
주축 모터의 전기적 특성을 고려한 절삭력 모니터링
Copyright © The Korean Society for Precision Engineering
This is an Open-Access article distributed under the terms of the Creative Commons Attribution Non-Commercial License (http://creativecommons.org/licenses/by-nc/3.0) which permits unrestricted non-commercial use, distribution, and reproduction in any medium, provided the original work is properly cited.
This paper was presented at KSPE Spring Conference in 2024
Abstract
The importance of cutting forces in machining has been emphasized for monitoring and optimizing cutting conditions, leading to various method to detecting cutting forces researched. Cutting forces can be directly measured using dynamometer or indirectly estimated using AE sensors and accelerometers, etc. However, these external sensors demand high costs and have accuracy limitations due to environment issues. To compensate for these drawbacks, utilizing internal signals of machine tool has been developed. Among these, using internal electrical signals of machine tool is representative. In commercial machine tools, cutting forces are often estimated through current measurements. However, due to the characteristics of the spindle motor, electrical properties such as slip, power factor, and efficiency vary with the load, resulting in relatively lower accuracy. This study introduces current-based method considering characteristics of motor and power-based method for estimating cutting forces and compare accuracy of those methods with the measurements from dynamometer respectively.
Keywords:
Cutting force monitoring, Machine tool, Spindle motor current, Spindle motor power키워드:
절삭력 모니터링, 공작기계, 주축 모터 전류, 주축 모터 전력1. 서론
공작기계를 통한 절삭 공정 중 발생하는 절삭력은 공정 상태에 대한 다양한 정보를 담고 있어 절삭 과정 중 발생하는 다양한 현상들을 알기 위해서는 절삭력을 감지하는 것이 중요하다. 절삭력을 활용하여 공구 마모, 재료의 표면조도 추정 등 절삭 공정 중 발생하는 물리현상들의 측정과 공구 파손 및 채터와 같은 이상상황발생 감지도 가능하며, 이송 속도 및 절삭 속도의 최적 조건을 선정하는데 활용할 수도 있다. 이처럼 절삭력은 가공공정과정 중의 전반적인 가공 상태 및 현상들을 나타내는 중요한 지표로 활용되고 있으며, 절삭력 감지를 위한 다양한 방법들이 연구되어 왔다.
절삭력을 감지하는 방법에는 대표적으로 공구동력계를 가공기에 설치하여 가공 중에 발생하는 힘을 직접 측정하는 방식이 있다. 공구동력계를 이용한 직접 측정 방식은 높은 정확도와 신뢰성이 보장된다. 그러나 일반적인 공구동력계의 경우 X, Y, Z방향으로 발생하는 절삭력은 측정 가능하지만, 절삭에 가장 영향을 많이 미치는 접선 방향의 성분은 측정할 수 없다는 한계가 있다. 이러한 단점을 보완하기 위하여 Kistler 사에서는 스핀들에 공구동력계를 부착하여 절삭력을 측정하는 방식으로 접선 방향의 절삭력을 감지하며, Altintas 등은 스핀들 내부에 힘센서를 설치하여 접선 방향의 절삭력을 감지하였다[1,2]. 이러한 직접 측정 방법 외에도 간접적으로 절삭력을 추정할 수 있는데, AE (Acoustic Emission) 센서를 통해 측정한 음향 방출 신호를 이용하거나, 가속도 센서를 스핀들에 부착하여 절삭력을 추정할 수 있다. 음향 방출 신호의 경우, 넓은 대역폭의 측정이 가능하며 금속 가공 과정에서 발생하는 대부분의 현상 감지가 가능하다는 특징이 있다[3,4]. Hase 등은 선삭 가공 중에 발생하는 음향 방출 신호를 측정하여 절삭 시 발생하는 현상과 음향 방출 신호와의 관계를 연구했으며, 음향 방출신호를 통해 칩 형성 역학과 공구 마모 및 파손을 감지할 수 있음을 보였다[5]. Postel 등은 밀링 스핀들 하우징에 가속도 센서를 부착하여 가속도 센서 및 모달 테스트를 통해 절삭력을 구할 수 있음을 보였다[6]. 하지만 음향 방출 신호만을 사용하여 절삭력을 추정하는 방식은 외부 환경의 영향을 많이 받아 신호에 노이즈가 첨가될 가능성이 높으며, 가속도 센서의 경우 넓은 대역폭의 측정이 가능하지만, 민감도가 떨어져 고주파 영역에서는 데이터 손실이 발생할 문제가 있다[7].
