
비정질 탄소 분말 첨가에 따른 퓨란 전구체 탄화 공정의 열분해 수축 저감 연구
Copyright © The Korean Society for Precision Engineering
This is an Open-Access article distributed under the terms of the Creative Commons Attribution Non-Commercial License (http://creativecommons.org/licenses/by-nc/3.0) which permits unrestricted non-commercial use, distribution, and reproduction in any medium, provided the original work is properly cited.
Abstract
Vitreous carbon (VC) is an excellent material for glass molding due to its high hot hardness and low adhesion to glass materials. As a low-cost VC micro/nano mold fabrication method, carbonization of replicated Furan precursor has been investigated for various glass molded micro/nano optical and fluidic devices. One of the critical issues identified in the method is the substantial pyrolysis shrinkage (~22%) during the carbonization process. In this study, a method of minimizing pyrolysis shrinkage by adding VC powder to the initial Furan resin mixture was investigated. The mixing ratio of Furan resin, initiator, and ethanol was experimentally optimized for each VC powder mixing ratio, and the effects of the VC powder mixing ratio on the pyrolysis shrinkage of VC mold were examined. As the VC powder mixing ratio increased from 0% to 40%, we observed a reduction in the shrinkage ratio from 22.18% to 12.89% aligning closely with theoretical expectations.
Keywords:
Vitreous carbon, Pyrolysis shrinkage, Carbonization, Vitreous carbon mold, Glass molding키워드:
비정질 탄소, 열분해 수축, 탄화, 비정질 탄소 몰드, 유리성형1. 서론
기계적/광학적 성능이 우수한 유리소재를 이용한 마이크로/나노 구조물의 저가 제작기술로서 유리소재와 몰드를 소재의 유리전이온도 이상으로 가열하여 압축하는 마이크로/나노 유리 성형 기술이 연구되고 있다. 유리성형 공정의 몰드 소재는 높은 고온 경도, 낮은 열팽창 계수, 낮은 표면에너지 등의 특성을 가져야 하며, 마이크로/나노 유리성형을 위해 실리콘, 실리콘 카바이드, 텅스텐카바이드, 비정질 탄소(Vitreous Carbon, VC) 등을 이용한 몰드 제작 기술이 연구되었다[1-3]. 다양한 몰드 소재중 VC는 높은 열적 우수성을 가지며, 유리소재와 이형특성이 우수하여 유리성형을 위한 최적의 몰드 소재로 알려져 있다.
마이크로/나노 VC 몰드의 제작을 위해 열적, 기계적, 화학적 에너지를 이용한 직접가공방법이 시도되었다. Youn 등은 VC 평판상에 Focused Ion Beam (FIB) 밀링 및 Laser Machining, Mechanical Machining 공정을 통해 마이크로/나노 VC 몰드를 제작하고, Pyrex Glass 및 Quartz 소재의 유리성형을 보고하였다[4]. Prater 등은 Reactive Ion Etching 공정을 통해 VC 평판상에 마이크로 패턴을 형성하고 저 융점 유리소재를 이용한 유리 성형을 통해 회절광학소자를 제작하였다[5]. 직접가공을 통한 VC 몰드 제작공정은 VC 소재의 높은 열적, 기계적, 화학적 내구성으로 인해 높은 에너지가 요구되며, 가공속도가 느린 단점을 갖는다. 이에 본 연구팀은 VC 소재가 고탄소 고분자의 탄화 과정으로 제작되는 특성을 이용하여, 고탄소 고분자인 Furan 수지의 복제공정을 통해 마이크로/나노 구조를 갖는 Furan 전구체를 제작하고 이의 탄화 공정을 통해 VC 몰드를 제작하는 공정을 개발하고[6], 이를 이용하여 마이크로유체칩[7], 마이크로렌즈어레이[8], 마이크로프레넬 렌즈[9], 나노 그레이팅[10], 반사 방지 나노패턴[11], 플라즈모닉 나노닷 어레이[12] 등 다양한 유리 마이크로/나노 구조를 제작하였다. Furan 수지의 복제 및 탄화 공정으로 제작되는 VC 몰드는 탄화과정에서 약 22%의 열분해 수축이 발생하며, 이러한 수축은 수지의 표면과 내부의 수축량 차이에 의해 비 선형적인 특성을 가진다[13].
