인된 구리판은 10분 동안 초음파 세척, 건조 후 백색광 주사 간섭계(White Light Scanning Interferometer, NV-Series, NanoSystem)로 사전 각인된 지점의 깊이 및 표면조도를 측정하였다. 깊이 측정 완료 후 사전 각인된 샘플에 LIPBD 공정이 사전 각인에 사용된 동일한 조건으로 진행되었다. 구리가 증착된 유리 기판은 10분 동안 초음파세척 및 건조된 후 증착 정도가 분석되었다
2.3 LIPBD 테스트 시편 준비 및 제작
LIPBD 테스트 시편을 제작하기 위한 공정은 다음과 같다. 먼저, 증착 대상 소재인 구리판의 증착 면을 기계적 연마한다. 기계적 연마는 #600, #1200으로 각 10분 동안 수행하며 광학현미경(Optical Microscope, OM)으로 균일한 표면을 확인한다. 두번째로, 연마된 구리판 표면에 21.14 W의 레이저 세기, 600 mm/sec의 레이저 속도로 사전 각인을 10회 반복 수행한다. 사전 각인이 끝난 구리판은 에탄올 수조에서 10분 동안 초음파 세척되었다. 마지막으로, 사전 각인된 구리판 위에 슬라이드 글라스를 올리고 LIPBD 공정 테스트 시편이 제작된다.
테스트 시편의 조건은 Table 1과 레이저 파워의 모든 조건의 행렬로 구성되며, 가로축에는 레이저 파워, 세로축에는 레이저 속도로 각각 조건 변화 따라 5(길이) × 2.5 mm2(너비) 크기로 증착이 이루어진다.
2.4 표면분석
LIPBD 공정으로 증착된 테스트 샘플의 표면 형상은 OM(Optical Microscope, AxioLab, Zeiss) 그리고 SEM (Scanning Electron Microscope, Regulus 8220, Hitachi)으로 분석되었다. 유리 기판 자체에는 전도성이 없기 때문에 LIPBD 테스트 샘플은 SEM 관찰 전 백금으로 스퍼터링 되었고, 15 keV의 가속전압을 이용하여 3,000배, 10,000배, 40,000배 확대되어 미세구조가 분석되었다. SEM 이미지에서 샘플의 균열이 분석되었으며, 3,000배에서 육안으로 증착물 사이의 틈을 확인 가능한 조건을 균열 조건으로 판단하였다.
SEM 장비에 모듈화되어있는 EDS (Energy Dispersive X-ray Spectroscopy, Ultim MAX100, Oxford)로 LIPBD 테스트 샘플의 성분분석도 같이 수행되었다. EDS는 10 keV 가속전압을 이용하여 Mapping 되었다.
XRD (X-ray Diffraction, Smartlab, Rigaku)를 이용한 결정구조 분석도 수행되었다. XRD는 20o에서 80o까지 1 스텝 당 0.02o 간격으로 수행되었다.
밀착력 분석 전후로 4-point Probe (M4P205, MS Tech) 및 멀티미터(DMM6500, Keithley)를 통한 면저항이 측정되었다.
2.5 기판손상 및 밀착력 분석
제조된 LIPBD 테스트 시편에 밀착력 분석이 수행되었다. 밀착력 분석을 위한 시편은 다른 표면분석 시편과 겹치지 않게 단독으로 제작되었다. 밀착력 분석을 위한 테스트 시편은 LIPBD 공정 이후 30분 동안 초음파 세척 후 건조되었다. 건조 후 ASTM D330 규격을 참고해 Tape Peeling Test로 밀착력 분석이 수행되었다. 테이프(600-QC33, 3 M Scotch)는 45o의 각도로 제거되었다.
3. 결과 및 고찰
3.1 LIPBD 공정 메커니즘
LIPBD 공정은 넓은 범주에서의 레이저 투명 기판 생산공정으로 유사 공정으로는 레이저 기반 역방향 전사(Laser Induced Backward Transfer, LIBT)가 있다. 레이저가 유리를 통과해 증착 소재에 조사되는 공정이라는 점과 증착물이 레이저 방향과 반대로 증착된다는 점이 LIPBD 공정과 LIBT 공정의 공통점이다.
하지만 LIPBD 공정은 LIBT 공정과 달리 기판과의 증착 및 밀착력을 최대로 높인 공정으로 증착물의 열의 축적을 과도하지도 부족하지도 않은 수준으로 조절한 공정이다[15].
