
히트펌프기술을 적용한 농업용 하이브리드형 분산 난방 시스템 개발
Copyright © The Korean Society for Precision Engineering
This is an Open-Access article distributed under the terms of the Creative Commons Attribution Non-Commercial License (http://creativecommons.org/licenses/by-nc/3.0) which permits unrestricted non-commercial use, distribution, and reproduction in any medium, provided the original work is properly cited.
Abstract
Air-source heat pumps are widely used in places that require large-scale cooling and heating facilities such as factories and offices due to their ease of installation. However, their application to greenhouses with different installation environments is rare. Typical reasons are maintenance issues in existing farmhouses that use geothermal energy and energy inefficiency. In this regard, a hybrid heating system is necessarily considering the heating environment of greenhouses is increasing. At the same time, demand for a distributed heating algorithm to minimize energy wastage and lower heating cost is increasing. These developments provide an environmental condition and heating model that can grow crops at the same temperature throughout the greenhouse. The study aims to provide an optimized solution for heating greenhouses using a high-efficiency heat pumps and small electric heaters. In this study, we develop a hybrid distributed heating system consisting of a gateway server that can wirelessly manage a 10-kW wireless heat pump electric heater and a 3-kW small PTC electric heater, and monitor and control it using an external smartphone. We verify the reliability of the prototype development through structural analysis, EMC testing, and safety inspection.
Keywords:
Wireless, Distributed heater, Agriculture heat-pump, Remote automatic control, High efficiency heater키워드:
무선, 분산 난방기, 농업용 히트펌프, 원격 무선제어, 고효율 난방기1. 서론
우리나라 시설원예 면적은 2021년 기준 5만 3,359 ha로, 연간 시장 규모 또한 2018년 328억 원 대비 2022년 1,262억 원 추정으로 4배 이상 급격하게 증가했으며, 겨울철에 화석연료나 전기 등을 열원으로 이용해 난방을 하는 가온 재배 면적도 매년 증가해 전체 면적의 30.2%를 차지하고 있다[1,3].
2020년도에 발간한 에너지 총조사 보고서에서 석유 소비량은 57.3%, 전력 소비량은 40.0%로서 석유를 이용한 난방이 절반 이상을 차지하고 있다. 이처럼 유류의존도가 높다 보니 시설원 예농가는 유가변동에 매우 민감하고 경쟁력도 취약한 실정이며, 시설재배농가의 전체 경영비 중에서 겨울철 난방비가 차지하는 비중이 30-40% 정도로 매우 높아 난방비를 절약하는 것이 곧 농가의 소득을 높이는 방법이라 할 수 있다.
최근에는 이러한 난방비를 절감하기 위해서 전기를 이용한 난방방식을 도입하는 농가가 늘어나고 있다. 에너지 소비 추이를 보면 석유 소비량은 지속적으로 감소(2016년 대비 연평균 2.2%)하고 전력 소비량은 지속적으로 증가(2016년 대비 연평균 2.0%)하고 있다[2].
전기를 이용한 난방은 일반적으로 전기를 이용해 공기를 데워 순환시키는 방식이며, 대부분 농가에서 이러한 방식을 이용하여 난방을 하고 있다. 미국, 유럽, 일본 등에는 동절기 전력소모를 줄이기 위해서 전기히터, 온풍기, 전기장판 등의 난방기구를 대신하여 고효율 난방장치인 히트펌프를 사용하고 있다.
본 연구에서는 한국형 시설하우스 형태(연동, 단동 비닐하우스)를 고려하여, 난방효율을 높이기 위한 10 kW급 공기열 히트펌프 온풍기와 시설하우스의 국지적 가온을 위한 소형 PTC 전기히터를 개발하여 서로 상호 운영되는 하이브리드형 온실난방 시스템을 개발하였으며, 해당 시스템의 난방 능력 성능평가와 구성 시스템의 EMC 규격대응 설계 및 분석 결과를 소개하고자 한다.
