
무윤활 상태에서 3D 프린팅용 PLA 및 PETG 소재의 마모 현상에 관한 연구
Copyright © The Korean Society for Precision Engineering
This is an Open-Access article distributed under the terms of the Creative Commons Attribution Non-Commercial License (http://creativecommons.org/licenses/by-nc/3.0) which permits unrestricted non-commercial use, distribution, and reproduction in any medium, provided the original work is properly cited.
Abstract
With the recent development of 3D printing technology, various 3D printing materials have been developed and used. To utilize 3D-printed products with mechanical parts, studies on friction and wear characteristics according to relative motion between materials are required. However, tribology studies on 3D-printed materials are limited compared to those of the existing materials for mechanical parts. In this study, the frictional and wear characteristics are identified through a reciprocating wear test in non lubricated conditions between the Polylactic Acid (PLA) and Polyethylene Terephthalate Glycol (PETG) printed in the Fused Deposition Modeling (FDM) method. In the wear test between the same materials, the friction coefficient and wear rate were higher in the PLA than in the PETG, and PLA was deposited on the block due to high frictional heat. In the wear test of the PLA block and PETG bump, the wear of the PLA block decreased compared to the wear test between the same materials, but the wear of the PETG bump tended to increase. Therefore, it seems that the 3D-printed PETG may be more advantageous in terms of friction and wear than 3D-printed PLA during relative movement in a non lubricating condition.
Keywords:
3D printing material, Dry friction, Adhesive wear, Polylactic acid, Polyethylene terephthalate glycol키워드:
3D 프린팅 소재, 건식 마찰, 응착 마멸, 폴리젖산, 폴리에틸렌 테레프탈레이트 글리콜1. 서론
기계산업에 있어 부품의 다양화와 복잡화 추세에 따라 전통적인 기계 가공으로 구현하기 힘든 부품 생산을 위해 적층 제조(Additive Manufacturing, AM)에 관한 관심이 증가하고 있다[1]. 특히, 적층 제조 기술은 복잡한 구조를 가진 제품의 생산 시 금형을 필요로 하지 않기 시제품 생산에 있어 큰 장점을 가진다. 기존에는 주로 연구자들과 산업계 위주로 적층 제조 기술의 연구와 활용이 이루어졌으나, 3D 프린팅이라는 명칭으로 대중에게 알려지고 보급된 후 교육용이나 개인용으로 활용하는 경우도 많아지고 있다[2,3].
적층 제조용 소재는 플라스틱, 금속, 왁스, 고무, 세라믹 등 다양하며 현재도 많은 연구자들이 지속적으로 개발 중에 있다[4]. 그러나, 3D 프린팅과 그 소재들의 대중화에도 불구하고 활용되고 있는 소재들의 트라이볼로지(Tribology) 특성에 관한 연구는 많이 이루어지지 않고 있다.
Sim 등[5]은 폴리젖산(Polylactic Acid, PLA)을 이용한 FDM (Fused Deposition Modeling) 방식의 3D 프린팅에서 미끄럼 방향에 따른 트라이볼로지 특성을 조사하였다. 그들의 연구에서는 볼(Ball)을 이용한 왕복동 마모시험기(Reciprocating Wear Tester)를 이용하였으며 볼 소재로는 SUJ2 베어링 볼을 활용하였다. 실험결과, 출력된 패턴의 방향과 45° 방향으로 미끄럼 운동이 발생하는 경우 가장 낮은 마찰계수를 보임을 확인하였으나, 그들의 연구에서는 동일한 PLA 소재들 간의 마찰 및 마모에 관해서는 고려하지 않았다.