이러한 외부 센서를 사용한 절삭력 감지 방법의 경우, 장비 내구축 비용이 높으며 가공 중 발생하는 칩과 절삭유의 사용으로 인해 정확한 측정이 어려워 실제 산업 현장에 적용하기에는 한계가 있다. 이와 같은 단점을 보완하기 위해 외부 센서를 사용하지 않고 장비 내부 센서와 내부 신호를 이용해 절삭력을 추정하는 연구들이 수행되어 왔다. 장비 내부 신호를 사용하여 절삭력을 추정하는 가장 대표적인 방법은 전기적 신호를 활용하여 절삭력을 추정하는 방법이다. 가공 중 발생하는 전류 신호를 사용하여 절삭 부하를 추정할 수 있는데, 대표적으로 DMG MORI사의 상용 공작기계에서도 전류를 이용한 절삭력 추정 방식을 통해 실시간으로 절삭 부하를 표시해 준다[8]. Jeong 등은 이송계 PMSM모터의 특성과 Feed Drive System의 구조를 이용하여 전류 d-q변환을 통해 이송계 X, Y, Z축에 걸리는 각 절삭력을 추정하였다[9]. 이송계 모터의 전기적 신호를 이용해 X, Y, Z방향의 절삭력 추정 방법 외에 주축 모터의 전기적 신호를 이용해 접선 방향 성분의 절삭력을 추정하는 방법도 연구되었는데, Li는 터닝센터에서 절삭 과정 중에 주축 모터에서 발생한 전류와 이송속도, 주축 각가속도를 ANFIS (Adaptive Neuro-Fuzzy Inference System)를 통해 접선 방향 및 반경 방향 절삭력을 도출하였다[10]. Aggarwal 등은 밀링에서의 주축 스핀들 모터 특성에 기반해 전기적 손실 및 기계적 손실을 고려하여 전류 기반 절삭력에서 접선 방향 절삭력 계수 도출 방법을 제안하며, 전류에 선형회귀를 통해 절삭력과 절삭 계수를 도출하였다[11]. 하지만 AC 모터의 경우, 전류를 이용하여 절삭 토크 및 절삭력을 추정하기에는 AC 모터의 전기적 특성상 한계가 존재하는데, DC 모터와는 달리 슬립이 존재한다는 특성이 있으며, 전류는 절삭 상태의 작은 변화에 둔감한 특성 때문에 전류만을 이용하여 절삭력을 추정하기는 어려움이 있다[12]. Mannan 등은 실험을 통해 절삭 중 스핀들 모터에서 출력되는 전력과 절삭 토크는 높은 상관관계를 가지고 있음을 보였다[13]. Stein은 AC 인덕션 모터의 성질을 이용하여 전력을 통해 절삭력을 추정하는 방법을 제시하였으며, HEIDENHAIN 사의 상용 공작기계에서는 스핀들 전력을 이용하여 부하를 모니터링한다[14,15].
본 연구에서는 전기적 신호를 이용하여 3가지의 절삭력 추정 방법을 비교하였으며, 각각 기존의 전류만을 이용한 절삭력 추정 방법과 주축 모터의 전기적 특성을 고려한 전류 기반 절삭력 추정 방법, 그리고 주축 전력 기반 절삭력 추정 방법을 공구동력계 측정 결과와 비교하여 각 방법의 정확도를 비교하였다. 3축 수직형 머시닝센터에서 가공 중에 출력되는 전기적 신호를 전류, 전압 측정 모듈을 이용해 수집하였으며, 엔드밀에 비해 비교적 넓은 부하범위의 가공이 가능한 페이스 커터를 사용하여 동일 RPM에서 가공 실험을 수행하였다. 각각의 절삭력 추정 방법 중 기존 전류 기반 절삭력 추정 방법의 경우, 공구동력계로 측정한 절삭력을 통해 주축 모터의 토크 상수를 도출하여 절삭력을 추정하였다. 하지만 실제 부하가 변화하는 가공 상황에서 전류와 토크의 관계가 선형적이지 않아 정확도가 떨어지는 문제가 있다. 이러한 문제를 해결하기 위해 주축 모터로 사용하고 있는 3상 인덕션 모터에서 부하가 변함에 따라 역률, 슬립, 효율 등의 주축 모터의 전기적 특성이 변화하는 성질을 반영하여 주축 모터의 특성을 고려한 전류 기반 절삭력 추정 방법을 제안하였다. 제안한 방법은 주축 모터의 전기적 특성을 반영해 슬립과 토크 관계를 통해 절삭력을 추정하는 방법으로 기존의 토크 상수를 도출하여 절삭력을 추정하는 전류 기반 추정 방법에 비해 향상된 정확도를 기대할 수 있다. 주축 전력 기반 절삭력 추정 방법에서는 Blondel’s Theorem의 2전력계 측정 방식을 이용해 전력을 도출하고, 주축 RPM과 공구 직경을 이용해 절삭력을 추정하였다[16].
