
수학적 필터링 기반 TPMS 열교환기 유동 특성 개선 연구

Copyright © The Korean Society for Precision Engineering
This is an Open-Access article distributed under the terms of the Creative Commons Attribution Non-Commercial License (http://creativecommons.org/licenses/by-nc/3.0) which permits unrestricted non-commercial use, distribution, and reproduction in any medium, provided the original work is properly cited.
This paper was presented at KSPE Autumn Conference in 2023
Abstract
Recent advancements in additive manufacturing (AM) have made it possible to create compact heat exchangers (HXs) with complex geometries. This study introduces a new approach that uses Triply Periodic Minimal Surface (TPMS)-based designs for HXs. Mathematical filtering techniques are incorporated to optimize the local morphology changes. The goal of the proposed mathematical filtering method is to improve the flow characteristics and heat exchange capability of TPMS HXs by modifying the structure's morphology at the inlet and outlet regions. This modification facilitates flow selection and reduces pressure drop. The HX design includes cylindrical flow domains at the inlet and outlet regions. Three different HX designs with varying inlet/outlet domains (through-hole, half-hole, and taper-hole) were fabricated using polymer AM and DLP 3D printing. These designs were then tested for pressure drop. Among the three designs, the taper-hole configuration showed the best flow characteristics, with a 50% reduction in pressure drop compared to previous studies. The taper-hole design was then replicated using metal AM technology, resulting in a 70-125% improvement in heat exchange capacity compared to previous studies.
Keywords:
Triply period minimal surface, Heat exchanger, Mathematical filtering, Additive manufacturing, Computational fluid dynamics키워드:
삼중주기적 최소곡면, 열교환기, 수학적 필터링, 적층 제조, 전산 유체 해석1. 서론
열교환기(Heat Exchanger, HX)는 서로 다른 온도의 2개 이상의 유체 간에 열에너지를 교환하기 위한 목적으로 사용되는 열전달 장치이다. 열교환기는 전자, 자동차 및 전력 시스템을 포함하는 다양한 산업 분야에서 열에너지 관리에 중요한 역할을 한다. 고집적(Compact) 열교환기는 면적 대 부피 비율(Area Density)이 높은 열교환기를 의미하는데, 액체 간의 열교환의 경우 200-400 m2/m3의 전열 면적 비율을 갖는 것으로 알려져 있다[1,2]. 고집적 열교환기는 단위 부피당 열교환 능력이 높은 장점이 있으며, 판형(Plate Type)[3], 판형-핀[4] 및 회로[5] 유형을 포함하여 낮은 유동 저항으로 열교환 능력을 향상시키기 위해 다양한 고집적 열교환기가 제안되었다[6]. 판형 고집적 열교환기는 일반적으로 다수의 미세 요철부를 포함하는 금속 박판을 적층하고 결합해서 제조하며, 이는 여러 단계의 제조 및 조립 공정을 필요로 한다[7].
최근 적층 제조(Additive Manufacture) 기술을 활용하여 고집적 열교환기를 개발하기 위한 연구가 수행되고 있다. 적층 제조는 2차원 단면을 적층하여 원하는 3차원 형상을 제조하는 방법으로 기존 기계가공으로 제조가 어려운 복잡한 형상을 제작할 수 있다[8]. 최근 적층 제조의 높은 설계 자유도를 활용하여 설계 최적화 및 맞춤형 부품생산에 널리 적용되고 있으며[9-11], 복잡한 열-유체 응용 부품의 설계 및 제작에 사용되고 있다[12]. 적층 제조를 통해 제작된 부품은 일체형으로 제작되기 때문에 향상된 열전달 능력을 제공하는 새로운 열교환기를 설계하기 위한 목적으로 사용되고 있다[13-15]. 또한 적층 제조를 사용하여 미세 반복(Micro-cellular) 구조의 용이한 제작이 가능하며[16-18], 다양한 미세 반복 구조를 적용하여 열교환기의 효율을 향상시키기 위한 목적으로 활용되고 있다[19].
상기 미세 반복 구조 중에서 삼중 주기 최소 곡면(Triply Periodic Minimal Surface, TPMS) 구조가 열교환기를 개발하기 위한 목적으로 널리 활용되고 있다[20-22]. TPMS 구조는 3차원 공간을 두 개의 연속적인 공간으로 구분할 수 있어 고온-저온 유체가 분리된 공간에서 열교환에 유리한 장점이 있다. 또한 설계 공간에 따라 단위 셀의 특성을 변화시킬 수 있어 열교환기의 기능성을 제고하기 위한 설계가 가능하다[23]. TPMS는 삼각함수 수식을 기반으로 3차원으로 특정 주기를 가지며 동일한 구조가 무한히 확장되는 미세 반복 구조이며[24], 삼각함수의 조합에 따라 Primitive, Gyroid, Diamond 등 다양한 단위 셀(Unit Cell)의 반복 구조로 표현된다[25]. TPMS 곡면은 평균 곡률을 0으로 유지하여 채널 내부에서 적은 압력 손실로 유체의 유동이가능하며, 이러한 장점으로 인해 유체 혼합기(Fluid Mixer)[26], 방열부품(Heat Sink)[27], 금형 냉각 모듈[28]을 포함한 다양한 열-유체 응용 분야에 사용되어 왔다.
본 연구는 TPMS 열교환기의 유동 특성 및 열교환 성능을 제고하기 위해 수학적 필터링(Mathematical Filtering) 기반 TPMS 설계안을 제시하였다. TPMS 구조의 수학적 필터링 기법은 복잡한 TPMS 구조의 국부적 형상 변화를 위한 방법으로 유동 채널의 유동 특성 개선[29], 열교환기의 유동 선별 기능 부여[30] 등의 목적으로 본 연구자의 선행 연구로 수행되었다. 본 연구에서는 TPMS 열교환기 입출구 영역에의 유동 선별 및 압력강하 저감을 목적으로 다양한 형태의 TPMS 열교환기 입출구 설계를 위한 수학적 필터링 기법을 제안하였다. 특히 수직으로 주입되는 유동 특성을 고려하여 유체가 열교환기 내부로 빠르게 주입되도록 TPMS 열교환기 입출구 하단에 원통형 유동 선별 영역을 설계하였다. 상기 열교환기 설계안의 유동 특성을 전산 유체해석을 통해 고찰하였고, 적층 제조를 통해 시제품을 제작하여 실험적으로 검증하였다.