Jo 등[6]은 볼온디스크(Ball-on Disk)와 핀온디스크(Pin-on-disk) 마모 시험을 통해 무윤활 상태에서 SLA (Stereo Lithography Apparatus) 방식의 3D 프린팅용 유사 ABS 레진(Acrylonitrile Butadiene Styrene-like Resin, ABS-like Resin) 소재의 트라이볼 로지 특성에 관해 조사하였다. 그들의 연구에서는 SUS304과 SLA 방식으로 출력된 볼 및 핀(Pin)을 이용하였으며, 무윤활 상태에서는 유사 ABS 레진 간의 상대운동 조건보다 SUS304와 유사 ABS 레진 소재 간의 상대운동 조건이 마찰 및 마모 측면에서 유리함을 보여주었다.
Park 등[7]은 앞선 Jo 등의 연구를 바탕으로 서로 다른 동점도를 지닌 디메틸 실리콘 오일(Dimethyl Silicon Oil)을 활용한 볼온디스크 마모시험을 실시하였다. 그들은 동점도가 높은 실리콘 오일을 사용하여 유사 ABS 레진 간의 마찰 및 마모를 줄일 수 있음을 실험적으로 보여주었다.
Portoacă 등[8]은 핀온디스크 마모시험기를 활용하여 FDM 3D 프린팅 시 충전밀도(Infill Density)와 층 두께(Layer Thickness) 조건에 따른 PLA와 ABS의 마찰계수(Coefficient of Friction, COF)와 표면 거칠기(Surface Roughness)를 조사하였다. 그들의 연구에서는 마찰계수가 충전밀도와 층 두께에 따라 경향성을 보이지는 않았지만, 전반적으로 PLA는 얇은 층 두께(0.1 mm) 조건에서 높은 마찰계수를 보인 반면, ABS는 높은 두꺼운 층 두께에서 높은 마찰계수를 보였다. 마모 후 표면 거칠기의 경우, 높은 충진밀도와 두꺼운 층 두께 조건에서 높은 값을 보였다.
본 연구에서는 무윤활 상태에서 왕복동 마모 시험(Reciprocating Wear Test)을 통해 교육용 및 개인용으로 많이 활용되고 있는 FDM 방식의 3D 프린팅용 소재 중 PLA와 폴리에틸렌 테레프탈레이트 글리콜(Polyethylene Terephthalate Glycol, PETG)의 트라이볼로지 특성에 관한 기초연구를 수행하고자 한다.
2. 연구방법 및 내용
2.1 3D 프린팅
본 연구에서는 PLA 및 PETG 소재의 마찰 및 마모 시험을 위해 연구실에서 자체 제작한 FDM 방식의 3D 프린터를 활용하였다. 3D 프린터는 Fig. 1과 같이 CoreXY 방식으로 구동이 되며, 최대 500 × 500 × 450 mm3의 출력 사이즈를 가지고 있다. 그리고 소재의 출력은 구멍 직경 ϕ0.4 mm인 노즐을 사용하였다. 3D 프린팅 시 조건은 소재에 따라 아래 Table 1과 같으며 Figs. 2와 3과 같이 돌기형상(Bump)과 블록(Block)의 형태로 출력되었다.
2.2 마찰 및 마모 시험
FDM 3D 프린팅 소재의 마찰 및 마모 시험을 위해 자체 제작한 왕복동 마모 시험기를 활용하였다. 마모 시험기에는 Fig. 4와 같이 로드셀(Load Cell)을 장착하여 마모 시험 중 마찰력을 측정하였으며 무게 추를 이용하여 하중을 부가한다. 블록의 상하 왕복 길이는 50 mm이다.
왕복동 마모시험 시 하중은 9.81 N으로 고정하였으며, 미끄럼 속도(Sliding Velocity)를 0.1, 0.2, 0.3 m/s로 변화시키며 마모 과정 중 마찰계수와 시험 후 돌기와 블록의 마모량을 측정하였다. 실험은 동일 소재의 블록과 돌기의 마모 현상을 관찰 후 이종 소재들 간의 마모시험을 통해 낮은 마모 수준을 가지는 조합을 선정하고, 선정된 조합을 바탕으로 미끄럼 속도 변화에 따른 마찰 및 마모 특성을 파악하는 순서로 진행되었다. 3D 프린팅된 소재들 간의 미끄럼 운동 방향은 출력된 층의 방향을 기준으로 90°로 교차되도록 하였다. 마모시험 직후 시편의 온도는 열 화상카메라(TiS20, Fluke Corp.)를 이용하여 측정하였다.
