
티타늄 소재 극저온 가공 시 극미량 윤활 조건에 따른 가공 특성 분석 연구

Copyright © The Korean Society for Precision Engineering
This is an Open-Access article distributed under the terms of the Creative Commons Attribution Non-Commercial License (http://creativecommons.org/licenses/by-nc/3.0) which permits unrestricted non-commercial use, distribution, and reproduction in any medium, provided the original work is properly cited.
Abstract
Titanium alloys are used in various industries due to their superior mechanical strength and corrosion resistance. However, titanium is classified as a difficult-to-machine material due to its low thermal conductivity that consequently causes poor tool life. In this study, cryogenic+MQL milling was performed to improve the machinability of Ti-6Al-4V; a cryogenic coolant and a minimum quantity fluid were sprayed simultaneously. The machinability was analyzed according to the cooling and lubrication conditions, focusing on the cutting force and tool wear. When the minimum quantity fluid was injected using two nozzles during cryogenic machining, the cutting force remained low despite the increase in machining distance due to the effective lubrication. The average cutting force at the long machining distances (82-86 passes) was 14.8% lower than that under the wet condition. The tool wear progressed without chipping, and the flank wear length was 55.5% lower than that of the wet machining because the cryogenic cooling and minimum quantity lubrication reduced the tool temperature, friction, and thermal shock.
Keywords:
Cryogenic machining, Minimum quantity lubrication, Milling, Titanium, Machinability키워드:
극저온 가공, 극미량 윤활, 밀링, 티타늄, 가공성1. 서론
티타늄 합금은 우수한 기계적 물성을 보유하고 있어 다양한 산업 분야에서 각광을 받고 있다. 해당 소재는 강도 대비 높은 중량 비율을 보유하고 있으며, 우수한 내식성을 가진 것으로 알려져 있다[1,2]. 반면 낮은 열전도도를 비롯한 취약한 열적 특성을 보유하고 있어 절삭 가공이 어려운 단점이 있다. 위 특성은 가공 중 발생된 열을 전단 영역에 집중시키며, 가공 온도 및 공구 온도를 증가시켜 공구 수명을 단축시킨다[3,4]. 티타늄 소재의 가공성을 향상시키기 위해 실험적 연구가 요구되며, 공구 수명을 향상시킬 수 있는 가공 환경 도출이 필수적이다.
일반적으로 가공성이 취약한 소재들은 난삭재로 분류된다. 앞선 연구를 통해 난삭재의 가공성 향상을 위한 가공 방법들이 제안되어 왔으며, 해당 방법에는 극저온 가공과 극미량 윤활(MQL) 가공이 포함된다. 극저온 가공이란 액체 질소와 같이 극저온을 가지는 절삭유를 공구에 분사하는 공정이다. 분사된 액체 질소는 가공 온도를 감소시켜, 가공성을 향상시키는 것으로 알려져 있다[5-11]. 티타늄 합금 소재 가공 시 액체질소를 분사하는 경우, 공구의 기계적 물성이 향상되며 공구 수명이 증가하는 것으로 보고된 바 있다[5,6]. 인코넬 및 탄탈륨 소재에 극저온 가공을 적용하는 경우에도 공구 수명이 향상됨이 확인되었다[9,10]. MQL 가공은 극미량의 유체를 절삭유로 적용하여 공구 표면 마찰 특성을 개선하는 공정이다. 분사된 유체는 공구 표면의 윤활 효과를 높이고 칩 배출을 원활하게 만들어, 절삭 가공 시 가공성을 향상시키는데 긍정적인 영향을 준다[12-15]. 앞선 연구를 통해 스틸 소재 가공 시 표면 조도를 감소시키고 공구 수명을 향상시키는 것으로 보고된 바 있다[14,15]. 일부 문헌에서는 극저온 액체 질소와 극미량 유체를 함께 분사하는 ‘극저온 MQL 가공’을 수행한 사례도 존재한다. 해당 공정은 공구 냉각과 함께 공구 표면 윤활이 동시에 이루어지므로, 공구 수명 향상에 효과적인 것으로 보고되고 있다[16,17]. 하지만 대다수의 연구가 짧은 가공 길이 또는 제한된 절삭유 분사 조건에서 수행되었으므로, 실험적 연구 성과가 미비한 상태이다. 극저온 MQL 가공은 공구 수명에 직접적인 영향을 주는 공정이므로, 긴 가공 길이를 바탕으로 가공량 변화에 따른 가공성을 지속적으로 분석할 필요가 있다. 또한, 두 종류의 절삭유가 미치는 영향을 상세히 분석할 필요가 있다.