2. 주축 모터의 전기적 특성
2.1 테스트베드 구성
주축 전류 및 전력 모니터링을 위하여 상용 3축 수직형 머시닝센터(DNM4500, DN Solutions)에 테스트베드를 구축하였다. 테스트베드 구성을 Figs. 1(a)에 표현하였고, 그의 도식을 1(b)에 표현하였다. 주축에서 출력된 3상(U상, V상, W상)의 전류 및 전압 측정을 수행하였다. 전류는 24 bit의 분해능을 가진 전류 수집 모듈(NI-9247, National Instrument)을 사용하였으며, 주축에서 출력되는 3상 중 2상(U상, V상)의 전류를 수집하였다. 전압은 24 bit의 분해능을 가진 전압 수집 모듈(NI-9225, National Instrument)을 사용하였으며, U상과 V상 각각의 W상과의 전위차를 수집하였다. 전류 기반 절삭력 추정 결과 및 전력 기반 절삭력 추정 결과 각각을 실제 절삭력 값과 비교하기 위하여 공구 동력계(9257A, Kistler)를 설치하였고, 16 bit 분해능을 가진 전압 입력 모듈(NI-9215, National Instrument)을 사용하여 X, Y, Z 방향의 절삭력 값을 측정하였다. 전류, 전압, 절삭력 측정을 위한 측정 모듈들은 모두 NI-DAQ Chassis를 사용하여 동일한 샘플링 타임으로 데이터를 취득하도록 구성하였다.
2.2 인덕션 모터의 전기적 특성
상용 공작기계에서는 주축 스핀들 모터로 인덕션 모터를 주로 사용하는데, 인덕션 모터를 이용해 가공을 진행하며 부하가 가해지면 인덕션 모터의 전기적 특성에 따라 역률, 슬립, 효율 등의 다양한 인자에 변화가 발생한다.
본 연구에 사용된 장비에 장착된 스핀들 모터는 최대 출력 18.3 kW, 최대 토크 118 Nm의 3상 인덕션 모터이다. 교류에서는 직류와는 달리 전류와 전압 간의 위상차에 의해 역률(Power Factor, PF)이 발생하게 되는데, 이는 모터가 사용하는 유효전력과 피상전력의 비율로 표현할 수 있다. 역률 도출 과정은 식(1)을 따르며, 출력 전력 Pout 을 전류의 실효값 Irms과 전압 실효값 Vrms의 곱으로 나누어 역률 PF를 표현할 수 있다.
(1) |
식(1)을 사용하여 페이스커터(6날 80 ϕ, Taegutec)를 사용해 S45C 시편을 1,500 RPM으로 가공 깊이와 이송속도를 변경해 전력 부하를 다르게 하여 가공하며 역률을 계산하였다. 계산한 역률과 전력 부하, 전류 부하를 Fig. 2에 나타내었으며, 부하가 변화함에 따라 역률이 변화하는 모습을 확인할 수 있다.
이렇게 모터에 부하가 가해지는 상황에서 부하 토크에 의해 슬립이 발생하게 된다. 인덕션 모터는 동기 속도 Ns에 못 미치는 속도로 구동하게 되는데, 이때 동기 속도와 실제 회전 속도 N의 비율을 슬립 s이라고 하며, 식(2)와 같이 표현할 수 있다.
(2) |
인덕션 모터의 2차 회로를 간단히 Fig. 3의 (a)에 나타내었다. 이 때, 2차 회로에 가해지는 전류 I는 식(3)과 같이 슬립 s, 전압 E, 저항 R, 리액턴스 X성분으로 표현할 수 있으며, 실제 회전 속도가 작아져서 슬립이 커지면 전류가 커진다.
