
실리콘 카바이드의 미세 방전 가공 특성
Copyright © The Korean Society for Precision Engineering
This is an Open-Access article distributed under the terms of the Creative Commons Attribution Non-Commercial License (http://creativecommons.org/licenses/by-nc/3.0) which permits unrestricted non-commercial use, distribution, and reproduction in any medium, provided the original work is properly cited.
Abstract
Silicon carbide (SiC) is chemically stable, highly heat-resistant, and resistant to thermal shock. SiC having excellent characteristics in a high temperature and high voltage environment is used in high-power semiconductors, high-precision mechanical devices, optical components, etc. As it is used in various industries, there is a growing demand for processing fine holes or grooves in silicon carbide. In this study, micro holes and grooves were machined on 4H-SiC and sintered SiC using electrical discharge machining (EDM). Silicon carbide which has very high hardness can be easily processed by EDM as compared with mechanical processes. As a tool material, a polycrystalline diamond (PCD) which has high wear resistance was used and a micro tool of a diameter of 100 μm was fabricated by wire electrical discharge grinding (WEDG). In the EDM of SiC, the machining characteristics such as surface roughness, discharge gap, and tool wear were investigated.
Keywords:
Silicon carbide, EDM, PCD, Hole, Groove키워드:
탄화규소, 방전가공, 다결정 다이아몬드, 구멍, 홈1. 서론
최근, 반도체, 항공우주, 광학 등의 다양한 분야에서 미세 형상 가공에 대한 요구가 증가하고 있으며 그에 따라 절삭, 연삭, 레이저, 방전, 전해 가공 등 다양한 초정밀 가공 공정에 대한 많은 연구가 수행되고 있다[1-8]. 그 중 실리콘 카바이드(Silicon Carbide, SiC), 지르코니아, 알루미나 등과 같은 고경도 세라믹 재료에 대한 정밀 가공 수요가 높아지고 있다[1]. 특히 미세 형상의 크기는 수백 μm에서 수 μm까지 다양하게 요구되고 있으며 미세 형상에는 다양한 형상이 있을 수 있지만 구멍과 홈 가공이 가장 많이 요구되고 있다.
실리콘 카바이드는 화학적으로 안정적이고 고온 환경에서 열 충격에 강하다는 특성을 가지고 있으며 우수한 기계적 특성을 가지고 있어 고출력 전력반도체, 반도체 공정 부품, 우주 항공 및 광학 부품의 소재로 주목을 받고 있다. 하지만 높은 경도와 취성 성질로 인해 가공이 어려운 문제점이 있다[1].
Suzuki 등은 레이저를 이용하여 미세 다이아몬드 밀링 공구를 제작한 뒤 이를 이용하여 SiC를 가공하였으며 우수한 표면 품질의 미세 렌즈 어레이 몰드를 제작하였다[9]. Yan 등은 SiC에 방전으로 미세 구멍 형상을 가공한 뒤 가공 표면에서 SiC의 성분 변화 및 열변형층에 대해 연구하였으며 방전 가공 후 실리콘 카바이드가 실리콘과 탄소로 분해되는 것을 밝혔다[10]. Kliuev 등은 탈이온수를 이용한 방전 가공을 수행하였으며 인가전압과 펄스 폭 등의 가공 조건에 따른 가공 특성에 대해 연구하였다[11].