소재의 마모율 측정에 있어 마모흔(Wear Mark)이 대칭적이지 않아 소재의 마모된 부피보다는 마모로 인한 소재 높이의 변화를 관찰하였다. 따라서 돌기의 마모 높이는 광학현미경(DVM6, Leica Microsystems)을 이용하여 마모흔의 직경을 측정한 후 3D 모델링 데이터를 이용하여 마모량(마모된 높이)을 계산하였으며, 블록의 마모는 마모흔의 표면 형상 측정을 통해 마모 깊이를 측정하였다.
3. 결과 및 고찰
3.1 온도특성
동일한 소재로 출력된 블록과 돌기의 상대운동을 통한 마찰 및 마모 현상을 측정하기 위해 PLA 블록-PLA 돌기, PETG 블록-PETG 돌기를 이용한 시험을 실시하였다. 하중은 앞서 언급한 바와 같이 9.81 N으로 고정하였으며, 미끄럼 속도를 0.1, 0.2, 0.3 m/s로 변화시켰다. 실험에서는 미끄럼 거리를 동일하게 하기 위하여 시험 시간을 조절하여 각 실험 별 총 미끄럼 거리가 60 m가 되도록 하였다. Fig. 5는 마모 시험 후 시편의 표면온도를 보여준다.
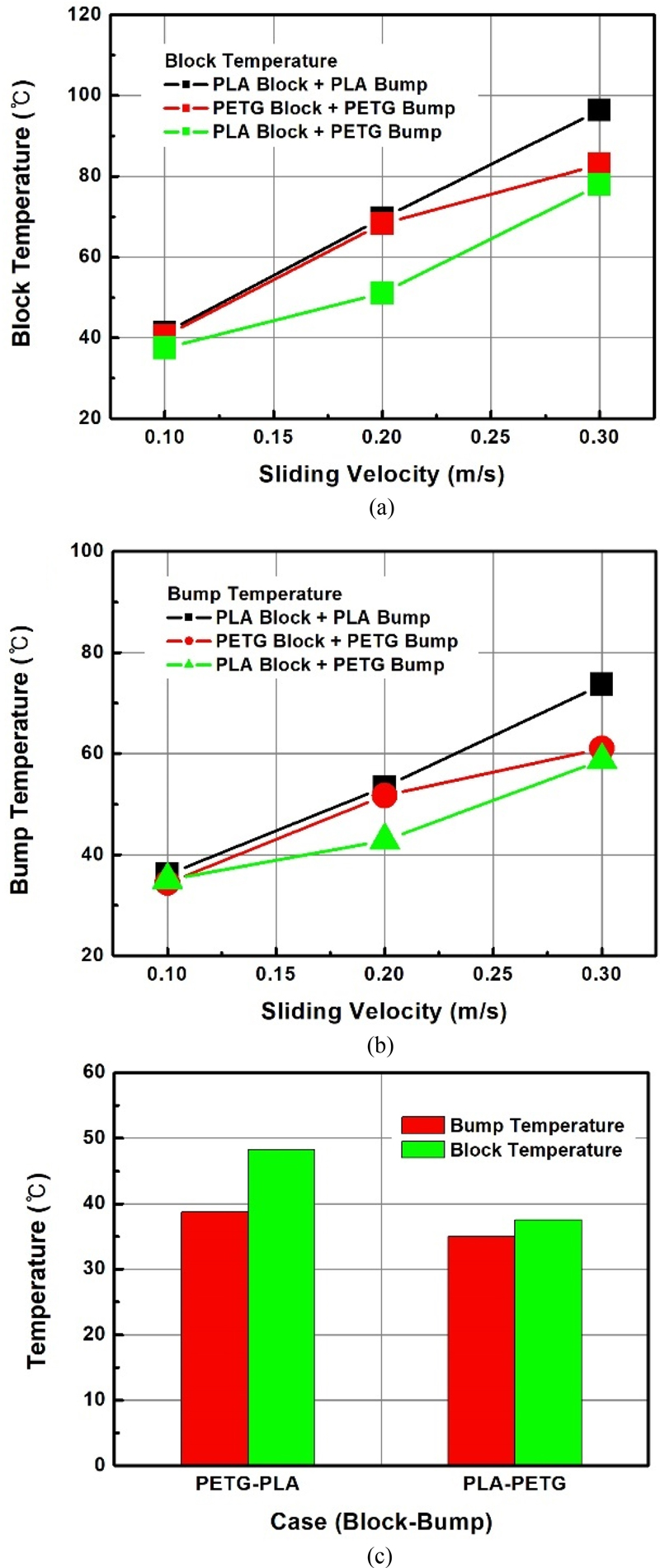
Temperature after wear test; (a) block, (b) bump, and (c) comparison of temperature between different 3D printed materials under 9.81 N and 0.1 m/s conditions
PLA 블록-PLA 돌기, PETG 블록-PETG 돌기를 이용한 실험에서 마모 시험 후 온도는 미끄럼 속도 증가에 따라 증가하는 경향을 보이며, PLA 소재가 PETG보다 상대운동 시 높은 마찰열이 발생하는 것으로 보이고 그 차이는 미끄럼 속도가 빠를수록 커지는 것이 확인되었다. 이러한 현상은 소재 사이의 마찰력(혹은 마찰계수)와 관련 있을 것으로 판단된다.