본 연구에서는 티타늄 합금 소재에 대해 극저온 MQL 가공을 적용하였다. 밀링 가공을 수행하였으며, 절삭유 분사 및 윤활 조건별 가공 길이에 따른 절삭 부하의 변화 특성을 분석하였다. 또한 긴 길이 가공 후 공구 상태를 측정하였으며, 이를 바탕으로 티타늄 가공 시 절삭유의 영향을 규명하였다.
2. 절삭유 분사 메커니즘
극저온 MQL 가공의 절삭유 분사 메커니즘은 적용된 두 절삭유의 분사 방법에 따라 결정된다. 극저온 절삭유는 총 3가지의 방법으로 분사되며, 이에는 외부 분사(External), 내부 분사(Internal), 간접 분사(Indirect)가 포함된다[18]. 각 분사 방법은 절삭유의 영향부가 다르게 나타나며, 관련 모식도는 Fig. 1에 나타난 바와 같다. External은 외부 노즐을 통해 절삭유를 공구에 분사하는 방법이다. 공구로부터 일정한 거리를 두고 절삭유가 분사되므로, 영향부가 가장 넓다. 절삭유의 공구 접촉이 주목적이지만, 가공 소재에 함께 접촉하게 되어 소재 냉각을 유발한다. Internal은 내부 유로를 포함하는 스핀들 및 공구 홀더를 적용한다. 내부 유로를 따라 공구 근처까지 도달한 절삭유는 분사구를 통해 외부로 분출되며 공구 끝단을 향해 분사된다. 외부 노즐에 비해 분사구와 공구 사이 거리가 짧아, 영향부가 좁으며, 소재 냉각의 정도가 작다. Indirect는 공구 내 유로를 통해 절삭유가 공구 내부를 순환하고 외부로 분사되도록 하는 방법이다. 공구에 직접 분사되지는 않지만, 내부 순환 과정을 통해 공구를 충분히 냉각시킬 수 있으며, 가공부가 아닌 외부로 분사되므로 소재 접촉이 없다. 절삭 가공 시 소재의 온도 감소는 가공 부하 증가를 초래할 수 있다[19]. 따라서 극저온 절삭유의 소재 접촉이 적을수록 가공성이 향상될 가능성이 높으며, 앞선 연구를 통해 Indirect 방법의 적용 시 우수한 가공성이 나타남이 검증된 바 있다[20].
MQL 가공은 극미량의 유체를 절삭 공구 표면에 국부적으로 분사하는 공정이다. 미스트 형태의 유체를 공구와 소재 사이에 고압으로 분사하며, 공구 표면 윤활에 효과적이다[13]. 분사된 유체의 영향은 적절한 공구 표면 유입 및 마찰 특성 개선으로 나타난다. 감소된 표면 마찰 계수는 마찰열 감소 및 원활한 칩 배출을 가능케 한다. 기존 문헌에서 스틸 소재 MQL 터닝 가공 시, 위 효과로 인해 공구 마모가 감소함이 확인되었다[21].
가공성은 가공 부하와 공구 수명에 의해 크게 좌우되며, 가공 부하 감소 및 공구 수명 향상을 위해 적절한 윤활 및 가공열 감소가 필수적이다. 극저온 가공의 경우 Indirect 방법을 적용할 시, 절삭유의 소재 접촉을 최소화를 통해 가공열 감소 효율을 유지하며 가공 부하 증가를 방지할 수 있다. MQL 가공의 경우 공구와 소재 접촉 시 극미량 유체가 공구 표면에 지속적으로 위치하고 있을수록, 마찰을 최소화하여 가공 부하 및 마찰열 감소에 긍정적인 영향을 줄 수 있다. Indirect 방법은 타 분사 방법과 달리 극저온 절삭유가 공구 표면을 흐르지 않으므로, 극미량 유체가 공구 표면에서 벗어날 가능성이 적다. 따라서 두 공정을 함께 적용하는 경우 가공성 향상에 큰 영향을 줄 수 있다. 해당 내용은 기존 문헌에서 확인된 바 있으며, Indirect 액체질소 분사 및 극미량 유체 적용 극저온 MQL 가공 시 공구 수명이 큰 폭으로 증가함이 보고되었다[18].