2. 설계검증 및 분석
2.1 해석모델 정의 및 구조해석
Fig. 1은 개발 시제품의 연동 시설하우스에 적용되는 형태를 나타낸 개념도로서, 기본 난방은 효율이 높은 히트펌프 온풍기로 수행하며 부분적 가온이 필요한 경우 PTC 전기히터를 이용하여 국지적으로 가온을 수행할 수 있다.
본 연구개발품은 농업의 열악한 환경에서도 안정적인 동작이 가능하도록 내구성과 실용성을 위해 SUS 재질로 케이스를 개발하였으며 Fig. 2와 같이 무선 PTC 전기히터는 소형으로 벽 또는 기둥에 부착할 수 있도록 벽부가 달려져 있어 안정성을 위해 구조해석을 하였다. 2D 도면을 이용하여 Figs. 2(a)와 같이 3차원 모델링을 하였고 HyperMesh를 이용하여 Solid Element 요소인 Hexa, Wedge와 Sheet Element 요소인 Quad, Tria를 이용하여 2(b)와 같이 분할을 하였다. 이때, 유한요소모델은 Node 19,375개, Element는 17,992개이다.
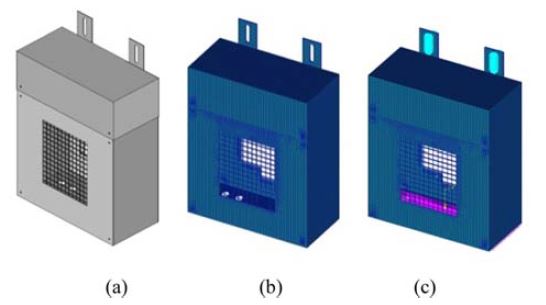
Structural analysis of PTC electric heater: (a) Three-dimensional model, (b) Finite element model generation, and (c) Boundary conditions
재료 물성치는 Table 1과 같이 사용하였다.
경계조건은 Fig. 2(c)와 같이 케이스 고정부를 3자유도 구속하고 하중조건은 케이스 내부에 부착되는 부품들의 하중 3 kg을 고려하여 구조의 안정성을 평가하였다.
구조해석 결과는 Fig. 3에 나타나 있으며, 최대 변형량은 케이스 하부에서 0.688 mm, 최대응력은 케이스 고정 브라켓 연결부에서 36.9 Mpa이 발생되었다. 응력은 케이스 브라켓에 집중이 되었으며 항복 응력을 고려하였을 때 케이스 구조 자체는 문제가 없었다.
2.2 EMC 노이즈 분석 및 대책 설계
전자기기의 구성 및 동작 제어에 따른 전자파 발생 영향성을 사전에 파악하고 전자파 노이즈 저감 대책 설계를 통한 제품 성능 개선 및 안정성 확대에 기여하고 KC 인증에 준한 EMC 시험평가 및 신뢰성 성능분석을 통해 문제점 도출 및 보완하여 개발 완료 제품의 최적 안을 제시하였다.
전자설계 회로도를 EMI Stream 시뮬레이션을 통한 PCB 회로검토 및 EMC 인증 진행 시 문제 발생 소지를 최소화하기 위한 설계대책을 적용하였다.
히트펌프 컨트롤러 PCB 회로검토 결과 Fig. 4(a)와 같이 신호 트레이스가 많고 양면 PCB로 설계되어 있어, 귀환전류(Return Current)가 최단거리로 형성되지 못해 신호 트레이스로부터 전자파가 발생할 가능성이 있으므로 Top Layer 빈 공간에 Decoupling Capacitor를 추가하여 특정주파수에서의 공진을 방지하였다.
PTC 전기 히터 컨트롤러는 Fig. 4(b)와 같이 전원 트레이스가 복잡하게 설계되어 있어 신호 트레이스가 겹치는 부분이 많아 노이즈가 서로 커플링 될 가능성이 있으므로 트레이스가 겹치지 않게 수정 설계하였다.
전자기기의 구성 및 동작 제어에 따른 전반적 EMI를 최소화하려면 직접 보드와 모듈의 방사소스를 파악해야 한다. Noise Scanner와 Near-Field Probe를 통해 개발품에서 노이즈가 발생되는 경로를 파악하고 이를 필터링 및 대책 설계하여 다양한 형태로 발생하는 전자파 요인을 제거하였다.