복제 및 탄화 공정을 이용한 VC 몰드 제작과정에서 발생하는 큰 수축은, 수축을 고려한 마스터 패턴의 설계를 통해 보정될 수 있으나[9], 큰 수축량은 마스터 제작 가공비용 상승 및 VC 몰드 제작 공정에서 결함 발생 가능성을 증가시키는 문제점이 있다. 또한 수축예측의 오차값은 전체 수축량 값에 비례하므로 탄화과정에서의 수축량을 최소화할 수 있다면 보다 정확한 수축 보정이 가능하다. 본 연구에서는 Furan 수지의 복제 및 탄화공정으로 제작되는 비정질 탄소 몰드 제작공정시 발생하는 수축량을 저감하기 위해, Fig. 1과 같이 초기 Furan 수지에 VC 분말을 혼합하고, Polydimethylsiloxane (PDMS) 몰드를 이용한 복제 및 탄화공정을 수행함으로써 수축율이 저감된 비정질 탄소 몰드 제작공정을 개발한다. 수축율 평가를 위해 등간격의 라인 형상의 Photoresist 마스터를 이용하여 PDMS 몰드를 제작하고 Furan 수지 VC 분말의 혼합비에 따른 VC 몰드 제작과정에서의 수축율 변화를 분석하였다.
2. 실험 방법
2.1 Ball Milling 공정을 통한 VC 분말의 제작
Furan 수지와 혼합할 VC 분말의 제작을 위해 단순 직육면체 형상의 VC 블록을 제작하고 이를 파쇄한 뒤, Ball Milling 공정을 수행하였다. VC 블록을 제작하기 위한 Furan 전구체 성형을 위해 내부 부피가 30 × 30 × 10 mm3 인 PDMS 용기를 제작하였다. 3D 프린터를 이용하여 PDMS 용기의 역상 형태의 마스터를 출력하고, 마스터 상에 Sylgard 184 (Dow Corning Co., Ltd., USA)와 경화제가 10 : 1의 무게비로 혼합된 수지를 붓고 Hot Plate를 이용하여 80°C에서 약 3시간 동안 경화하였다. 제작된 PDMS 용기에 Furan 수지(Phenol-Formalin, Kangnam Chemical Co., Ltd., Republic of Korea)와 p-Toluenesulfonic Acid (p-TSA), 에탄올을 500 : 1 : 50의 무게비로 혼합하여 부은 뒤, 100°C의 대류오븐에서 약 3시간 동안 열경화 공정을 진행하였다. 경화된 Furan 전구체를 PDMS 용기에서 이형 한 뒤 진공 퍼니스를 이용하여, 진공 분위기에서 1,000°C까지 빠르게 승온하고 10시간 유지한 뒤 냉각하는 공정으로 탄화하였다.
VC 블록의 제작을 위한 경화 및 탄화 공정은 VC 몰드 제작을 위한 경화 및 탄화 공정 대비 매우 빠른 속도로 진행되었으며, 빠른 경화 및 탄화 공정에서 Furan 수지 내부에서 발생하는 가스의 급격한 분출에 의해, 다수의 크랙 및 버블 결함이 발생하였다. 그러나 제작된 VC 블록은 파쇄한 뒤 Ball Milling을 통해 VC 분말을 제작하기 위한 것으로, 크랙 및 버블 결함은 후속 VC 블록의 파쇄 및 Ball Milling 공정에서 긍정적인 효과로 작용하므로, 결함여부와 관계없이 빠른 VC 블록의 제작 및 충분한 탄화공정이 완료될 수 있도록 공정 조건이 선정되었다. 제작된 VC 블록을 망치로 1차 파쇄하여 평균 약 1-2 mm의 VC 입자를 제작하였으며, 이후 Plantary Ball Mill PM 100 (Youwantech, Korea)에 직경 10 mm의 Zirconia Ball과 함께 3시간 동안 Ball Milling을 진행하여 직경 약 1-5 μm 크기의 VC 분말을 제작하였다.