PLA 소재 간이 마모 시험의 경우 0.2 m/s 조건에서 돌기와 블록의 최고 온도가 각각 53.4, 69.6°C이며, 0.3 m/s 조건에서는 각각 73.7, 95.3°C였다. PLA 소재의 유리전이온도(Glass Transition Temperature)가 56.9°C임을 고려했을 때, 0.2 m/s 이상의 미끄럼 조건에서는 마찰열에 의해 PLA의 유리전이온도 이상에서 소재 간의 용착이 발생할 것으로 보인다. 반면 PETG의 경우, 유리전이온도가 85.0°C이며 0.3 m/s 조건에서 돌기와 블록의 최고 온도가 각각 61.0, 82.9°C로 유리전이온도 이하에서 마모됨을 알 수 있다.
이종 소재 간의 마모 특성 확인을 위해 PETG 블록-PLA 돌기, PLA 블록-PETG 돌기를 대상으로 0.1 m/s의 미끄럼 속도에서 비교 실험을 실시한 결과(Fig. 5(c)), PETG 블록-PLA 돌기의 접촉 조건에서 블록 온도 48.3°C, 돌기 온도 38.7°C로 블록 온도 37.5°C, 돌기 온도 35.0°C인 PLA 블록-PETG 돌기 접촉 조건보다 높은 온도 특성을 보였다.
이종 소재 간의 비교 결과에서 온도 특성이 낮은 PLA 블록-PETG 돌기 조건을 대상으로 한 미끄럼 속도의 증가 실험 결과를 Figs. 5(a)와 5(b)에 나타내었으며, 전반적으로 동일 소재 간의 시험 결과보다 낮은 온도 특성을 보이며 소재들의 유리전이온도 이하에서 마모가 발생함을 알 수 있다. Fig. 6은 0.3 m/s 조건에서 마모 시험 후 돌기와 블록의 온도 측정의 예를 보여준다.
