
소형펀치시험에 의한 인코넬617용접부의 크리프거동 평가


Copyright © The Korean Society for Precision Engineering
This is an Open-Access article distributed under the terms of the Creative Commons Attribution Non-Commercial License (http://creativecommons.org/licenses/by-nc/3.0) which permits unrestricted non-commercial use, distribution, and reproduction in any medium, provided the original work is properly cited.
Abstract
In this research, the small punch (SP) test was applied to examine the local creep characteristics of a narrow gap weldment. To find the local creep property, an Ni-based 617 alloy and its narrow gap weldment. which is one of candidates for advanced fossil power plants, were employed. Thin square specimens were machined at three different locations: weld metal, base metal, and HAZ near the base metal from the Inconel 617 alloy narrow gap weldment. The results of the SPC test were evaluated. The microstructure of narrow gap weldment was observed by scanning electron microscopy and optical microscopy to investigate the effect of the microstructure on the creep properties of the weld zone. The creep rupture part of the weldment was observed by scanning electron microscopy. Finally, four different creep characteristics of the narrow gap weldment were obtained by the SPC test with good validity.
Keywords:
Small punch test, Cross weld, Weldment, Fusion line, Heat affected zone키워드:
소형펀치시험, 용접횡단부, 용접부, 용융선, 열영향부1. 서론
재료의 물성 측정에 있어서 시편의 경제적 활용은 실험을 수행하는데 있어서 다양한 이점을 가지고 있다. 소형화된 시험편은 가공공정의 경제성, 가공비용 및 시간, 대형 벌크에 비해 많은 수의 시험편 획득 등 다양한 활용성을 제공한다. 이러한 이점은 대형 설비부품의 기계적 물성이나 건전성평가를 위한 시편샘플링에 있어서 통상적인 시편의 크기와 달리 작은 크기의 시편채취는 비파괴 시험에 견줄만한 매우 좋은 효과를 가져온다.
이러한 측면에서 소형 펀치(Small Punch) 시험 방법은 기존의 인장 크리프 시편과 비교하여, 매우 작은 크기(10 × 10 × 0.5 mm)와 경량의 시편만 필요하기 때문에 운전중인 설비기기의 건전성에 아무 영향도 끼치지 않고 고온 크리프수명 예측에 있어서 비파괴적 방식으로 시편샘플을 채취할 수 있는 매우 유익한 잠재적 효용성을 가지고 있다[1-9]. 특히, 소형펀치 크리프(Small Punch Creep, SPC) 시험기는 직경 2.4 mm의 세라믹(Si3N4) 볼을 장착하여 시편의 표면에 반구(Half of a Sphere) 형태로 집중하중이 가해지기 때문에 다양한 미세구조의 협궤용접부의 국부적인 크리프 특성 평가가 가능하다[10-13]. 본 연구에서는 협궤 용접부의 국부적인 크리프 특성을 조사하기 위해 SPC 시험을 적용하였다. 용접부의 미세조직 별 SPC 시험가능성을 찾기 위해 Inconel 617 합금의 협궤 용접부를 사용했으며, SPC 시편을 용접재(Weldmetal), 모재(Basemetal) 및 열영향부(Heat Affected Zone)의 세 가지 미세 구조 영역별로 SPC 시편의 형태로 제작하였다. 추가적으로, 용접부 미세조직이 크리프 거동에 미치는 영향을 조사하기 위하여 광학 및 주사전자현미경으로 협궤 용접부의 미세조직 및 파단부를 관찰하였다. 본 연구에 사용된 Inconel Inconel® 합금 617(UNS N06617/W.Nr.2.4663a)은 고온 강도와 내산화성이 뛰어난 고용체 강화 니켈-크롬-코발트-몰리브덴 합금이며 광범위한 부식 환경에 대한 저항성이 우수하며 기존 기술에 의해 쉽게 용접되는 특성을 가지고 있다[14-17].
