
가스 검출을 위한 공동 광자감쇠 분광시스템용 고반사 코팅 기술 동향
Copyright © The Korean Society for Precision Engineering
This is an Open-Access article distributed under the terms of the Creative Commons Attribution Non-Commercial License (http://creativecommons.org/licenses/by-nc/3.0) which permits unrestricted non-commercial use, distribution, and reproduction in any medium, provided the original work is properly cited.
Abstract
Cavity ring-down spectroscopy (CRDS) is an ultra-sensitive direct absorption technique that offers unique advantages compared to other spectroscopic techniques. It can measure cooperative enhanced absorption for weakly absorbing species at ultra-low concentrations. This is achieved by leveraging the concept of a stable optical cavity, which allows for an effective optical path length of several kilometers within a small physical sample length. One advantage of CRDS technology is that it is unaffected by fluctuations in the intensity of the light source. Another advantage is its applicability to the detection of atoms, molecules, and radicals in the atmosphere. Additionally, the equipment associated with this technology is compact and robust. This paper will first introduce the fundamental principles and setup of CRDS technology. It will then provide an overview of the characteristics of the fabrication equipment and the high reflectivity mirror coating process used in cavity ring-down spectroscopy.
Keywords:
Cavity ring-down spectroscopy, High reflective mirror, Gas detection, Evaporation, Sputter키워드:
공동 광자감쇠 분광법, 고반사 거울, 가스 검출, 증발법, 스퍼터1. 서론
기체, 액체 및 웨이퍼 등의 광특성을 연구하는데 가장 널리 사용되고 있는 투과/반사 측정 장비는 UV-VIS-NIR 분광법이다. Fig. 1(a)에서 보는 것과 같이 UV-VIS-NIR 분광법은 먼저 측정하고자 하는 파장을 포함하는 광대역 파장 광원을 샘플 없이 측정하여 기준 스펙트럼을 획득한다. 그러고 나서 광원과 검출기 사이에 측정 샘플을 두고 측정된 스펙트럼을 기준 스펙트럼 대비 분석하여 측정 파장에서의 투과/반사 특성을 얻을 수 있다. 이 측정 방법은 넓은 파장의 스펙트럼을 한 번에 볼 수 있는 장점을 가지지만, 잡음 및 민감도로 인하여 99.0% 이상의 반사율 측정이 불가능하며, 희박한 농도의 액상 샘플 또는 기체 측정에 대응할 수 없는 단점을 가지고 있다. 이를 해결하기 위한 방법 중 하나로써 제안된 공동 광자감쇠 분광시스템(Cavity Ringdown Spectroscopy, CRDS)은 1988년 O’Keefe와 Deacon이 처음으로 연구 발표하였다[1]. Fig. 1(b)에서 보는것과 같이 공동 광자감쇠 분광법은 특정 파장을 갖는 광원의 빛을 높은 반사율을 갖는 거울 사이로 왕복하게 하여 측정되는 빛의 세기 손실을 비교 후, 공동 내 흡수 물질의 농도 정보를 분석하는 방법이다. 특히, 공동 양쪽 끝단에 위치한 고반사 거울 사이를 왕복하는 빛의 광경로 길이가 길어질수록 빛과 공동 내 매질이 상호작용하는 횟수가 증가하기 때문에 공동 광자감쇠 분광시스템은 희박한 농도의 가스를 검출하는데 매우 적합하다. 공동 광자감쇠 분광시스템이 개발된 이래로 여러 가지 가스 검출에 대한 연구가 진행되었으며, 최근 NO2[2], NH3[3], CH4[4], CH2F2[5] 및 습기[6] 검출에 대한 연구 결과가 보고되었다.