본 연구에서는 단결정 실리콘 카바이드인 4H-SiC와 Sintered SiC(소결 SiC)의 미세 방전 가공 특성에 대해 연구하였다. SiC는 대략 13-25 mΩ·cm의 비저항값을 갖고 있으며 이는 방전 가공을 적용할 수 있는 최대 저항값이라고 할 수 있다[11-15]. 4H-SiC는 고전력 반도체소자나 광학부품의 소재로 주로 사용되며 소결 SiC는 고경도 기계 부품 등에 사용된다. 방전 가공에서 공구 전극의 재료로 방전 마모에 대해 높은 저항을 갖는 다결정 다이아몬드(Polycrystalline Diamond, PCD)를 사용하였으며, 와이어 방전 가공의 일종인 와이어 방전 연삭(Wire Electrical Discharge Grinding, WEDG)으로 지름 100 μm의 원통형 공구 전극을 제작하여 실험을 진행하였다[16-19]. 제작한 공구를 이용해 실리콘 카바이드에 방전 가공으로 구멍과 홈을 가공하였다. 방전 가공 시, 사용하는 축전 용량에 따라 방전 에너지 크기가 달라지므로 축전 용량의 변화에 따른 구멍과 홈의 거칠기, 방전흔의 크기, 방전 갭, 가공 시간, 그리고 공구의 마모 정도의 차이를 측정하여 비교하였다.
2. SiC 재료와 실험 장치
실험에서 사용한 SiC는 Fig. 1과 같은 4H-SiC Wafer와 Sintered SiC이며, 각 SiC에서 같은 조건으로 구멍과 홈을 가공하여 SiC 종류에 따른 가공 특성의 차이를 비교하였다.
Fig. 2는 본 실험에서 사용한 가공 장치의 개략도이다. 약 3 μm 오차의 정밀도를 갖는 X-Y-Z 3축 이송 스테이지(300AT, Parker Hannafin Corp.)로 구성되어 있으며, Z축에는 PCD 공구 전극을 장착할 수 있는 만드렐이 있고 X, Y축에는 와이어 방전 연삭을 위한 와이어 장치가 설치되어 있다. 공구 제작 장치 바로 옆에 가공물을 장착하여 방전 가공을 할 수 있도록 수조를 장착하였다. 실험에서 쓰인 방전 회로는 저항(Resistor)과 축전기(Capacitor)로 이루어진 RC 타입의 회로이다.
3. 실험 방법
3.1 PCD 공구 전극 가공
공구 전극 재료로 PCD를 사용하였다. PCD는 높은 온도에서도 높은 경도와 내마모성을 갖고 있으며 열전도성이 우수하여 기계적 가공이나 방전 가공에서 공구 마모가 낮은 특성이 있다. PCD는 높은 경도를 갖고 있기 때문에 미세 공구 제작할 때 연삭과 같은 기계적 가공보다 방전 가공으로 제작하는 것이 보다 수월하다. 따라서 본 실험에서는 Fig. 3과 같이 와이어 방전 연삭(WEDG)으로 PCD 공구를 제작하였다. 공구를 제작할 때 사용한 가공 조건은 Table 1과 같다.
본 실험에서는 결정립 크기가 10 μm인 지름 1 mm의 PCD 소재를 방전 가공하여 Fig. 4와 같이 지름 100 μm, 총 길이 1,000 μm의 원통형 공구로 가공하였다. Fig. 4는 주사전자현미경(GeminiSEM300, Carl Zeiss Corp.) 으로 촬영한 사진이다.
3.2 방전 구멍과 홈 가공
Fig. 2의 실험 장치의 개략도와 같이 공구 제작을 위한 WEDG 모듈 옆에 SiC 방전 가공을 할 수 있도록 방전액을 채우기 위한 수조를 설치하고 그 위에 시편을 고정하여 방전 가공을 진행하였다. 시편으로는 각각 두께 500 μm와 1 mm의 4H-SiC 웨이퍼와 Sintered SiC의 판재를 사용하였다.
구멍 가공 방법으로 Fig. 5(a)와 같이 시편을 고정한 후 제작한 공구를 수직 방향으로 내리면서 방전 가공하였으며 구멍 방전 가공 조건은 Table 2와 같다. 공구를 수직방향(z축 방향)으로 1 μm/s의 속도로 이송하여 총 200 μm 깊이의 구멍을 가공하였다.