2. 실험방법
2.1 재료 및 경도시험
본 연구에는 상업용 Ni 기반 617 합금을 Thyssen 617(용가재)를 이용하여 동종용접을 수행한 협궤용접부를 실험 재료로 사용하였다. 이 합금은 첨단 화력 발전소와 원자력발전소 및 항공기 및 지상 기반 가스 터빈설비기기의 고온용 덕트, 초고온 원자로의 1차 냉각수 관로와 2차 냉각수 관로 사이의 중간 열교환기 등의 설비요소에 대한 매력적인 재료로 사용된다. Table 1은 HAYNES의 Inconel 617 합금(모재)과 Thyssen 617(용가재)의 화학 조성을 보여준다[18]. Fig. 1은 Inconel 617 합금의 협궤용접 블록을 나타낸다. 용접 절차는 TIG (Tungsten Inert Gas arc Welding)에 의해 7 패스로 수행되었으며, 용접 후 열처리는(Post Weld Heat Treatment, PWHT)는 미세조직의 고유특성을 조사하기 위해 수행하지 않았다. 용접부의 국부 강도를 조사하기 위해 AKASHI 미세 경도 시험기를 사용하여 용접재, 열영향부 및 용접부의 모재에서 경도 프로파일을 얻기 위해 용접부 전체에 걸쳐 횡방향으로 미세 경도 측정을 수행하였다. 미세경도시험의 시험하중과 하중시간은 각각 500 g과 5s의 조건으로 실시하였다.
2.2 소형펀치 크리프 시험
협궤 용접부의 국부 크리프 특성 평가가 가능한지를 알아보기 위해 SPC 시험을 적용하였다. Fig. 2는 본 연구에 사용된 SPC 시험기 및 지그를 보여준다. SPC 테스트 지그는 펀처, 볼, 상부다이, 하부다이로 구성된다. 시편은 먼저 하부 다이에 배치된 후 상부 다이가 하부 다이에 조립된다. 이 어셈블리는 최종적으로 4개의 클램핑 나사로 고정되고 직경 2.4 mm의 세라믹(Si3N4) 볼이 펀처를 통해 SPC 시편에 탄성한도 이내의 일정한 하중을 가하게 된다. SPC 시편의 준비는 Fig. 3과 같이 SPC 시편의 가공 위치를 결정하기 위해 용접부를 식각(Etching)하고 박판의 사각(10 × 10 × 0.5 mm) 시편을 용접부에서 3개의 서로 다른 위치, 즉 용접재, 모재 및 용접부의 열영향부에서 와이어커팅(Wire Cutting)으로 가공하였다. 특히 열영향부(Cross Weld) 시편은 용융선(Fusionline)이 시편 중앙에 위치하도록 가공하였다. 모든 SPC 시편은 표준 금속조직 샘플 준비방법에 따라 연마하였다. 가공 스크래치에 의한 응력 집중을 방지하기 위해 0.1 μm Al2O3 분말을 사용하여 최종 연마 공정을 진행하였으며, 최종 두께는 디지털 마이크로미터로 0.5 mm±10 μm 이내로 조절하였다. Table 2는 세 가지 시편에 대한 SPC 하중 조건을 나타낸다. 시편의 변위는 선형 가변 변위 변환기(LVDT)로 10-3 m의 정밀도로 측정하였다. 모든 SPC 시험은 시험중 산화를 방지하기 위해 아르곤가스 조건에서 700oC에서 수행되었다. SPC 시험기 고온챔버의 온도는 ±1oC의 정확도로 제어하였다.
2.3 미세조직 및 파괴
Inconel 617협궤 용접부의 크리프 거동에 미치는 미세조직의 영향을 알아보기 위해 용접부를 광학현미경(OM)과 주사전자현미경(SEM)으로 관찰하고 각 미세조직을 비교하였다. 또한 Inconel 617협궤 용접부의 석출물을 분석하기 위해 EDS(Energy Dispersive X-ray Spectroscopy)를 사용하였다. 특히, SPC 시험 후 협궤 용접부의 국부 적 미세조직특성이 크리프의 파단 양상에 미치는 영향을 조사하기 위해 용접재, 모재 및 열영향부 시편의 크리프 파단 부위를 주사전자현미경(SEM)으로 조사하였다.