레이저 기반 투명 기판 공정은 증착 물질 타겟(Doner), 그리고 타겟 위에 올려진 증착 대상인 유리 기판(Receiver)으로 이루어진다. 본 연구에 이용된 레이저는 1,064 nm의 근적외선 파장을 가지는 레이저로 유리의 투과율이 95% 이상이기 때문에 레이저는 파워의 손실 없이 대부분 유리 기판을 투과해 불투명한 타겟으로 조사된다[8]. 레이저의 조사로 온도가 높아진 타겟은 국부적으로 용융과 증발이 일어난다. 이 용융과 증발은 타겟을 이온화 시키고 국부적인 폭발과 함께 플라스마 흄을 발생시킨다. 플라스마 흄 내부에는 타겟 소재의 나노입자들이 들어있기 때문에 이 타겟 나노입자들이 유리 기판에 증착된다.
이 증착물들의 후속 상태에 따라 공정이 차별화된다. 증착물의 후속 상태는 열의 축적에 따라 분류되며 초점심도, 레이저 펄스 오버랩, 유리 기판과 타겟 사이의 거리에 따라 달라질 수 있다. 한 예인 초점심도에 의한 증착물의 후속 상태를 Fig. 2에 도식화하였다.
증착물이 초점심도 영역에 겹치지 않을 경우, 증착물이 후속 레이저 펄스에 영향을 받지 않고 추가적인 열의 축적이 일어나지 않는다. 이 공정은 LIBT 공정이라고 불리며 유리 기판과 상호작용이 일어나지 않기 때문에 타겟 증착물과 유리 기판 사이의 접착력이 좋지 못하다[13,16].
LIPBD 공정의 경우, 적절한 수준으로 초점심도의 z축 위치를 조절하여 유리 기판과 증착물 계면에 국부적인 용융 및 반응을 이끌어내어 새로운 계면층을 형성할 수 있다. 이 경우 유리와 기판 사이의 높은 밀착력을 확보하는 것이 가능하다[14].
3.2 Spacing Depth에 따른 증착성능 분석
사전 각인 횟수에 따른 사전 각인 깊이와 표면 조도 변화를 Fig. 3(a)에 나타내었다. 사전 각인 깊이는 사전 각인 1회 당 ~3 μm씩 선형적으로 증가하는 경향을 보인다. 레이저 조사 횟수에 따라 표면 조도는 사전 각인 2회 후 1.44 μm이였으나, 횟수가 거듭할수록 점점 증가하고 이후 사전 각인 횟수 ~10번 이후로는 수렴하기 시작해 ~2.5 μm 수준으로 수렴한다.
사전 각인된 구리판 위 유리에 증착된 LIPBD 증착물은 사전 각인의 깊이에 따라 총 3종류로 분류되었다. 먼저 사전 각인 깊이가 10 μm의 미만(0회-4회 반복)일 때, 유리 기판과 구리판이 용접되는 현상이 나타났다. 유리 기판은 위에서 균열이 발생하였고 유리 기판을 구리판에서 분리 후 Fig. 3(b)와 같이 구리판에 유리가 접착되어 잔류하는 것을 확인할 수 있었다. 이 잔류 유리들은 구리판의 초음파세척 후에도 떨어지지 않은 것으로 보아 밀착력이 상당한 것으로 분석된다. 두번째로, 사전 각인 깊이가 ~10 μm 이상 ~9 0 μm(5회-30회 반복)일 때, 유리 기판과 구리판의 용접이 이루어지지 않았고 오롯이 유리 기판 위 증착만 이루어졌다. 유리 기판의 초음파 세척 후에도 구리 증착물들은 형태를 유지하는 것으로 보아 준수한 밀착력을 가지는 것으로 판단된다.
마지막으로 사전 각인 깊이가 9 0 μm(30회 반복)를 넘어가면서 증착물들은 점점 초음파 세척에 분리되었다. 이후 사전 각인 깊이가 깊어짐에 따라 LIPBD 샘플의 증착물 초음파 세척 분리정도는 더욱 심해졌다.