3. 실험 환경
본 연구에서는 티타늄 합금 소재에 대해 Indirect 방법 기반의 극저온 MQL 가공 실험을 수행하였다. 대표적인 합금인 Ti-6Al-4V 재료가 100 × 100 × 100 mm3 블록 형태의 시편으로 적용되었으며, 자체 제작된 장비(HTC-1000, ㈜한국정밀)을 활용하여 다운 밀링을 진행하였다. 가공 장비는 외부에 위치한 극저온 절삭유가 장비 주축을 관통하여 일정한 압력으로 공구 끝단에 분사되도록 구축되었으며, 절삭유로는 액체 질소가 적용되었다. Indirect 방법 적용을 위해 상용 공구(F1200, Walter) 내부에 유로를 형성하였으며, 내부 순환한 액체 질소가 외부로 분사되도록 분사 구멍을 만들었다. 제작된 공구는 Fig. 2에서 확인 가능하다. MQL 분사는 외부 노즐을 적용하여 수행되었다. 베지터블 오일 기반의 극미량 유체가 사용되었으며, 외부 노즐은 공구 표면을 향하도록 설정되었다. 액체 질소와 극미량 유체는 각각 4 bar와 7 bar의 고정 압력으로 분사되었으며, 실험 환경은 Fig. 3과 같다.
극저온 가공 시 윤활 정도에 따른 가공성 분석을 위해 두 종류의 극미량 유체 분사량이 적용되었다. 분사량은 외부 노즐 개수로 조절되었으며, 1개 노즐과 2개 노즐 조건에서 각각 실험이 수행되었다. 분사 환경에 따른 영향을 비교하기 위해 습식 환경에서 추가 실험을 수행하였으며, 실험 조건은 Table 1에서 확인 가능하다. 빠른 가공 속도(90 m/min) 및 긴 가공 길이가 모든 절삭유 분사 환경에 적용되었다. 한 패스의 가공 길이를 100 mm로 정의할 때, 총 86 패스의 길이가 적용되었고, 분석 대상으로 절삭 부하와 공구 마모가 측정되었다. 절삭 부하의 경우 시편에 부착된 공구동력계(9139AA, Kistler)를 기반으로 측정되었으며, 가공 길이별 부하 변화를 분석하였다. 공구 마모의 경우 현미경(Leica Z16APO)을 활용하여 플랭크 면을 기준으로 측정되었으며, 동 가공 길이 조건에서 절삭유 분사 환경에 따른 마모 길이 차이를 분석하였다.
4. 실험 결과 및 분석
4.1 절삭 부하 분석
1개 및 2개의 극미량 유체 분사 노즐 적용 극저온 MQL 가공과 습식 가공 조건에서 가공 길이에 따른 절삭 부하를 측정하였으며, 비교 분석 연구를 수행하였다. 큰 절삭 부하는 가공 온도증가, 소재 표면 품질 악화, 공구 수명 감소를 초래할 수 있다. 절삭 부하의 증가는 가공 응력 및 에너지의 증가를 의미하며, 가공부에서 발생하는 열의 증가를 야기한다. 절삭 부하가 클수록 공구의 진동이 커지며, 소재 표면의 표면 조도가 증가하게 된다. 앞선 현상들이 공구에 가해지는 충격을 증가시켜, 공구 마모 진전을 가속화한다. 이를 고려하여, 가공성에 큰 영향을 주는 최대 절삭 부하를 기준으로 연구가 수행되었다. 다운 밀링의 경우 공구의 소재 진입 시 넓은 면적을 가공하게 되며, 공구 회전에 따라 가공 면적이 감소하게 된다. 가공 면적은 절삭 부하에 직접적인 영향을 주는 변수이며, 최대 가공 면적 환경에서 최대 절삭 부하가 나타난다. 따라서 공구의 소재 진입 시 발생되는 절삭 부하를 기준으로 연구가 수행되었다. 공구동력계를 통해 x, y, z 방향의 부하를 측정하고, 합력을 도출하였다. 이후, 합력에 대해 RMS 데이터 처리를 통해 실험 데이터를 확보하였다. 가공 길이 별 실험 결과는 Fig. 4에 나타난 바와 같다. 분사 조건에 따른 가공 길이 영향을 파악하기 위해, 짧은 가공 길이(1-5 패스)와 긴 가공 길이(82-86 패스) 조건에서의 절삭 부하 평균값들을 비교 분석하였으며, 분석 결과는 Fig. 5에서 확인 가능하다.