본 논문은 다음과 같은 순서로 구성된다. 2장에서 TPMS의 수학적 수식을 기반으로 원통형 입출구 영역에서의 유동 선별이 가능한 필터링 함수를 수식화하여 TPMS 열교환기 내부로 주입될 때 유동 저항을 줄일 수 있는 3가지의 설계안을 제시하였다. 3장에서 실험과 전산 유체 해석을 통해 압력강하와 내부 유체 거동을 비교하여 설계안을 선정하였다. 4장에서는 금속 적층 제조를 사용하여 TPMS 열교환기를 제작하고, 열교환 실험을 통해 본 연구에서 제시된 열교환기의 성능을 검증하였다.
2. TPMS 열교환기 설계
2.1 TPMS열교환기 설계 개요
Fig. 1(a)에 TPMS 열교환기의 모식도를 도시하였다. TPMS 열교환기는 본 연구자의 선행 연구를 기반으로 판형 열교환기를 기초로 설계하였으며, 내부 TPMS 영역의 크기는 98 × 60 × 44 mm이다. 열교환기 상측에 각각 2개의 입/출구가 교차하여 위치하도록 설계하였으며, 각 입출구의 내경은 12 mm로 설계하였다.
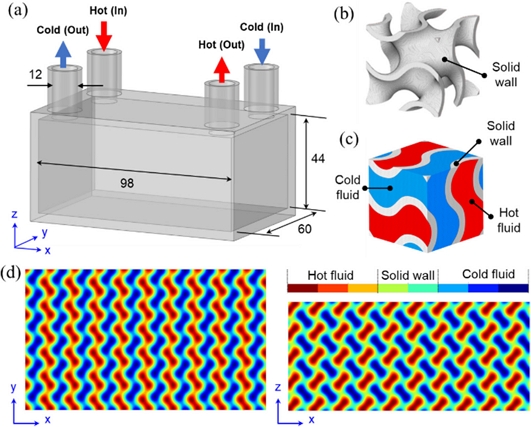
Description of TPMS heat exchanger (HX): (a) design configuration (unit: mm), (b) gyroid unit cell, (c) gyroid unit cell with colored fluids, and (d) signed distance fields (SDF) for the top view (XY-plane) and side view (XZ-plane)
본 연구의 Gyroid 형태의 TPMS 수식을 사용하여 열교환기를 설계하였다. 식(1)에 Gyroid형태 TPMS 곡면의 음함수 수식을 도시하였으며, 이를 기반으로 식(2)와 같이 레벨 셋(Level-set) 수식화를 통해 TPMS 내벽(Solid Wall)을 정의할 수 있다.
(1) |
(2) |
여기서 양수 C는 레벨 셋 상수(Level-set Constant)로 TPMS 내벽의 두께와 비례한다. 즉 Gyroid 함수의 절대값이 C보다 작은 영역이 TPMS 내벽에 해당되며, Fig. 1(b)에 C를 0.235로 설정한 경우 내벽 두께 0.5 mm로 형성된 Gyroid 구조물을 도시하였다. 반면 함숫값이 C 이상일 경우 고온의 유체 영역, -C 이하일 경우 저온의 유체 영역에 해당되며, Fig. 1(c)에 고온/저온 유체영역을 각각 적색과 청색으로 표시하여 도시하였다.
상기 레벨 셋 구분은 부호거리장(Signed Distance Field, SDF)을 통해 표현될 수 있다. Fig. 1(d)에 단위 셀 크기를 10 mm로 설정한 경우 TPMS 열교환기 내부의 부호거리장 분포도를 도시하였다. 여기서 녹색 영역이 TPMS 내벽을 의미하며, 적색 영역과 청색 영역이 각각 고온 유체와 저온 유체 영역을 의미한다.
2.2 입출구 유동선별을 위한 수학적 필터링
상기 TPMS 구조는 내벽을 경계로 고온유체 채널과 저온유체 채널이 번갈아가며 배열되는 형태를 갖는다. 따라서 입출구에서 고온/저온 유체를 해당 채널로만 선택적으로 분배하기 위해 Fig. 2(a)에 도시한 바와 같이 마스킹(Masking) 영역을 인위적으로 생성하는 방법이 일반적으로 사용된다[28]. 그러나 상기 방법은 채널 단면적의 국부적인 감소를 야기하여 유동저항이 증가하고 결과적으로 입출구에서의 압력강하가 급증하게 된다[30].
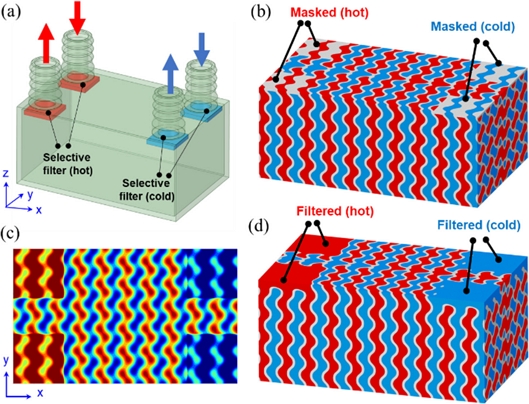
Mathematical filtering of a TPMS HX for fluid selection: (a) definition of the filtering domain (b) masked model for fluid selection, (c) SDF distribution for selection filtering, and (d) filtered model for fluid selection
이러한 문제점을 극복하기 위해 본 연구자의 선행연구에서 수학적 필터링 기법을 적용하여 입출구 영역에 대해 국부적으로 부호거리장을 수정하는 방법을 제안하였다. 수학적 필터링 기법은 식(3)과 같이 TPMS 음함수에 특정 영역에서만 유효만 값을 가지는 필터링 함수(Filtering Function)를 더하여 부호거리장을 변화시키는 방법이다[29].
(3) |
여기서 필터링 함수 F(x, y, z)는 Fig. 2(b)에 도시한 4개의 필터링 영역에 대해 전체적으로 양수 혹은 음수 영역으로 만들어 고온/저온 유체만 포함될 수 있도록 정의하였다. 이를 위해 3차원 공간에서의 필터링 함수는 시그모이드 함수(Sigmoid Function)를 기반으로 식(4)와 같이 정의된다.