Fig. 5(b)는 미세 홈을 가공하는 과정을 나타낸 것이다. 구멍 가공과의 차이점은 시편이 고정된 이송 스테이지가 X축 방향으로 좌우로 반복 운동 하는 상태에서 공구를 Z축 방향으로 이송하여 홈을 가공하였다는 것이다. 시편이 고정된 스테이지를 X축 방향으로 5,000 μm/s의 속도로 400 μm 길이를 반복 운동하도록 한 상태에서 공구를 Z축 방향으로 3 μm/s의 속도로 이송하였다. 미세 홈의 가공 조건은 Table 3과 같다.
방전 가공에서는 축전 용량의 크기에 따라 방전 에너지 크기가 달라진다[19-21]. 축전 용량의 크기에 따라 방전 가공 표면이 어떻게 달라지는지 알아보기 위해 구멍과 홈 방전 가공에서 5,600, 10,000, 100,000 pF의 3가지의 축전 용량을 사용하였다.
4. 실험 결과
4.1 방전 구멍과 홈 가공
4H-SiC에 방전 가공으로 구멍과 홈을 가공할 때 사용한 축전용량(Capacitance)의 크기에 따른 표면 거칠기와 공구의 마모 정도를 알아보았다. RC 형태의 방전 회로에서 방전에너지는 축전기의 축전 용량에 비례하며, 방전 에너지가 클수록 방전에 의한 재료 제거량이 커지게 된다.
Fig. 6는 각각 5,600, 10,000, 100,000 pF의 축전 용량에 따라 방전 가공된 구멍 입구부와 가공 표면의 사진이다. 방전으로 구멍을 가공하면 방전 에너지에 의해 재료가 녹고 재응고되면서 구멍 주변에 버(Burr)가 발생하는데, 축전 용량이 커질수록 구멍 입구에 발생하는 버가 더 많아지는 것으로 나타났다. 구멍의 입구 지름 또한 축전 용량에 따라 달라지는 경향을 보였다. 축전 용량이 커짐에 따라 구멍의 지름이 133, 140, 147 μm으로 점점 커지는 것을 확인할 수 있었다. 이는 방전 에너지가 커짐에 따라 방전 갭(Gap)이 커지기 때문이다. 동일한 이유로 구멍 표면의 방전흔도 커지는 것을 볼 수 있다.
Fig. 7은 축전 용량에 따른 방전 가공된 미세 홈과 홈 바닥의 표면 사진이다. 구멍 가공과 동일하게 5,600, 10,000, 100,000 pF의 축전 용량을 사용하였다. 구멍 가공 결과와 마찬가지로 축전 용량이 커질수록 홈의 입구 부분에서의 버가 더 많아지는 경향을 보였다. 바닥 면도 마찬가지로 축전 용량이 커질수록 방전흔의 크기가 더 커지는 것을 확인할 수 있다. 이에 따라 거칠기 또한 더 커지는 경향을 보였다.
4.2 Sintered SiC 가공 결과
4H-SiC Wafer를 가공할 때와 동일한 조건으로 Sintered SiC를 가공하였다. Figs. 8과 9는 각 축전 용량에 따른 구멍과 홈의 입구 부분과 가공 표면을 보여준다. 축전 용량이 커질수록 입구에서 발생하는 버가 더 많아지고 구멍의 입구 주변에 치핑(Chipping)이 더 많이 발생함을 확인할 수 있다. 방전흔도 4H-SiC와 마찬가지로 축전 용량이 더욱 커짐에 따라 같이 커지는 것으로 확인되었다.
4.3 SiC 종류에 따른 가공 결과 비교
4H-SiC와 Sintered SiC 방전 가공 결과 축전 용량에 따른 변화는 동일한 경향성을 보였다. 축전 용량이 커질수록 입구의 품질이 나빠지며, 방전흔의 크기가 커지고 가공면의 표면 거칠기가 커지는 경향이 나타났다.