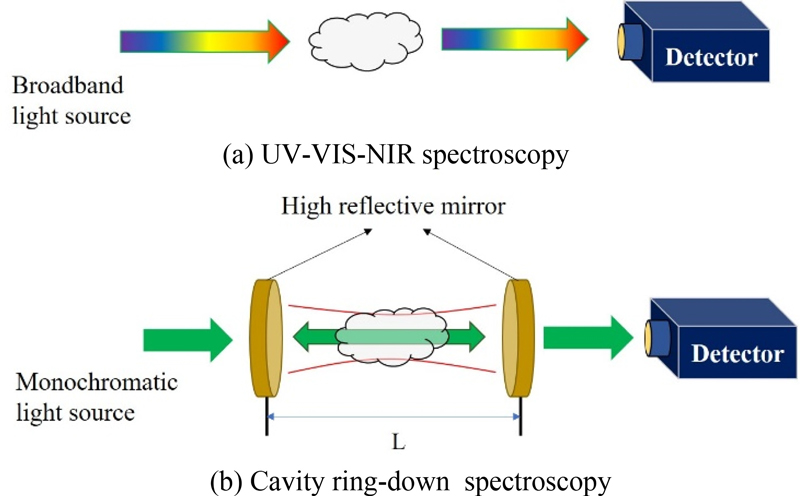
Schematics of basic principle of the (a)UV-VIS-NIR spectroscopy and (b) Cavity ring-down spectroscopy
본 논문에서는 먼저 매우 낮은 농도의 가스 검출에 사용되는 흡수율 기반 공동 광자감쇠 분광시스템의 원리와 장비에 대해서 간단히 소개한 후, 핵심 광학 부품인 고반사 거울에 대해 살펴보고자 한다. 나아가 고반사 거울 제작을 위한 코팅 장비 및 일반제작 공정에 대해서 살펴보고, 마지막으로 최근 다양한 응용처에 따른 고반사 코팅 및 특성 평가 기술 현황을 소개하고자 한다.
2. 공동 광자감쇠 분광 시스템
2.1 공동 광자감쇠 분광법 원리
공동 광자감쇠 분광법의 원리는 기 발표된 몇몇 논문[7-9]에서 상세히 나와 있기 때문에 본 논문에서는 간략하게 설명하고자 한다. 일반적으로 가스에 의해서 흡수되는 빛의 세기는 Beer-Lambert 법칙에 의하여 식(1)과 같이 표현되며 시간이 지남에 따라 빛의 세기가 감소하는 것을 볼 수 있다. 식(1)에서 σ는 측정 파장에 대한 특정 가스의 흡수율, d (mm)는 흡수가 일어나는 매질내 광 경로 길이를 의미하며, N (g/cm3)은 단위 부피당 특정 가스의 밀도를 나타낸다.
(1) |
Beer-Lambert 법칙을 Fig. 1(b)에서 보는 것과 같이 마주 보는 고반사 거울 두 개 사이를 왕복하는 빛에 적용하기 위해서는 다음 세 가지 요인을 고려하여야 한다.
- 1. 거울 사이를 한번 왕복했을 때 거울에서 반사되는 횟수
- 2. 거울 표면에서 1회 반사 시 발생하는 빛의 손실률
- 3. 거울내 빛의 총 왕복 횟수
위의 세 가지 요인을 포함하여 거울 내부에서의 흡수가 없다고 가정한다면 공동 광자감쇠 분광 시스템 내 시간에 따른 빛의 세기 변화 함수는 식(2)와 같이 표현할 수 있다. 아래 식(2)에서 R은 거울 표면의 반사율을 L (mm)은 공동의 길이를 의미하며, 정리된 된 식(4)에서 τ0는 공동내에서 빛의 세기가 감소하는데 필요한 시간을 나타낸다.
(2) |
(3) |
(4) |
공동 내 가스와 같은 매질에 의하여 빛이 흡수되어 빛 세기의 손실이 발생하는 경우 식(3)으로부터 흡수 정보를 추가하여 관계식을 도출할 수 있다. 빛이 가스가 채워져 있는 공동 내부에서 1회 왕복할 때 발생하는 손실과 공동 내 빛의 총 왕복 횟수를 고려하면 아래 식(5)와 같이 정의된다. 식(5)의 두 번째 항의 α는 가스의 고유 흡수 계수를 의미하며 공동내 가스가 균일하게 퍼져 있다고 가정한다면 매질내 빛의 흡수가 일어나는 광경로 길이 d (mm)는 공동의 길이 L (mm)과 같다.
(5) |
(6) |
(7) |
위의 식(4)와 식(7)에서 구해지는 τ0와 τ를 역수로 취한 값은 공동 내 가스 유무에 따른 빛의 세기 감쇠율을 의미하며, 이를 아래 식(8)과 같이 매질의 흡수 계수 α로 표현할 수 있다.