3.2 마찰특성
Fig. 7은 PLA 블록-PLA 돌기와의 상대운동에서 미끄럼 거리에 따른 마찰계수의 변화를 보여준다. 0.1, 0.2, 0.3 m/s의 미끄럼 속도에서 평균 마찰계수는 각각 0.813, 1.277, 1.685로 측정되었다. 0.1 m/s 조건의 경우 마찰계수의 변화가 크지 않은 반면, 0.2 m/s의 조건에서는 마찰계수가 1.0 이상으로 증가한 이후 크게 변동하는 것을 확인할 수 있다. 0.3 m/s 조건에서는 마찰계수가 2.5 이상으로 크게 증가하다가 감소하는 경향을 보였다. 이러한 현상은 마찰과정에서 발생하는 마찰열과 관련 있을 것으로 보인다. 앞선 온도 측정 결과에 따르면 0.2 m/s 조건 이상에서 PLA 소재 간의 마찰에서의 온도는 유리전이온도 이상으로 증가하게 되어 소재의 융착이 발생할 가능성이 높아지기 때문으로 생각된다. 0.3 m/s의 조건에서는 Fig. 8과 같이 시험 후 블록의 마모가 발생하는 것이 아니라 용융된 돌기가 녹아 적층되며 블록 위 용착부가 다시 돌기의 형상을 불균일하게 마모시키는 현상이 관찰된다. 따라서 0.3 m/s 조건에서 실험 후반의 마찰계수 감소는 융착부에 의한 돌기의 불균일한 마모에 의한 것으로 판단된다.
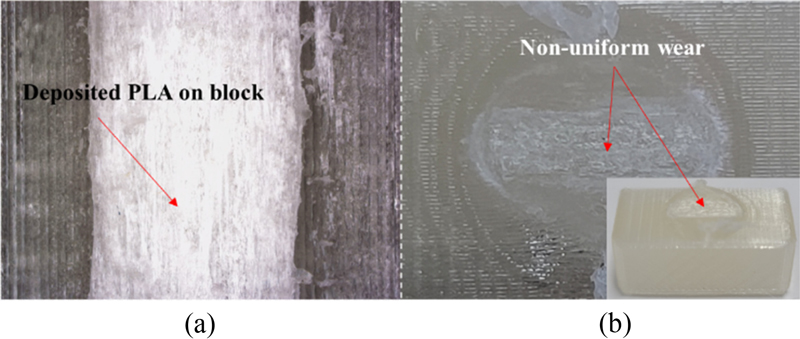
Images of PLA block and bump after wear test under 0.1 m/s condition; (a) deposited PLA on block and (b) non-uniform wear of bump
PETG 소재 간의 마모시험에서는 전반적으로 PLA 소재 간의 마모 시험보다 마찰계수가 낮은 것으로 확인되었다. Fig. 9는 PETG 블록-PETG 돌기와의 상대운동에서 미끄럼 거리에 따른 마찰계수의 변화를 보여준다. 0.1, 0.2, 0.3 m/s의 미끄럼 속도에서 평균 마찰계수는 각각 0.554, 1.227, 1.532로 측정되었다. 0.1 m/s 조건에서는 미끄럼이 진행됨에 따라 균일한 마찰계수를 보이는 반면, 0.2, 0.3 m/s 조건에서는 미끄럼이 진행됨에 따라 마찰계수가 다소 상승하는 경향을 보인다. 이는 미끄럼 거리의 증가에 따른 온도 상승과 마모에 따른 접촉면적 증가의 영향으로 판단된다.
Fig. 10은 PETG 블록-PLA 돌기와 PLA 블록-PETG 돌기의 상대운동에 따른 마찰계수를 보여주고 있으며, 마모시험 시 하중은 9.81 N, 미끄럼 속도는 0.1 m/s이다. 이종 소재 간의 상대 운동에서 마찰계수는 PLA 블록-PETG 돌기의 경우가 PETG 블록-PLA 돌기의 경우보다 낮은 것을 확인할 수 있다. 따라서 Fig. 5(c)에서 제시한 이종 소재 간의 마모 시 온도 특성은 마찰계수의 차이에 기인한다고 볼 수 있다.