Fig. 10은 두 종류의 SiC에서 홈 가공 시 축전 용량에 따른 표면 거칠기(Ra)와 공구의 마모 정도를 비교한 그래프이다. 4H-SiC와 Sintered SiC에서 모두 축전 용량이 커짐에 따라 거칠기도 커지는 경향을 보이고 있다. 4H-SiC의 표면거칠기는 0.197 μm Ra에서 0.285 μm Ra로 증가하였으며, Sintered SiC는 0.154 μm Ra에서 0.175 μm Ra로 증가하였다. 전체적으로 Sintered SiC의 거칠기가 4H-SiC보다 더 작게 나타나는 경향을 보인다.
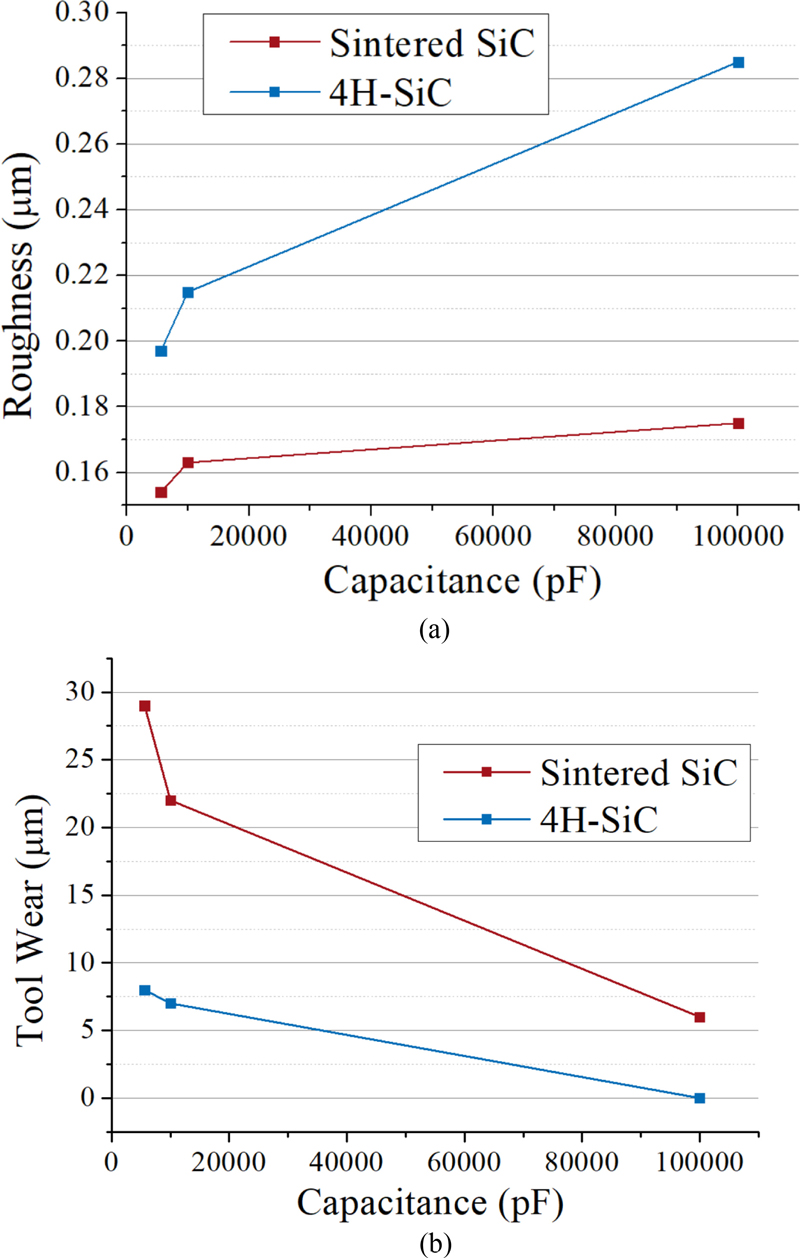
(a) Average surface roughness of the groove surface, (b) tool wear in the machining of groove on 4H-SiC and Sintered SiC according to capacitance
공구의 마모는 방전 가공 이전과 이후의 공구의 길이 차이를 측정하여 비교하였다. Fig. 10(b)는 방전 가공 전후의 공구의 길이 차이를 축전 용량에 따라 나타낸 그래프이다. Sintered SiC 가공보다 4H-SiC 가공에서 공구 마모가 작게 측정되었으며 축전 용량이 커질수록 공구 마모가 더 작게 발생하는 경향을 보인다. 축전 용량이 커질수록 Sintered SiC 가공에서의 공구 마모는 29 μm 에서 6 μm로 줄었으며 4H-SiC 가공에서는 8 μm에서 거의 0 μm 수준으로 줄어들었다. 폭 100 μm, 깊이 100 μm, 길이 400 μm의 홈 크기를 고려했을 때 공구 마모가 매우 작게 발생하였다. 이송 스테이지의 정밀도와 전기 접촉 등의 오차를 고려하더라도 수 마이크로 미터 수준의 길이 방향 마모는 매우 적은 수치이며 이에 대한 더 정밀한 실험이 필요하다. Tables 4와 5에 축전 용량에 따른 미세 홈의 표면 조도와 공구 마모량을 나타내었다.