2.2 실리콘 마스터 및 PDMS 몰드 제작
VC 분말 첨가에 따른 수축율 변화 특성을 분석하기 위해 등 간격의 라인 형상을 갖는 마스터 패턴을 실리콘 기판상에 제작하였다. 4인치 실리콘 웨이퍼 상에 SU-8 3050 (Microchem, Co., USA)을 도포하고 3,000 RPM에서 30초간 Spin Coating하여 높이 50 μm의 PR 코팅층을 형성하였다. Hot Plate를 이용하여 110°C에서 15분간 Soft Baking을 진행하였으며, 선폭 50 μm의 라인 패턴이 100 μm 간격으로 형성된 필름 마스크를 이용하여 노광공정을 진행하였다. 노광기의 Exposure Intensity는 250 mJ/cm2이며 노광시간은 15초로 설정되었다. Hot Plate를 이용하여 110°C에서 5분간 Post Exposure Bake를 진행한 뒤, SU-8 Developer 용액에 6분간 Developing을 진행하였다. Post Baking 공정은 Hot Plate에서 150°C에서 5분간 진행하였으며, 최종적으로 Ethanol을 이용하여 세척을 진행하여, Fig. 2(a)와 같이 선폭 50 μm, 간격 100 μm의 라인패턴이 50 μm 깊이의 음각 형태로 형성된 PR 마스터 패턴을 제작하였다. 제작된 마스터상에 Sylgard 184와 경화제를 무게비 10 : 1로 혼합하여 붓고 경화하여 Fig. 2(b)와 같이 양각의 라인 패턴 형상이 형성된 PDMS 몰드를 제작하였다. PDMS 경화 과정에서 발생하는 수축을 방지하기 위해 PDMS 몰드 제작을 위한 경화 공정은 상온에서 48시간 동안 진행되었다[14].
2.3 액상 Furan 수지와 VC 분말 혼합물 배합 최적화
액상의 Furan 수지는 p-TSA 경화제와 혼합되며 열경화반응이 시작된다. 경화제 혼합 과정에서 발생하는 기포와 경화반응의 부산물로 산출되는 기체는 경화과정 중에 외부로 배출되어야 하나 초기 Furan 수지의 높은 점도는 내부 기포 및 가스의 배출을 어렵게 하여 내부 결함을 발생시키는 원인이 된다. 이에 Furan 수지와 p-TSA 경화제 혼합과정에서 Furan 수지 대비 10% 무게비 수준의 에탄올을 첨가하여 혼합물의 점도를 제어한다. Furan 수지에 VC 분말을 혼합하는 경우 혼합물의 점도가 추가적으로 증가하므로, VC 분말 혼합 비율에 따라 안정적인 성형 공정이 가능한 수준의 점도를 확보하기 위해 추가적인 에탄올 첨가가 요구된다. 혼합물에 추가되는 에탄올은 성형과정에서 모두 증발하여 Furan 전구체의 탄화과정 에서 발생하는 열분해 수축에는 영향을 주지 않으나[6], 과도한 에탄올 첨가는 Furan 수지 혼합물의 경화를 지연시키거나, 혼합물 내 Furan 수지 함유량을 감소시켜 PDMS 몰드의 마이크로캐비티를 Furan 수지가 충진하지 못하는 현상을 야기하므로, 성형 공정에서 크랙 및 기포 결함이 발생하지 않고, 원활한 마이크로패턴 복제 공정이 가능한 최적 에탄올 첨가 무게비를 Table 1과 같이 실험적으로 선정하였다. VC 분말 혼합비(0-40%)에 따라 Furan 수지와 VC 분말 혼합 무게비를 선정하였으며, p-TSA의 경우 Furan 수지 무게 대비 0.2% 무게로 선정하고, 에탄올의 경우 Furan 수지와 VC 분말 혼합 무게 대비 10-40%로 선정되었다. 선행 연구를 통해 Furan 수지, p-TSA, 에탄올의 무게비 500 : 1 : 50에서(VC 분말 혼합비 0%) 결함이 없는 Furan 전구체를 제작할 수 있음을 확인하였으며, VC 분말 혼합비 10-20%에서는 추가적인 에탄올 첨가 없이도 안정적인 성형공정이 가능함을 확인하였다. 30%의 VC 분말을 혼합하는 경우 점도 증가로 인해 Furan 수지와 VC 분말의 혼합 무게 대비 30%의 에탄올 첨가 시 안정적인 공정이 가능함을 확인하였고, VC 분말 40% 혼합비의 경우 혼합 무게 대비 40%의 에탄올 첨가가 필요함을 확인하였다. 50% 이상의 VC 분말 혼합비에서는 혼합물에서 Furan 수지의 비율이 감소하여 에탄올 첨가량과 관계없이 안정적인 공정이 불가능함을 실험적으로 확인하였다.