(3) |
이를 Fig. 3(b)에 표현된 임피던스 삼각형을 이용하여 역률과 슬립의 관계를 살펴보았을 때, 역률은 저항 성분과 리액턴스가 이루는 각 θ에 의해 결정되며, 역률은 코사인함수를 이용해 표현할 수 있다. 이 때, 슬립이 증가하게 되면, 리액턴스는 일정하기 때문에 θ가 감소하며 역률이 감소하게 된다. 이렇게 역률이 낮을 경우에는 전력 손실이 생겨 에너지 측면으로 보았을 때 효율이 떨어지게 된다. 일반적으로 저역률을 보상하기 위해 커패시터 또는 인덕턴스를 추가하여 PFC (Power Factor Correction) 회로를 구성한다.
역률과 슬립 외에도 부하가 가해지는 상황에서 모터의 효율 η 또한 변화가 발생한다. 효율은 식(4)와 식(5) 같이 출력 전력에서 스핀들 모터의 각속도 ωM을 나눠서 도출하는 전기적 힘에서 기계적 힘 Tmech으로 변환되는 과정에서 발생하는 효율이며, 동손, 철손 등과 같은 전기적 손실이 포함된 값으로 볼 수 있다. 앞서 진행한 실험에서의 부하에 따른 효율을 Fig. 4에 나타내었으며, 부하에 따른 효율 변화를 확인할 수 있다.
(4) |
(5) |
3. 주축 전기신호 기반 절삭력 추정 방법
3.1 주축 전류 기반 절삭력 추정 방법
기존 주축 전류 기반 절삭력 추정 방법의 경우, 식(6)과 같이 가공 중 출력된 전류의 실효값과 토크 상수 KT의 곱으로 표현된 절삭토크에 공구 반지름 r을 나누어 절삭력 FT,I을 추정하였다.
(6) |
출력된 전류는 무부하 상태일 때의 전류를 포함하고 있으므로 절삭에 해당하는 전류를 구하기 위해 측정값에서 무부하 상태에서의 전류값을 제거하여 절삭 시의 전류를 구하였다. 실제 기존 전류 기반 추정 방법을 사용하기 위해 Table 1에 나타난 절삭 조건으로 전류 실효값과 공구동력계로 측정한 절삭력을 이용해 토크 상수를 구한 결과, Table 2와 같이 부하에 따라 토크 상수가 변함을 볼 수 있다. 또한, 도출된 토크 상수들의 평균을 대푯값으로 정하여 기존 전류 기반 방법으로 절삭력을 도출한 결과, Fig. 5와 같은 결과를 얻을 수 있었으며, 공구동력계 측정값의 경향을 추종하지만, 정확도가 떨어짐을 확인할 수 있다.
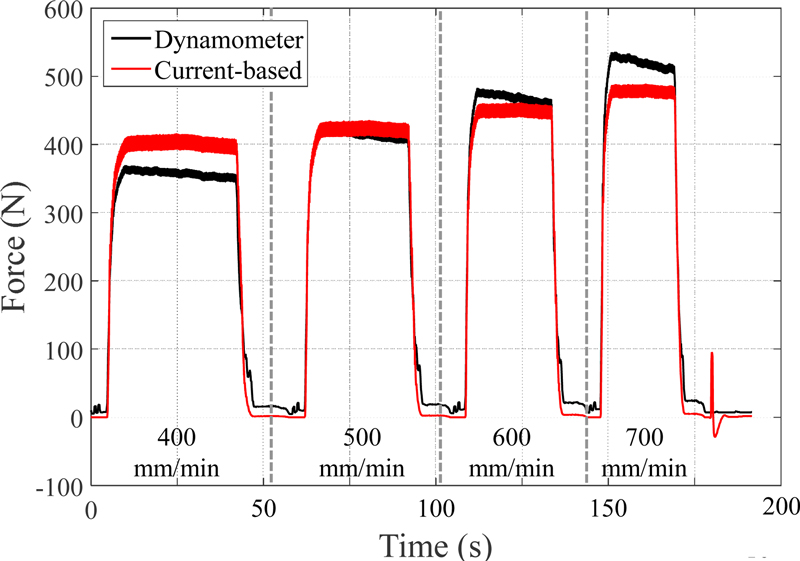
Cutting force determination in basic experiment using tool dynamometer, conventional current-based method
이러한 기존 주축 전류 기반 절삭력 추정 방법의 문제를 보완하기 위하여, 주축 모터의 전기적 특성을 고려한 주축 전류 기반 절삭력 추정 방법을 제안하였다. 3상 인덕션 모터에서의 슬립에 따른 토크 및 전류의 관계를 Fig. 6에 나타내었다.