일반적으로 건식 티타늄 가공의 경우 재료 물성의 영향으로 인해 공구 온도가 큰 폭으로 상승하고, 소재에 진입한 공구가 빠져나옴에 따라 온도가 감소한다. 해당 과정에서 절삭유가 분사되는 경우 윤활 및 냉각 효과로 인해 공구 온도의 변화 추이가 달라지게 된다. 적용된 절삭유의 윤활 효과가 클수록 공구와 칩 사이의 마찰이 감소하여 온도 증가 정도가 감소할 수 있다. 해당 현상으로 인해 습식 조건에 비해 MQL 분사 조건에서 공구 온도 상승 폭이 작을 것으로 사료된다. 또한 절삭유의 온도가 낮을수록 가공 전 공구의 온도가 낮을 수 있으며, 가공 후 상승된 공구 온도의 감소 속도가 빠를 수 있다. 이로 인해 습식 조건에 비해 액체 질소 분사 조건에서 공구의 초기 온도가 낮을 것으로 판단되며, 가공 시 상승했던 공구 온도가 급속도로 감소할 것으로 판단된다. 관련 내용은 Fig. 6에서 도식화되었으며, 이는 절삭 부하 측정 실험 결과를 뒷받침할 수 있다.
절삭 부하 측정 결과, 습식 조건의 경우 가공 길이가 증가함에 따라 절삭 부하가 증가하는 경향을 보였다. 가공량의 증가는 지속적인 열 발생과 함께 공구에 데미지를 가한다. 분사된 절삭유가 가공열을 일부 감소시키지만, 티타늄 합금의 취약한 열적 특성으로 인해 높은 가공 온도가 나타날 수 있으며, 공구 마모가 진전될 수 있다. 이로 인한 공구의 형상 변화는 절삭 부하를 증가시킬 수 있으며, 해당 영향으로 인해 위 현상이 나타난 것으로 판단된다. 반면, 2개의 노즐을 활용한 극저온 MQL 가공의 경우 가공 길이가 증가함에도 불구하고 절삭 부하 크기가 유지되었다. 일반적으로 가공 온도가 감소하면, 절삭 가공 시 전단 영역에서 큰 응력이 발생하게 된다. 따라서 액체 질소만 분사될 시 절삭 부하가 증가할 수 있다. 이와 반대로, 공구 표면의 적절한 윤활은 부하 감소를 야기할 수 있다. 윤활에 의한 표면 마찰 계수 감소가 마찰 부하 및 절삭 부하를 감소시키게 된다. 해당 조건에서는 액체 질소와 극미량 유체가 함께 분사되었다. 액체 질소가 공구를 냉각시킴으로써 가공열을 감소시키고, 충분한 유량의 유체가 적절한 윤활 환경을 마련함에 따라 마찰열을 감소시킨다. 이에 따라 낮은 공구 온도로 인해 공구 마모 진전이 늦춰지게 되어 위와 같은 현상이 나타난 것으로 보인다. 따라서 타 조건에 비해 작은 절삭 부하가 확인되었으며, 82 패스 이상의 긴 가공 길이에서 습식 조건과 비교하였을 때, 14.8% 작은 절삭 부하가 측정되었다. 하지만 1개의 노즐을 활용한 극저온 MQL 조건에서는 절삭 부하가 타 조건들보다 빠르게 증가하는 경향을 보였다. 