Fig. 11은 PLA 블록-PETG 돌기의 상대운동에 따른 마찰계수를 보여주고 있다. 평균 마찰계수는 0.1, 0.2, 0.3 m/s 조건에서 각각 0.427, 0.762, 1.770이었다. 0.1 m/s 조건에서 마찰계수는 초기 0.155-0.230로 낮게 형성되다가 급격히 증가하기 시작한다. 이러한 현상은 0.1 m/s 조건의 PETG 소재 간의 마찰계수 변화에서도 마모 시험 초기에 짧게 나타나는 것으로 보아 PETG의 마모 특성에 따른 것으로 보인다. 0.3 m/s의 조건에서는 PLA와 PETG 동일 소재 간의 마모 시험에서 보다 높은 마찰계수를 보인다. 0.3 m/s 조건에서 PLA 블록의 온도는 유리전이온도보다 높은 반면, PETG 돌기는 유리전이온도 이하의 온도(Fig. 5)를 보이고 있기 때문에 0.3 m/s 조건에서의 높은 마찰계수는 블록 소재인 PLA가 일종의 고무 상태(Rubbery State)가 되기 때문으로 판단된다.
3.3 마모특성
Fig. 12는 마모시험에 따른 소재의 마모율을 보여주고 있다. 동일 소재들 간의 마모시험에서 PLA 소재의 경우 0.3 m/s의 조건에서 PLA 블록 표면에 용착부가 형성되어 PLA 돌기의 불균일 마모(Fig. 8)가 발생해 마모율 측정이 불가능하였다. PLA 블록 표면의 용착부 평균 높이는 1.05 mm로 단위 거리당 용착 높이는 17.50 μm/m였다(Fig. 12(b)에서 음의 값으로 표시). Fig. 13는 용착부의 형상을 보여주고 있다. 0.1, 0.2 m/s 조건에서의 PLA 돌기와 블록의 마모율은 각각 9.67, 6.67 μm/m과 23.50, 9.83 μm/m였다. PETG 소재들 간의 마모시험에서는 미끄럼 속도가 증가함에 따라 마모율이 증가하는 경향을 보였으며, 0.1, 0.2, 0.3 m/s 조건에서 PETG 돌기의 마모율은 7.50, 18.66, 42.17 μm/m이고, PETG 블록의 마모율은 4.67, 6.33, 15.17 μm/m였다.