이를 통해 LIPBD 증착을 위한 유리 기판과 구리판 사이의 사전 각인 최적 깊이는 10 μm 이상 9 0 μm 이하인 것으로 분석할 수 있다. 90 μm 이상에서는 초음파 세척으로 구리가 분리되는 것으로 보아 각인 깊이가 얕아질수록 유리와 구리 증착물 사이 접착력은 강해지고 깊어질수록 약해진다. 하지만 너무 얕은 각인 깊이는 유리 기판과 구리판의 용접을 발생시키기 때문에 10 μm 이상의 깊이 확보는 필수적인 것으로 보여진다.
3.3 LIPBD 샘플 형상 분석
Table 1의 다양한 조건의 레이저 속도와 레이저 파워로 LIPBD 테스트 샘플이 제작되었다. 유리 기판의 증착된 면과 그 반대면이 OM으로 분석되었다(Fig. 4). LIPBD의 색깔의 경우 증착면은 어두운 갈색을 띠며 증착 반대면은 갈색을 띠었다.
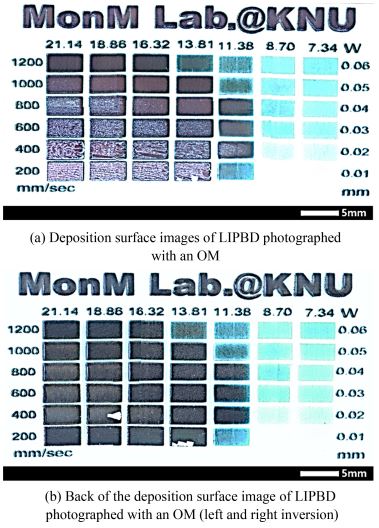
Test sample optical microscope (OM) image generated by laser-induced plasma backward deposition (LIPBD) process
레이저 조건에 따라 투명도가 달라지는 것을 확인할 수 있었는데, 레이저 세기가 강해질수록 불투명도가 높아지는 경향을 보였다. 레이저 세기가 강해지리 수록 플라스마 흄에 존재하는 나노 입자 들의 양이 많아지고, 이 나노 입자들의 양의 차이 때문에 레이저의 세기가 세질수록 증착물은 불투명해지는 것으로 분석할 수 있다.
LIPBD 테스트 샘플의 증착 반대면에서 유리의 균열을 확인할 수 있다. 이 균열은 증착면에서는 확인이 불가능했는데 속도가 느릴수록, 레이저 파워가 세질수록 더 높은 빈도로 균열을 확인할 수 있었다. 균열이 심한 경우 자연적으로 박리가 발생되기도 하였다. 테스트 샘플의 불투명한 증착면에서는 육안으로 균열을 확인하기 힘들었기 때문에 균열은 유리 기판과 증착물 사이에서 생성되어 전파되는 것으로 분석된다. 균열의 발생 원인은 기판에 가해지는 과도한 열축적 때문이며, 이 열축적은 레이저 세기가 세질수록, 레이저 속도가 느릴수록 많이 일어나는 것으로 보여진다. Fig. 4(b)에서 레이저 파워가 높을수록 레이저 속도가 느릴수록 균열이 많이 발생하는 양상은 이를 뒷받침해준다.
LIPBD 테스트 시편의 미세구조를 확인하기 위해 SEM 분석이 시행되었다. 레이저 속도에 따른 미세구조의 차이를 분석하기 위해 가장 경향이 뚜렷한 21.14 W를 선정하여 Fig. 5(a)에 대표적인 이미지를 도시하였다.
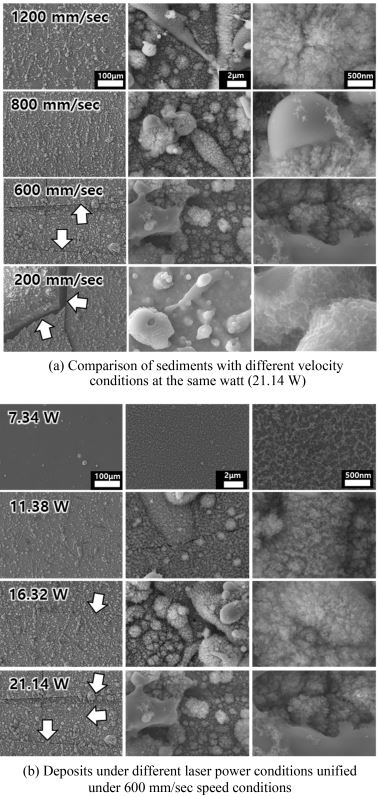
Comparative analysis of deposited properties according to various laser conditions using scanning electron microscope (SEM). 3,000 times, 10,000 times, 40,000 times enlarged images from in order from the left and the identified surface cracks are marked with white arrows
증착물은 증착 형상에 따라 크게 두 종류로 분류가 가능하다. 먼저, 유리 기판 위 평평하게 깔린 증착물들과 그리고 그 위 ~50 μm에서 100 μm 이상까지 여러 크기로 불규칙적으로 증착된 마이크로 입자들은 두 부분으로 구성되는데, 이 증착물들을 10,000배, 40,000배 확대한 SEM 이미지에서는 이 마이크로 증착물들이 형상과 무관하게 대부분 나노 입자로 이루어져 있다는 것을 확인했다.