(4) |
여기서 xp, yp, zp는 필터링 영역의 좌표이며, kx, ky, kz는 방향별 시그모이드 계수를 의미한다. b는 시그모이드 함수의 크기를 결정하는 계수로 양수로 설정할 경우 양의 부호거리장을, 음수로 설정할 경우 음의 부호거리장을 부여하는 효과를 갖는다.
상기 필터링 함수를 적용하여 도출된 TPMS 상면의 부호거리장 분포를 Fig. 2(c)에 도시하였다. 좌측 고온 유체 입출구 영역의 부호거리장이 적색 계열로 변화되어 고온 유체의 유동만이 허용되고, 우측 저온 유체 입출구 영역의 부호거리장은 청색 계열로 변화되어 저온 유체의 유동만이 허용됨을 알 수 있다. Fig. 2(d)에 상기 부호거리장을 적용하여 생성된 TPMS 구조를 도시하였으며, 입출구 영역에 해당 유체만 존재하여 유동 면적이 증가되고 결과적으로 압력강하를 감소시킬 수 있다[30].
2.3 원통형 영역에 대한 입출구 유동선별 필터링
본 연구에서는 입출구 유동 특성의 추가적인 향상을 위해 입출구 하단에 원통형의 채널 공간을 만들어 유동 선별과 동시에 열교환기 내부까지 유동저항 없이 주입되도록 필터링 영역을 설계하였다. 상기 목적의 달성을 위해 식(5)와 같이 기존의 필터링 함수 F(x, y, z) 내부에 특정 영역을 정의하는 영역함수 G(x, y, z)를 합성시켜 유효한 값을 가지는 공간을 정의할 수 있도록 하였다.
(5) |
본 연구에서는 관통형(Through-hole), 부분 관통형(Half-hole), 경사형(Taper-hole)의 3가지 형태의 원통형 영역을 정의하여 필터링 함수를 정의하였으며, 각각에 대한 수학적 표현은 다음과 같이 정의된다.
Fig. 3(a)에 관통형 입출구 필터링 영역을 정의하였으며, 유체 주입 시 열교환기의 하단까지 장애물 없이 흐르도록 하기 위해 원통형의 관통부를 설계하였다. 각 입출구 원통의 직경은 주입구의 내경과 동일하게 12 mm로 설계하였다. 상기 관통부 영역에 대한 필터링 함수는 식(6)과 같이 표현된다.
(6) |
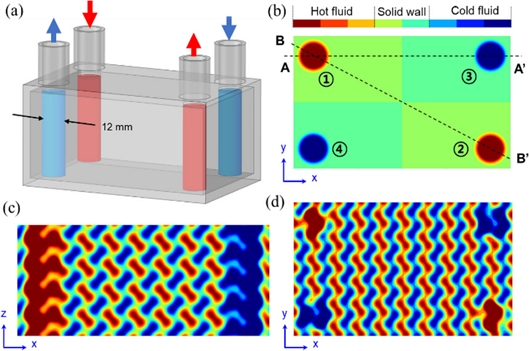
Design modification of a TPMS HX with the through-hole selection filtering: (a) definition of the filtering domain, (b) SDF distribution for selection filter (Top View), (c) SDF distribution after filtering (Section A-A’), and (d) SDF distribution after filtering (Top View)
여기서 xc, yc는 원통형 영역의 중심점을, r은 원통형 영역의 반경을 의미한다. 4개의 입출구 영역에 대한 중심점 좌표 및 계수를 Table 1에 요약하였다.
Fig. 3(b)에 상기 4개의 영역에 대한 필터링 함수로부터 도출된 부호거리장 분포를 도시하였다. 고온유체 입출구 영역은 양의 부호거리장이 부여되어 고온유체만 통과할 수 있도록 하였고, 마찬가지로 저온유체 입출구 영역은 음의 부호거리장이 부여되어 저온유체만 통과할 수 있도록 설정하였다. 상기 필터링 함수를 적용하여 도출된 부호거리장을 Figs. 3(c)와 3(d)에 도시하였다. Fig. 3(c)는 A-A’ 단면에서의 부호거리장으로 좌측에서는 고온유체가, 우측에서는 저온유체가 유입되도록 부호거리장이 변화되었음을 알 수 있다. Fig. 3(d)에 상측면의 부호거리장을 도시하였으며, 고온/저온 유체의 입출구가 구분됨을 확인할 수 있다.
Fig. 3에 도시한 관통형 입출구 설계안의 경우 입구로 유입된 유체가 바닥 면까지 수직으로 흐르게 되어 수평방향의 유동이 상대적으로 저하될 가능성이 있다. 이러한 문제점을 개선하기 위해 Fig. 4(a)에 도시한 바와 같이 원통형 영역이 TPMS 내부의 중간에 위치하는 부분 관통형(Half-hole) 필터링 영역을 정의하였다. 각 입출구 원통의 직경은 주입구의 내경과 동일하게 12 mm로 설계하였으며, 원통의 높이는 TPMS 영역 높이의 절반인 22 mm로 설계하였다. 상기 부분 관통부 영역에 대한 필터링 함수는 식(7)과 같이 표현된다.
(7) |
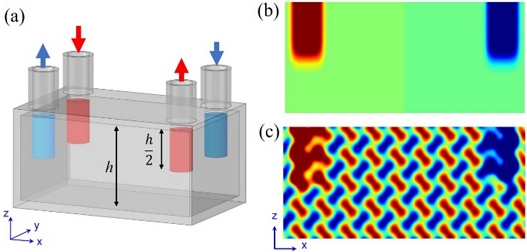
Design modification of a TPMS HX with the half-hole selection filtering: (a) definition of the filtering domain, (b) SDF distribution of half-hole filtering, and (c) SDF distribution after filtering (Section A-A’)
여기서 영역함수 G(x, y)는 식(6)의 관통형 영역함수와 동일하게 설정하였고, zp좌표를 지정하여 원통부의 높이를 조절할 수 있도록 하였다. 본 연구에서는 Fig. 4(a)에 도시한 바와 같이 관통 깊이를 전체 TPMS 높이의 절반(h/2)으로 설계하기 위해 zp좌표를 0으로, 시그모이드 계수 kz를 0.5로 설정하였다.