(8) |
특정 파장에서 공동 광자감쇠 분광법으로 획득된 흡수 계수는 공동내 가스의 농도와 흡수율 곱으로 표현할 수 있다. 특정 파장에서의 가스의 흡수율 데이터는 HITRAN[10]과 같은 표준화된 분광 데이터베이스를 구할 수 있으며, 이를 이용하여 공동 내 가스의 농도를 구할 수 있다.
3. 고반사 거울 제작 개요
3.1 고반사 거울 제작사
고반사 거울은 광학 및 레이저 응용 분야에서 사용되는 중요한 부품 중 하나이다. 고반사 거울을 제작하는 회사는 전 세계적으로 다양하며, 광학 기술 및 재료 공학에 특화된 기업들이 고반사 거울을 생산하고 있다. 세계적으로 유명한 고반사 거울제조기업은 Thorlabs, Edmund Optics, Newport Corporation 및 OptoSigma 등이 있으며, 각 제조사에서 판매 중인 일부 고반사 거울의 반사율 및 허용손상한계값 규격 비교는 Table 1과 같다. 허용손상한계값(Laser Induced Damage Threshold, LIDT)은 예상되는 손상 가능성이 0일 때 광학 부품으로 입사되는 레이저 광선의 최대량을 나타내는 값으로 반사율과 더불어 광학 거울의 사양을 나타내는 매우 중요한 특성이다. Thorlabs사는 레이저 및 광학 부품을 생산하는 회사로써, 고반사 거울을 비롯한 다양한 광학 구성품을 생산 및 판매하고 있다. Thorlabs사의 고출력 고반사 거울은 허용손상한계값을 갖는 유전체 코팅을 갖추고 있어 미세 가공 및 레이저 재료 가공 시스템에 활용되고 있다[11]. Edmund Optics 사는 광학 부품 및 시스템 제조업체 중 하나로, 다양한 종류의 고반사 거울을 생산한다. Edmund Optics사의 고반사 거울은 요건이 까다로운 Nd:YAG 레이저 용도를 충족하기 위해 비교적 높은 반사, 우수한 표면 품질도, 정밀한 표면 평탄도 규격을 보유하고 있다. 각각의 코팅은 연속파 및 펄스 레이저 시스템과의 호환성을 위해 일정 이상의 허용손상한계값을 갖도록 디자인되어 있으며, 266, 355, 532, 1,064 nm 및 멀티 라인 Nd:YAG미러 코팅을 판매 중이다[12]. Newport 사는 고성능광학 및 레이저 시스템 공급 업체 중 하나로, 고반사 거울과 관련된 제품을 제공한다. Newport 사의 레이저 라인 유전체 거울은 좁은 파장 범위에 최적화된 고효율 반사 타입이다. 제품은 모든 편광에 대해 0-45° 입사각에서 99% 이상의 반사율을 제공한다. 코팅은 내구성이 매우 뛰어나 반복적으로 청소하기가 더 쉽고 레이저 손상에 대한 저항력이 더 높다. 특히, Nd:YAG 및 엑시머 레이저 응용 분야를 위해 UV 용융 실리카 기판에 초경질유전체 코팅이 적용된 미러를 제작 및 판매하고 있다[13]. 마지막으로 OptoSigma는 광학 및 레이저 시스템의 솔루션을 제공하는 글로벌 회사로, 고반사 거울을 비롯한 다양한 광학 부품을 생산한다. OptoSigma의 고반사 미러 제품군은 코팅 후 높은 수준의 평탄도를 제공한다. 기본 1,064부터 248 nm까지 레이저용으로 특별히 설계되었으며 유전체 코팅을 기반으로 하여 최대 99.5% 반사율 규격을 만족한다[14]. 이 외에도 수많은 광학 회사들이 고반사 거울을 생산하고 있으며, 고객의 요구에 맞게 다양한 크기, 모양, 반사율 등의 제품을 제공하고 있다.