Fig. 6에서 Torque는 모터의 구동 토크를 의미하며, Load Torque는 모터의 회전자에 가해지는 부하 토크를 나타낸다. 구동토크가 최대가 되는 점을 기준으로 구동 시작부터 최대 토크지점까지의 고 슬립 영역을 Unstable Region, 최대 토크 이후부터 슬립이 0이 되는 지점까지의 저 슬립 영역을 Stable Region으로 구분한다. Unstable Region에서는 슬립이 증가할수록 토크는 감소하는데, 이때 토크가 감소할수록 부하가 추가되고 모터속도는 감소하여 작동이 불안정한 반면, Stable Region에서는 슬립과 토크가 선형적인 관계를 가지기 때문에 안정적으로 작동할 수 있으며, 모터는 항상 Stable Region에서 작동한다. 절삭 또한 Stable Region의 구동 토크와 부하 토크가 만나는 운전점 부근에서 이뤄지는데, 이때 토크와 슬립이 비례함을 가정할 수 있다. 식(3)의 전류 식에 토크와 슬립이 서로 비례함을 나타낸 식(7)을 대입하면, 인덕션 모터에 흐르는 전류 I를 식(8)과 같이 정리할 수 있다. 정리된 식을 다시 토크 T에 대한 식으로 정리하면 저항, 리액턴스, 전압은 일정한 값을 가지기 때문에 하나의 상수로 치환하여 식(9)와 같이 정리할 수 있다.
(7) |
(8) |
(9) |
이렇게 구한 토크는 절삭토크 Tc와 구동토크 Ti의 합인데, 전체토크를 식(9)와 같이 정리하였고, 구동토크는 일정한 값을 가지기 때문에 상수로 가정하면 절삭토크는 식(10)과 같이 정리 할 수 있다. 따라서, 모터의 전기적 특성을 고려한 주축 전류 기반 절삭력 추정 방법은 식(11)과 같이 절삭토크에 공구반지름을 나누어 도출할 수 있다.
(10) |
(11) |
3.2 주축 전력 기반 절삭력 추정 방법
수집된 가공 중 전류, 전압 수집 값을 Blondel’s Theorem을 사용하여 식(12)와 식(13)의 과정으로 전력값을 도출하였다. 3상 회로에서의 전력은 식(12)과 같이 각 상의 전류와 전압의 곱을 합한 것과 같다는 점을 이용하였다. U, W상의 전위차와 V, W상의 전위차를 각각 V1, V2로 설정하였을 때, 출력 전력은 U상의 전류 IU와 V1의 곱과 V상의 전류 IV와 V2의 곱을 합한 것과 같다.
(12) |
(13) |
도출된 출력 전력은 전류와 마찬가지로 무부하 상태일 때의 전력을 포함하고 있으므로, 출력된 전력에서 무부하 상태의 전력 Pair을 제거하여 절삭 시의 전력을 통해 절삭력을 추정해야 한다. 도출된 절삭 시의 전력을 주축 스핀들 모터의 각속도와 공구반지름으로 나누어 절삭력을 추정할 수 있으며, 그 과정은 식(14)의 과정을 따른다.
(14) |
3.3 각 추정 방법의 정확도 비교
앞서 소개했던 기존 주축 전류 기반 추정 방법, 제안된 주축 전류 기반 추정 방법, 그리고 주축 전력 기반 추정 방법 등의 방법으로 도출한 절삭력을 공구동력계 측정값과 비교하여 각 방법의 정확도를 비교하였다. 정확도 비교 방법에 대한 간단한 도식을 Fig. 7에 나타내었다. 실험 조건은 Table 3과 같이 절삭 조건을 구성하였으며, 2.1과 동일한 테스트베드에서 절삭 실험을 하였다. 주축 회전 속도는 장비 기저 속도인 1,500 RPM으로 고정하여 이송속도에만 변화를 주었는데, 20부터 300 까지는 20 mm/min씩, 300부터 1,000 까지는 50 mm/min씩 이송 속도를 증가시켰다.