하지만 800 mm/sec 조건의 경우, 두 번째 10,000배 확대 이미지에서 국부적으로 나노 입자가 아닌 매끈한 마이크로 입자들을 확인할 수 있다. 이 매끈한 마이크로 입자들은, 800 mm/sec에서 속도가 느릴수록 보다 높은 빈도로 관찰되었다. 마지막, 속도가 가장 느린 200 mm/sec에서는 나노 입자들의 관찰이 불가능했고, 전면이 매끈한 표면으로 변한 것을 확인했다.
크랙의 생성도 레이저 속도에 반비례한다. 600 mm/sec 레이저 속도부터는 표면에 균열을 확인할 수 있었다. 이후 레이저 속도가 느려지면서 점점 균열이 많이 발생했고, 200 mm/sec에서는 가장 넓은 수준의 균열이 생성되었다.
동일한 속도 조건에서 파워에 따른 증착 미세구조의 비교도 수행되었다. 600 mm/sec 레이저 조건에서 여러 레이저 파워에 대한 SEM 이미지를 Fig. 5(b)에 대표적인 이미지를 도시하였다. 가장 파워가 낮은 7.34 W에서는 아주 옅은 수준의 평평한 증착물들이 주를 이루었다. 이 증착물들도 10,000배와 40,000배 확대 이미지에서 나노 입자들로 구성하는 것을 확인하였다. 11.38 W의 레이저 에너지에서는 평평한 증착물 위 마이크로 입자들이 증착되기 시작한다. 이후 16.32 W 에너지 조건에서는 Micro-particles의 비율이 높아지고 매끈한 마이크로 입자들도 확인 가능하다. 21.14 W에서는 매끈한 마이크로 입자들의 비율이 높아진다. 표면 균열의 경우 16.32 W에서 처음 발견되었고 21.14 W에서 균열의 성장을 확인할 수 있다.
Fig. 5(b) 결과를 통해 증착의 순서로 평평한 증착면이 형성되고 난 이후 마이크로 입자들이 점차적으로 증착되는 것으로 분석하였다. Figs. 5(a)보다 5(b)의 증착량 변화가 확실하게 나타나는 것으로 보아 증착량은 레이저 속도보다는 세기에 우세하게 반영되는 것으로 보여진다. Fig. 5(a)는 증착 속도가 느려질수록, Fig. 5(b)는 레이저 세기가 강해질수록 균열의 생성이 우세해지는 결과로 미루어 보아 낮은 레이저 속도와 높은 레이저 세기는 기판에 열을 과도하게 축적하는 효과가 있다는 것을 재확인했다. 매끈한 마이크로 입자들의 증착물에 열이 축적되기 시작하면 증착물 내부의 나노 입자들이 용융 및 소결되어 매끈한 모양의 마이크로 입자들을 형성한다고 분석하였다.
속도가 느려짐에 따라, 그리고 레이저 세기가 높아짐에 따라 점차적으로 늘어나는 매끈한 마이크로 입자들이 이를 반증한다.
3.4 증착물 성분 분석
증착물의 성분을 분석하기 위해 SEM 챔버 내부에서 EDS Mapping 분석이 수행되었다. 가장 고른 분포를 보여주는 800 mm/sec 레이저 속도와 18.86 W 레이저 세기의 증착물의 EDS Mapping Data와 X-선 그래프의 대표 이미지가 Fig. 6에 도시되었다. 모든 샘플은 Cu, Si, O의 피크를 확인할 수 있었고 스퍼터링에 사용된 Pt의 피크도 확인할 수 있었다. Cu, Si, O의 Atomic%는 각각 54.94, 8.38, 35.58이다.