2.4 Furan 수지 혼합물 경화 및 탄화공정
각각의 VC 분말 혼합비율에 따라 최적 비율의 에탄올이 첨가된 Furan 수지 혼합물을 복제된 PDMS 몰드에 도포하고, 상온에서 3일간 1차 경화를 진행한 뒤, 대류오븐에서 0.5°C/min의 승온 속도로 100°C까지 가열하고 2시간 동안 온도를 유지하는 2차 경화 공정을 진행하였다. PDMS 몰드에서 이형된 VC 분말 첨가 Furan 전구체는 Back Polishing을 통해 두께를 2 mm 내외로 가공한 뒤, 진공 퍼니스를 이용하여 탄화 하였다. 탄화공정은 10-3Torr의 진공분위기에서 0.2°C/min의 속도로 600°C까지 승온한 뒤 1°C/min 의 속도로 1,000°C까지 승온하였고, 1,000°C에서 10시간 동안 온도를 유지하고 자연 냉각하는 순서로 진행되었다. 매우 느린 경화 및 탄화 공정은 Furan 수지의 경화 및 탄화 공정에서 발생하는 기체의 배출에 의해 발생하는 결함을 방지하기 위해 선정되었다. Fig. 3은 30%의 VC 분말이 첨가된 혼합물을 이용하여 제작된 Furan 전구체 및 탄화된 VC 몰드의 SEM 사진을 보여준다. 경화 및 탄화과정에서 표면에 노출된 VC 분말에 의해 일부 거친 표면을 확인할 수 있으나 라인패턴이 정확히 복제된 것을 확인할 수 있다.
2.5 수축율 및 표면거칠기 측정
제작된 VC 몰드 표면에 형성된 라인패턴 Pitch를 광학현미경을 이용하여 측정하여 VC Powder 첨가량에 따른 VC 몰드의 수축율을 분석하였다. 설계된 라인패턴의 Pitch는 100 μm이며, 5개 라인마다 존재하는 긴 라인패턴의 간격은 500 μm로 설계되었다. Fig. 4는 각각의 VC 분말 혼합비에 따라 제작된 VC 몰드의 현미경 사진에서 긴 라인패턴의 간격을 측정한 결과이다. VC 분말의 첨가량이 증가함에 따라 긴 라인 패턴간 거리가 증가하는 것을 확인할 수 있으며, 이는 VC 분말의 첨가에 따라 탄화과정에서 발생하는 열분해 수축률이 감소함을 직관적으로 보여준다. 한편 VC 분말이 첨가된 Furan 수지 혼합물을 이용하여 제작된 VC 몰드의 경우(Figs. 4(b)-4(e)) VC 분말이 포함되지 않은 VC 몰드(Fig. 4(a))와 비교할 때 매우 거친 표면을 갖는 것을 확인할 수 있으며, 이는 1-5 μm 크기를 갖는 VC 분말이 경화 및 복제 공정에서 표면에 노출되었기 때문이다. VC 분말 첨가에 따른 표면거칠기 영향을 확인하기 위해 Confocal Microscopy (OLS4100-SWF, Olympus Co. Ltd., Japan)를 이용하여 제작된 시편의 평면 위치에서 표면 거칠기를 측정하였다.