먼저 무선 히트펌프 컨트롤러의 PCB TOP 면의 Noise Scanner를 통한 노이즈 발생분포를 육안으로 확인했을 때, Fig. 5(a)와 같이 신호처리단 및 IC 칩 주변에서 노이즈 강도가 가장 크게 나타남을 확인하였다. 전자계를 측정하여 노이즈 분포를 파악한 결과를 토대로 Near Field Probe를 이용하여 방사 노이즈를 스펙트럼으로 재확인 결과, FPCB 케이블의 신호, 데이터, 클럭 라인을 타고 나오는 EMI 방사 노이즈가 스위칭되어 Fig. 5(b)와 같이 30 MHz 대역에서 가장 높게 발생함을 확인하였다.
다음으로 무선 소형 PTC의 PCB Top 면에서의 최대 노이즈 발생 위치를 확인한 결과, Fig. 5(c)와 같이 AC-DC 컨버터 주변에서 노이즈 강도가 높음을 확인한 후 30 MHz-1 GHz 대역에서 근접필드 프로브를 사용하여 실시간 스펙트럼 분석기로 재확인한 결과, 컨버터에서 스위칭 전원의 출력파형이 일정한 주기를 띄며 고주파 노이즈가 발생하고 있었다. 또한 Fig. 5(d)와 같이 메인 MCU로부터 발생하는 노이즈가 신호 트레이스를 통해 방사되고 있으므로 스위칭 노이즈와 그 하모닉 성분을 줄이기 위해 스너버 회로로 Drain-Souce 사이에 최적의 RC 값을 적용하면 스위칭 노이즈를 감소할 수 있다. 정전용량 100 pF을 적용하면 200 MHz 이상 고주파 스위칭 노이즈를 감소할 수 있다[4,5].
Fig. 5(e)는 무선 게이트웨이의 PCB Top 면의 노이즈 스캐너 분석결과 신호처리단 및 IC 칩 주변에서 노이즈가 발생하고 있으며, 이를 Figs. 5(f) 및 6과 같이 스펙트럼으로 확인한 결과 또한 IC 칩 및 RF 안테나에서 발생하는 25.24 MHz 하모닉 성분의 스위칭 노이즈임을 알 수 있었다. 현재 부품변경은 불가하여 페라이트 코어를 통해 200 MHz 이하의 그라운드성 노이즈의 레벨이 낮아짐과 200 MHz 이상의 하모닉성 고주파 노이즈의 전달 경로가 제거됨을 확인한 후 최종적으로 무선 게이트웨이의 KC 인증획득을 위해 EMC 시험을 진행한 결과, Fig. 7과 같이 기준치에 만족하는 결과를 확인할 수 있었다.
3. 실증 실험용 테스트베드 구축
3.1 실증 실험을 위한 시뮬레이션 수행
본 결과물의 실증 실험을 위한 시스템 설치에 앞서, 실증 온실의 모양 및 형태를 참조하여 본 시스템의 설치 위치 및 주변 환경의 영향을 사전 검토를 위하여 Ansys 사의 Fluent 기반으로 시뮬레이션을 수행하였다. 이는 실제 온실의 모양 및 설치 여건 등에 의하여 히트펌프 난방기의 설치 위치가 제약적이었으며, 이를 고려 했을 때, 순환팬 및 PTC 난방기의 위치에 의하여 공기의 흐름과 와류 등의 문제는 없는지 그리고 열전달 흐름과 시간에 따른 열전달 온도변화는 어떻게 변하는지를 시뮬레이션을 수행하였다.
Fig. 8(a)와 같이 실증 온실은 약 700평 규모의 계단과 같은 형태를 가지며, 그림의 오른쪽 편은 도랑이 존재하여 히트펌프는 왼쪽 편에 위치할 수 밖에 없었다.