Comparison of high reflective mirror specifications at near IR wavelength range [11-14] (Adapted from Refs. 11-14 on the basis of OA)
잘 알려진 바와 같이 박막 광학은 1950년 Abeles가 처음으로 특성 행렬을 이용하여 박막 설계의 기본 이론을 확립한 후 여러가지 광학 특성을 구현할 수 있는 연구들이 활발하게 진행되고 있다. 일반적으로 광학 코팅은 고반사 코팅(High Reflectance Coating), 무반사 코팅(Anti-reflection Coating) 및 선택적 투과 또는 반사를 위한 필터 코팅(Band-pass Filter Coating) 등으로 분류된다[15]. Fig. 2에서 보는 것과 같이 고반사 코팅은 거울 표면에 증착되는 물질의 종류에 따라 크게 금속 코팅과 유전체 코팅으로 분류된다. 금속 코팅은 금속 고유의 특성으로 인하여 넓은 반사 파장을 가지고 있지만, 외력에 의해 표면이 쉽게 손상되며 공기 중 장시간 노출되면 산화막에 의해 반사율이 점차 감소하는 단점이 있다. 이러한 단점을 보완하기 위해 Fig. 2(a)에서 보는 것과 같이 금속 코팅층 위에 보호막 층을 올리거나 Fig. 2(b)의 예와 같이 유전체 코팅층을 추가하는 방법이 활용되고 있다. 이와 달리 Fig. 2(c)와 같이 유전체 코팅은 고굴절 물질과 저굴절 물질을 번갈아 증착했을 때, 각 층에서 반사되는 빛이 서로 보강간섭을 일으켜 반사율을 높이는 코팅 방법이다. 사용되는 유전체 물질의 굴절률 차이에 의해 반사 파장 범위가 결정되므로 금속 코팅에 비해 반사할 수 있는 파장 범위가 좁은 특징을 가지고 있다. 반사 효율 측면에서도 금속층을 포함한 Fig. 2(b)의 강화된 금속 코팅은 약 95-98% 범위의 반사율을 보이는 반면에 Fig. 2(c)의 유전체 코팅은 99.5% 수준의 반사율을 나타낸다. 특히, 유전체 물질의 특성으로 인하여 높은 허용손상 한계값을 보유하고 있기 때문에 고출력 레이저용으로 폭넓게 활용되고 있으며, 사용되는 유전체 물질의 두께나 층수 등을 조절하여 반사율을 최대로 증가시킬 수 있다[15,16].
4. 고반사 거울 코팅 장비 및 공정
4.1 고반사 거울 제작 장비 특징
박막제조를 위한 진공 증착은 크게 물리기상증착(Physical Vapor Deposition, PVD)과 화학기상증착(Chemical Vapor Deposition, CVD)으로 구분된다. 광학 거울 및 광학렌즈를 포함하는 광학부품의 코팅은 코팅 막질 향상을 위해 대부분 물리기상증착 방법을 사용하고 있다. 물리기상증착법은 크게 증발법(Evaporation), 스퍼터링(Sputtering) 및 이온플레이팅(Ion Plating)으로 분류되며, 고반사 거울 코팅은 Fig. 3에서 보는 것과 같이 증발법과 스퍼터링 방법이 주로 사용된다. Fig. 3(a)에서 보는 것과 같이 증발법은 코팅 대상물에 올라가는 코팅 물질을 기화하여 기판에 코팅 물질을 증착시키는 방법이며, 소스의 종류에 따라 저항가열증발법, 유도가열 증발법 및 전자빔 증발법으로 구분된다. 저항가열 증발법은 저항에 의해 발생하는 열로 코팅 물질을 기화하는 전통적인 방법으로 광학 부품의 제조, 포장지의 반사막 및 다양한 차단막 코팅 등에 이용된다. 최근에는 모바일 부품과 같은 소형 부품의 금속 증착이나 장식성 외관 코팅에도 널리 이용되고 있다. 유도가열 증발법은 고주파 전원을 이용하여 코팅 물질을 용융 및 증발시키는 것으로 대용량 증발을 통해 대형 패널이나 자동차 전장부품을 코팅하는 데 장점을 가지고 있다. 마지막으로 전자빔 증발법은 전자빔을 이용하여 코팅 물질을 기화하는 방법을 채용하는데, 다른 증발법과 달리 산화물도 증발시킬 수 있어서 광학 부품이나 디스플레이용 소형 윈도우 무반사 코팅에 주로 이용되고 있다.