Fig. 4(b)에 식(7)로 정의된 필터링 함수의 부호거리장 분포를 Fig. 3(b)의 A-A’ 단면에서 도시하였다. 좌측 상단 영역에 양의 부호거리장이 부여되어 고온 유체가 주입될 수 있도록 하였고, 마찬가지로 우측 상단 영역에 음의 부호거리장이 부여되어 저온 유체가 주입될 수 있도록 하였다. Fig. 4(c)에 상기 필터링 함수를 적용하여 계산된 A-A’ 단면에서의 TPMS 부호거리장 분포를 도시하였으며, 의도한 바와 같이 좌측 상단 원통부는 양의 부호거리장이, 우측 원통부는 음의 부호거리장이 부여됨을 알 수 있다.
Fig. 5(a)에 경사형 입출구 필터링 영역을 정의하였다. 경사형 입출구는 하단으로 갈수록 원형 단면의 중심이 열교환기의 모서리 부분으로 이동하며 유동 진행 방향으로 감소하도록 설계하였다. 상기 경사형 영역에 대한 필터링 함수는 식(7)과 동일한 형태를 가지며, 경사형 영역함수 G(x, y, z)를 식(8)과 같이 정의하였다.
(8) |
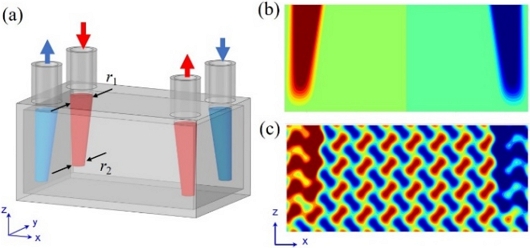
Design modification of a TPMS HX with the taper-hole selection filtering: (a) definition of the filtering domain, (b) SDF distribution of taper-hole filtering, and (c) SDF distribution after filtering (Section A-A’)
여기서 Xc, Yc는 원통형 영역의 중심점을, R은 원통형 영역의 반경을 의미하며, 높이에 따라 선형적으로 변화하도록 z의 함수로 설정하였다. 각각의 선형 함수는 식(9)부터 식(11)과 같이 정의된다.
(9) |
(10) |
(11) |
여기서 r1, r2는 경사면 상측과 하측 단면에서의 반경으로 각각 12, 6 mm로 설정하였다. 또한 상기 경사형 영역의 부피가 2.3.2절의 부분 관통형 영역과 동일하도록 경사형 영역의 높이를 38 mm로 설계하였고, 그에 따른 상/하측 단면의 중심점 좌표를 Table 2에 요약하였다.
Fig. 5(b)에 경사형 필터링 함수의 A-A’ 단면(Fig. 3(b) 참조) 부호거리장 분포를 도시하였다. 역시 좌측 상단 영역에 양의 부호거리장이, 우측 상단 영역에 음의 부호거리장이 부여됨을 알 수 있으며, 내측으로 경사면이 형성되어 수직 방향으로 주입되는 유체가 수평 방향으로도 분배될 수 있도록 설계하였다. Fig. 5(c)에 상기 필터링 함수를 적용하여 계산된 TPMS 부호거리장 분포를 도시하였으며, 좌측에 형성된 고온 유체 영역과 우측에 형성된 저온 유체영역에 경사면이 형성된 상대로 부호거리장이 형성되었음을 알 수 있다.
3. 입출구 설계안에 따른 유동 특성 고찰
3.1 압력강하 실험 결과
각 입출구 설계안이 유동 특성에 미치는 영향을 확인하기 위해 압력강하 실험을 실시하였다. 압력강하 실험을 위한 TPMS 열교환기 시제품은 DLP 방식의 3차원 프린터(IMD, Carima, Republic of Korea)를 사용하여 제작하였다. 적층 두께는 50 μm로 설정하였으며 UV광량은 6.4 W/cm로 설정하였다. 재료는 아크릴 계열 광경화성 플라스틱(CUKC06G, Carima, Republic of Korea)을 사용하였고, 후경화 처리는 UV 경화기(CL300, Carima, Republic of Korea)를 사용하여 60초 동안 진행하였다.
TPMS열교환기의 수력 직경(Hydraulic Diameter, Dh)은 다공성 물질의 수력 직경 계산 수식인 식(12)을 기반으로 도출하였다.
(12) |
여기서 ε은 전체 열교환기 부피에 대한 유체의 부피 비율(Void Fraction)이고, A는 전체 열교환기 부피에 대한 전열면적 비율(Area Density)이다. Table 3에 본 실험에 사용된 3가지의 TPMS 열교환기의 형상 정보 및 계산된 수력 직경 결과를 비교하였으며, 관통형 설계안에 비해 부분 관통형 및 경사형 설계안이 상대적으로 수력 직경이 작게 계산됨을 알 수 있다.
Fig. 6(a)에 압력강하 측정 실험을 위한 실험 장치 구성도를 도시하였다. 펌프를 통해 25oC의 물을 순환시켰으며, 유량계(Volume Flowmeter)를 사용하여 3-10 L/min 범위 내에서 유량을 조절하였다. 또한 TPMS 열교환기의 입출구에 차압계(Differential Pressure Transducer)를 설치하여 압력강하(Pressure Drop)를 측정하였다.