기존의 주축 전류 기반 절삭력 추정 방법, 모터의 전기적 특성을 고려한 주축 전류 기반 절삭력 추정 방법 등으로 추정한 절삭력을 공구동력계로 측정한 절삭력과 비교하여 Figs. 8(a)에 나타내었으며, 각 방법으로 구한 절삭력과 공구동력계 측정값과의 오차를 8(b)에 나타내었다. 인덕션 모터의 경우 저부하 구간에서는 철손이 급격히 증가하여 효율 저하가 발생하게 된다[17]. 기존 주축 전류 기반 방법으로 도출한 절삭력의 RMS 오차는 55.81 N, 모터의 전기적 특성을 고려한 주축 전류 기반 방법의 오차는 10.73 N, 그리고 주축 전력 기반 방법의 평균 오차는 13.86 N이며, 오차율은 각각 19.42, 3.73, 4.82% 로 나타났다. 각 방법의 오차율을 비교하였을 때, 모터의 전기적 특성을 고려한 주축 전류 기반 추정 방법과 주축 전력 기반 추정 방법이 비교적 높은 정확도로 절삭력을 추정할 수 있음을 보였다.
4. 결론
본 연구에서는 외부 센서를 사용하지 않고 전기적 신호를 이용해 절삭력을 감지하는 방법을 모색하고, 기존 주축 전류 기반 추정 방법에서 정확도가 떨어지는 문제를 보완하기 위해 스핀들 모터의 전기적 특성을 고려한 주축 전류 기반 절삭력 추정 방법을 제안하였다. 기존 주축 전류 기반 방법, 모터의 전기적 특성을 고려한 주축 전류 기반 방법, 그리고 주축 전력 기반 방법 등의 3가지 방법들로 추정한 절삭력을 각각 공구동력계 결과와 비교하여 각 방법들의 정확도를 비교하였다.
3축 수직형 머시닝센터에 전류 및 전압을 수집할 수 있는 모듈과 실제 절삭력을 측정할 수 있는 공구동력계를 통해 실시간으로 데이터 수집이 가능한 테스트베드를 구성하였으며, 페이스커터를 이용해 가공실험을 하며 전류, 전압, 공구동력계 측정 데이터를 수집하였다. 수집된 전류 및 전압을 통해 부하가 변함에 따라 역률, 슬립, 효율 등의 모터의 전기적 특성들이 달라짐을 확인할 수 있었다.
기존 전류 기반 방법에서는 절삭 중에도 토크와 전류가 비례 한다고 가정하여 식(8)의 과정으로 FT,I를 도출하였다. 하지만 제안된 모터의 전기적 특성을 고려한 전류 기반 방법에서는 전류 – 슬립 관계를 이용해 토크와 슬립이 일정함을 가정하여 절삭력 FT,Current을 도출하였다. 주축 전력 기반 방법에서는 수집된 전류 및 전압을 이용해 전력을 구하여 절삭력 FT,Power을 추정하였다.
각각의 방법으로 추정한 절삭력을 공구동력계 측정 결과와 비교하였을 때, 기존 전류 기반 방법, 제안된 전류 기반 방법, 전력 기반 방법 각각 55.81, 10.73, 13.86 N의 RMS오차를 보이며 각 방법의 오차율은 19.42, 3.73, 4.82%로 나타났다. 각 방법들의 오차율을 비교한 결과, 모터의 전기적 특성을 고려한 주축 전류 기반 절삭력 추정 방법과 주축 전력 기반 절삭력 추정 방법의 정확도가 높음을 확인할 수 있었다.
Acknowledgments
본 연구는 2022 년도 정부(산업통상자원부)의 재원으로 한국산업기술진흥원(No. P0020616, 2022 년 산업혁신인재성장지원사업)과 2021 년도 산업통산자원부 및 산업기술평가관리원(KEIT) 연구비 지원에 의한 연구임(No. 20012834).
References
- KISTLER,Rotating cutting force dynamometers (RCDs), Fz max 20 kN, Mz max 150 Nm / 9170A, https://www.kistler.com/INT/en/cp/rotating-cutting-force-dynamometers-9170a/P0000633
-
Altintas, Y., Park, S., (2004), Dynamic compensation of spindle-integrated force sensors, CIRP Annals, 53(1), 305-308.