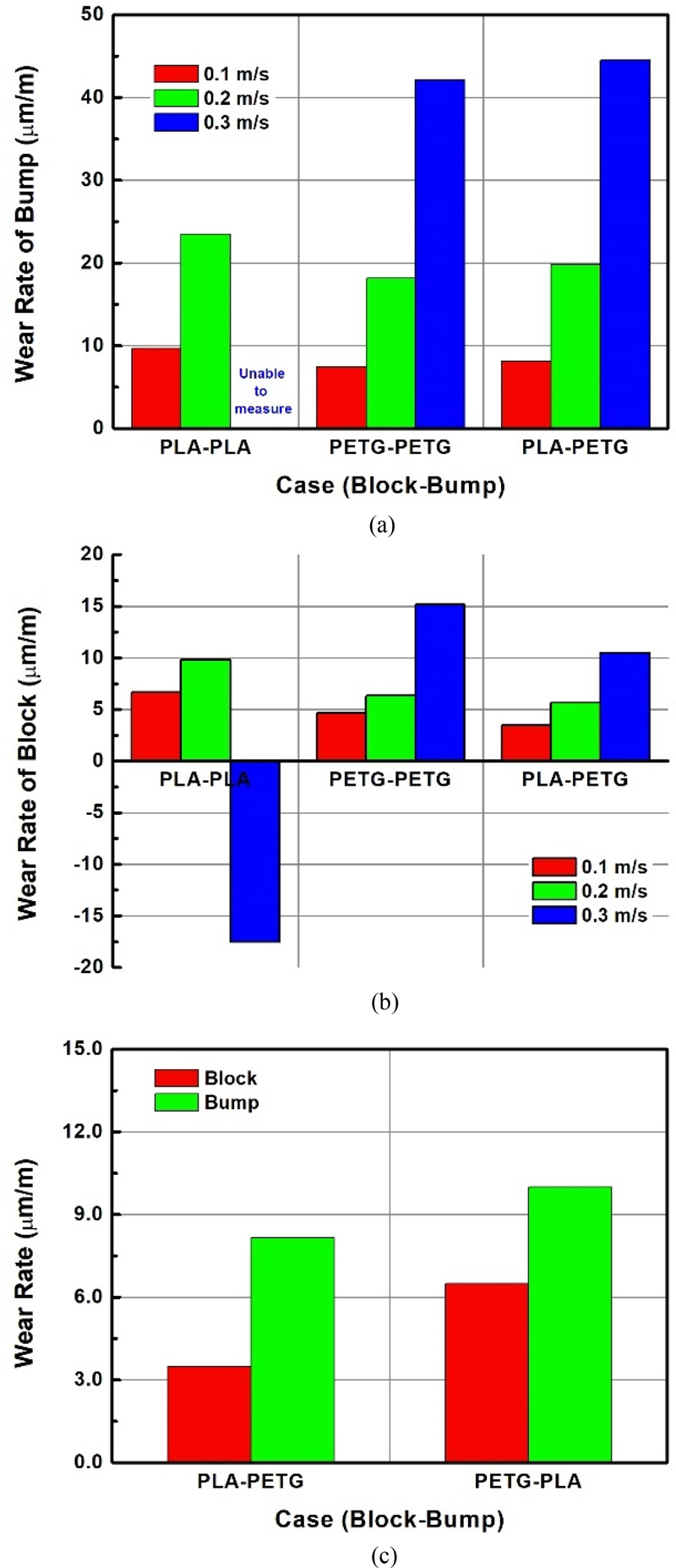
Wear rate; (a) block, (b) bump, and (c) comparison of wear rate between different 3D printed materials under 9.81 N and 0.1 m/s conditions
전반적으로 동일 소재들 간의 마모시험에서 PETG 소재가 PLA 소재보다 낮은 마모율을 보임을 알 수 있다. 이러한 특성은 3.2절의 마찰특성과 동일하며 소재의 성질에 따른 마찰계수와 관련 있는 것으로 보인다.
Fig. 12(C)는 PETG 블록-PLA 돌기와 PLA 블록-PETG 돌기의 상대운동에 따른 마모율을 보여주고 있으며, 마모시험 시 하중은 9.81 N, 미끄럼 속도는 0.1 m/s였다. PLA 블록-PETG 돌기에 비하여 PETG 블록-PLA 돌기에서 더 높은 마모율을 확인할 수 있으며 이는 Fig. 10에서와 같이 마찰특성에 따른 결과로 사료된다.
이종 소재의 마모시험 중 상대적으로 낮은 마모율을 보이는 PLA 블록-PETG 돌기의 상대운동 조건에서 미끄럼 속도에 따른 돌기와 블록의 마모율은 Figs. 12(a), 12(b)와 같이 속도에 따라 증가하는 경향을 보인다. PLA 블록-PETG 돌기의 마모시험에서의 돌기 마모율은 0.1, 0.2, 0.3 m/s의 조건에서 8.17, 19.83, 44.50 μm/m였으며, 블록의 마모율은 3.50, 5.67, 10.50 μm/m였다. 동일 소재 간의 실험과 비교했을 때, PETG 돌기 마모율은 PLA 블록-PETG 돌기의 조건에서 조금 더 크게 나타나지만, PLA 블록 마모율은 낮아지는 결과를 얻었다. 이러한 현상은 마모시험 중 마찰과 온도에 따른 소재의 상태변화에 기인한 것으로 생각된다.