노즐의 개수는 유체의 유량을 의미한다. 1개 노즐 조건의 경우 2개 노즐 조건에 비해 절반 수준의 유량을 가지게 된다. 따라서 불충분한 윤활 환경이 가공 부하를 충분히 감소시키지 못한 것으로 사료된다. 또한, 위 윤활 환경이 2개 노즐 적용 조건에 비해 큰 마찰열 및 공구 온도 상승을 유발하여 빠른 공구 마모 진전과 가공 부하 증가를 발생시킨 것으로 판단된다. 추가적으로 액체 질소가 급작스러운 공구 온도 감소를 유발할 수 있으므로, 공구의 파손 및 공구 마모 진전을 가속화할 수 있다. 액체 질소의 온도가 일반 절삭유보다 낮으므로, 습식 조건보다 빠른 절삭 부하 증가를 보인 것으로 사료된다. 위 결과를 고려할 때, 극저온 가공 시 절삭 부하 감소를 위해 충분한 윤활이 필수적인 것으로 판단되며, 2개 노즐 적용 극저온 MQL 조건이 절삭 부하 기준 최적인 것으로 사료된다.
4.2 공구 마모 분석
제시된 모든 조건에서 특정 길이를 가공한 공구에 대해 마모 분석이 수행되었다. 냉각 및 윤활 환경의 가공성에 대한 영향을 명확히 분석하기 위해 86 패스에 해당하는 긴 가공 길이를 적용하였으며, 플랭크 면을 기준으로 발생된 마모의 종류를 분석하였다. 관련 내용은 Fig. 7에서 확인 가능하다. 분석 결과 모든 조건에서 플랭크 마모가 발생되었다. 지속적인 가공 진행으로 인해 공구에 가해지는 응력 및 열이 영향을 준 것으로 판단된다. 또한, 습식 및 1개 노즐 적용 극저온 MQL 가공 조건에서는 치핑 현상이 발견되었다. 치핑이란 공구가 깨지는 현상을 의미하며 급작스러운 충격, 열 변화 등이 나타났을 때 발생될 수 있다. 절삭 가공의 경우 공구의 소재 접촉 시 소재가 소성 변형되면서 전단영역에서 큰 열이 일차적으로 발생된다. 이후 소성 변형된 소재가 공구 표면을 지나며 마찰열이 발생된다. 두 차례 과정으로 상승한 공구 온도가 절삭유에 의해 급격히 감소하게 되고, 해당 온도 변화가 공구에 열 충격을 가한 것으로 사료된다. 반면, 2개 노즐 적용 극저온 MQL 가공 조건에서는 치핑 현상이 발견되지 않았다. 2개 노즐을 활용한 분사는 충분한 유량의 유체를 공구 표면에 위치 시킬 수 있다. 이는 공구 표면 마찰 계수를 낮출 수 있으며, 마찰열 감소를 야기할 수 있다. 마찰에 의한 열이 감소하므로, 타 냉각 조건과 달리 공구의 초기 상승 온도가 감소하게 된다. 따라서, 내부 순환된 액체 질소에 의한 온도 감소 폭이 줄어들어, 열 충격 효과가 감소한 것으로 판단된다. 관련된 사항은 Fig. 6에서도 확인 가능하다.