3. 결론 및 고찰
3.1 금속 조직 및 미세경도
Inconel 617협궤 용접부의 주사전자 현미경과 광학현미경에 의한 미세조직 관찰결과는 각각 Figs. 5와 7에 제시되어 있다. Fig. 6은 Inconel 617협궤 용접부의 석출물에 대한 EDS 스팟 및 라인 스캔 분석 결과를 나타낸다. Fig. 4는 미세경도 시험 결과를 나타낸다. Fig. 4에서 보는 바와 같이 용접재에서 모재로 갈수록 경도가 급격하게 떨어지는 것으로 나타났다. 이러한 경도분포는 열영향부에 형성된 용접계면 미세조직에서 멀어짐에 따라 냉각이 급격히 감소함을 나타내며, 미세조직의 불균일성은 경도 변화와 향후 크리프 시험에도 영향을 미칠 것이 예상된다.
Fig. 5는 (a) 모재, (b) 용접재 및 (c), (d) HAZ에 대한 주사전자 현미경 관찰결과를 보여준다. 모재와 용접 재의 미세조직은 용융선을 경계로 서로 다른 조직을 나타내었다. Figs. 5(d)와 7(f)는 Thyssen 617 Filler 용접재와 Inconel 617 모재의 계면 영역에 대한 미세조직을 나타내며, 서로 간에 혼합되지 않은 영역은 크게 관찰되지가 않았다. 이러한 미세조직의 특성은 용융온도와 화학조성의 관점에서 617 Filler와 모재의 유사성에 기인할 수 있다. Fig. 5에서 보는 바와 같이 (a) 모재의 미세조직은 평균 입도가 50 μm인 오스테나이트계(γ) 기지와 일부 입계 및 입계 석출물을 보이는 반면, 용접재는 주상정(Dendrite) 조직을 가진 기지내에 분산된 석출물을 포함한 완전한 오스테나이트 조직을 나타낸다. Figs. 6(b)와 6(c)는 각각 6(a)에 표시된 석출물을 표적으로 삼은 빨간색 기호와 파란색 기호의 EDS Spot에 의한 성분분석 결과를 보여준다. Figs. 6(a), 6(b), 6(c)에 나타난 바와 같이, 일부 입계에서 약 5 μm의 평균 크기를 갖는 탄화물 석출물은 Cr-rich (M23C6), Mo-rich (M6C) Carbides로 사료되며 결정립 내의 밝은 입자는 Figs. 6(d), 6(e)에 표시된 Ti(N)으로 판단된다[14,15].
또한 입계를 가로지르는 EDS 라인스캔에 의한 성분 분석에서 스캔 프로파일의 결과는 Figs. 6(b) 및 6(c)와 유사하였다. 용접재에서 대부분의 미세 구조는 Figs. 5(b), 5(e) 및 7(d)와 같이 미세한 등축의 주상정으로 조사되었다. Thyssen 617 Filler 용접재는 다른 용접재에 비해 최대 극한 인장 강도와 총 연신율을 나타내는 것으로 보고되어있다[18]. 이는 Thyssen 617 Filler 용접재의 미세한 주상정(Dendrite) 미세조직과 관련이 깊은 것으로 사료된다. 따라서 이러한 등축 주상정 미세조직은 크리프 저항에 기여하고 모재와는 다른 크리프 파단 거동을 나타낼 것으로 예상된다. 일반적으로 이러한 미세조직은 용접 공정 중 응고 균열을 줄이는 더 낮은 Mo의 편석 비율을 가지고 있는 것으로 보고되어있다[19,20].
Figs. 5(f)와 7(e)에서 볼 수 있듯이 MGB (Migrated Grain Boundary)가 적게 관찰되었으며 이는 SGB (Solidification Grain Boundary)와 Subgrain Boundary를 따라 석출물이 형성되었기 때문일 수 있다. 이러한 석출물과 SGB는 크리프 파괴 거동에 있어서 전위의 이동에 대한 피닝(Pinning) 효과를 불러올 수 있는 중요한 역할을 한 것으로 사료된다[21].