4H-SiC와 Sintered SiC 가공 시 표면 거칠기와 공구 마모의 변화 경향성은 비슷하지만 크기에 차이가 발생하였다. 4H-SiC 가공 시 Sintered SiC보다 표면 거칠기가 더 크고 공구 마모는 더 작은 결과를 보였으며, 이는 Sintered SiC의 바인더 성분에 의해 차이가 발생한 것으로 추정된다. 본 연구에서 사용한 Sintered SiC는 바인더로 A1을 사용한 것이며, 바인더 재료에 따라 SiC 특성이 달라진다고 알려져 있다[15,22]. 해당 바인더로 인해 전기 저항(Electrical Resistivity)이 낮아지므로 방전 가공 시 방전 전류 강도(Current Intensity)가 더 커져 공구의 마모가 많이 발생한 것으로 판단된다[22-24]. 또한 소결 조건에 따라 파괴 인성(Fracture Toughness)에도 영향을 준다[25-28]. 이러한 이유로 4H-SiC와 Sintered SiC 가공 시 표면 거칠기와 공구 마모의 크기에 차이가 발생한 것으로 추정되며 추후 이에 대한 더 많은 연구가 필요하다.
5. 결론
본 연구에서는 PCD 공구를 이용하여 4H-SiC와 Sintered SiC에 구멍과 홈을 방전 가공하여 축전 용량에 따른 가공 표면, 공구 마모 등의 가공 특성을 연구하였다. 축전 용량은 5,600, 10,000, 100,000 pF을 사용하였고 두 종류의 SiC에서 모두 축전 용량이 커짐에 따라 구멍과 홈의 입구에 버가 많아지며 가공면에 발생하는 방전흔의 크기가 커지고 표면 거칠기가 커지는 경향을 보였다. 표면 거칠기는 Ra 0.2 μm 수준으로 측정되었다. 지름 100 μm의 공구로 길이 400 μm, 깊이 100 μm의 미세 홈을 가공하였을 때 길이 방향의 공구 마모를 관찰하였으며, Sintered SiC의 경우 6-29 μm, 4H- SiC의 경우 10 μm 이내의 공구 마모가 측정되었다. 이는 다른 재료의 방전 가공에 비해 매우 작은 공구 마모량이며, 이에 대해 더 많은 연구가 필요하다.
Acknowledgments
이 성과는 정부(과학기술정보통신부)의 재원으로 한국연구재단의 지원을 받아 수행된 연구임(No. 2022R1F1A1067961).
REFERENCES
-
Cho, Y., Hwang, J., Park, M.-S., Kim, B. H., (2022), Fabrication methods for microscale 3D structures on silicon carbide, International Journal of Precision Engineering and Manufacturing, 23(12), 1477-1502.
[https://doi.org/10.1007/s12541-022-00717-z]
-
Shin, H.-S., Kim, B.-H., Kim, G.-M., Chung, D.-K., Chu, C.-N., (2009), Micro electrochemical machining using a multi-function electrode, Transactions of the Korean Society of Mechanical Engineers A, 33(5), 496-501.