이러한 조건으로 내부 온도 및 공기흐름을 해석한 결과, 히트펌프와 PTC 사용 시 순환팬에서 나오는 2 m/s, 3oC의 공기가 전체 흐름에 영향이 있어 주변의 고온과 저온 유체가 잘 혼합되게 하므로 전체적으로 14.834oC (287.834 K)의 평형상태에 도달하였다. 그러나 실제 순환팬은 주변 온도에 맞춰 회전하는 기능만 하기 때문에 팬 3D Model과 차이는 존재하나 온실 규모 및 열원 발생 온도 그리고 온실의 단열재 등을 고려하면 해당 오차는 무시할 수 있다.
약 6 × 8 m 간격으로 순환팬 모델을 두고 시뮬레이션을 수행한 결과 Fig. 9와 같이 대략 5분 이내로 토마토 재배를 위한 야간 설정값인 15oC 값에 도달하였다.
3.2 실증 실험 환경 구축
시뮬레이션 결과를 바탕으로 본 연구에서 개발된 난방기 및 운영 시스템의 성능을 실증 실험하기 위해 테스트베드를 Fig. 10과 같이 경북 김천에 구축하였다.
하우스 모델은 실제 재배작물인 토마토 하우스로, 1중에는 PE 필름과 2중에는 차광과 보온 다겹으로 구성되었다. 토마토 재배 기준으로 야간 15oC 난방을 위해 약 190 kW 정도의 난방능력이 필요하며 이를 위해 250 kW 수전은 추가 설치되었다. 야간 15oC 난방 능력을 발휘하기 위해 본 테스트베드에는 10 kW급의 히트펌프 10개, 3 kw 급의 PTC 전기히터 51개를 설치하였다.
또한 외부 환경 정보 수집을 위해 외부 기상대를 설치하였고, 온실의 온도 변화량 모니터링을 위한 온습도 센서노드를 52개 설치하였다.
3.3 에너지 효율 모니터링 실증 실험
본 실증 실험에서는 난방효율 검증방법으로 식(1)의 난방부하 수식을 기반으로 에너지 효율을 모니터링하였다[6].
(1) |
여기서, Q는 난방부하(kcal/h), AW는 시설의 표면적(m2), U는 피복의 난방부하계수(kcal/m2/h/oC), Tin는 실내설정온도(oC), Tout는 실외온도(oC), fr는 보온피복의 열절감율이다.
테스트베드의 시설의 표면적은 약 3,465 m2, 기초피복의 난방부하계수는 5.7 (PE Film), 보온 다겹과 차광의 열절감율 7.5%를 삽입하였고, 난방기를 15oC 온도유지 설정으로 야간 14시간(오후 5시-다음 날 오전 7시) 동안 동작시켜 실험단계에서의 난방부하를 계산하였고 그 결괏값은 식(2)와 같이 다시 kW로 환산하여 입력된 전력값과 비교하여 에너지 효율은 평균 2,281.8 kcal/1 kW로 Fig. 11과 같이 실증되었다.
일반적으로 히트펌프의 성능은 COP (Coefficient of Performance) 계수로 표시하지만 COP는 온도에 따라 다르게 나타날 뿐만 아니라 해당 연구에서는 PTC 난방기가 혼용되었으며, 실험과 같이 외부기온과 내부기온을 바탕으로 전체 시간을 기반으로 값을 도출하였기에 의미가 있는 값이다.
(2) |
여기서, Qheat-pump는 난방용량(kcal/h), Q는 난방부하, CFBlowing method는 송풍방식 보정계수로, SF는 안전계수이다. 송풍방식 보정계수는 무덕트 방식 온풍난방으로 1.1, 안전계수는 0.1로 적용하였다.
또한 테스트베드 온실 내부의 온도는 게이트웨이를 통해 클라우드에 저장된 누적 데이터 로그로 환산 및 적분 후 최고와 최저 온도 차이는 2.3oC로써 Fig. 12와 같이 도출하였다.