Figs. 7(b), 7(c)와 같이 용융선으로부터 약 0.2 mm까지는 모재와 용접재의 결정립이 혼합된 결정립조직과 조대한 결정립이 관찰되었다. Fig. 5(g)에 도시된 바와 같이, 기계적 성질에 악영향을 미칠 수 있는 균열 및 미세공극이 관찰되었다. 이러한 균열은 응고균열에 의해 발생하는 것으로 여겨진다[19]. Fig. 7(e)는 열영향부 지역의 혼합된 결정립을 고배율로 관찰한 결과를 나타낸다. 혼합된 결정립은 오스테나이트 매트릭스와 미세한 등축 덴드라이트 미세 구조로 나타나며. 이러한 미세조직의 천이 영역은 크리프 강도 불일치를 초래할 수는 원인이 될 수가 있다. 또한 균열, 미세공극과 같은 결함은 Fig. 3에서 기술한 SPC 열영향부(Cross Weld) 시편의 포함 여부에 관계없이 크리프 시험결과의 데이터의 산포에 영향을 미칠 것으로 판단된다.
3.2 Inconel 617협궤 용접부의 크리프거동
Fig. 8은 다양한 하중 조건에서 Inconel 617협궤 용접부의 모재, 용접재 및 열영향부 시편의 SPC 시험에서 얻은 변위-파단 시간 곡선을 나타낸다. SPC 곡선은 단축 크리프 곡선과 유사한 결과를 나타냈으며 Fig. 9는 모재, 용접재 및 열영향부에 대한 SPC 곡선의 비교 결과를 나타낸다. Figs. 9(a)와 9(b)와 같이 동일한 하중 조건에서 용접재에서 가장 긴 크리프 파단 수명이 나타났지만 열영향부는 가장 짧은 파단 수명과 가장 가파른 변위 기울기를 나타내었다. 용접재의 크리프 속도가 가장 느리게 나타나는 원인은 위에서 언급한 바와 같이, 용접재의 미세한 등축 주상정 미세조직이 크리프 강도와 파단 수명의 증가에 기여하였기 때문인 것으로 사료된다. 열영향부 시편의 파단 시간은 모재 및 용접재의 파단 시간보다 낮았으며 이러한 크리프 시험결과는 시험 하중이 감소함에 따라 더욱 중요하게 나타났다. 이는 열영향부의 크리프 강도가 모재 및 용접재의 크리프 강도보다 낮음을 나타내는 결과이다. 폭이 0.2 mm인 열영향부의 크리프 변형에 주변 재질의 일부 기여가 있었음에 틀림없으며, 이러한 영향은 2.4 mm 볼 압입자에 의한 균열 시작 및 전파가 모두 열영향부지역 내에서 발생하는 것으로 관찰되었기 때문인 것으로 고려해볼 수 있다. 보고서에 따르면 열영향부에는 크리프 강도를 낮추는 3축 응력 상태가 존재하는 것으로 알려져 있다[10].
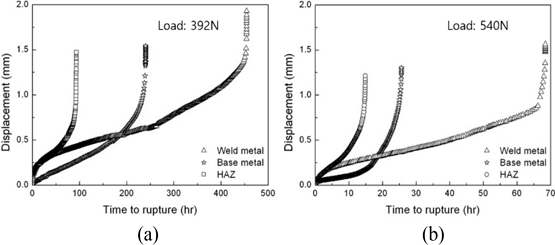
Comparison results of SP creep curves of (a) Base metal (b) Weld metal (c) HAZ (cross weld) of Fig. 8 at same load condition
일반적으로 열영향부의 크리프 변형은 상대적으로 크리프 강도가 높은 용접재와 모재에 의해 기계적으로 구속되며 열영향부에서 3축 응력 조건을 생성하게 된다. 선행 연구에서 우리는 일련의 단속된 크립 파단 시험을 통해 상대적으로 많은 수의 크리프 캐비티(Cavity)가 발견된 Type IV 영역에서 크립 파단의 넥킹이 발생했음을 입증한 바가 있다[5]. 크리프 공동(Voids)은 Prior Austenite Grain Boundaries에서 큰 M23C6 탄화물의 계면에서 자주 관찰되었으며, 이 자리가 크리프 공동생성에 기여한 것으로 판단된다.
Fig. 10은 SPC 시험으로부터 얻은 617 Alloy 용접부의 각각의 재질별 시편의 최소 변위속도와 적용 하중 사이의 관계를 나타낸다. SPC 시험에서 최소변위속도 (mm/hr)과 하중 P (N) 사이의 관계는 방정식(1)로 설정할 수 있다.