4. 결론
본 연구에서는 3D 프린팅용 PLA와 PETG 소재의 마찰 및 마모 특성에 관한 연구를 수행하였다. 실험에서는 블록과 돌기 형상으로 FDM 방식으로 3D 프린팅된 소재를 사용하여 건식 마찰상태에서의 왕복동 마모시험을 통해 소재들의 트라이볼로지 특성을 확인하였다. PLA 블록-PLA 돌기, PETG 블록-PETG 돌기의 상대운동에서 PLA 블록-PLA 돌기와의 마모 시험에서 가장 높은 마찰계수와 마모율을 확인할 수 있었으며, 0.3 m/s의 미끄럼 속도 조건에서 마모 시험에 따른 온도가 유리전이온도 이상으로 상승하면서 돌기가 블록 위로 융착되는 현상이 발생하는 것으로 보인다. 반면, PETG 블록-PETG 돌기의 경우 유리전이온도 이하에서 마모되었다. PLA 블록-PETG 돌기의 이종 재료 간의 상대운동 조건의 경우, 미끄럼 속도 증가 시 PLA 블록의 마모는 PLA 블록-PLA 돌기 조건보다 크게 감소하고 소재의 융착 현상이 발생하지 않았으나, PETG 돌기의 경우 PETG 블록-PETG 돌기의 경우보다 다소 높은 마모율을 보였다. 따라서, 본 연구에서 활용한 PLA와 PETG 중 PETG로 출력된 소재가 무윤활 상태에서 상대운동 시 마찰 및 마모의 관점에서 보다 유리할 것으로 판단된다. 향후 3D 프린팅 소재를 이용한 시제품의 제작에 활용되는 다양한 소재에 관한 트라이볼로지 연구와 적합한 조합의 이종소재를 찾는 연구와 마찰 감소를 위한 윤활유에 관한 연구가 필요할 것으로 보인다.
Acknowledgments
본 연구는 한국연구재단 이공분야 기초연구사업(NRF-2021R1F1A1063060)과 부산광역시 및 (재)부산테크노파크의 BB21plus 사업으로 지원된 연구임.
REFERENCES
-
Choi, S. J., Bae, Y. H., Lee, I. H., Kim, H., (2018), Latest research trends of 3D printing in Korea, Journal of the Korean Society for Precision Engineering, 35(9), 829-834.
[https://doi.org/10.7736/KSPE.2018.35.9.829]
-
Choi, J.-W., Kim, H.-C., (2015), 3D printing technologies-A review, Journal of the Korean Society of Manufacturing Process Engineers, 14(3), 1-8.
[https://doi.org/10.14775/ksmpe.2015.14.3.001]
-
Ford, S., Minshall, T., (2019), Invited review article: Where and how 3D printing is used in teaching and education, Additive Manufacturing, 25, 131-150.
[https://doi.org/10.1016/j.addma.2018.10.028]
-
Iftekar, S. F., Aabid, A., Amir, A., Baig, M., (2023), Advancements and limitations in 3D printing materials and technologies: A critical review, Polymers, 15(11), 2519.
[https://doi.org/10.3390/polym15112519]
- Sim, J. W., Caro, C. N. D., Seo, K.-J., Kim, D.-E., (2019), A study on tribological properties of 3D-printed surface with respect to sliding orientation, Tribology and Lubricants, 35(6), 337-342.
-
Jo, Y. S., Lee, H. S., (2019), Friction and wear characteristics of ABS-like resin for 3D printing under non-lubricated condition, Journal of the Korean Society for Precision Engineering, 36(12), 1117-1124.
[https://doi.org/10.7736/KSPE.2019.36.12.1117]
- Park, S., Son, J., Woo, S., Ryu, E., Lee, H., (2020), Tribological characteristics of ABS-like resin according to silicon oil viscosity, Tribology and Lubricants, 36(6), 365-370.
-
Portoacă, A. I., Ripeanu, R. G., Diniță, A., Tănase, M., (2023), Optimization of 3D printing parameters for enhanced surface quality and wear resistance, Polymers, 15(16), 3419.
[https://doi.org/10.3390/polym15163419]
Assisted Professor in the Department of Mechanical Engineering, Dong-A University. His research interests are tribology and additive manufacturing.
E-mail: bluecys@dau.ac.kr
Associate Professor in the Department of Mechanical Engineering, Dong-A University. His research interests are CMP, abrasive machining, and tribology.
E-mail: hyunseop@dau.ac.kr