스퍼터링 공정은 1939년에 발견된 글로우(Glow) 방전에 기초를 두고 있으며 초기에 이극 또는 삼극 스퍼터링이 사용되다가 1970년대에 마그네트론 스퍼터링이 등장하면서 스퍼터링 기술의 표준으로 자리 잡고 있다. 스퍼터링 방법이 증발법과 가장 큰 차별성을 갖는 부분은 코팅 물질이 기판에 증착될 때 운동에너지를 가지고 있는지 여부이다. Fig. 3(b)는 가장 일반적인 마그네트론 스퍼터링 장비의 모식도이다. 기본적으로 직류 전원의 전압차에 의해 이온화된 아르곤 이온이 가속하여 코팅 물질이 장착되어 있는 타깃1과 타깃2에 충돌하면 코팅 물질 원자가 타깃에서 운동에너지를 가진 채 기판에 박막을 형성하게 된다. 코팅 물질 원자에 운동에너지가 부여되는 과정을 스퍼터링(Sputtering) 이라고 하며 코팅 물질의 원자를 스퍼터링하는 여러 가지 방법 등이 제안되고 있다. 이를 통해 균일하고 치밀한 코팅막을 제작하는 기술들이 보고되고 있다[17,18]. 스퍼터링은 증발법에 비해 운동에너지를 갖는 코팅 물질로 증착이 되기 때문에 코팅 표면의 입자가 매우 조밀하게 구성되며, 외부의 열적, 물리적 변화에 매우 강한 저항성을 갖게 된다. 그래서, 스퍼터링으로 제작된 코팅층은 고출력 에너지를 보유한 레이저 시스템이나 선박 또는 항공기 등 가혹한 외부 환경에 노출되는 영역의 광학계 표면에 자주 활용된다. 마그네트론 스퍼터링 외 광학 부품 등을 제작하는 여러가지 스퍼터링 방식이 있으나, 본 논문에서는 국내에 아직 잘 알려지지 않은 라디칼 보조 스퍼터링(Radical Assisted Sputtering, RAS)에 대해서 4.2.2절을 통해 소개하고자 한다.
4.2 고반사 거울 코팅 공정
증발법은 물리기상증착법 중에서 간단한 형태의 진공 증착방법이며, 진공 중에 가열되어 기화된 코팅 물질을 Fig. 3(a)에서 보는 것과 같이 돔 상부의 기판에 부착시키는 방법이다. 이때, 코팅 물질을 샘플에 증착할 때 이온빔 보조 유무에 따른 일반적인 증발법과 이온빔 보조 증발법(Ion Assisted Deposition, IAD)으로 구분된다. 일반적인 증발법은 증착 입자의 낮은 운동성 때문에 국부적인 기둥구조를 가지며 밀도가 낮아 기둥 사이 미세 공간의 수분 흡수가 쉽게 발생하면서 광학적 및 기계적 성질이 불안정해지는 단점이 있다. 반면 이온빔으로 보조하는 증착은 필름이 성장하는 과정에 에너지를 가진 이온 빔을 조사하여 높은 증착 밀도로 기둥 구조를 채워 줌으로써 조밀도를 증가시킨다.
코팅 물질을 기화하는 방법은 앞서 설명한 것 같이 저항가열, 유도가열 및 전자빔이 있다. 저항가열과 유도가열 증발법은 일반적으로 녹는점이 낮은 재료(예: 알루미늄(Al), 구리(Cu), 니켈(Ni), 티타늄(Ti), 은(Ag), 금(Au) 등)의 증착에 유리하며, 전자빔 증발법은 증착 물질의 녹는점이 높은 경우(예: 텅스텐(W), 니오븀(Nb), 실리콘(Si))에 주로 사용된다. 특히, 전자빔 증발법은 둘 이상의 원소가 포함된 합금이나 화합물의 증착이 가능한 장점을 가지고 있어서 최근에는 대부분 전자빔 증발법을 사용하고 있다.
전자빔 증발법을 이용하면 Fig. 2에서 소개하고 있는 세 가지 고반사 코팅 공정이 가능하다. 먼저, 보호형 금속 고반사 코팅(Protected Metal Mirror Coating)과 반사 강화형 고반사 코팅(Enhanced Metal Mirror Coating)은 크게 두 단계의 공정으로 제작된다. 공통적으로 거울 내 반사면은 알루미늄, 은 및 금 등의 물질로 코팅되며, 그 위에 금속 거울의 내구성 및 산화 방지를 목적으로 산화 실리콘(SiO2) 등의 물질이 올라가거나, 반사 강화를 위해 유전체 물질층(고굴절 물질/저굴절 물질 층)이 코팅된다. 이와 달리 유전체 고반사 코팅(Dielectric Mirror Coating)에서는 프레넬 반사가 일어나는 동안 보강 간섭을 기반으로 빛이 반사되며, 특정 파장 범위에서 반사율을 극대화하기 위해 특별히 선정된 두께에 따른 고굴절률(산화니오븀(Nb2O5), 산화지르코늄(ZrO2), 산화탄탈륨(Ta2O5), 산화하프늄(HfO2)등) 과 저굴절률(산화 실리콘(SiO2)) 소재가 번갈아 증착된다[19,20].