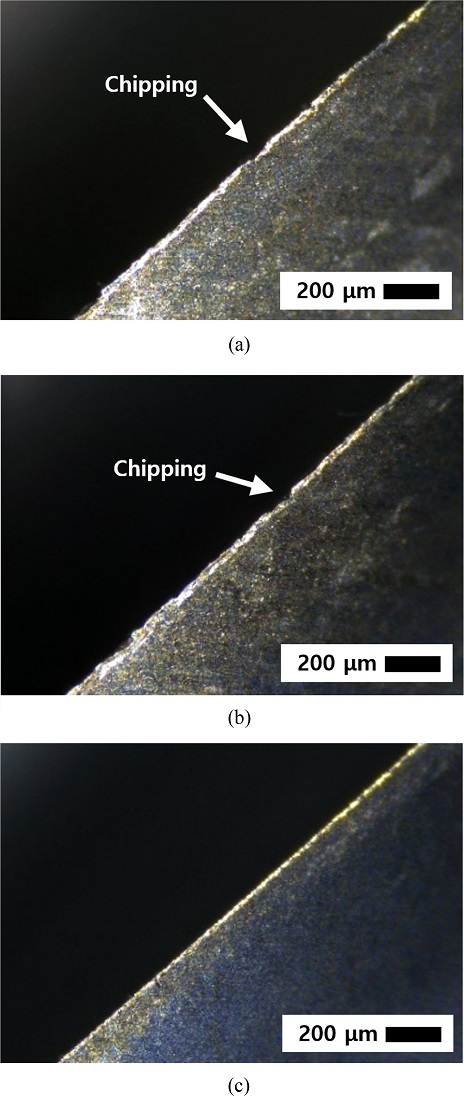
Flank faces of cutting tools at the machining distance of 86 passes under (a) wet, (b) cryogenic+MQL with 1 nozzle, and (c) cryogenic+MQL with 2 nozzle conditions
추가적으로 플랭크 마모 길이가 측정되었다. 측정 결과 습식, 1개 노즐 적용 극저온 MQL, 2개 노즐 적용 극저온 MQL 조건에 대해 각각 45, 55, 20 μm의 마모 길이가 나타났다. 2개 노즐을 적용한 극저온 MQL 조건에서 최소값이 측정되었으며, 습식 조건에 비해 55.5% 적은 수준을 보였다. 열 충격이 줄어든 조건에서 공구 온도가 감소되었기 때문에, 해당 결과가 나타난 것으로 판단된다. 위 경향은 가공 길이에 따른 절삭 부하의 증가 경향과 유사하게 나타났다. 공구 마모가 클수록 절삭 부하가 빠르게 증가하였으며, 마모 진전으로 인한 공구 형상 변화가 해당 현상을 초래한 것으로 보인다. 위 결과로 미루어 볼 때, 극저온 밀링 가공에서 공구 수명 향상 시 MQL 조건 적용이 효과적인 것으로 판단되며, 충분한 양의 유체를 분사할수록 가공성 개선 효과가 커지는 것으로 사료된다.
5. 결론
본 연구에서는 티타늄 합금 소재에 대해 극저온 MQL 가공을 진행하였으며, 실험 결과를 토대로 가공성 분석을 수행하였다. 상세한 내용은 하단에 나타난 바와 같다.
(1) 극저온 MQL 가공 시 2개의 극미량 유체 분사 노즐을 적용한 경우 적절한 윤활 환경 조성 및 공구 냉각으로 인해 공구 온도가 낮게 유지됨에 따라 가공 길이의 증가에도 불구하고 절삭 부하가 유지되었다. 긴 가공 길이 조건에서 습식에 비해 14.8% 낮은 수준의 부하 값을 보였다.
(2) 습식 및 1개 노즐 극저온 MQL 조건에서 86 패스 가공의 경우 상승한 공구 온도가 큰 폭으로 감소함에 따라 열 충격에 의해 공구 치핑 현상이 발생했다. 반면, 2개 노즐 극저온 MQL 가공 시에는 온도 증가 및 감소 폭이 작으므로 해당 현상이 나타나지 않았다.
(3) 2개 노즐 극저온 MQL 조건에서 최소의 플랭크 마모 길이가 측정되었으며, 해당 값은 습식 조건 대비 55.5% 감소된 수준을 보였다.
(4) 2개 노즐 적용 극저온 MQL 가공 시 적은 절삭 부하와 공구 마모는 적절한 공구 냉각 및 윤활에 의한 것으로 판단되며, 티타늄 밀링 가공 시 다량의 MQL 분사를 동반한 극저온 조건이 가공성 향상에 적합한 것으로 사료된다.
Acknowledgments
본 연구는 정부(산업통상자원부)의 재원으로 한국에너지기술평가원(20206310200010, 국산 CNC 기반 산업기계 재제조 스펙업 및 보급·확산 기반 조성) 및 한국산업기술진흥원(P0015354, 난삭재 고난도 형상 가공 및 제어 기술 개발)의 지원을 받아 수행됨.