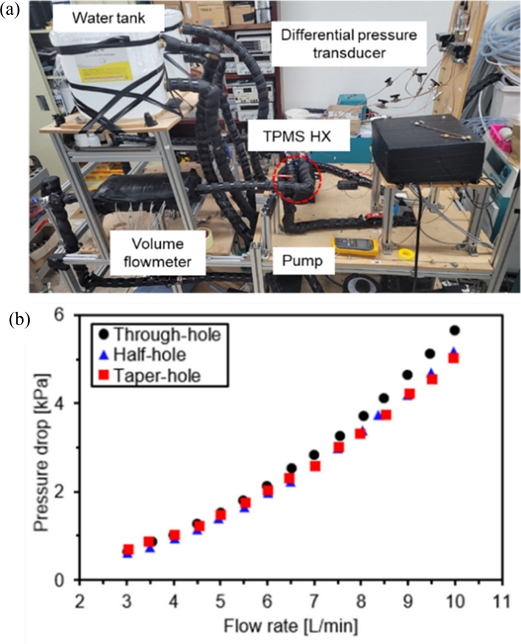
Pressure drop tests for various HX designs: (a) experimental setup, and (b) comparison of pressure drops
Fig. 6(b)에 유량변화에 따른 3가지 열교환기의 압력강하 측정 결과를 도시하였다. 낮은 유량(3-5 L/min)에서는 3가지 설계안의 압력강하가 비슷한 수준으로 나타남을 알 수 있다. 반면 유량이 6 L/min일 경우 압력강하가 1.96-2.13 kPa 수준으로 측정되어 선행연구의 결과(3.99 kPa)[30]의 절반 수준으로 압력강하를 줄일 수 있음을 확인하였다. 한편 유량이 6 L/min 이상으로 커질수록 관통형의 압력강하가 증가함을 알 수 있다. 이러한 차이는 유량이 증가할수록 더 두드러지게 나타나며, 10 L/min에서 관통형 설계안의 압력강하가 5.67 kPa로 측정되어 부분 관통형(5.17 kPa) 및 경사형(5.02 kPa)의 결과에 비해 10% 이상 크게 나타남을 알 수 있다.
3.2 CFD 시뮬레이션 결과
상기 열교환기 내부 채널에서 유동 특성을 고찰하기 위해 전산 유체 해석(Computational Fluid Dynamics, CFD)을 실시하였다. 해석은 상용 CFD 해석 S/W인 Simerics MP+를 사용하였다. 격자 조건은 Conformal Adaptive Binary Tree 방식으로 각 해석 모델당 약 1억 6천만개의 격자로 구성하였다. 해석 조건은 k-ε 난류 모델을 사용하였고, 작동 유체로 25oC의 물 6 L/min가 흐르도록 하였다.
Fig. 7에 B-B’ 단면(Fig. 3(b) 참조)에서 유체의 유선(Streamline)을 도시하였으며, 해당 위치에서의 유속을 색깔로 도시하였다. Fig. 7(a)는 관통형 설계안의 유선 분포이며, 입구부터 원기둥 하단으로 수직에 가까운 유동이 발생하여 결과적으로 열교환기 좌측 하단에 와류(Vortex)가 발생함을 알 수 있다. 반면 부분 관통형 및 경사형 설계안의 경우 해당 위치에서 와류가 발생하지 않아 상기 와류의 발생이 압력강하 증가에 영향을 미침을 알 수 있다. 또한 부분 관통형 설계안의 경우 Fig. 7(b)에 도시한 바와 같이 원통형 영역이 끝나는 중간 지점에서부터 수평방향 유동이 발생하여 하단부에서 수평방향 유동이 발생하는 관통형 설계안에 비해 유동 특성이 개선됨을 알 수 있다. 반면 출구 측 하단에서는 유동 밀도가 상대적으로 낮음을 알 수 있는데, 이는 부분 관통 영역 하단에서 국부적인 유동 정체가 발생하기 때문으로 판단된다. 한편 Fig. 7(c)에 도시한 경사형 설계안의 경우 입구 영역의 경사면에 의해 수평방향 유동 발생 위치가 상측으로 이동하여 상단과 하단에서 고르게 유동 분배가 이루어짐을 확인할 수 있다.
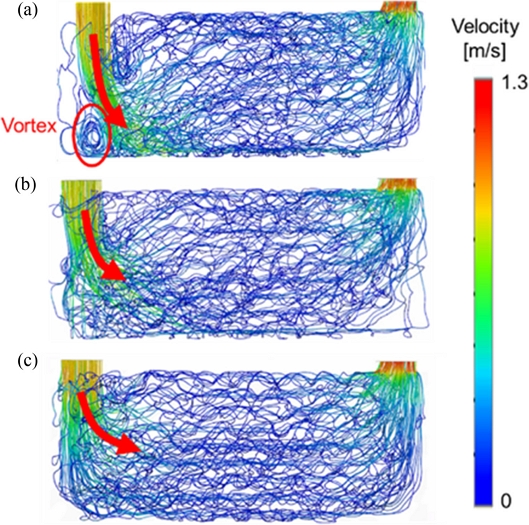
Comparison of streamlines across section B-B’ for various inlet/outlet designs: (a) through-hole filtering, (b) half-hole filtering, and (c) taper-hole filtering
Fig. 8에 B-B’ 단면(Fig. 3(b) 참조)에서의 수평방향 유속 크기를 정량적으로 비교하였다. 특히 유동 진행 방향으로의 속도 분포를 비교하기 위해 유동 진행 방향 단면의 법선 벡터와 속도 벡터를 내적하여 수평방향 속도 성분의 크기를 계산하여 가시화하였다. Fig. 8(a)에 관통형 입출구 설계안의 유속 분포를 도시하였으며 열교환기 하단에서 수평방향 유동이 발생함을 알 수 있다. 반면 Fig. 8(b)에 도시한 부분 관통형 설계안의 경우 수평방향 유동이 열교환기 중앙부에서 지배적으로 발생하는 것으로 나타나 유동 분배 특성이 개선됨을 확인할 수 있다. 반면 경사형 설계안의 경우는 Fig. 8(c)에 도시한 바와 같이 상단에서부터 수평방향 유동이 발생하여 상단과 하단에서 전체적으로 균일하게 유량이 분배됨을 알 수 있다. 상기 결과로부터 경사형 입출구 설계안이 가장 좋은 유동 분배 특성을 보여 압력강하를 감소시킬 수 있는 설계안으로 판단된다.