앞서 설명한 증발법이나 마그네트론 스퍼터링 방법은 코팅 하고자 하는 물질을 타깃으로 만들 수 있어야만 코팅 공정이 가능한 단점을 가지고 있다. 다시 말하자면 산화 실리콘을 증착하기 위해서는 산화 실리콘 타깃 물질을 보유하고 있어야 하며, 산화물 특성상 코팅 과정에서 산화물 박막의 균질도 확보는 불가능하다. 그래서, 산화물 또는 화합물을 코팅하기 위해 반응성 스퍼터링이 제안되었으며, 이는 스퍼링된 코팅 소재가 증착 직전에 반응성 기체(예: 산소(O2), 질소(N2) 등)와 반응하여 코팅되는 공정을 포함하고 있다. 라디칼 보조 스퍼터링은 반응성 스퍼터링의 일종으로 글로우 방전을 일으키기 위한 매질로 아르곤(Ar)과 같은 비활성 기체를 활용한다. Fig. 4에서 보는 것과 같이 금속 코팅 소재 원자가 아르곤 이온에 의해서 스퍼터링 되고 반응성 기체인 산소 또는 질소와 만나 산화물 또는 질화물 형태로 드럼 위 기판에 코팅된다. 일반적으로 금속 타깃을 장착할 수 있는 챔버 내 공간은 두 개로 고굴절률(산화니오븀, 산화지르코늄, 산화탄탈륨, 산화하프늄 등) 과 저굴절률(산화 실리콘) 소재를 각각 활용하기 때문에 증발법에 비해 매우 다양한 코팅 소재를 증착할 수 있는 장점이 있다. 라디칼 보조 스퍼터링은 Fig. 4의 하단에서 보는 것과 같이 유도 결합플라즈마(Inductively Coupled Plasma, ICP) 파트를 보유하고 있으며, 이를 이용하면 반응 기체가 스퍼터링 된 코팅 소재와 라디칼(Radical)을 형성하여 일부 반응 기체가 코팅소재 타깃 표면을 오염하는 것을 방지한다. 특히, 라디칼 결합된 코팅 소재와 반응 기체 원소는 일반 스퍼터링된 코팅 소재 원자에 비해 매우 높은 안정성을 가지기 때문에 고품질의 코팅막을 제작할 수 있다.
앞서 설명한 전자빔 증발법과 마찬가지로 스퍼터링 방법을 이용하여 세 가지 고반사 코팅 공정이 모두 가능하며 이미 여러 연구 그룹에서 활용하고 있다[21,22]. 전자빔 증발법에 비해 라디칼 보조 스퍼터링은 보호막 코팅과 유전체 코팅에 적용할 수 있는 물질, 예를 들어 실리콘나이트라이드(Si3N4)등의 질화물계와 같은 물질도 적용 가능하기 때문에 더 넓은 파장 범위에 특화된 고반사 코팅도 수행할 수 있다. 다만, 스퍼터링 방법의 특성상 코팅 물질이 운동 에너지를 가지고 기판에 증착되기 때문에 코팅 후 내부 응력이 강하게 발생하기도 한다.