(1) |
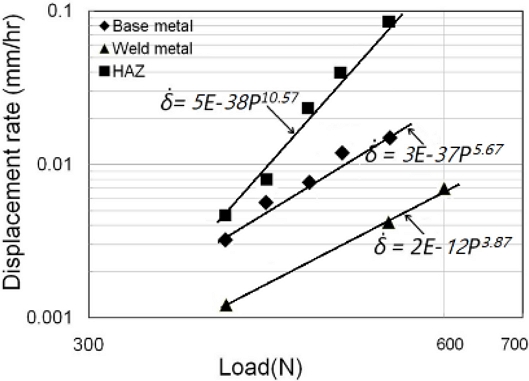
Comparison results of SP minimum displacement rate of (a) Base metal (b) Weld metal (c) HAZ (Cross weld) at 700oC
여기서 A는 상수이고 n은 하중지수이다.
용접재와 모재의 하중 지수는 각각 3.87과 5.67인 반면, HAZ의 하중 지수는 10.57로 나타났다. 용접재와 모재의 변위속도는 매우 유사한 경향을 보였다.
용접재 시편은 최소 변위속도가 가장 낮았고, 열영향부는 가장 높은 최소 변위속도를 나타내었다. 열영향부 시편의 최소 변위속도는 모재 및 용접재보다 높게 나타났다. 이러한 결과는 더높은 하중 조건에서 더 중요해지는데, 이는 비균질한 미세조직을 갖는 열영향부가 상대적으로 균일한 미세구조를 갖는 모재 및 용접재에 비해 하중조건에 매우 민감함을 의미한다. 이 결과는 SPC 시험 중 파괴 거동과 관련이 있는 것으로 판단된다.
용접재, 모재 및 열영향부에 대한 변위 속도와 파단 시간 사이의 관계는 Fig. 11에 나와 있으며 이는 일축 크리프 시험에 대한 Monkman-Grant 방정식의 Power Law 표현방식과 유사하다. 일반적으로 Monkman–Grant 방정식의 지수 값 m은 대부분의 금속 합금에서 1과 같다는 것이 알려져 있으며, 매우 좋은 선형관계를 나타내기 때문에 SPC 수명에 대해 Monkman-Grant 방정식의 형태와 유사한 방정식을 생성하려는 시도가 있어왔다. 그 결과 방정식은 다음 방정식으로 유도된다.
(2) |
여기서 B는 상수이고 m은 속도지수 값을 나타낸다.
Fig. 11(a)에서 보는 바와 같이 모재, 용접재, 열영향부를 개별적으로 비교한 결과 용접재와 모재의 지수값은 각각 1.02와 0.93으로 거의 유사한 반면, 열영향부는 0.53으로 나타났다. 그러나 Fig. 11(a)의 모든 데이터를 포함하는 결과는 Fig. 11(b)와 같이 양호한 선형관계를 보여주며 속도지수값은 0.76으로 나타났다. 따라서 이러한 결과는 국부적인 SPC 시험방법의 타당성과 가능성을 반영한 것으로 사료된다.
3.3 Inconel 617협궤 용접부의 크리프 파괴거동
각 SPC 파단 시편의 파단면 관찰을 통해 이에 대한 파괴양상이 밝혀졌다. Fig. 12는 392 N의 하중에서 용접부의 각 미세조직별 SPC 시험시편의 파단면을 보여준다. Fig. 12(a) 모재에서 보는 바와 같이 크리프 취성 입계 파괴 모드가 관찰되었으며 중앙의 파단구멍을 중심으로 방사 방향의 여러 개의 취성 가지 균열이 주로 형성되어있다. Figs. 12(b)는 12(a)의 균열부위를 고배율로 관찰한 것으로, Inconel 617 합금의 크리프 파단부에서 전형적으로 관찰되는 결정립계를 따라서 균열이 전파되는 크리프 균열이 관찰되었으나, 크라프 공동이나 연성 딤플은 관찰되지 않았다. 그러나 용접재의 경우 파단양상은 Fig. 12(c)와 같이 거의 연성파괴를 보였고 약간의 취성파괴가 나타났다.