4. TPMS 열교환기의 열교환 성능 고찰
4.1 금속 적층 제조를 사용한 열교환기 제작
TPMS 열교환기의 열교환 성능을 확인하기 위해 전술한 3가지 설계안 중 가장 우수한 유동 특성을 보인 경사형 입출구 설계안을 금속 적층 제조를 사용하여 제작하였다. 열교환기의 적층 제조는 분말 용융 적층(Powder Bed Fusion, PBF) 방식의 금속 3D 프린터(CL M2 Cusing, GE Additive, USA)와 알루미늄 합금 분말재(AlSi7Mg, Tekna Advanced Materials, Canada)를 사용하여 수행하였다. 적층 제조를 위한 레이저 출력은 370 W, 이송 속도는 1,600 m/s로 설정하였고, 적층 두께, 레이저빔 직경, 해칭 간격은 각각 40, 110, 120 μm로 설정하였다. 적층 제조된 열교환기는 마이크로 블라스팅 장비를 사용하여 표면처리를 수행하였고, 280oC의 온도로 90분 동안 진공 열처리를 수행하였다.
금속 적층 제조로 제작된 TPMS 형상의 내부 형상정밀도를 확인하기 위해 X-선 단층촬영을 실시하였다. X-선 단층촬영은 마이크로-CT 스캐너(Phoenix VTOMEX S240, Waygate Technologies, Germany)를 사용하여 실시하였다. 상기 장비의 촬영 해상도는 100 μm이며 약 13억개 이상의 복셀로 내부 구조를 표현할 수 있다. Figs. 9(b)부터 9(d)에 3개 단면(C-C’, D-D’, E-E’)에서의 CT사진을 도시하였으며, 각각의 단면 위치는 Fig. 9(a)에 표시하였다. 각 단면에서 표시한 영역의 두께는 각 0.53, 0.52, 0.53 mm로 측정되어 설계 치수인 0.5 mm와 6% 정도 오차가 있었고 내부 기공과 누출 영역 없이 제작된 것을 확인하였다. 또한 입출구 영역의 크기가 하단으로 내려갈수록 점차적으로 감소하며 E-E’ 단면에서는 존재하지 않아 경사형 입출구가 적절하게 구현되었음을 알 수 있다.
4.2 열교환 실험을 통한 성능 분석
적층 제조로 제작된 금속 TPMS 열교환기의 열교환 성능을 확인하기 위해 단상 유동 열전달 실험을 진행하였다. 고온측 유체는 에틸렌 글로켈과 물을 동일 부피로 섞어 25oC로 유지시켰다. 저온측 유체는 냉각기(Chiller)를 사용하여 10oC의 물이 흐르도록 하였고 고온측과 저온측의 열교환율의 차이를 ±5% 이하로 유지하여 실험을 진행하였다. 고온측 유량을 8-10 L/min으로 변화시킨 상태에서 저온측 유량을 3-10 L/min 범위에서 0.5 L/min 간격으로 변경시키며 열교환기의 열전달 및 압력강하를 측정하였다.
Fig. 10(a)에 유량별 열교환 용량(Heat Capacity, Q)을 그래프로 도시하였다. 고온측 유량을 8 L/min로 고정한 경우 열교환 용량은 저온측 유량이 10 L/min일 때 최대 1.93 kW까지 증가하였으며, 고온측 유량을 10 L/min로 고정한 경우 열교환 용량은 저온측 유량이 10 L/min 일 때 최대 2.14 kW까지 증가하였다. 상기 결과는 고온측 유량이 8 L/min에서 10 L/min으로 20% 증가하였을 때, 동일한 저온측 유량 조건에서 최대 11%까지 열교환 용량이 증가함을 의미한다.
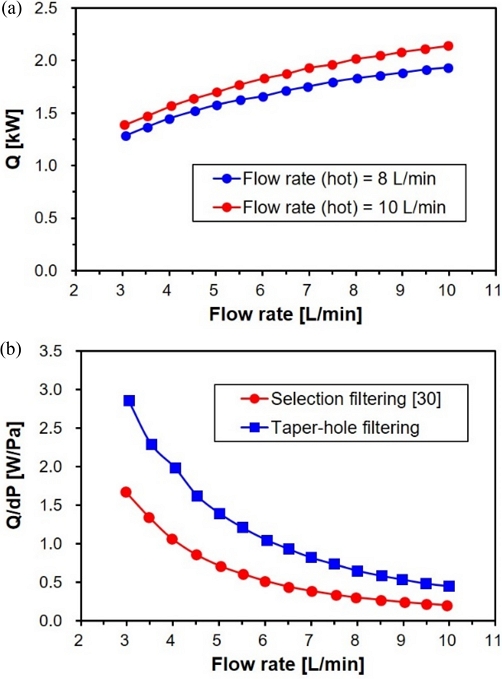
Results of heat exchange tests: (a) comparison of heat transfer rate (Q), and (b) comparison of heat transfer rate per pressure drop (Q/dP)
상기 결과를 바탕으로 본 연구에서 개발한 TPMS 열교환기(경사형 입출구 적용)의 열교환 성능을 선행연구 결과[30]와 종합적으로 비교하기 위해 2가지 열교환기의 압력강하 대비 열교환 용량(Q/dP)을 비교하였다. 전반적으로 유량이 증가할수록 압력강하 대비 열교환 용량이 감소함을 알 수 있으며, 본 연구에서 개발한 경사형 입출구 적용 열교환기의 경우 선행 연구의 열교환기와 비교했을 때 2배 이상의 높은 열교환 성능(70.1-125.1%)을 보임을 알 수 있다.
5. 결론
본 연구에서는 TPMS 구조를 활용하여 고집적 열교환기 설계에 관한 연구를 수행하였다. 열교환기 입출구의 유동 특성 향상을 위해 원통형 영역에 대한 시그모이드 합성함수를 적용한 수학적 필터링 기법을 활용하여 유동 선별 기능이 포함된 3가지 입출구 형상(관통형, 부분 관통형, 경사형)을 설계하였다. 실험과 전산 유체 해석을 통해 유동 성능을 확인하는 연구를 수행하였으며, 다음과 같은 결론을 도출하였다.
(1) DLP 적층 제조를 사용하여 플라스틱 열교환기 시제품을 제작하고 압력강하 실험을 수행하였다. 유량 6 L/min에서는 부분 관통형에서 압력강하 값이 1.96 kPa로 가장 작게 나타나 선행연구의 절반 수준으로 감소됨을 확인하였다. 또한 유량 10 L/min에서는 경사형 입출구에서 압력강하 값이 5.02 kPa로 가장 작게 나타났다.