3. 결과 및 고찰
제작된 마스터, PDMS 몰드, Furan 전구체, VC 몰드의 긴 라인 패턴간의 거리(5개 위치에서의 평균값), 설계치(500 μm) 대비 수축율, 표면거칠기를 측정하여 Table 2에 정리하였다. 초기 PR 마스터 패턴의 긴 라인 패턴간 거리는 측정오차를 고려할 때 설계치(500 μm)와 동일값으로 간주될 수 있는 499.57 μm이며, PDMS 몰드 역시 499.52 μm으로 장시간 상온 경화로 제작된 PDMS 몰드의 경우 수축이 발생하지 않음을 확인하였다.

Summary of the measured length between long line pattern, shrinkage ratio, and surface roughness (Ra) of master, PDMS mold, VC-powder added furan precursors, and VC mold with different VC-filler addition ratio
서로 다른 VC 분말 혼합비를 가진 Furan 전구체의 수축율은 모두 약 1.7% 수준으로 VC분말 첨가에 따른 Furan 전구체 제작 공정에서의 수축율 차이는 확인되지 않았다. 이는 VC 분말이 첨가된 Furan 수지 혼합물의 경화과정에서 Furan 수지간 Cross Linking에 의한 수축은 VC 분말에 의해 방해받지 않고 VC 분말간 거리의 감소로 나타나기 때문이다.
최종 제작된 VC 몰드의 수축율은 VC 분말의 혼합비에 따라 선형적으로 감소하는 경향을 보여준다. 이는 VC 분말의 혼합비가 증가함에 따라 전체 질량에서 Furan 수지가 차지하는 비율이 감소하고, VC 분말의 경우 탄화 공정에서 열분해가 발생하지 않으므로 탄화과정에서 열분해에 의한 수축은 Furan 수지의 질량비율에 비례하기 때문이다. VC 분말 첨가 공정에서 VC 몰드의 수축율 S는 VC 분말이 첨가되지 않은 Furan 전구체의 탄화에 의한 수축율을 S0라고 하고, VC 분말의 혼합비(%)을 R이라고 할 때 식(1)과 같이 표현될 수 있다.
(1) |
Fig. 5는 VC 분말 첨가량에 따른 VC 몰드의 수축량 측정값과 식(1)에 의한 예측값을 비교한 것으로 두 값이 거의 일치함을 알 수 있다.
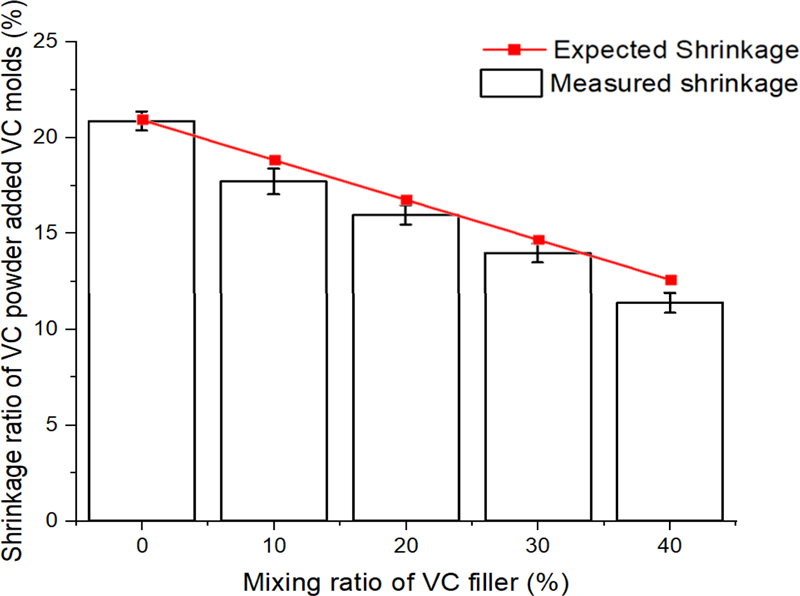
Comparison of measured shrinkage of VC mold and expected shrinkage for the mixing ratio of VC powder
한편 표면 거칠기값은 VC 분말을 혼합하는 경우 Furan 전구체 단계에서부터 그 값이 Ra 기준 약 1.5-2.5 μm으로 증가하며 탄화 공정이후에도 유사한 표면거칠기 값을 보여준다. 이는 경화 및 탄화 과정에서 표면에 노출된 VC 분말(입자 크기 1-5 μm)에 의한 것이다.