유리의 화학식이 SiO2이기 때문에 Si의 Atomic% 함량의 두 배보다 많은 O의 Atomic%는 CuO의 결합 구조에서 검출되었다고 분석할 수 있으며, 증착물은 Cu, 그리고 CuO로 구성되는 것으로 보여진다.
XRD를 통해 증착 조건에 따른 결정구조의 비교가 수행되었다. 가장 증착량이 많은 Fig. 5(a) 조건들에 대한 XRD 분석을 통해 Fig. 7에 도시하였다. 모든 조건 공통적으로 3개의 피크를 가지고 있고, 가장 속도가 느린 200 mm/sec 조건의 경우 37o 부근에서 새로운 피크가 생긴 것을 확인 가능하다. 레이저 속도가 느려질수록 피크들의 상대 높이는 높아진다.
레이저 속도가 느릴수록 펄스 오버랩이 늘어나기 때문에 많은 양의 증착물이 생성되어 결정 구조의 절대량이 늘어나 피크의 높이가 높아진 것으로 분석된다. 모든 조건 공통으로 존재하는 피크는 Cu의 피크인 것으로 확인된다. 37o 부근의 피크는 CuO의 피크로 확인되며, CuO의 피크가 다른 Cu 피크에 비교하여 작은 피크 높이를 가지는 것으로 보아 CuO는 Cu에 비해 낮은 함량으로 증착되는 것으로 분석된다. Fig. 4의 색깔 분석에서 내부(갈색) 와 외부(어두운 갈색)의 색깔이 달랐었는데, 이는 증착물의 내부에는 Cu(갈색)가 외부에는 CuO(어두운 갈색)가 증착되었기 때문으로 분석된다.
3.5 LIPBD 샘플 밀착력 테스트 이후 특성 분석
Tape Peeling Test는 테이프 기반의 접착력을 측정하는 시험이다. 시스템에 존재하는 힘은 테이프와 증착물 사이의 밀착력, 증착물 내부의 응집력, 증착물과 유리 기판 사이의 밀착력, 유리 기판 사이의 응집력이 존재한다. 이중 가장 약한 부분의 박리가 이루어지는 것으로 이를 통해 유리 기판의 결함 분석이 가능하다.
기판의 손상 정도를 파악하고 밀착력을 테스트하기 위해 샘플은 증착 이후 초음파 세척을 30분 동안 진행했다. 이후 Tape Peeling Test를 수행하고 샘플의 OM 이미지를 Fig. 8에 도시하였다. 초음파 세척 이후에는 샘플의 손상 및 박리를 확인할 수 없었다. 하지만 Tape Peeling Test에서 테이프에 상당량의 증착물 및 유리 기판이 제거되었다. 증착물의 제거는 Fig. 4(b)에서 균열을 확인할 수 있었던 높은 레이저 파워와 낮은 레이저 속도 조건에서 지배적으로 발생하였으며, 증착물과 균열이 발생한 유리 기판 자체가 박리되는 것을 통해 유리 기판 사이의 열 축적 및 균열로 약해진 응집력으로 박리가 발생하는 것으로 분석된다.
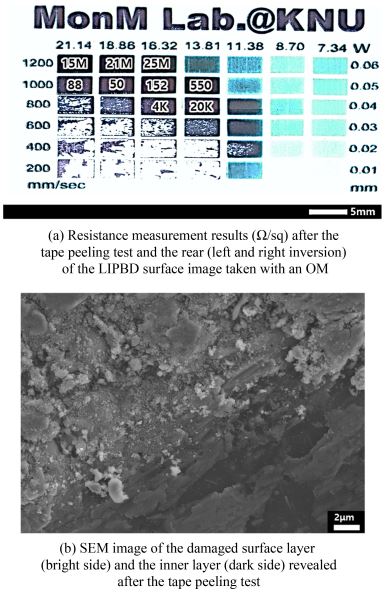
Laser-induced plasma backward deposition (LIPBD) sample after tape peeling test, characteristics and surface analysis using optical microscope (OM) and scanning electron microscope (SEM)
초음파 세척 및 Tape Peeling Test 전후로 전도성 측정이 이루어졌다. 먼저 초기상태의 증착물에는 수백 M Ω/sq 수준의 저항을 확인하거나 Overload로 저항을 측정할 수 없었다. 이후 초음파 세척 후 Tape Peeling Test를 거치고 유리 기판이 떨어지지 않은 부분들에 대한 전도성 측정이 다시 수행되었다. 샘플의 저항은 Fig. 8(a)에 도시되었다.