(2) CFD 해석 수행 결과 관통형의 경우 유체가 바닥 면과 충돌하여 와류가 발생한 것이 압력강하의 증가를 유발함을 확인하였다. 또한 경사형 입출구가 유동 가이드 역할을 수행하며 상단과 하단에서 균일한 유동 분배가 이루어지고 결과적으로 압력강하가 감소됨을 확인하였다.
(3) 경사형 입출구를 적용하여 금속 적층 제조를 통해 열교환기를 제작하여 열교환 성능(압력강하 대비 열교환 용량)을 측정한 결과 선행연구 대비 2배 이상의 높은 열교환 성능(70.1-125.1%)을 보임을 알 수 있었다.
상기 결과로부터 본 연구에서 제안된 경사형 TPMS 열교환기는 기존 연구결과 대비 낮은 압력강하와 유동 분배 측면에서 장점이 보임을 알 수 있다. 향후 보다 복잡하고 유동에 최적화된 TPMS 열교환기에 대한 추가 연구를 수행하여 기술의 완성도를 높일 전망이다.
NOMENCLATURE
ϕG : | Gyroid-type TPMS Surface Function |
ϕ'G : | Filtered Gyroid-type TPMS Function |
C : | Level-set Constant for TPMS Structure |
F(x, y, z) : | Sigmoid-based Filtering Function |
G(x, y, z) : | Filtering Function for Inlet and Outlet Domains |
kx, ky, kz : | Directional Sigmoid Coefficients |
β : | Magnitude of Sigmoid Function |
(xp, yp, zp) : | Threshold Position of Sigmoid Function |
(xc, yc) : | Center Position of Cylindrical Filtering Domain |
(Xc, Yc) : | Center Position of Tapered Filtering Domain |
R(z) : | Radius Function of Tapered Filtering Domain |
Dh : | Hydraulic Diameter of TPMS Channels |
Acknowledgments
이 논문은 산업통상자원부 전자시스템 전문기술개발사업(No. 20016840) 및 과학기술정보통신부(한국연구재단)의 기초연구실사업(No. 2022R1A4A1032030)의 지원으로 수행된 결과임.
REFERENCES
- Kays, W. M., London, A. L., (1984), Compact heat exchangers, Krieger Publishing Company.
-
Zohuri, B., (2015), Application of compact heat exchangers for combined cycle driven efficiency in next generation nuclear power plants, Springer.
[https://doi.org/10.1007/978-3-319-15560-9]
-
Kan, M., Ipek, O., Gurel, B., (2015), Plate heat exchangers as a compact design and optimization of different channel angles, Acta Physica Polonica A, 128(2B).
[https://doi.org/10.12693/APhysPolA.128.B-49]
-
Lin, Z.-M., Liu, C.-P., Lin, M., Wang, L.-B., (2015), Numerical study of flow and heat transfer enhancement of circular tube bank fin heat exchanger with curved delta-winglet vortex generators, Applied Thermal Engineering, 88, 198-210.
[https://doi.org/10.1016/j.applthermaleng.2014.11.079]
-
Mortean, M. V. V., Cisterna, L. H. R., Paiva, K. V., Mantelli, M. B. H., (2019), Thermal and hydrodynamic analysis of a cross-flow compact heat exchanger, Applied Thermal Engineering, 150, 750-761.
[https://doi.org/10.1016/j.applthermaleng.2019.01.038]
-
Song, Y., Asadi, M., Xie, G., Rocha, L. A. O., (2015), Constructal wavy-fin channels of a compact heat exchanger with heat transfer rate maximization and pressure losses minimization, Applied Thermal Engineering, 75, 24-32.
[https://doi.org/10.1016/j.applthermaleng.2014.05.027]
-
Kaur, I., Singh, P., (2021), State-of-the-art in heat exchanger additive manufacturing, International Journal of Heat and Mass Transfer, 178, 121600.
[https://doi.org/10.1016/j.ijheatmasstransfer.2021.121600]
-
Guo, N., Leu, M. C., (2013), Additive manufacturing: technology, applications and research needs, Frontiers of Mechanical Engineering, 8, 215-243.
[https://doi.org/10.1007/s11465-013-0248-8]
-
Park, J.-H., Goo, B., Park, K., (2019), Topology optimization and additive manufacturing of customized sports item considering orthotropic anisotropy, International Journal of Precision Engineering and Manufacturing, 20, 1443-1450.
[https://doi.org/10.1007/s12541-019-00163-4]
-
Oh, E.-J., Lee, J.-H., Kim, J.-E., Park, K., (2020), Lightweight design of a sledge frame for para ice hockey using design for additive manufacturing, Journal of the Korean Society for Precision Engineering, 37(6), 407-414.
[https://doi.org/10.7736/JKSPE.020.039]
-
Cha, E., Kim, T.-Y., Ha, T., Park, K., (2021), Lightweight design of a vacuum gripper for inspection equipment using topology optimization, Journal of the Korean Society for Precision Engineering, 38(9), 683-690.
[https://doi.org/10.7736/JKSPE.021.051]
-
McGlen, R. J., (2021), An introduction to additive manufactured heat pipe technology and advanced thermal management products, Thermal Science and Engineering Progress, 25, 100941.
[https://doi.org/10.1016/j.tsep.2021.100941]
-
Da Silva, R. P. P., Mortean, M. V. V., De Paiva, K. V., Beckedorff, L. E., Oliveira, J. L. G., Brandão, F. G., Monteiro, A. S., Carvalho, C. S., Oliveira, H. R., Borges, D. G., Chastinet, V. L., (2021), Thermal and hydrodynamic analysis of a compact heat exchanger produced by additive manufacturing, Applied Thermal Engineering, 193, 116973.
[https://doi.org/10.1016/j.applthermaleng.2021.116973]
-
Sabau, A. S., Bejan, A., Brownell, D., Gluesenkamp, K., Murphy, B., List III, F., Carver, K., Schaich, C. R., Klett, J. W., (2020), Design, additive manufacturing, and performance of heat exchanger with a novel flow-path architecture, Applied Thermal Engineering, 180, 115775.