5. 고반사 거울 코팅 및 특성평가 기술 전망
공동 광자감쇠 분광 시스템용 고반사 거울은 상용 제품이 대부분 사용되고 있지만, 최근 초민감 가스 검출을 위해 고출력 레이저가 광원으로 사용되면서[23] 허용손상한계값이 높은 고반사 거울의 시스템 적용 검토가 이루어지고 있다. 또한, 최근 고출력 레이저를 기반으로 하는 시스템; 예를 들어 우주물체/인공위성 추적 시스템, 미사일/드론 요격 시스템 등에 고출력 레이저가 필수적으로 적용되고 있다. 고출력 레이저 기반 시스템에서는 무엇보다도 에너지 손실이 거의 없는 전용 고반사 거울이 필요하며, 해외 및 국내 방산업체에서 일부 제작하고 있으나 매우 제한적이다. 고출력 레이저 전용 고반사 거울을 시스템에 적용하기 위해서는 고반사율과 허용손상한계값 특성을 동시에 만족해야 한다. 반사거울의 고반사율 측정은 앞서 언급한 공동 광자감쇠 분광법으로 가능하며, 현재 전 세계적으로 유일하게 독일의 UFI(UltraFast Innovations)사에서 상용 장비를 판매하고 있으나 측정 표준에 대한 부분이 아직 아쉬운 실정이다. 이와 달리 허용손상한계값은 국제규격(International Standard, ISO) ISO 21254-1, 21254-2를 통해 측정 규격이 규정되어 있으며, 미국 SPIE (Laser Damage) 학회에서 관련 연구 결과들이 다수 발표되고 있다. 특히, 2020년부터는 Thin Film Damage Competition을 통해 세계 여러 연구 그룹 및 회사에서 제작된 고반사 거울의 파장 및 레이저별 최대 허용손상한계값에 대한 정보가 일부 제공되고 있다[24].
6. 결론
본 논문에서는 가스 검출을 위한 공동 광자감쇠 분광법과 공동 광자감쇠 분광시스템용 고반사 코팅 기술에 대해 소개하였다. 공동 광자감쇠 분광법은 UV-VIS-NIR 분광법에 비해 정밀 측정이 가능하기 때문에 희박한 농도의 가스 검출에 매우 적합한 방법이다. 공동 광자감쇠 분광법은 최근 몇 년 동안 눈에 띄게 발전하였으며, 주변 환경에서 미량 가스종을 현장 모니터링하는 가장 인기있는 기술로 부상하였다. 또한 분자 분광학, 대기 감지, 호기 진단, 플라즈마 진단 및 흡수 모니터링 등 다양한 연구 분야를 포괄하는 광범위한 응용 분야에 적용되고 있다. 나아가 다양한 응용 분야에 적용하기 위한 테라헤르츠 및 자외선 영역의 고반사 코팅 기술이 개발된다면 다양한 파생 산업 등이 창출될 것으로 기대된다.
Acknowledgments
이 논문은 2024년도 정부(방위사업청)의 재원으로 국방기술진흥연구소의 지원과(No. KRIT-CT-21-024, 고에너지 레이저용 변형거울 설계 및 파면보상 기술) 과학기술정보통신부 선도연구시설 고도화 지원사업(PG2024023-01-05)의 지원을 받아 진행되었습니다.
References
-
O’Keefe, A., Deacon, D. A. G., (1988), Cavity ring-down optical spectrometer for absorption measurements using pulsed laser source, Review of Scientific Instrument, 59(12), 2544-2551.
[https://doi.org/10.1063/1.1139895]
-
Rao, G. N., Karpf, A., (2010), High sensitivity detection of NO2 employing cavity ringdown spectroscopy and an external cavity continuously tunable quantum cascade laser, Applied Optics, 49(26), 4906-4914.
[https://doi.org/10.1364/AO.49.004906]
-
Gadedjisso-Tossou, K. S., Stoychev, L. I., Mohou, M. A., Cabrera, H., Niemela, J., Danailov, M. B. Vacchi, A., (2020), Cavity ring-down spectroscopy for molecular trace gas detection using a pulsed DFB QCL emitting at 6.8 μm, Photonics, 7(3), 74.
[https://doi.org/10.3390/photonics7030074]
-
Ma, G., He, Y., Chen, B., Deng, H., Liu, Y., Wang, X., Zhao, Z., Kan, R., (2021), Quasi-simultaneous sensitivity detection of two gas species by cavity-ringdown spectroscopy with two lasers, Sensors, 21(22), 7622.
[https://doi.org/10.3390/s21227622]
-
Yumoto, M., Kawata, Y., Wada, S., (2022), Mid-infrared-scanning cavity ring-down CH2F2 detection using electronically tuned Cr:ZnSe laser, Scientific Reports, 12(1), 7879.