4. 결론
본 연구에서는 농업용 온실에서 탄소 및 에너지 절감을 위한 히트펌프 온풍기와 국지적 난방이 가능한 PTC 전기 히터를 개발하였으며, 해당 시스템의 단독 성능평가 및 실증 시뮬레이션과 테스트베드 구축을 통하여 실제 온실 환경에서 적용 가능한지 실험을 수행하였다. 수행 결과 다음과 같은 결론을 얻을 수 있었다.
(1) Ansys Fluent 시뮬레이션 결과와 실증 실험을 통하여 약 2 m/s 순환팬을 6 × 7 m 간격으로 공기순환 방향을 반대로 한다면, 일반 온실에서 사용하는 비닐 덕트 없이 온도 편차가 3oC 이하로 난방이 가능하다.
(2) 본 결과물인 농업용 히트펌프 온풍기와 PTC 전기히터의 하이브리드형은 kw당 2,281.8 kcal로 기존의 농업용 전기 온풍기의 860 kcal에 비하여 약 2.6배의 에너지 효율을 나타냈다.
(3) 다량의 온풍기와 전기히터를 무선기반 네트워크를 통하여 효율적으로 관리할 수 있음을 확인하였으며, 해당 시스템은 농가의 사용 편의를 도모할 수 있을 것으로 기대된다.
이상과 같은 실험을 통해 제작된 분산 난방 시스템은 전자파 설계가 반영되어 있어 실제의 서비스 환경하에서 무선 성능이 우수하여 전파 성능에 대한 신뢰도를 확보하였다. 실제 무선기반 네트워크 환경 구축에는 개발품에서 방사되는 다양한 잡음원과 다중경로간섭 등이 혼재하고 있지만 이러한 요소를 고려한 효율적인 하이브리드형 분산 난방 시스템을 설계할 수 있는 기반을 만들 수 있었다.
Acknowledgments
This paper was presented at KSPE Spring Conference 2021
REFERENCES
- Rural Development Administration, (2019), 2018 Smart Greenhouse Guideline, https://www.nihhs.go.kr/pdf/farmerUseProgram/smart_greenhouse_guideline.PDF
- Korean Energy Economics Institute, (2022), 2020 Energy Consumption Survey. http://kemco.or.kr/web/kem_home_new/info/statistics/data/kem_view.asp?sch_key=&sch_value=&c=305&h_page=1&q=23399
- Ministry of Agriculture, Food and Rural Affairs, (2018), A Study on the Development of Smart Farm Equipment Industry. http://www.the30f.com/wp-content/uploads/2019/10/1.-%EA%B5%AD%EB%82%B4%EC%99%B8-%EC%8A%A4%EB%A7%88%ED%8A%B8%ED%8C%9C-%EA%B8%B0%EC%9E%90%EC%9E%AC-%EA%B8%B0%EC%88%A0%ED%98%84%ED%99%A9-%EB%B6%84%EC%84%9D%EB%B3%B4%EA%B3%A0%EC%84%9C-1.pdf
-
Hata, R., Nishiyama, S., (2018), The effect of built-in CR snubber capacitor into the power module, Proceedings of the 2018 International Power Electronics Conference (IPEC-Niigata 2018-ECCE Asia), 2149-2152.
[https://doi.org/10.23919/IPEC.2018.8507733]
- Kim, J. S., (2019), SMPS EMI/EMC technology trends and countermeasures technology, The Proceeding of the Korean Institute of Electromagnetic Engineering and Science, 30(1), 29-38.
- Rural Development Administration(RDA), (2014-2015), Development of a hybrid heat pump system for greenhouse with solar and air heat source, (Report No. 1395039880). https://scienceon.kisti.re.kr/srch/selectPORSrchReport.do?cn=TRKO201600003316
Senior researcher in the Daegu Mechatronics & Materials Institute. Her research interest is EMC engineering and analysis.
E-mail: jmlee@dmi.re.kr
CTO at UBN Co., Ltd.. His research interest is wireless smart farm networking.
E-mail: gjkim@ubncorp.kr
CEO at UBN Co., Ltd.. His research interest is A.I. and big data in smart agriculture.
E-mail: ekahn@ubncorp.kr