[https://doi.org/10.1016/j.applthermaleng.2020.115775]
-
Chekurov, S., Kajaste, J., Saari, K., Kauranne, H., Pietola, M., Partanen, J., (2019), Additively manufactured high-performance counterflow heat exchanger, Progress in Additive Manufacturing, 4, 55-61.
[https://doi.org/10.1007/s40964-018-0059-x]
-
You, J.-H., Lee, J.-W., Oh, S.-H., Park, K., (2022), Conformal mold heating and cooling using a carbon nanotube film heater and additively manufactured cellular metamaterial, International Journal of Precision Engineering and Manufacturing-Green Technology, 9(6), 1463-1476.
[https://doi.org/10.1007/s40684-021-00407-7]
-
You, J.-H., Park, K., (2021), Design and additive manufacturing of thermal metamaterial with high thermal resistance and cooling capability, Additive Manufacturing, 41, 101947.
[https://doi.org/10.1016/j.addma.2021.101947]
-
Yang, L., Li, Y., Wu, S., Chen, P., Wu, H., Su, J., Wang, H., Liu, J., Yan, C., Shi, Y., (2022), Tailorable and predictable mechanical responses of additive manufactured TPMS lattices with graded structures, Materials Science and Engineering: A, 843, 143109.
[https://doi.org/10.1016/j.msea.2022.143109]
-
Kaur, I., Singh, P., (2021), Critical evaluation of additively manufactured metal lattices for viability in advanced heat exchangers, International Journal of Heat and Mass Transfer, 168, 120858.
[https://doi.org/10.1016/j.ijheatmasstransfer.2020.120858]
-
Kaur, I., Singh, P., (2021), Flow and thermal transport characteristics of triply-periodic minimal surface (TPMS)-based gyroid and schwarz-P cellular materials, Numerical Heat Transfer, Part A: Applications, 79(8), 553-569.
[https://doi.org/10.1080/10407782.2021.1872260]
-
Li, W., Yu, G., Yu, Z., (2020), Bioinspired heat exchangers based on triply periodic minimal surfaces for supercritical CO2 cycles, Applied Thermal Engineering, 179, 115686.
[https://doi.org/10.1016/j.applthermaleng.2020.115686]
-
Yan, K., Wang, J., Liu, L., Deng, H., (2023), Numerical investigation into thermo-hydraulic characteristics and mixing performance of triply periodic minimal surface-structured heat exchangers, Applied Thermal Engineering, 230, 120748.
[https://doi.org/10.1016/j.applthermaleng.2023.120748]
-
Kim, J., Yoo, D. J., (2020), 3D printed compact heat exchangers with mathematically defined core structures, Journal of Computational Design and Engineering, 7(4), 527-550.
[https://doi.org/10.1093/jcde/qwaa032]
-
Yoo, D. J., (2011), Porous scaffold design using the distance field and triply periodic minimal surface models, Biomaterials, 32(31), 7741-7754.
[https://doi.org/10.1016/j.biomaterials.2011.07.019]
-
Yoo, D. J., (2011), Computer-aided porous scaffold design for tissue engineering using triply periodic minimal surfaces, International Journal of Precision Engineering and Manufacturing, 12, 61-71.
[https://doi.org/10.1007/s12541-011-0008-9]
-
Ouda, M., Al-Ketan, O., Sreedhar, N., Ali, M. I. H., Al-Rub, R. K. A., Hong, S., Arafat, H. A., (2020), Novel static mixers based on triply periodic minimal surface (TPMS) architectures, Journal of Environmental Chemical Engineering, 8(5), 104289.
[https://doi.org/10.1016/j.jece.2020.104289]
-
Khalil, M., Ali, M. I. H., Khan, K. A., Al-Rub, R. A., (2022), Forced convection heat transfer in heat sinks with topologies based on triply periodic minimal surfaces, Case Studies in Thermal Engineering, 38, 102313.
[https://doi.org/10.1016/j.csite.2022.102313]
-
Oh, S.-H., Ha, J.-W., Park, K., (2022), Adaptive conformal cooling of injection molds using additively manufactured TPMS structures, Polymers, 14(1), 181.
[https://doi.org/10.3390/polym14010181]
-
Lee, J.-W., Oh, S.-H., Jeon, E., Kim, J., Park, K., (2022), Functional gradation of the morphological properties of TPMS channel for enhanced flow performance, Materials and Design, 224, 111413.
[https://doi.org/10.1016/j.matdes.2022.111413]
-
Oh, S.-H., An, C.-H., Seo, B., Kim, J., Park, C. Y., Park, K., (2023), Functional morphology change of TPMS structures for design and additive manufacturing of compact heat exchangers, Additive Manufacturing, 76, 103778.
[https://doi.org/10.1016/j.addma.2023.103778]
M.Sc. candidate in Department Mechanical System Design Engineer-ing, Seoul National University of Scie-nce and Technology. Her research interest is DfAM (Design for Additive Manufacturing).
E-mail: osh516406@seoultech.ac.kr
M.Sc. candidate in the Dept. Mechanical Design and Robot Engine-ering, Seoul National University of Science and Technology. Her research area is experimental and numerical heat transfer.
E-mail: 421_kim@naver.com
B.Sc. candidate in the Dept. Mechanical System Design Engine-ering, Seoul National University of Science and Technology. His research area is experimental and numerical heat transfer.
E-mail: wltjd4664@naver.com
B.Sc. in the Dept. of Mechanical System Design Engineering, Seoul National University of Science and Technology. His research area is computational fluid dynamics and HX Simulation (Thermal Fluid Analysis)
E-mail: kdr0527@seoultech.ac.kr
Professor in the Dept. Mechanical System Design Engineering, Seoul National University of Science and Technology. His research area is computational fluid dynamics and its application to thermo-fluidic parts, including heat exchangers.
E-mail: kimjw@seoultech.ac.kr
Professor in the Dept. Mechanical System Design Engineering, Seoul National University of Science and Technology. His research area is phase change phenomena, heat transfer, heat exchangers, energy systems, and HVAC&R systems.
E-mail: cypark@seoultech.ac.kr
Professor in the Dept. Mechanical System Design Engineering, Seoul National University of Science and Technology. His research area is multi -physics numerical simulation and its application to DfAM (Design for Additive Manufacturing).
E-mail: kpark@seoultech.ac.kr