[https://doi.org/10.1016/S0007-8506(07)60703-3]
-
Dornfeld, D., Kannatey-Asibu, E., (1980), Acoustic emission during orthogonal metal cutting, International Journal of Mechanical Sciences, 22(5), 285-296.
[https://doi.org/10.1016/0020-7403(80)90029-6]
-
Teti, R., Jemielniak, K., O’Donnell, G., Dornfeld, D., (2010), Advanced monitoring of machining operations, CIRP Annals, 59(2), 717-739.
[https://doi.org/10.1016/j.cirp.2010.05.010]
-
Hase, A., Wada, M., Koga, T., Mishina, H., (2014), The relationship between acoustic emission signals and cutting phenomena in turning process, The International Journal of Advanced Manufacturing Technology, 70, 947-955.
[https://doi.org/10.1007/s00170-013-5335-9]
-
Postel, M., Aslan, D., Wegener, K., Altintas, Y., (2019), Monitoring of vibrations and cutting forces with spindle mounted vibration sensors, CIRP Annals, 68(1), 413-416.
[https://doi.org/10.1016/j.cirp.2019.03.019]
-
Kuntoğlu, M., Salur, E., Gupta, M. K., Sarıkaya, M., Pimenov, D. Y., (2021), A state-of-the-art review on sensors and signal processing systems in mechanical machining processes, The International Journal of Advanced Manufacturing Technology, 116(9), 2711-2735.
[https://doi.org/10.1007/s00170-021-07425-4]
- DMG MORI, Monitoring Cycles, Easy Tool Monitoring. https://www.dmgmori.co.jp/en/products/machine/id=2693
-
Jeong, Y.-H., Cho, D.-W., (2002), Estimating cutting force from rotating and stationary feed motor currents on a milling machine, International Journal of Machine Tools and Manufacture, 42(14), 1559-1566.
[https://doi.org/10.1016/S0890-6955(02)00082-2]
-
Li, X., (2005), Development of current sensor for cutting force measurement in turning, IEEE Transactions on Instrumentation and Measurement, 54(1), 289-296.
[https://doi.org/10.1109/TIM.2004.840225]
-
Aggarwal, S., Nešić, N., Xirouchakis, P., (2013), Cutting torque and tangential cutting force coefficient identification from spindle motor current, The International Journal of Advanced Manufacturing Technology, 65, 81-95.
[https://doi.org/10.1007/s00170-012-4152-x]
-
Kim, H. Y., Ahn, J., Kim, S., Takata, S., (2002), Real-time drill wear estimation based on spindle motor power, Journal of Materials Processing Technology, 124(3), 267-273.
[https://doi.org/10.1016/S0924-0136(02)00111-5]
-
Mannan, M., Broms, S., Lindström, B., (1989), Monitoring and adaptive control of cutting process by means of motor power and current measurements, CIRP Annals, 38(1), 347-350.
[https://doi.org/10.1016/S0007-8506(07)62720-6]
- HEIDENHAIN, User's manual cycle programming, iTNC 530. https://content.heidenhain.de/doku/tnc_guide/pdf_files/iTNC530/34049x-05/zyklen/670_388-20.pdf
-
Stein, J., Wang, C.-H., (1990), Analysis of power monitoring on AC induction drive systems, Journal of Dynamic Systems. Measurement, and Control, 112(2), 239-248.
[https://doi.org/10.1115/1.2896131]
- Tektronix, The fundamentals of three-phase power measurements, https://download.tek.com/document/55W_28943_0_HR_Letter.pdf
-
Hamid, R. H., Amin, A. M., Ahmed, R. S., El-Gammal, A. A., (2006), New technique for maximum efficiency of induction motors based on particle swarm optmization (pso), IEEE International Symposium on Industrial Electronics, 2176-2181.
[https://doi.org/10.1109/ISIE.2006.295910]
Master student in the School of Mechanical Engineering, Chungnam National University. Her research interest is real time monitoring.
E-mail: jaeeunk@o.cnu.ac.kr
Ph.D. candidate in the School of Mechanical Engineering, Chungnam National University. His research interest is intelligent CNC.
E-mail: kingoj0@o.cnu.ac.kr
Ph.D. candidate in the School of Mechanical Engineering, Chungnam National University. His research interest is digital twin.
E-mail: bssim@cnu.ac.kr
Associate Professor in the School of Mechanical Engineering, Chungnam National University. His research interests include smart machine tool, robotic machining systems and digital twin.
E-mail: wklee@cnu.ac.kr