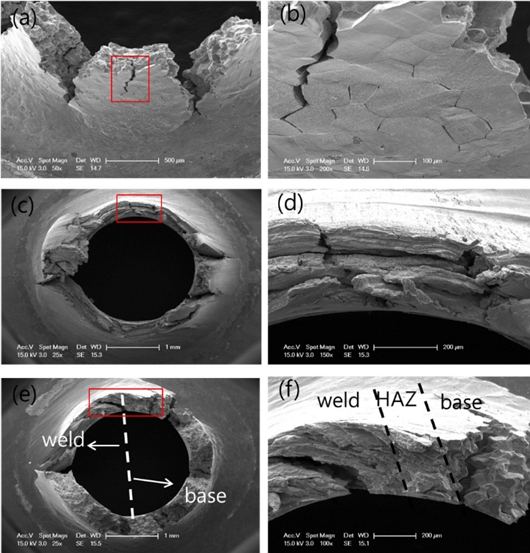
Bottom fracture surface of SP creep rupture specimen (a) Base metal (c) Weld metal (e) HAZ at 392 N (T = 700oC)
그러나 모재와 같이 방사방향의 취성가지균열은 거의 관찰되지 않았다. Figs. 12(d)는 12(c)의 고배율 관찰결과로서 MGB와 SGB에서 파단이 발생한 것을 알 수 있다. Fig. 12(e)는 HAZ 시편의 파단면을 보여준다. Fig. 12(e)와 같이 모재와 용접재의 파단양상이 혼합된 상태로 용접계면부에서 관찰되었다. Figs. 12(f)는 12(e)의 고배율 관찰결과로 용접부에서 국부적으로 가장 약한 부분인 열영향부에서 파단이 발생한 것을 알 수 있다. 이 결과로부터 열영향부의 파단거동이 용접재와 모재의 기계적 강도차이와 불균일한 미세조직으로 인한 금속조직학적 거동에 영향을 받고 있음으로 조사되었다.
4. 결론
SPC 시험에 의한 Inconel 617 합금 용접부의 국부적 크리프 거동으로부터 다음과 같은 결론을 얻었다. 열영향부 지역은 크리프 변위속도가 가장 빠르고 파단수명이 가장 짧아 용접부 전체에서 가장 취약한 부분인것으로 조사되었다. 금속조직학적 조사 및 파괴 양상 관찰 결과에서 용접부 열영향부의 미세조직의 천이영역으로 인하여 크리프 조기 파손으로 이어지는 크리프 강도 불일치를 초래할 수 있음을 알 수가 있었다. 그러나 모재 및 용접재 시편에서는 파단 양상이 취성이기는 하지만 상대적으로 크리프 수명이 길게 나타났다. 최종적으로, Inconel 617 합금 용접부에 대해 제안된 SPC 크리프 시험방법은 용접부의 다양한 미세조직에 대한 크리프 특성을 도출하고 국부적 SPC 시험방법의 타당성과 가능성을 제공할 수 있는 것으로 판단된다.
NOMENCLATURE
: | Minimum Displacement Rate |
P : | Strip Applied Load |
n : | Load Exponent |
m : | Exponent of Displacement Rate |
tf : | Time to Rupture |
Acknowledgments
본 연구는 오산대학교 2021년 교내학술연구지원에 의하여 이루어졌습니다.
REFERENCES
- Parker, J. D., (1994), Creep behaviour of miniature disc specimens of low alloy steel, PVP, 279, 167-172.
-
Ule, B., Sustar, T., Rodic, T., Dobes, F., Milicka, K., Bicego, V., Tettamanti, S., Maile, K., Schwarzkopf, C., Whelan, M. P., (1999), Small punch test method assessment for the determination of the residual creep life of service exposed components, Technology, Law and Insurance, 4(3-4), 283-293.
[https://doi.org/10.1080/135993799349036]
- Yun, G.-B., Park, T.-G., Sim, S.-H., Jeong, I.-S., (2001), Assessment of creep properties of 9Cr steel using small punch creep testing, Transactions of the Korean Society of Mechanical Engineers A, 25(9), 1493-1500.
-
Kim, B., Lim, B., Ki, D., (2006), Creep behavior and life evaluation of aged P92 steel, International Journal of Modern Physics B, 20(25n27), 4231-4236.