REFERENCES
-
Castellani, C., Lindtner, R. A., Hausbrandt, P., Tschegg, E., Stanzl-Tschegg, S. E., Zanoni, G., Beck, S., Weinberg, A.-M., (2011), Bone-implant interface strength and osseointegration: Biodegradable magnesium alloy versus standard titanium control, Acta Biomaterialia, 7(1), 432-440.
[https://doi.org/10.1016/j.actbio.2010.08.020]
-
Lee, H.-H., Lee, S., Park, J.-K., Yang, M., (2018), Friction and wear characteristics of surface-modified titanium alloy for metal-on-metal hip joint bearing, International Journal of Precision Engineering and Manufacturing, 19(6), 917-924.
[https://doi.org/10.1007/s12541-018-0108-x]
-
Li, N., Chen, Y.-J., Kong, D.-D., (2018), Wear mechanism analysis and its effects on the cutting performance of PCBN inserts during turning of hardened 42CrMo, International Journal of Precision Engineering and Manufacturing, 19(9), 1355-1368.
[https://doi.org/10.1007/s12541-018-0160-6]
-
Choudhury, S., Bartarya, G., (2003), Role of temperature and surface finish in predicting tool wear using neural network and design of experiments, International Journal of Machine Tools and Manufacture, 43(7), 747-753.
[https://doi.org/10.1016/S0890-6955(02)00166-9]
-
Hong, S. Y., Markus, I., Jeong, W.-C., (2001), New cooling approach and tool life improvement in cryogenic machining of titanium alloy Ti-6Al-4V, International Journal of Machine Tools and Manufacture, 41(15), 2245-2260.
[https://doi.org/10.1016/S0890-6955(01)00041-4]
-
Hong, S. Y., Ding, Y., Jeong, W.-C., (2001), Friction and cutting forces in cryogenic machining of Ti-6Al-4V, International Journal of Machine Tools and Manufacture, 41(15), 2271-2285.
[https://doi.org/10.1016/S0890-6955(01)00029-3]
-
Dhar, N., Paul, S., Chattopadhyay, A., (2001), The influence of cryogenic cooling on tool wear, dimensional accuracy and surface finish in turning AISI 1040 and E4340C steels, Wear, 249(10-11), 932-942.
[https://doi.org/10.1016/S0043-1648(01)00825-0]
-
Dhar, N., Kamruzzaman, M., (2007), Cutting temperature, tool wear, surface roughness and dimensional deviation in turning AISI-4037 steel under cryogenic condition, International Journal of Machine Tools and Manufacture, 47(5), 754-759.
[https://doi.org/10.1016/j.ijmachtools.2006.09.018]
-
Wang, Z., Rajurkar, K., (2000), Cryogenic machining of hard-to-cut materials, Wear, 239(2), 168-175.
[https://doi.org/10.1016/S0043-1648(99)00361-0]
-
Wang, Z., Rajurkar, K., Fan, J., Petrescu, G., (2002), Cryogenic machining of tantalum, Journal of Manufacturing Processes, 4(2), 122-127.
[https://doi.org/10.1016/S1526-6125(02)70138-2]
-
Bertolini, R., Lizzul, L., Pezzato, L., Ghiotti, A., Bruschi, S., (2019), Improving surface integrity and corrosion resistance of additive manufactured Ti6Al4V alloy by cryogenic machining, The International Journal of Advanced Manufacturing Technology, 104, 2839-2850.
[https://doi.org/10.1007/s00170-019-04180-5]
-
Sidik, N. A. C., Samion, S., Ghaderian, J., Yazid, M. N. A. W. M., (2017), Recent progress on the application of nanofluids in minimum quantity lubrication machining: A review, International Journal of Heat and Mass Transfer, 108, 79-89.
[https://doi.org/10.1016/j.ijheatmasstransfer.2016.11.105]
-
Roy, S., Kumar, R., Sahoo, A. K., Das, R. K., (2019), A brief review on effects of conventional and nano particle based machining fluid on machining performance of minimum quantity lubrication machining, Materials Today: Proceedings, 18, 5421-5431.