샘플의 저항이 기존 수백 M Ω/sq에서 Tape Peeling Test 진행 이후 ~50 Ω/sq까지 측정되었다. 샘플을 덮고 있던 CuO(어두운 갈색) 입자들이 도포되어 높은 저항을 가지는 것으로 분석되었으며, 초음파 세척되고 Tape Peeling 되면서 밑에 존재하는 Cu(갈색)가 드러나 저항이 낮아진 것으로 분석되었다. Fig. 8(b)에서 Tape Peeling Test 이후 SEM 이미지에서 박리 및 손상된 표면층과 내부의 층을 같이 확인할 수 있다.
4. 결론
본 연구에서는 LIPBD 공정을 통해 유리 기판 위에 면형 증착을 수행하고 각종 시스템의 조건에 따른 증착 특성을 분석했다.
먼저, 유리 기판과 구리판 사이의 최적 거리는 10 μm 이상 90 μm이다. 최적 범위보다 거리가 짧아지면 유리 기판과 구리판 사이의 용접 현상이 발생하고, 멀어지면 증착물과 유리 기판 사이의 밀착력이 떨어지는 현상이 발생하는 것을 확인하였다.
증착물의 성분 분석에서는 EDS Mapping과 XRD 분석을 통해 증착물이 Cu와 CuO로 구성됨을 확인하였다. 레이저 속도가 느릴수록 레이저 세기가 높을수록 CuO의 구성 비율이 늘어나고 증착 양이 많아지는 것을 확인했다.
낮은 레이저 속도와 높은 레이저 세기는 유리 기판에 높은 수준의 열축적을 일으키기 때문에 균열을 발생시켜 유리의 박리를 야기한다. Tape Peeling Test 결과 균열이 생긴 조건의 LIPBD 테스트 샘플에서는 박리가 발생하였고 전기 전도성도 확인할 수 없었다. 균열이 발생하지 않은 조건의 증착물에서는 ~50 Ω/sq의 저항을 확인할 수 있었다.
결과적으로, LIPBD 공정을 통해 형성된 Cu와 CuO로 구성된 증착물은 적절한 증착 두께와 적절한 레이저 조건을 선택할 경우 유리 기판과 우수한 밀착성을 갖는 안정적인 구조를 형성할 수 있음을 확인하였다. 증착물의 특성은 레이저 조건에 크게 의존한다. 증착 두께와 성분 변화에 따른 증착물의 특성을 고려하여 최적의 LIPBD 공정 조건을 설정하는 것이 중요한 것으로 분석된다. 또한 증착물의 안정성과 전도성을 향상시키기 위해서는 증착 공정 이후의 추가적인 처리가 필요하며, 증착물의 특성 변화를 잘 이해하여 실제 응용에 적용할 수 있도록 연구를 진행할 필요가 있다.
Acknowledgments
This research was supported by Basic Science Research Program through the National Research Foundation of Korea (NRF) funded by the Ministry of Education (2021R1I1A3045191 and 2020R1C1C1008113) and POSCO HOLDINGS.
REFERENCES
-
Del Rio, D. D. F., Sovacool, B. K., Foley, A. M., Griffiths, S., Bazilian, M., Kim, J., Rooney, D., (2022), Decarbonizing the glass industry: A critical and systematic review of developments, sociotechnical systems and policy options, Renewable and Sustainable Energy Reviews, 155, 111885.
[https://doi.org/10.1016/j.rser.2021.111885]
- Mehta, N., (2006), Applications of chalcogenide glasses in electronics and optoelectronics: A review. https://nopr.niscpr.res.in/handle/123456789/4967
-
Liu, H., Lin, W., Hong, M., (2021), Hybrid laser precision engineering of transparent hard materials: Challenges, solutions and applications, Light: Science & Applications, 10(1), 162.
[https://doi.org/10.1038/s41377-021-00596-5]
-
Esashi, M., Ono, T., (2005), From MEMS to nanomachine, Journal of Physics D: Applied Physics, 38(13), R223.
[https://doi.org/10.1088/0022-3727/38/13/R01]
-
Liu, S., Shen, B., Hao, H., Zhai, J., (2019), Glass–ceramic dielectric materials with high energy density and ultra-fast discharge speed for high power energy storage applications, Journal of Materials Chemistry C, 7(48), 15118-15135.