[https://doi.org/10.1142/S0217979206041148]
-
Kameda, J., Bloomer, T., Sugita, Y., Ito, A., Sakurai, S., (1997), Mechanical properties of aluminized CoCrAlY coatings in advanced gas turbine blades, Materials Science and Engineering: A, 234, 489-492.
[https://doi.org/10.1016/S0921-5093(97)00283-9]
- Tettamanti, S., Crudeli, R., (1998), Small punch creep test: A promising methodology for high temperature plant components life evaluation, BALTICA ? Plant Maintenance for Managing Life & Performance, 501-509.
- Wachter, O., Zabelt, K., Ennis, P., Helmrich, A., Bohme, A., (1998), The design, manufacture and installation of a P92 header, Forschungszentrum Juelich Schriften Reihe Energietechnik, 5(1), 351-360.
-
Hyde, T., Stoyanov, M., Sun, W., Hyde, C. J., (2010), On the interpretation of results from small punch creep tests, The Journal of Strain Analysis for Engineering Design, 45(3), 141-164.
[https://doi.org/10.1243/03093247JSA592]
-
Hyde, T., Sun, W., Williams, J., (2007), Requirements for and use of miniature test specimens to provide mechanical and creep properties of materials: A review, International Materials Reviews, 52(4), 213-255.
[https://doi.org/10.1179/174328007X160317]
- Sturm, R., Jenko, M., Ule, B., (2004), Accelerated creep tests of all-weldes metals, Materiali in Tehnologije, 38, 295-298.
-
Komazaki, S.-I., Sugimoto, T., Hasegawa, Y., Kohno, Y., (2007), Damage evaluation of a welded joint in a long-term service-exposed boiler by using a small punch creep test, ISIJ International, 47(8), 1228-1233.
[https://doi.org/10.2355/isijinternational.47.1228]
-
Kim, B., Lim, B., (2008), Local creep evaluation of P92 steel weldment by small punch creep test, Acta Mechanica Solida Sinica, 21(4), 312-317.
[https://doi.org/10.1007/s10338-008-0836-z]
- Podro, T. L. T. V., Bata, I. V. Z. U. M., (2006), Small-punch testing of a weld’s heat-affected zones, Materiali in Tehnologije, 40(2), 49-54.
-
Mankins, W., Hosier, J., Bassford, T., (1974), Microstructure and phase stability of Inconel alloy 617, Metallurgical and Materials Transactions B, 5, 2579-2590.
[https://doi.org/10.1007/BF02643879]
-
Totemeier, T., Tian, H., Clark, D., Simpson, J., (2005), Microstructure and strength characteristics of Alloy 617 welds, (Report No. INL/EXT-05-00488), Idaho National Lab.(INL), Idaho Falls, ID (United States).
[https://doi.org/10.2172/911266]
- Hosier, J., Tillack, D., (1972), INCONEL alloy 617: A new high-temperature alloy, Metals Eng. Quart, 12(3), 51-55.
-
Ren, W., Swimdeman, R., (2009), A review paper on aging effects in Alloy 617 for Gen IV Nuclear Reactor applications, Journal of Pressure Vessel Technology, 131(2), 024002.
[https://doi.org/10.1115/1.2967885]
- Böhler Welding, http://www.bohlerwelding.ru/files/cat/full_catalog.pdf
-
Naffakh, H., Shamanian, M., Ashrafizadeh, F., (2008), Weldability in dissimilar welds between Type 310 austenitic stainless steel and Alloy 657, Journal of Materials Science, 43, 5300-5304.
[https://doi.org/10.1007/s10853-008-2761-4]
-
Dehmolaei, R., Shamanian, M., Kermanpur, A., (2008), Microstructural characterization of dissimilar welds between alloy 800 and HP heat-resistant steel, Materials Characterization, 59(10), 1447-1454.
[https://doi.org/10.1016/j.matchar.2008.01.013]
- Lippold, J. C., Kotecki, D. J., (2005), Welding metallurgy and weldability of stainless steels, Wiley.
Professor in the Department of Mechanical Engineering, Osan University. His research interest is mechanical design and fracture mechanic.
E-mail: kultra@osan.ac.kr