[https://doi.org/10.3795/KSME-A.2009.33.5.496]
-
Moon, I. Y., Chung, D. K., Kim, B. H., (2018), Fabrication of micro tool electrode by micro EDM using wear ratio, Journal of the Korean Society of Manufacturing Technology Engineers, 27(1), 1-6.
[https://doi.org/10.7735/ksmte.2018.27.1.1]
- Jo, C.-H., Kim, B.-H., Chu, C.-N., (2008), Electrochemical machining using a disk electrode for micro internal features, Journal of the Korean Society for Precision Engineering, 25(7), 139-144.
-
Lee, P. A., Nam, E., Kim, B. H., (2018), The state of the art in electrochemical micro machining technologies, Journal of the Korean Society for Precision Engineering, 35(3), 229-239.
[https://doi.org/10.7736/KSPE.2018.35.3.229]
- Kim, S.-H., Chung, D.-K., Kim, B.-H., Oh, K.-H., Jeong, S.-H., Chu, C.-N., (2009), Micromachining using hybrid of laser beam and electrical discharge machining, Journal of the Korean Society for Precision Engineering, 26(10), 108-115.
-
Park, J. W., Chung, D. K., Kim, B. H., Ok, J. G., Kim, W. J., Kim, Y. H., Chu, C. N., (2012), Wire electrical discharge machining of carbon nanofiber mats for field emission, International Journal of Precision Engineering and Manufacturing, 13(4), 593-599.
[https://doi.org/10.1007/s12541-012-0076-5]
-
Chung, D. K., Shin, H. S., Kim, B. H., Chu, C. N., (2011), High frequency micro wire EDM for electrolytic corrosion prevention, International Journal of Precision Engineering and Manufacturing, 12(6), 1125-1128.
[https://doi.org/10.1007/s12541-011-0150-4]
-
Suzuki, H., Okada, M., Asai, W., Sumiya, H., Harano, K., Yamagata, Y., Miura, K., (2017), Micro milling tool made of nano-polycrystalline diamond for precision cutting of SiC, CIRP Annals, 66(1), 93-96.
[https://doi.org/10.1016/j.cirp.2017.04.017]
-
Tan, T.-H., Yan, J., (2017), Atomic-scale characterization of subsurface damage and structural changes of single-crystal silicon carbide subjected to electrical discharge machining, Acta Materialia, 123, 362-372.
[https://doi.org/10.1016/j.actamat.2016.10.045]
-
Kliuev, M., Maradia, U., Boccadoro, M., Perez, R., Stirnimann, J., Wegener, K., (2016), Experimental study of EDM-drilling and shaping of SiSiC and SiC, Procedia CIRP, 42, 191-196.
[https://doi.org/10.1016/j.procir.2016.02.269]
-
Bilal, A., Jahan, M. P., Talamona, D., Perveen, A., (2018), Electro-discharge machining of ceramics: A review, Micromachines, 10(1), 10.
[https://doi.org/10.3390/mi10010010]
-
Schubert, A., Zeidler, H., Kühn, R., Hackert-Oschätzchen, M., (2015), Microelectrical discharge machining: A suitable process for machining ceramics, Journal of Ceramics, 2015, 470801.
[https://doi.org/10.1155/2015/470801]
-
Ji, R., Liu, Y., Zhang, Y., Cai, B., Ma, J., Li, X., (2012), Influence of dielectric and machining parameters on the process performance for electric discharge milling of SiC ceramic, The International Journal of Advanced Manufacturing Technology, 59(1), 127-136.
[https://doi.org/10.1007/s00170-011-3493-1]
-
Zeller, F., Ojha, N., Müller, C., Reinecke, H., (2014), Electrical discharge milling of silicon carbide with different electrical conductivity, Key Engineering Materials, 611-612, 677-684.