4. 결론
Furan 수지의 복제 및 탄화 공정으로 제작되는 마이크로/나노 VC 몰드는 유리 마이크로/나노 구조물을 유리성형 공정으로 제작함에 있어 많은 장점을 가지나, Furan 전구체의 탄화과정에서 필연적으로 발생하는 약 22%의 수축은 기술의 활용에 여러 걸림돌로 작용하고 있다. 본 연구에서는 VC 분말을 초기 Furan 수지 혼합물에 첨가함으로써 탄화과정에서 발생하는 수축을 저감할 수 있는지 그 가능성을 확인하였다. VC 분말의 혼합에 따른 점도 상승 문제는 혼합비에 따라 에탄올을 추가함으로써 최대 40% VC 분말 혼합비의 VC 몰드를 제작할 수 있었다. 전구체 성형 단계에서 발생하는 미량의 수축은 VC 분말의 첨가에 영향을 받지 않았으나, 탄화 공정에서 발생하는 대량의 수축은 VC 분말의 혼합비에 따라 이론값과 같이 선형적으로 감소함을 확인하였다. VC 분말 미첨가 시 VC 몰드 제작공정의 수축율은 22.18% 였으나 40%의 VC 분말 혼합비에서 12.89%의 수축율을 달성하였다.
본 연구에 사용한 VC 분말의 크기는 1-5 μm인 관계로 VC 분말 첨가 시 표면 거칠기가 급격히 증가하는 문제가 있으나, 이는 향후 나노스케일 크기의 VC 분말을 적용함으로써 개선될 수 있으리라 예상된다.
NOMENCLATURE
VC : | Vitreous Carbon |
PDMS : | Polydimethylsiloxane |
p-TSA : | p-Toluenesulfonic Acid |
S : | Shrinkage Ratio of VC Mold |
S0 : | Shrinkage Ratio of VC Mold without VC Powder |
R : | Mixing Ratio of VC Powder |
Acknowledgments
본 연구는 정부(과학기술정보통신부)의 소재융합사업(No. 2020M3D1A2101795) 및 이공분야 기초연구사업(No. 2021R1A2C200445811)의 지원으로 수행되었으며, 2021년도 중앙대학교 연구년 결과물로 제출됨
REFERENCES
-
Asgar, M. A., Kim, J., Haq, M. R., Kim, T., Kim, S.-M., (2021), A comprehensive review of micro/nano precision glass molding molds and their fabrication methods, Micromachines, 12(7), 812.
[https://doi.org/10.3390/mi12070812]
-
Hwang, Y., Cha, D.-H., Kim, J.-H., Kim, H.-J., (2012), Ultraprecision grinding of glassy carbon core for mold press lens, Journal of the Korean Society for Precision Engineering, 29(3), 261-265.
[https://doi.org/10.7736/KSPE.2012.29.3.261]
-
Kim, Y.-J., Choi, H.-J., Yeo, W.-J., Jeong, J.-Y., Kim, Y.-S., Kim, G.-H., (2020), A study on the characteristics of ultra-precision surface cutting of the mold material (STAVAX) for the development of large satellite lens, Journal of the Korean Society for Precision Engineering, 37(11), 819-825.
[https://doi.org/10.7736/JKSPE.020.088]
-
Youn, S., Takahashi, M., Goto, H., Maeda, R., (2006), Microstructuring of glassy carbon mold for glass embossing–Comparison of focused ion beam, nano/femtosecond-pulsed laser and mechanical machining, Microelectronic Engineering, 83(11-12), 2482-2492.