[https://doi.org/10.1038/s41598-022-12019-5]
-
Abe, H., (2023), Trace-moisture measurement using cavity ringdown spectroscopy at NMIJ, Journal of Physics: Conference Series, 2439, 012001.
[https://doi.org/10.1088/1742-6596/2439/1/012001]
-
Busch, K. W., Busch, M. A., (1999), Cavity-Ring-down Spectroscopy, American Chemical Society.
[https://doi.org/10.1021/bk-1999-0720]
-
Lehmann, K. K. Berden, G., Engeln, R., (2010), An introduction to cavity ring-down spectroscopy, in: Cavity Ring-down Spectroscopy: Techniques and Applications, Berden, G., Engeln, R., (Eds.), Blackwell Publishing Ltd.
[https://doi.org/10.1002/9781444308259.ch1]
-
Maity, A., Maithani, S., Pradhan, M., (2021), Cavity ring-down spectroscopy: recent technological advancements, techniques and applications, Analytical Chemistry, 93(1), 388-416.
[https://doi.org/10.1021/acs.analchem.0c04329]
- HITRAN, The HITRAN Database, https://www.hitran.org, /
- Thorlabs, High power mirrors for picosecond Ytterbium lasers. https://www.thorlabs.com/newgrouppage9.cfm?objectgroup_id=12944
- Edmund Optics, Nd:YAG laser line Mirrors. https://www.edmundoptics.co.kr/f/ndyag-laser-line-mirrors/39566, /
- Newport, Laser line mirrors. https://www.newport.com/c/laser-line-mirrors
- OptoSigma, High surface flatness mirrors. https://www.optosigma.com/us_en/optics/mirrors/high-surface-flatness-mirrors.html
- Hwangbo, C. K., (2016), Thin film optics, Tech Media.
-
Macleod, H. A., (2001), Thin-film optical filters third edition, CRC Press.
[https://doi.org/10.1201/9781420033236]
- Jun, J. H., Jeong, J. I., (1999), Plasma assisted PVD and CVD, Journal of Welding and Joining, 17(1), 28-36.
-
Jeong, J.-I., Yang. J.-H., (2011), Trend and prospect of thin film processing technology, Journal of the Korean Magnetics Society, 21(5), 185-192.
[https://doi.org/10.4283/JKMS.2011.21.5.185]
-
Maiti, N., Karmakar, P., Barve, U., Bapat, A., (2008), An evaporation system for film deposition using electron beam sources, Journal of Physics Conference Series, 114(1), 012049.
[https://doi.org/10.1088/1742-6596/114/1/012049]
-
Feinstein, L. G., Bill, M. J., (1975), Reduction of nodules in electron-gun- evaporated Au films, Journal of Vacuum Science and Technology, 12(3), 704-708.
[https://doi.org/10.1116/1.568650]
-
Febvrier, A. l., Landalv, L., Liersch, T., Sandmark, D., Sandstrom, P., Eklund, P., (2021), An upgraded ultra-high vacuum magnetron-sputtering system for high-versatility and software-controlled deposition, Vacuum, 187, 110137.
[https://doi.org/10.1016/j.vacuum.2021.110137]
-
Musil, J., Baroch, P., Vlček, J., Nam, K. H., Han, J. G., (2005), Reactive magnetron sputtering of thin films: present status and trends, Thin Solid Films, 475(1), 208-218.
[https://doi.org/10.1016/j.tsf.2004.07.041]
-
Karpf, A., Qiao, Y., Rao, G. N., (2016), Ultrasensitive, real-time trace gas detection using a high-power, multimode diode laser and cavity ringdown spectroscopy, Applied Optics, 55(16), 4497-4504.
[https://doi.org/10.1364/AO.55.004497]
- SPIE Laser-damage, Technical Conference at SPIE Laser Damage. https://spie.org/conferences-and-exhibitions/laser-damage/program/conference
received his Ph.D. degree in the department of electrical engineering from Chonnam National University in 2018. Now, he is working as a senior researcher at Korea Photonics Technology Institute (KOPTI). His research interest is optical coating and nano photonics materials for intelligent optical module.
E-mail: hyjung@kopti.re.kr
received his Ph.D. degree in the department of Physics from Chung-Ang University in 2011. Now, he is working as a team leader at Korea Photonics Technology Institute (KOPTI). His research interest is optical coating and precision lens molding process for intelligent optical module.
E-mail: jpark@kopti.re.kr