[https://doi.org/10.1016/j.matpr.2019.07.571]
-
Padmini, R., Krishna, P. V., Rao, G. K. M., (2016), Effectiveness of vegetable oil based nanofluids as potential cutting fluids in turning AISI 1040 steel, Tribology International, 94, 490-501.
[https://doi.org/10.1016/j.triboint.2015.10.006]
-
Uysal, A., Demiren, F., Altan, E., (2015), Applying minimum quantity lubrication (MQL) method on milling of martensitic stainless steel by using nano MoS2 reinforced vegetable cutting fluid, Procedia-Social and Behavioral Sciences, 195, 2742-2747.
[https://doi.org/10.1016/j.sbspro.2015.06.384]
-
Park, K.-H., Yang, G.-D., Suhaimi, M., Lee, D. Y., Kim, T.-G., Kim, D.-W., Lee, S.-W., (2015), The effect of cryogenic cooling and minimum quantity lubrication on end milling of titanium alloy Ti-6Al-4V, Journal of Mechanical Science and Technology, 29, 5121-5126.
[https://doi.org/10.1007/s12206-015-1110-1]
-
Pereira, O., Rodríguez, A., Fernández-Abia, A., Barreiro, J., de Lacalle, L. L., (2016), Cryogenic and minimum quantity lubrication for an eco-efficiency turning of AISI 304, Journal of Cleaner Production, 139, 440-449.
[https://doi.org/10.1016/j.jclepro.2016.08.030]
-
Suhaimi, M. A., Yang, G.-D., Park, K.-H., Hisam, M. J., Sharif, S., Kim, D.-W., (2018), Effect of cryogenic machining for titanium alloy based on indirect, internal and external spray system, Procedia Manufacturing, 17, 158-165.
[https://doi.org/10.1016/j.promfg.2018.10.031]
-
Kim, J., Kim, D. Y., (2022), Study on the machinability of cryogenic milling for compacted graphite iron, Journal of the Korean Society for Precision Engineering, 39(1), 13-19.
[https://doi.org/10.7736/JKSPE.021.080]
-
Bogajo, I. R., Tangpronprasert, P., Virulsri, C., Keeratihattayakorn, S., Arrazola, P. J., (2020), A novel indirect cryogenic cooling system for improving surface finish and reducing cutting forces when turning ASTM F-1537 cobalt-chromium alloys, The International Journal of Advanced Manufacturing Technology, 111, 1971-1989.
[https://doi.org/10.1007/s00170-020-06193-x]
-
Sayuti, M., Sarhan, A. A., Salem, F., (2014), Novel uses of SiO2 nano-lubrication system in hard turning process of hardened steel AISI4140 for less tool wear, surface roughness and oil consumption, Journal of Cleaner Production, 67, 265-276.
[https://doi.org/10.1016/j.jclepro.2013.12.052]
Senior Researcher in Korea Institute of Industrial Technology. His research interest in aerospace manufacturing process.
E-mail: dkim0707@kitech.re.kr
Deputy General Manager in Nakwon Co., Ltd.. His research interest in machining technology for difficult-to-cut materials.
E-mail: hungbum@nakwon21.com
CEO in Nakwon Co., Ltd. and Nakwon T&A Co., Ltd..
E-mail: kbg1341@nakwon21.com
Senior Researcher in Korea Institute of Industrial Technology. His research interest in machine tool metrology and aerospace manufacturing system.
E-mail: hhlee84@kitech.re.kr
Principal Researcher in Korea Institute of Industrial Technology. His research interest in aerospace material fabrication.
E-mail: h69231@kitech.re.kr
Senior Research Engineer of Commercial Aircraft Design Team in Korea Aerospace Industries, Co., Ltd..
E-mail: kihyukkim@koreaaero.com
Principal Research Engineer of Commercial Aircraft Design Team in Korea Aerospace Industries, Co., Ltd..
E-mail: mc2mc2@koreaaero.com
Assistant Professor in the School of Mechanical Engineering, Kyungnam University. His research interest is machining.
E-mail: doyoungk@kyungnam.ac.kr