[https://doi.org/10.1016/j.mee.2006.05.007]
-
Prater, K., Dukwen, J., Scharf, T., Herzig, H. P., Plöger, S., Hermerschmidt, A., (2016), Micro-structuring of glassy carbon for precision glass molding of binary diffractive optical elements, Optical Materials Express, 6(11), 3407-3416.
[https://doi.org/10.1364/OME.6.003407]
-
Ju, J., Lim, S., Seok, J., Kim, S.-M., (2015), A method to fabricate low-cost and large area vitreous carbon mold for glass molded microstructures, International Journal of Precision Engineering and Manufacturing, 16, 287-291.
[https://doi.org/10.1007/s12541-015-0038-9]
-
Haq, M. R., Kim, Y. K., Kim, J., Ju, J., Kim, S.-M., (2019), Fabrication of all glass microfluidic device with superior chemical and mechanical resistances by glass molding with vitreous carbon mold, Journal of Micromechanics and Microengineering, 29(7), 075010.
[https://doi.org/10.1088/1361-6439/ab1f99]
-
Kim, Y. K., Ju, J. H., Kim, S.-M., (2018), Replication of a glass microlens array using a vitreous carbon mold, Optics express, 26(12), 14936-14944.
[https://doi.org/10.1364/OE.26.014936]
-
Kim, Y. K., Haq, M. R., Kim, S.-M., (2019), Glass molding of all glass Fresnel lens with vitreous carbon micromold, Optics Express, 27(2), 1553-1562.
[https://doi.org/10.1364/OE.27.001553]
-
Kim, J., Kim, Y. K., Ju, J., Asgar, M. A., Kim, T., Kim, S.-M., (2022), Nanoimprinting of soda–lime glass using vitreous carbon nanomold for high-temperature stable nanophotonic crystal filter, Optics & Laser Technology, 150, 107970.
[https://doi.org/10.1016/j.optlastec.2022.107970]
-
Haq, M. R., Kim, J., Yeom, J.-W., Ryu, S., Asgar, M. A., Kim, Y. K., Kim, S.-M., (2020), Fabrication of cross-sinusoidal anti-reflection nanostructure on a glass substrate using imperfect glass imprinting with a nano-pin array vitreous carbon stamp, Micromachines, 11(2), 136.
[https://doi.org/10.3390/mi11020136]
-
Badshah, M. A., Kim, J., Yeom, J., Abbas, N., Haq, M. R., Kim, Y., Lu, X., Kim, S.-M., (2021), Glass nanoimprinted plasmonic nanostructure for high power laser stable surface-enhanced Raman spectroscopy substrate, Applied Surface Science, 542, 148587.
[https://doi.org/10.1016/j.apsusc.2020.148587]
-
Haq, M. R., Kim, J., Ju, J., Kim, Y. K., Chang, W.-J., Kim, S.-M., (2019), Development of shrinkage model of micro structured vitreous carbon mold for glass molding, Journal of Mechanical Science and Technology, 33, 5747-5752.
[https://doi.org/10.1007/s12206-019-1118-z]
-
Badshah, M. A., Jang, H., Kim, Y. K., Kim, T.-H., Kim, S.-M., (2014), Development of a rapid cure polydimethylsiloxane replication process with near-zero shrinkage, Journal of Micro/Nanolithography, MEMS, and MOEMS, 13(3), 033006-033006.
[https://doi.org/10.1117/1.JMM.13.3.033006]
Research Professor in Chung-Ang University. His research interest is fabrication of glass molded optical components using vitreous carbon mold
E-mail: kykdes@cau.ac.kr
Master in Mechanical System Engineering, Chung-Ang University. His research interest was micro metal forming using vitreous carbon mold.
E-mail: hdi2305@naver.com
Chief Technical Officer in Goodpnc Co., Ltd.. His research interest was design and fabrication of optical components and systems.
E-mail: hmkim@goodpnc.com
Chief Executive Officer in Goodpnc Co., Ltd.. His research interest was design and fabrication of optical components and systems.
E-mail: shahn@goodpnc.com
Professor in Department of Computer Science and Engineering, Mechanical System Engineering, Chung-Ang University. His research interest is glass optical components, functional surface, and biosensors.
E-mail: smkim@cau.ac.kr