[https://doi.org/10.4028/www.scientific.net/KEM.611-612.677]
-
Sim, D. B., Yang, C. Y., Kim, B. H., (2022), Machining of Vshaped microchannel on cemented carbide using PCD tools, Journal of the Korean Society for Precision Engineering, 39(10), 747-752.
[https://doi.org/10.7736/JKSPE.022.083]
-
Moon, I. Y., Kim, B. H., (2013), Micro machining of titanium alloy using polycrystalline diamond tools, Journal of the Korean Society for Precision Engineering, 30(3), 284-291.
[https://doi.org/10.7736/KSPE.2013.30.3.284]
-
Lee, U. S., Yang, C. Y., Lee, J. H., Kim, B. H., (2021), Micro drilling of single crystal SiC using polycrystalline diamond tool, Journal of the Korean Society for Precision Engineering, 38(7), 471-478.
[https://doi.org/10.7736/JKSPE.021.013]
- Doan, C. X., Kim, B.-H., Chung, D.-K., Chu, C.-N., (2011), Fabrication of PCD micro tool and its hybrid micro machining, Journal of the Korean Society for Precision Engineering, 28(6), 694-700.
-
Park, J. A., Lee, U. S., Kim, B. H., (2020), Micro pin fabrication of tungsten carbide using polycrystalline diamond, Journal of the Korean Society for Precision Engineering, 37(11), 791-796.
[https://doi.org/10.7736/JKSPE.020.085]
-
Na, Y., Kim, B. H., (2019), Effect of vibration and machining area in the fabrication of micro tool by reverse EDM, Journal of the Korean Society for Precision Engineering, 36(2), 169-175.
[https://doi.org/10.7736/KSPE.2019.36.2.169]
-
Hong, S., Kao, P., (1991), Mechanical properties of Al-SiC composites made by resistance sintering of mechanically alloyed powders, Materials Science and Engineering: A, 148(2), 189-195.
[https://doi.org/10.1016/0921-5093(91)90821-4]
-
Luis, C., Puertas, I., Villa, G., (2005), Material removal rate and electrode wear study on the EDM of silicon carbide, Journal of Materials Processing Technology, 164-165, 889-896.
[https://doi.org/10.1016/j.jmatprotec.2005.02.045]
-
Sharma, D., Hiremath, S. S., (2021), Review on tools and tool wear in EDM, Machining Science and Technology, 25(5), 802-873.
[https://doi.org/10.1080/10910344.2021.1971711]
-
Zhao, Y., Kunieda, M., Abe, K., (2016), EDM mechanism of single crystal SiC with respect to thermal, mechanical and chemical aspects, Journal of Materials Processing Technology, 236, 138-147.
[https://doi.org/10.1016/j.jmatprotec.2016.05.010]
-
Kaur, S., Cutler, R. A., Shetty, D. K., (2009), Short?crack fracture toughness of silicon carbide, Journal of the American Ceramic Society, 92(1), 179-185.
[https://doi.org/10.1111/j.1551-2916.2008.02829.x]
-
Magnani, G., Brentari, A., Burresi, E., Raiteri, G., (2014), Pressureless sintered silicon carbide with enhanced mechanical properties obtained by the two-step sintering method, Ceramics International, 40(1), 1759-1763.
[https://doi.org/10.1016/j.ceramint.2013.07.075]
-
Barak, Y., Srivastava, A., Osovski, S., (2019), Correlating fracture toughness and fracture surface roughness via correlation length scale, International Journal of Fracture, 219(1), 19-30.
[https://doi.org/10.1007/s10704-019-00377-7]
Undergraduate student in the School of Mechanical Engineering, Soongsil University. Her research interest is micro machining.
E-mail: jhlee23@soongsil.ac.kr
M.S. student in the department of Mechanical Engineering, Graduate School, Soongsil University, Korea. His research interest is micro machining.
E-mail: cyyangmech@soongsil.ac.kr
Professor in the School of Mechanical Engineering, Soongsil University. His research topics are micro mechanical and non-conventional machining processes.
E-mail: bhkim@ssu.ac.kr