[https://doi.org/10.1039/C9TC05253D]
-
Longobardo, A. V., (2010), Glass fibers for printed circuit boards, Fiberglass and Glass Technology: Energy-Friendly Compositions and Applications, 175-196.
[https://doi.org/10.1007/978-1-4419-0736-3_4]
-
Li, L., Zhang, J., Wang, Y., Zaman, F. U., Zhang, Y., Hou, L., Yuan, C., (2021), Laser irradiation construction of nanomaterials toward electrochemical energy storage and conversion: Ongoing progresses and challenges, InfoMat, 3(12), 1393-1421.
[https://doi.org/10.1002/inf2.12218]
-
Wei, K., Lin, C.-K., Tung, P.-C., Ho, J.-R., Tsao, I.-Y., (2023), Formation of subsurface Cu-O-Si system through laser-induced plasma-assisted copper penetration for fabricating robust adhesive copper wire on glass substrate, Applied Surface Science, 609, 155149.
[https://doi.org/10.1016/j.apsusc.2022.155149]
-
Kim, H.-G., Park, M. S., (2017), Circuit patterning using laser on transparent material, Surface and Coatings Technology, 315, 377-384.
[https://doi.org/10.1016/j.surfcoat.2017.02.049]
-
Kim, H.-G., Park, M.-S., (2021), Fast fabrication of conductive copper structure on glass material using laser-induced chemical liquid phase deposition, Applied Sciences, 11(18), 8695.
[https://doi.org/10.3390/app11188695]
-
Seo, J. M., Kwon, K.-K., Song, K. Y., Chu, C. N., Ahn, S.-H., (2020), Deposition of durable micro copper patterns into glass by combining laser-induced backside wet etching and laser-induced chemical liquid phase deposition methods, Materials, 13(13), 2977.
[https://doi.org/10.3390/ma13132977]
-
Suh, Y. D., Kwon, J., Lee, J., Lee, H., Jeong, S., Kim, D., Cho, H., Yeo, J., Ko, S. H., (2016), Maskless fabrication of highly robust, flexible transparent Cu conductor by random crack network assisted Cu nanoparticle patterning and laser sintering, Advanced Electronic Materials, 2(12), 1600277.
[https://doi.org/10.1002/aelm.201600277]
-
Praeger, M., Papazoglou, S., Pesquera, A., Zurutuza, A., Levi, A., Naveh, D., Zergioti, I., Eason, R. W., Mills, B., (2020), Laser-induced backward transfer of monolayer graphene, Applied Surface Science, 533, 147488.
[https://doi.org/10.1016/j.apsusc.2020.147488]
-
Zhang, C., Yu, Y., Cao, Y., Wei, X., Su, S., Liu, W., (2021), Routing a glass substrate via laser induced plasma backward deposition of copper seed layer for electroplating, Optics & Laser Technology, 138, 106849.
[https://doi.org/10.1016/j.optlastec.2020.106849]
-
Liu, H., Li, Y., Lin, W., Hong, M., (2020), High-aspect-ratio crack-free microstructures fabrication on sapphire by femtosecond laser ablation, Optics & Laser Technology, 132, 106472.
[https://doi.org/10.1016/j.optlastec.2020.106472]
-
Zywietz, U., Evlyukhin, A. B., Reinhardt, C., Chichkov, B. N., (2014), Laser printing of silicon nanoparticles with resonant optical electric and magnetic responses, Nature Communications, 5(1), 3402.
[https://doi.org/10.1038/ncomms4402]
M.Sc. candidate in the Department of Advanced Science and Technology Convergence, Kyungpook National University. His research interest is about energy beam-based manufacturing process.
E-mail: lee1789911@gmail.com
Ph.D. candidate in the Department of Advanced Science and Technology Convergence, Kyungpook National University. His research interest is precision mechanical engineering.
E-mail: lhg0314@knu.ac.kr
Principle researcher in Korea Institute of Industrial Technology (KITECH). His research interest is in advanced manufacturing process.
E-mail: dkim0707@kitech.re.kr
Professor in the Department of Precision Mechanical Engineering, Kyungpook National University. His research interest is precision mechanical engineering.
E-mail: kimtw@knu.ac.kr
Professor in the Department of Precision Mechanical Engineering, Kyungpook National University. His research interest is about energy beam-based manufacturing process.
E-mail: js.kim@knu.ac.kr